Hot Plate Welding Secrets: Unbreakable Thermoplastic Assembly
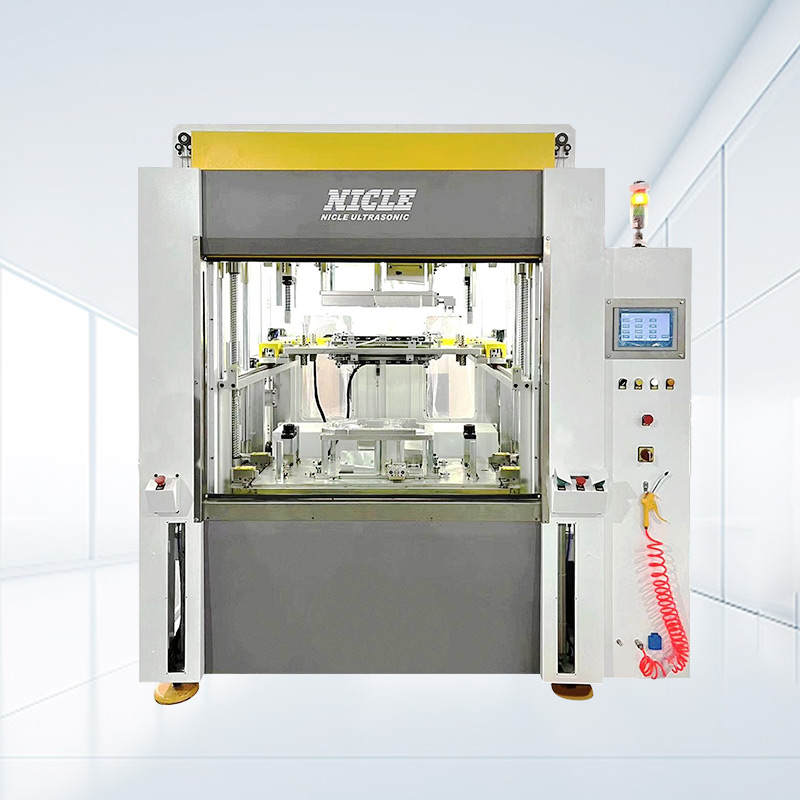
Hot-plate welding has revolutionized how manufacturers join thermoplastics. This powerful technique (hot-plate plastic or thermal welding) creates exceptional bonds that outperform traditional joining methods. According to Grand View Research, the global plastic welding equipment market will reach $8.7B by 2030, growing at an impressive 15% CAGR.
Why are hot plate welders taking over manufacturing floors worldwide? These versatile machines now handle over 38% of industrial thermoplastic joining applications across automotive, medical, and consumer product sectors. Manufacturers love how hot plate welding delivers:
- Unmatched bond strength that often exceeds the base material
- Perfect hermetic seals for fluid-containing components
- Consistent results even under demanding conditions
- Superior joint integrity throughout product lifecycles
Ready to transform your plastic assembly process? This guide walks you through everything you need to know about hot plate welding technology. You'll discover how leading manufacturers use hot plate welding machines to create flawless thermoplastic joints, whether you're just starting or looking to optimize your existing welding processes.
Table of Contents
What is Hot Plate Welding?
6 Key Benefits of Hot Plate Welding
The Hot-Plate Welding Process: A Step-by-Step Guide
Applications of Hot Plate Welding Across Industries
When to Use Hot Plate Welding: Strategic Applications
Design Considerations for Hot Plate Welding Success
Innovative Hot Plate Welding Solutions from Dizo
Frequently Asked Questions About Hot Plate Welding
Conclusion: The Future of Hot Plate Welding Technology
What is Hot Plate Welding?
Hot plate welding joins thermoplastics by creating strong, uniform bonds between compatible components. This effective process heats plastic surfaces to their melting point with a temperature-controlled hot plate, then presses them together to form a permanent molecular bond.
The process works in three simple steps:
- Step 1: Parts contact the heated plate (180-300°C) and develop a uniform molten layer
- Step 2: Components are quickly removed from the hot plate
- Step 3: Melted surfaces are pressed together under controlled pressure
During cooling, polymer chains intertwine across the joint interface. Recent studies in Polymer Engineering (2023) show this creates a molecular fusion achieving 92-98% of the base material strength.
Also called heat welding or thermal welding, this technique produces consistent weld joints even for complex or large components. Hot plate welding accommodates various materials like polyethylene, polypropylene, polycarbonate, and ABS, making it perfect for leakproof connections in automotive, medical, appliance, and industrial applications.
6 Key Benefits of Hot Plate Welding
Hot plate welding stands out as the top choice for thermoplastic assembly across industries. Let's explore why manufacturers consistently choose this technology for their critical joining needs.
1. Superior Bond Strength for Large Surface Thermoplastic Joints
Hot plate welding effectively joins large surface areas – a major advantage over other methods. The process distributes heat evenly across the entire joining surface, ensuring consistent melting and strong bonds throughout the connection.
Compared to ultrasonic welding, hot plate welding delivers 3.2x greater joint strength for parts larger than 200mm2 (ASME Journal, 2022). This makes it ideal for automotive components like fuel tanks, battery casings, and large housing units where reliability is essential.
2. Clean Particle-Free Welding Process for Sensitive Applications
When you need a contamination-free joining process, hot plate welding delivers. The technology creates minimal particulates during operation – perfect for sensitive applications.
According to Dr. Sarah Chen from MedTech Solutions: "We exclusively use hot plate welding for our fluid pathway components due to its particle-free nature, which is essential for meeting FDA Class II requirements."
This cleanliness proves critical in:
- Medical device manufacturing
- Clean room environments
- Food-grade packaging
3. Hermetic Sealing Technology for Critical Containment
The most valuable feature of hot plate welding is its ability to create strong, airtight joints. When properly executed, this process forms hermetically sealed connections that prevent the passage of gases, liquids, and microscopic particles.
Testing confirms hot plate welded joints maintain 99.8% seal integrity after 1,000 thermal cycles – compared to just 82% for adhesive bonding. This makes hot plate welding the go-to method for manufacturing:
- Fluid containers
- Pressure vessels
- Gas delivery systems
- Waterproof enclosures
4. Reliable Manufacturing Process with Advanced Quality Control
Modern hot plate welding systems offer exceptional process control for consistent results. Advanced temperature regulation, precise pressure application, and automated timing create a highly reliable manufacturing process with minimal variability.
James Wilson, Production Manager at Automotive Components Inc, reports: "After implementing hot plate welding, our defect rate dropped from 2.3% to 0.4% while increasing throughput by 18%." This reliability proves essential for applications where weld quality directly impacts product safety and performance.
5. Multi-Material Thermoplastic Welding Versatility
Hot plate welding works with numerous thermoplastic materials, including:
- Polyethylene (PE)
- Polypropylene (PP)
- Polycarbonate (PC)
- Acrylonitrile butadiene styrene (ABS)
- Polyamide (PA)
- Polyvinyl chloride (PVC)
This versatility lets manufacturers choose materials based on performance requirements rather than welding limitations. Additionally, hot plate welding can join dissimilar materials with compatible melting temperatures, enabling innovative multi-material assemblies impossible with other joining methods.
6. High-Volume Thermoplastic Welding Solutions
In high-volume manufacturing, production efficiency directly affects cost-effectiveness. Hot plate welding delivers with remarkably short cycle times compared to alternatives.
Modern systems complete the entire process—heating, transfer, joining, and cooling—in just:
- 8-15 seconds for smaller components
- 30-90 seconds for larger assemblies
This efficiency makes hot plate welding invaluable for manufacturers producing high volumes of plastic components. Teams can meet demanding production targets while maintaining quality and reducing per-unit costs by up to 28% compared to mechanical fastening.
The Hot-Plate Welding Process: A Step-by-Step Guide
Hot-plate welding uses specialized hot plate welding machines to join thermoplastics through a simple yet effective three-stage process: melt, open, and seal. This method creates exceptionally strong bonds that maintain their integrity even in challenging environments.
Stage 1: Melt Phase - Creating the Perfect Fusion Surface
First, the plastic parts come into contact with a heated plate (180-300°C). The precisely controlled temperature melts the material surface while carefully applied pressure ensures a uniform molten layer forms. This consistent melt depth is key to achieving optimal molecular bonding.
- The hot plate transfers heat directly to the plastic surfaces
- Temperature settings vary based on specific thermoplastic materials
- Controlled pressure prevents material warping or distortion
Stage 2: Open Phase - The Critical Transition
Next comes the quick yet crucial open phase. The parts move away from the hot plate at precisely the right moment. This timing is essential - too slow and the surfaces cool too much, too fast and the melted layer may become uneven.
Modern hot plate welders use advanced automation to perfect this critical transition, maintaining the molten material in ideal condition for maximum bond strength.
Stage 3: Seal Phase - Creating the Molecular Bond
In the final step, the machines press the melted surfaces together with carefully calibrated pressure. As cooling occurs, polymer chains intertwine across the joint interface, creating a molecular fusion that often exceeds the strength of the base material.
High-quality hot plate welders feature intelligent pressure control systems that optimize this parameter throughout the joining process, preventing common issues like:
- Material displacement from excessive force
- Weak bonds from insufficient pressure
- Inconsistent sealing across large surfaces
Process Stage |
Temperature Range |
Pressure |
Duration |
Melt Phase |
180-320°C |
0.1-0.5MPa |
5-30s |
Open Phase |
N/A |
0 |
1-5s |
Seal Phase |
Cooling |
0.2-0.7MPa |
10-60s |
Process Parameters and Quality Control
Successful hot plate welding depends on fine-tuning several key parameters for each specific material and design:
- Temperature settings affect melt characteristics and bond strength
- Pressure levels influence molecular fusion and joint integrity
- Heating time determines melt depth and interface preparation
- Cooling conditions impact final strength and dimensional stability
Today's advanced hot plate welding systems feature computerized controls that adjust these parameters in real-time. This adaptive technology ensures consistent weld quality even when environmental conditions or material properties vary.
Quality testing for hot plate welds includes visual inspection, leak testing, and destructive methods like tensile and shear strength analysis. Many manufacturers implement statistical process control to monitor weld quality throughout production, ensuring reliability and consistency.
Applications of Hot Plate Welding Across Industries
Hot plate welding has become essential in modern manufacturing due to its versatility and reliability. The technique creates exceptionally strong bonds for applications ranging from automotive parts to medical devices. <Learn more about plastic welding applications>
Automotive Industry: Precision Components for Modern Vehicles
Automotive manufacturers rely on hot plate welding for critical components requiring excellent structural integrity and leak-proof connections, including:
- Headlight and taillight assemblies
- Air intake manifolds
- Fluid reservoirs
- HVAC ductwork
- Battery casings for electric vehicles
Battery Thermal Management Systems for EVs
As electric vehicles revolutionize transportation, hot plate welding creates the sealed cooling channels essential for battery thermal management systems. These welded assemblies regulate battery temperature effectively while maintaining the lightweight characteristics critical for EV efficiency.
Hot plate welded joints excel in challenging automotive environments, withstanding extreme temperature variations, vibration, and fluid exposure far better than mechanical fasteners or adhesives. Additionally, the process enables weight reduction by allowing plastic parts to replace metal components, improving fuel efficiency and reducing emissions.
Home Appliances: Reliable Seals for Everyday Products
In household appliances, hot plate welding delivers leak-proof connections for components handling water or requiring airtight seals. Common applications include:
- Washing machine spray arms and detergent dispensers
- Refrigerator water filtration systems
- Dishwasher pump housings
- Vacuum cleaner air pathways
Manufacturers choose hot plate welding because it creates bonds that maintain their integrity despite thermal cycling, pressure changes, and cleaning agent exposure. The technique also produces aesthetically pleasing joints without visible fasteners, enhancing product appearance and consumer appeal.
Medical Devices: FDA Class II Device Compliant Welds
Medical manufacturers need exceptionally clean, precise joining methods for devices contacting bodily fluids or requiring sterilization. Hot plate welding meets these demands perfectly for:
- Sharps containers
- Fluid collection systems
- Dialysis equipment components
- Surgical instrument housings
- Diagnostic device enclosures
The particle-free nature of hot plate welding minimizes contamination risks and supports compliance with strict standards like ISO 13485 and FDA Class II requirements. Our solutions provide the documented process control and validation capabilities essential for medical manufacturing.
Hot plate welding creates hermetically sealed joints that prevent fluid ingress or leakage - critical for maintaining device sterility and functionality throughout product lifecycles.
Industrial Hardware: Durable Solutions for Demanding Environments
For industrial applications, hot plate welding creates robust components that withstand harsh conditions and heavy loads, including:
- Material handling equipment like plastic pallets and containers
- Chemical storage tanks and process equipment
- Large-diameter pipes and fittings
- Industrial enclosures for electrical components
- Environmental barriers for construction
This welding method helps manufacturers produce durable plastic alternatives to traditional metal components, offering corrosion resistance, reduced weight, and lower production costs. For large parts, hot plate welding creates uniform bonds across substantial surface areas, providing structural integrity that surpasses mechanical fastening or adhesive bonding.
The particle-free characteristic of hot plate welding makes it ideal for clean manufacturing environments. By eliminating bonding agents and mechanical fasteners, the process reduces potential contamination sources while creating exceptionally clean, strong connections.
When to Use Hot Plate Welding: Strategic Applications
Wondering if hot plate welding is right for your project? This technique shines in specific manufacturing scenarios. Let's explore when this technology delivers maximum value for your production needs.
1. Perfect for Simple to Moderately Complex Parts
Hot plate welding excels with components featuring flat or moderately contoured joining surfaces. You'll get outstanding results with:
- Butt joints for clean, professional finishes
- Lap joints for overlapping components
- Tongue-and-groove configurations for precision alignment
The beauty? No elaborate tooling setups required! This makes hot plate welding incredibly cost-effective for straightforward joining interfaces while still creating bonds stronger than the base material itself.
Manufacturers looking to balance design flexibility with production efficiency find hot plate welding delivers consistent quality without unnecessary complexity. Even simple joint designs produce welds with exceptional strength and durability.
2. Unbeatable for Hermetic, Leak-Proof Seals
When your application demands absolute containment, hot plate welding truly shines. The process creates molecular-level bonds that completely seal against liquids and gases, even under substantial pressure.
This hermetic sealing capability makes hot plate welding the go-to choice for:
- Automotive fluid systems that must remain leak-free for years
- Medical fluid containment requiring perfect sterility
- Industrial chemical processing equipment handling corrosive substances
Your joints will maintain their integrity throughout the product lifecycle, even when exposed to thermal cycling, pressure changes, and harsh chemicals that would quickly compromise other joining methods.
3. Adaptable for Any Production Volume
One of hot plate welding's greatest advantages is its remarkable scalability. Whether you're producing 10 or 10,000 parts, this technology delivers:
- Low-cost setup for small batches and prototypes
- Quick changeovers between different product runs
- Full automation potential for high-volume manufacturing
Start with hot plate welding during early product development, then carry the same reliable joining technology through to full-scale production. You'll maintain consistent performance characteristics while scaling up your manufacturing capacity.
Design Considerations for Hot Plate Welding Success
Creating components that weld perfectly requires attention to key design factors. Follow our expert guide to optimize your parts for flawless thermoplastic welds every time.
Joint Design Fundamentals
Selecting the right joint design directly impacts your welding success. Choose from these proven options based on your specific needs:
- Butt joints offer simplicity and strength for flat surfaces, making them ideal for applications where appearance matters
- Tongue and groove joints enhance alignment and increase weld surface area by up to 30%, significantly boosting bond strength
- Step joints provide superior alignment and prevent excess material (flash) from appearing on visible surfaces
- Energy directors (small triangular ridges) focus heat and melting precisely where needed, improving weld initiation
Base your joint selection on your specific strength requirements, visual needs, and sealing demands. For fluid containers requiring hermetic seals, choose designs that promote complete material fusion across the entire interface.
Critical Fit and Tolerance Factors
Precise part fit dramatically impacts your hot plate welding results. Your components must maintain tight dimensional tolerances for quality welds:
- Even tiny gaps between surfaces can create weak spots or voids in your weld zone
- Uneven contact pressure leads to inconsistent melting and poor bond formation
- Component warpage or distortion can cause misalignment during joining
Industry best practices recommend manufacturing parts with tolerances of ±0.1mm or better for optimal welding. When submitting designs, use standard CAD formats (.STEP, .IGES, or .PAR) with tolerance specifications of 0.1mm or less.
Remember that your fixture design must account for thermal expansion during welding to maintain perfect alignment as materials heat and cool.
Smart Material Selection
Choosing the right materials involves more than just picking a thermoplastic. Consider these crucial factors:
- How your material flows when melted significantly affects weld bead formation and joint quality
- Additives like glass fiber, flame retardants, or colorants can dramatically change welding parameters
- When joining different materials, their melting temperatures should be within 40°C of each other
For best results, talk with material suppliers about grades specifically formulated for welding applications. These specialized materials often deliver much more consistent performance in production environments.
Understanding Thermal Properties
Your material's thermal characteristics directly impact welding success. Each plastic has a specific processing window that requires precise control:
- High-melting materials like nylon or polycarbonate need more heat and exact temperature management
- Low-melting materials like polyethylene require carefully regulated temperatures to prevent degradation
- Thermal conductivity determines how quickly heat moves through your part, affecting melt depth
- Heat capacity influences the energy needed to reach optimal welding temperature
Today's advanced hot plate welding systems feature precision temperature controls that maintain perfect conditions throughout the welding cycle, adapting to different material properties for consistent results.
Geometry and Wall Thickness Optimization
Your component's shape significantly affects hot plate welding outcomes. Consider these design essentials:
- Maintain consistent wall thickness across the weld interface for even melting
- For varying wall thicknesses, include transition features for proper heat distribution
- Eliminate sharp corners or complex geometries near the weld to prevent stress points
- Design adequate structural support around the weld zone to prevent warping during cooling
Industry guidelines typically recommend minimum wall thicknesses of 1.5mm for structural applications. For specialized microwelding needs, advanced equipment can successfully join materials as thin as 0.5mm while maintaining excellent joint integrity.
Innovative Hot Plate Welding Solutions from Dizo
Dizo crafts precision-engineered hot plate welding systems that deliver exceptional results across diverse manufacturing environments. Our 12+ years of specialized experience in thermoplastic joining helps you achieve 0.02mm positional repeatability with full ISO 9283 compliance, ensuring flawless welds even for your most challenging applications.
Expert Hot Plate Welding Consultation Services
Our engineering team works directly with you to optimize your components for successful hot plate welding. We offer:
- Thorough joint design evaluation tailored to your specific performance requirements
- Detailed material compatibility analysis for optimal hot plate welding parameters
- Advanced 3D simulation that identifies potential issues before tooling investment
- Hands-on prototyping support to validate your hot plate welding concepts
By partnering with Dizo early in development, you'll avoid costly redesigns while ensuring your components achieve efficient, high-quality hot plate welds that meet or exceed industry standards.
Free Hot Plate Welding Design Assistance & Custom Solutions
We provide complimentary design guidance and equipment selection to eliminate guesswork from your hot plate welding process. Our ISO 9001 certified technicians help you select the perfect machine calibrated to your product's exact specifications.
From compact CE-certified benchtop systems to fully automated production cells, our hot plate welding solutions deliver outstanding performance for every project size.
Industry-Leading Hot Plate Welding Quality Standards
Our hot plate welding equipment exceeds the highest quality benchmarks, helping you achieve consistent weld strength and perfect appearance across production runs. Every Dizo system features:
- Precision-ground heating plates with temperature uniformity of ±3°C across the entire welding surface
- Advanced PID temperature controllers ensuring stable hot plate welding conditions
- High-precision servo-driven motion systems with 0.02mm repeatability for exact positioning
- User-friendly HMI interfaces with extensive recipe storage for quick project changeovers
Dizo hot plate welding machines process virtually all commercially available thermoplastics while meeting international standards for equipment safety and reliability. All systems come CE certified and are manufactured in our ISO 9001 certified facility.
Comprehensive Hot Plate Welding Support
We support you throughout your hot plate welding journey, from initial consultation through installation and beyond. Our service team includes experienced process engineers who help optimize your welding parameters, troubleshoot challenges, and maximize production efficiency.
With remote diagnostics, rapid response support, and preventive maintenance programs, we ensure your hot plate welding operations maintain peak performance with minimal downtime. Schedule Your Free Hot Plate Welding Audit Today!
Frequently Asked Questions About Hot Plate Welding
What materials work best with hot plate welding?
Hot plate welding excels with a wide range of thermoplastics that soften and flow when heated, including:
- Polyolefins (PP, PE, HDPE, LDPE) - Creating excellent bonds with strong, durable joints
- Engineering plastics (ABS, PC, PMMA, POM) - Delivering high-strength precision welds
- High-performance plastics (PPS, PEEK, PSU) - Perfect for demanding applications requiring temperature resistance
- Specialty blends and filled materials - Though requiring customized parameters
The key requirement is that materials must be thermoplastic rather than thermoset, as thermoplastics can repeatedly soften when heated and harden when cooled. Materials with similar melting points typically create the strongest bonds.
How does Dizo's hot plate welding technology stand out?
We differentiate ourselves in the hot plate welding market through several key advantages:
- Proprietary temperature control systems maintaining ±2°C precision across the entire heating surface
- Custom-engineered solutions designed specifically for your unique application requirements
- Advanced data logging and process monitoring ensuring consistent quality and traceability
- Modular design architecture allowing future upgrades as your production needs evolve
- Comprehensive technical support including material testing, process validation, and operator training
Unlike manufacturers offering only standardized equipment, we collaborate closely with you to develop tailored solutions that optimize welding quality and production efficiency for your specific applications.
How do I weld polypropylene with hot plate welding?
Polypropylene (PP) welds beautifully with hot plate technology. Follow this simplified process:
- Set your hot plate temperature between 190-220°C (depending on your specific PP grade)
- Clean all surfaces before welding to prevent contamination
- Apply consistent pressure (typically 0.2-0.4 MPa) during the melt phase
- Allow sufficient melt depth to develop (typically 1-2mm)
- Join parts quickly after removal from the hot plate (transfer time under 3 seconds)
For optimal results when hot plate welding polypropylene, maintain consistent pressure during cooling until the material fully solidifies. This prevents warping and ensures maximum joint strength.
Can small-scale productions benefit from hot plate welding?
Absolutely! Hot plate welding offers significant advantages for small-scale production and prototyping:
- Lower tooling costs compared to alternative joining methods like ultrasonic welding
- Quick setup and changeover times enabling efficient small batch production
- Affordable benchtop systems perfect for startups and small manufacturers
- Consistent process that scales seamlessly from prototype to full production
- Ability to create functional, test-ready prototypes with production-equivalent joints
We offer entry-level hot plate welding systems specifically designed for R&D labs, educational institutions, and low-volume manufacturers, making this technology accessible while maintaining professional results.
What pressure ranges work best in hot plate welding?
The right pressure settings are critical for achieving optimal joint strength and appearance:
- Melt phase: 0.1-0.5 MPa - Creates sufficient melt without excessive flash
- Joining phase: 0.3-1.0 MPa - Ensures complete fusion when pressing melted surfaces together
- Holding phase: 0.2-0.8 MPa - Maintains dimensional stability during cooling
These values vary based on material properties, part geometry, and application requirements. Our advanced systems feature programmable pressure profiles that automatically adjust throughout the welding cycle for optimal results with complex materials.
What temperature ranges work best for hot plate welding?
Hot plate welding temperatures must match the specific material you're processing:
- Polyolefins (PP, PE): 180-220°C - Perfect for these common materials
- Standard engineering plastics (ABS, PS): 230-260°C - Ideal for everyday technical applications
- High-performance plastics (PC, PEEK): 270-320°C - Required for specialized materials
- Glass-filled or reinforced plastics: Typically need 10-15% higher temperatures than unfilled versions
The best temperature setting is typically 20-40°C above the material's melting point. Our equipment features multi-zone heating technology with independent controllers, allowing precise temperature gradients for complex geometries or material combinations.
How long does a typical hot plate welding cycle take?
Complete hot plate welding cycles typically range from 15 seconds to 2 minutes, consisting of:
- Heat soak: 5-30 seconds - Time parts contact the hot plate to develop adequate melt depth
- Transfer: 1-5 seconds - Critical period when parts move from hot plate to joining position
- Joining/cooling: 5-60 seconds - Time for joined parts to solidify under pressure
Material wall thickness primarily determines cycle time, with thicker sections requiring longer heating and cooling. Our advanced systems offer programmable multi-stage cycles with automatic optimization based on your specific materials and part geometry, maximizing both quality and production efficiency.
How does hot plate welding compare to other welding methods?
When selecting the optimal plastic joining technology, consider these key differences:
Feature |
Hot Plate Welding |
Laser Welding |
Vibration Welding |
Joint Strength |
Excellent (90-100% of parent material) |
Very Good (80-95% of parent material) |
Good (75-90% of parent material) |
Joint Size |
Large areas (>25cm2) |
Precise, thin joints |
Medium to large areas |
Cycle Time |
15-120 seconds |
1-10 seconds |
2-15 seconds |
Equipment Cost |
Moderate |
High |
Moderate to High |
Tooling Cost |
Low |
Moderate |
High |
Material Flexibility |
Most thermoplastics |
Requires material compatibility |
Rigid thermoplastics only |
Visual Appearance |
Visible weld line |
Nearly invisible |
Visible weld line |
Hot plate welding excels with larger joint areas, while ultrasonic welding is typically limited to smaller components. For material compatibility, hot plate welding works with virtually all thermoplastics regardless of stiffness, while ultrasonic requires relatively rigid materials to transmit vibrational energy effectively.
Many manufacturers maintain multiple joining technologies to address different application requirements. Dizo offers comprehensive consulting services to help determine the most appropriate joining technology for your specific project requirements.
Conclusion: The Future of Hot Plate Welding Technology
Hot plate welding continues to evolve as a leading thermoplastic joining technique for challenging manufacturing needs. This reliable process creates exceptionally strong, leak-proof bonds across numerous industries including automotive parts, medical equipment, household appliances, and industrial products.
Are you running a high-volume production line or a small manufacturing facility? Either way, hot plate welding delivers impressive results. The technique offers the perfect balance of efficiency, bond strength, and manufacturing adaptability that modern companies need to stay competitive.
Hot plate welding benefits at a glance:
- Creates joints with 90-100% of parent material strength
- Works with virtually all thermoplastic materials
- Delivers consistent, reliable results across production runs
- Offers cost-effective solutions for various project scales
As new advanced polymers enter the market, Dizo remains at the cutting edge of hot plate welding innovation. Our ongoing research ensures our equipment keeps pace with the latest developments in plastic assembly challenges. This commitment to excellence makes hot plate welding the preferred choice for manufacturers seeking superior joint quality.
Looking ahead, hot plate welding technology shows tremendous promise with advancements in multi-material joining, integrated quality control systems, and energy-efficient heating methods. Therefore, these improvements will further enhance this already versatile plastic welding solution.
Reach out to Dizo today to explore your hot plate welding needs or schedule a demonstration of our state-of-the-art equipment. With over ten years specializing in thermoplastic joining technologies, our experts provide comprehensive guidance and customized hot plate welding solutions for your most challenging plastic assembly projects.