What is the Ultrasonic Weld Checker?
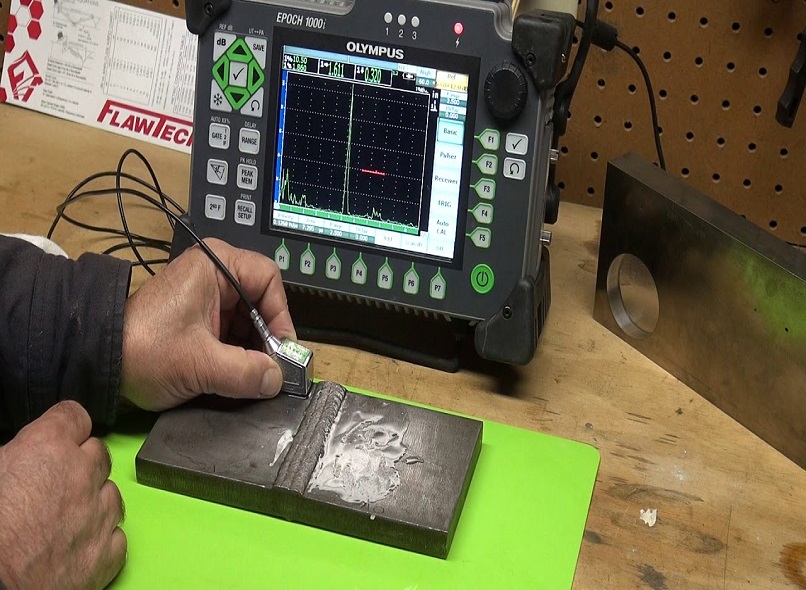
The ultrasonic weld checker is an innovative and advanced device that has transformed the field of non-destructive testing of welds. With its cutting-edge technology, precise capabilities, and wide range of applications, it has become an indispensable tool for ensuring the highest quality, integrity, and safety of welded joints in various industries.
Utilizing the power of ultrasonic waves, the ultrasonic weld checker performs a thorough and comprehensive inspection of welds in different materials. It emits high-frequency sound waves into the material under examination, which propagate through the material until they encounter a change in density, such as a weld or a flaw. These sound waves are intelligently reflected back to the device, where they are meticulously analyzed to identify any defects or inconsistencies in the weld.
The ultrasonic weld checker's ability to detect and evaluate defects in welds is crucial for maintaining the structural integrity of various components and assemblies. In industries such as manufacturing, construction, automotive, aerospace, oil and gas, and even art restoration, where welded joints play a vital role, ensuring the reliability, durability, and safety of these joints is of utmost importance. The ultrasonic weld checker serves as a powerful tool in this regard, providing inspectors with accurate and detailed information about any potential weaknesses or flaws in the weld.
One of the key advantages of the ultrasonic weld checker is its ability to detect a wide range of defects, including cracks, voids, lack of fusion, porosity, inclusions, and even hidden internal flaws. By identifying these flaws, inspectors can take immediate corrective actions to prevent further damage or failure. Moreover, the device also provides valuable insights into the size, shape, orientation, and location of the detected defects, allowing inspectors to assess their severity and impact on the overall quality of the weld.
In addition to defect detection, the ultrasonic weld checker offers numerous benefits in terms of efficiency, cost-effectiveness, and versatility. By enabling swift and precise inspections, it saves valuable time and resources. Inspectors can quickly identify any potential flaws or weaknesses in welds, allowing for timely repairs or necessary adjustments. This not only prevents costly rework but also ensures that the welded components meet the required standards, specifications, and regulatory requirements.
Furthermore, the ultrasonic weld checker enhances the overall quality control process by providing objective and reliable data. Inspectors can make well-informed decisions based on the information provided by the device, ensuring that the welds meet the desired standards and performance requirements. This ultimately contributes to the longevity, reliability, and safety of the welded structures and components.
The applications of the ultrasonic weld checker are vast and diverse. In addition to traditional industries such as manufacturing, construction, and automotive, it is also extensively used in fields such as aerospace, oil and gas, power generation, shipbuilding, and even medical device manufacturing. In each of these industries, the device plays a crucial role in ensuring the safety, functionality, and longevity of welded joints, which are critical for the integrity of various structures and systems.
In conclusion, the ultrasonic weld checker is a game-changer in the field of non-destructive testing. Its advanced technology, precise capabilities, and comprehensive inspection process make it an indispensable tool for detecting, evaluating, and ensuring the highest quality of welds. By utilizing the power of ultrasonic waves, it empowers inspectors to make informed decisions and take necessary actions to maintain the quality and integrity of welded joints. In doing so, it significantly contributes to the overall safety, reliability, efficiency, and success of various industries.