Washing Machine Dispenser Hot Melt Welder: How It Works
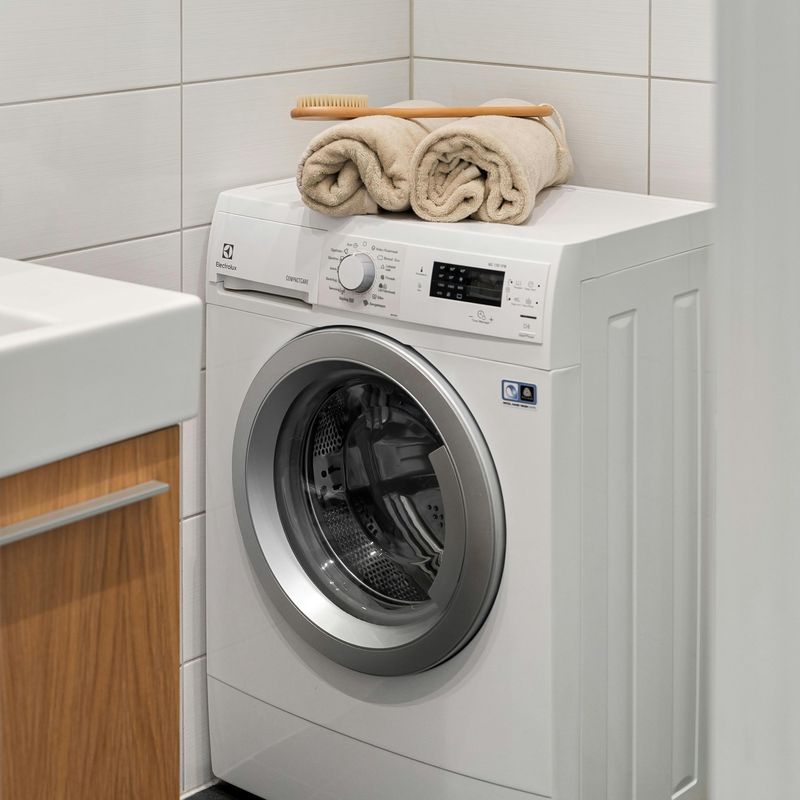
Ever wondered how washing machine dispensers are put together without glue or screws showing? The secret is a tool called a Washing Machine Dispenser Hot Melt Welder. It uses heat to bond parts securely, making them strong and neat.
For plastic parts manufacturers, older bonding methods can be slow and messy. This hot melt welding equipment solves the problem by offering a quick, reliable, clean way to make production easier.
This hot melt welder controls temperature and force to ensure perfect dispenser construction. It removes any openings that might lead to leaks or mechanical damage. This blog will explain what a Dizo Hot Melt Welding Machine is and how it can help with your production issues.
Table of Contents
What is a Washing Machine Dispenser Hot Melt Welder??
How Does a Washing Machine Dispenser Hot Melt Welding Machine Work?
Advantages of Using a Hot Melt Welding Equipment
Applications of a Hot Melt Plastic Welding Machine in the Industry
Why Choose the Dizo Washing Machine Dispenser Hot Plate Plastic Welder?
The Bottom Line- Is it Hype Worthy?
FAQs
What is a Washing Machine Dispenser Hot Melt Welder?
A hot melt welder enables you to load detergent into your washing machine while experiencing flawless functionality since there will be no leaks or cracks. The hero behind this everyday miracle? A hot melt welder.
The high-tech "invisible glue" machine uses precise heat to create unbreakable single pieces from plastic components, which includes your detergent dispenser.
The plastic welder heats plastic edges until they become soft, then uses pressure to join them together. Thus creating a bond that exceeds the strength of the base materials.
A hot plate welder creates an ideal design. It forms welds without screws. It also prevents gaps and mid-cycle soap floods.
The hot melt welding process requires more than simple attachment of objects. The process produces parts designed to withstand constant vibration and rotation while remaining durable even after years of exposure to detergents.
The adhesion technology used in this plastic welding technique wins the love of manufacturers because it delivers quick results while being environmentally friendly and reducing production waste. There are no toxic glues and no fuss, just clean, efficient production.
How Does a Washing Machine Dispenser Hot Melt Welding Machine Work?
The perfect hot plate welding process ensures watertight seals that resist leaking throughout 1,000 washing machine cycles. The detergent components and fabric softeners prove extremely challenging to plastic.
Tide pods cannot harm welded joints that stand strong against traditional glue or screw deterioration. Here is a detailed step-by-step explanation of how the Washing Machine Dispenser hot melt welder operates and how precision hot plate welding occurs:
Step 1: Preparation of Parts
The washing machine dispenser components should be placed into their correct positions before starting. The alignment process holds immense importance since any improper bonds might result from slight misplacement between plastic parts.
The hot melt welding area requires cleaning to eliminate any potential contaminants that would impact the joining process to establish a flawless bond.
Step 2: Application of Heat and Pressure
The hot melt welding machine then uses an advanced heating element to generate intense, controlled heat. This heat is precisely directed to the edges of the parts that need to be joined.
The temperature is carefully calibrated to soften or melt the material without causing damage. Simultaneously, pressure is applied to hold the parts securely in place during the process, ensuring they remain aligned as the material softens. <Learn more tips for plastic welding>
Step 3: Melting and Bonding
The heating process liquefies part edges before an even force applies between surfaces. At this point, the molten materials blend together to form a continuous strong bond with each other.
During the fusion operation, the joint obtains strength that enables durability in washing machine dispenser uses where users handle it regularly while it encounters exposure to water and detergent.
Step 4: Cooling and Hardening
After the plastic parts are fused, the hot melt machine facilitates the cooling process. By allowing the heated material to gradually cool down, the bond hardens into a durable connection.
This cooling phase is critical because it determines the strength and longevity of the bond. The final result is a robust joint that can handle stress and be used regularly without breaking or leaking.
Step 5: Testing and Inspection
Once the hot melt plastic welding process is complete, the final product undergoes thorough testing and inspection. This step ensures the parts are firmly joined and meet high-quality standards.
The bond is checked for strength, alignment, and resistance to wear and tear. Any defects, such as weak spots or misalignments, are identified and corrected before the dispenser moves to the next stage of manufacturing or assembly.
Advantages of Using a Hot Melt Welding Equipment
Let's be honest: traditional bonding approaches lead to numerous efforts for most users. Production speed decreases because messy glues and problematic screws, together with extended drying times, create opportunities for mistakes to happen during manufacturing processes.
The hot plate welder functions as a powerful device that has become the secret force behind modern manufacturing processes. Here are the perks of using the hot plate plastic welding technique:
1. Speed That Doesn't Sacrifice Quality
Hot melt welding equipment boost production speed at an unprecedented pace. These plastic welding machines form instant bonds. A hot plate welder allows you to assemble parts within seconds instead of wasting minutes while it enhances your production line performance significantly.
2. Bonds That Outlast the Competition
Have you encountered product failure from a deteriorated joint? Hot melt welding produces molecular connections and make seamless joints which result in bonds that exceed the strength of individual polymers.
These welds which secure car bumpers as well as washing machine dispensers prove resistant to stress and vibration and daily use.
3. Wallet-Friendly Wins
No more pricey screws, specialty adhesives, or wasted materials. The cost-saving ability of hot plate welding occurs because it streamlines operations and reduces material waste. Even better? Less labor means more savings.
4. Plays well with (Almost) Everything
Different industries pick hot melt welding. It can bond a variety of materials, which makes it very versatile in industrial assembly processes. Plastics, composites, and hybrid materials can all work together as hot melt welders help them fit well.
5. Kind to the Planet
There are no toxic fumes or chemical runoff. The hot melt plastic welding process using hot plate technology results in clean operation with low energy consumption and minimal product waste.
Applications of a Hot Plate Plastic Welding Machine in the Industry
Let's talk about something you use weekly or daily, like your washing machine. The detergent dispensers in washing machines exist because hot plate plastic welding creates a reliable waterproof system that protects them from constant water immersion and hard impacts.
Hot melt welding serves as an understated technology that enables the production of car interiors along with medical devices while also welding detergent dispensers used in washing machines. The technology exists for more applications than washing machines only. It's everywhere:
- Cars: Bonding dashboards, door panels, and even airbag housings.
- Electronics: Sealing smartphone cases and laptop components.
- Medical Equipment: Medical personnel use the technology to construct sterile, airtight equipment like IV pumps.
- Appliances: Fridge shelves, dishwasher parts, and yes, your trusty washing machine's dispenser.
Why Choose the Dizo Washing Machine Dispenser Hot Plate Plastic Welder?
The Dizo Hot Plate Welder changes challenges into trusted results in manufacturing. First, let's talk precision.
The Dizo platic welder adjusts heat levels easily. Its temperature system creates strong bonds that can withstand even a soap-wielding child. Durability? This hot plate welding machine's powerful design allows it to be a production powerhouse. It can run all day without facing any issues.
But here is the kicker: This device reduces power consumption by 20% as it efficiently creates seamless joints. It features flexible materials, can adapt to new design methods, and still meets current construction standards.
The best part is that it's imported PLC programmable microcomputer control systems that ensure easy operation. Modern control systems lower errors and reduce training time. This means more high-quality dispensers are made on your manufacturing line.
The Bottom Line- Is it Hype Worthy?
Hot plate welding machines use exact heat and pressure to bond detergent compartments. This makes them strong and leak-proof for washing machine dispensers. This platic welding technique replaces screws and adhesives.
It creates strong seals, boosts productivity, cuts waste, and supports eco-friendly practices. Thus, the hot plate welder is versatile. Moreover, it works in automotive, electronics, and medical devices. This shows its industrial efficiency.
A high-performance welder, like Dizo Hote Plate Welder, gives you precise results. It uses energy efficiently and works well with modern manufacturing.
Its intuitive design addresses common manufacturing challenges, delivering consistent, high-quality results. Hot plate welding provides manufacturers with an affordable, long-lasting, and sustainable solution for daily routine products.
FAQs
What types of materials can be bonded using a hot plate welder?
Hot plate plastic welding can effectively bond various materials, including plastics, metals, and composites. The key factor is the compatibility of the material with the adhesive used in the process.
Is hot plate welding faster than traditional welding methods?
Yes, hot melt welding is generally faster as it eliminates the need for cooling and solidification time between passes. This leads to increased efficiency and productivity in manufacturing processes.
Why is it important in washing machine production?
This hot plate welding equipment ensures the reliable assembly of washing machine dispensers by creating strong, leak-resistant bonds. It increases the dispenser's quality and longevity, as dispensers frequently come in contact with water, detergents, and daily wear.