What is standard hot plate welding?
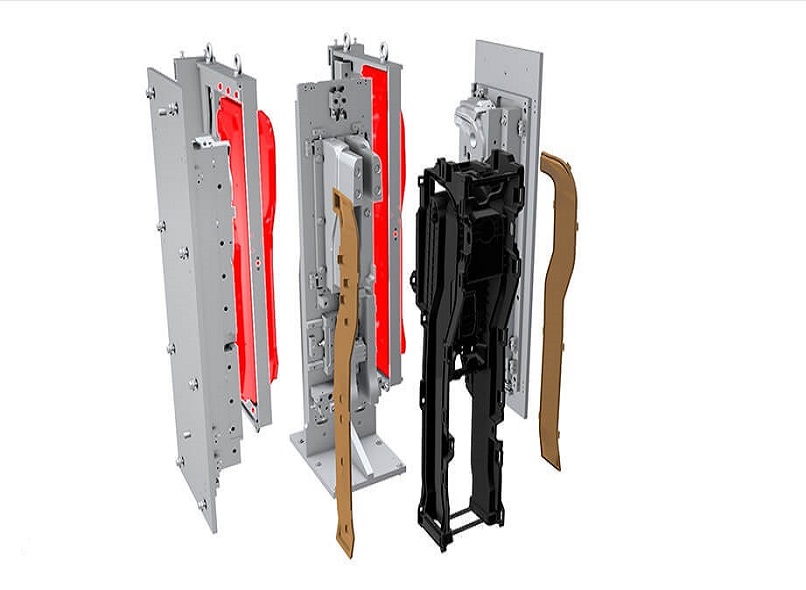
Standard hot plate welding is a widely recognized and extensively utilized technique in the field of plastic welding. It involves the precise application of heat and pressure to join two plastic parts together. The process begins by heating a metal plate to a specific temperature, which is carefully determined based on the type of plastic being welded. Once the desired temperature is reached, the heated plate is placed between the plastic parts, effectively softening the plastic and allowing for fusion under pressure.
The advantages and applications of standard hot plate welding are diverse and significant. One of the key advantages of this method is its ability to join thermoplastics with high melting points. This makes it a preferred choice for applications that require excellent heat resistance, ensuring the durability and reliability of the final product. Moreover, standard hot plate welding is particularly effective for large plastic parts or parts with complex geometries, as the uniform heating provided by the heated metal plate ensures consistent fusion and bonding across the entire surface area.
In the automotive industry, standard hot plate welding plays a crucial role in the production of various plastic components found in vehicle interiors. Dashboards, door panels, and other interior parts often require strong and seamless joints, which can be achieved through hot plate welding. Similarly, in the medical devices sector, standard hot plate welding is employed to assemble critical components such as syringes, surgical instruments, and other plastic medical devices. The reliable and robust bonds created by hot plate welding ensure the safety and effectiveness of these medical products. In the consumer electronics industry, hot plate welding is used to join plastic components in devices like smartphones, tablets, and laptops, providing structural integrity and longevity. Additionally, the packaging industry relies on standard hot plate welding to create secure and airtight seals on plastic packaging materials, ensuring product freshness and safety.
Proper preparation and precise control over the welding parameters are essential for achieving successful results with standard hot plate welding. The plastic parts to be joined must be clean and free of contaminants to ensure optimal bonding. The temperature and pressure must be carefully monitored and controlled to achieve the desired fusion without compromising the structural integrity of the plastic parts. When executed correctly, standard hot plate welding produces joints with outstanding mechanical strength and hermetic seals, meeting the stringent quality requirements of various industries.
It is important to note that advancements and variations in hot plate welding techniques continue to emerge. For instance, infrared heating has been introduced as an alternative to traditional metal plates, offering advantages such as reduced cycle times and increased energy efficiency. This technology enhances the capabilities and flexibility of hot plate welding, allowing for more efficient and sustainable production processes.
In conclusion, standard hot plate welding is a highly effective and versatile technique used in plastic welding. Its ability to join thermoplastics with high melting points and handle large or complex parts makes it indispensable in industries such as automotive, medical devices, consumer electronics, and packaging. By ensuring proper preparation and precise control over welding parameters, standard hot plate welding produces durable and reliable joints, contributing to the overall quality and performance of the final products.