Vibration Welding Design Guidelines: Creating Strong and Reliable Bonds
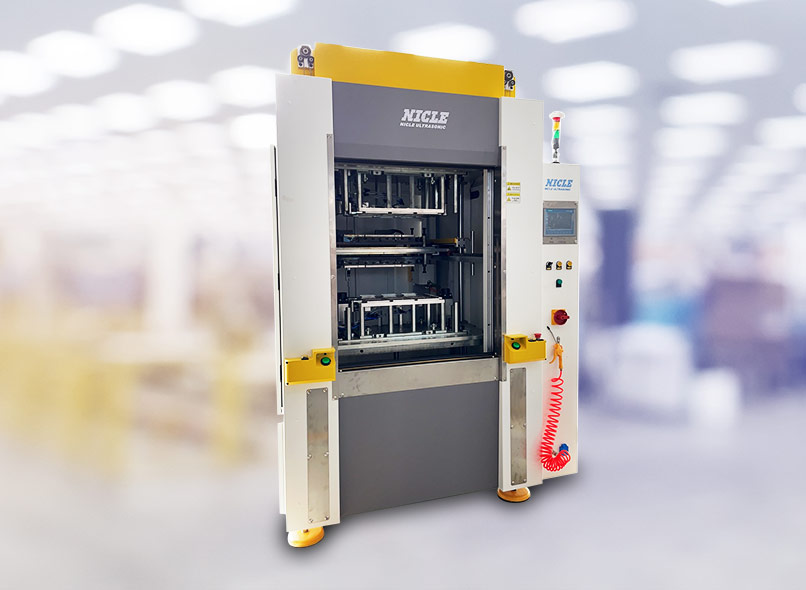
When it comes to joining plastic components, welding is often the preferred method for creating strong and permanent bonds. One such welding technique is vibration welding, which utilizes frictional heat to melt and weld thermoplastic parts together. In this comprehensive guide, we will explore the principles, advantages, and considerations of vibration welding, along with practical design guidelines to ensure successful welds.
The Basics of Vibration Welding
Vibration welding involves the horizontal movement of one plastic part against another under pressure, generating heat through surface friction and creating a molecular bond between the parts. This process operates at lower frequencies, higher amplitudes, and greater clamping force compared to ultrasonic welding. The electromagnetic heads in vibration welding machines eliminate the need for lubrication and reduce wear on bearing surfaces.
Understanding the Vibration Welding Process
The vibration welding process can be divided into several stages: solid friction, transient, steady-state melt flow, and cooling. During the solid friction phase, heat is generated through friction between the surfaces of the parts, eventually reaching the melting point of the polymer. The transient phase involves the melting of the polymer and the formation of a molten layer that links the components. In the steady-state melt flow phase, the molten material flows outward along the seam, resulting in a uniform and stable weld. Finally, during the cooling phase, the molten material solidifies, forming a strong and permanent bond.
Vibration Welding Equipment
To carry out vibration welding, specialized equipment is required. A vibration welder typically consists of a vertical machine press with a moving element and a fixed element. The moving element, known as the vibration head, is driven by hydraulic pistons or electromagnets and delivers the power needed for the frictional welding process. The fixed element, called the lifting table, brings the parts into contact by raising the lower tooling and ensures even pressure is applied during welding. The machine also includes tooling fixtures specific to the application, a sound enclosure, and a control cabinet housing the drive mechanism and electrical system.
Materials Suitable for Vibration Welding
Vibration welding is compatible with a wide range of thermoplastics, including acrylonitrile butadiene styrene (ABS), polyethylene (PE), polypropylene (PP), and polycarbonate (PC), among others. It can also join dissimilar materials with compatible melting points, composite materials, and fabrics. The choice of material depends on factors such as the application, desired strength, and environmental conditions. It is important to consider the type and composition of the material, including any fillers or reinforcements present, to ensure a successful weld.
Design Considerations for Vibration Welding
Proper part and weld design are crucial for achieving strong and reliable vibration welds. The joint design should be tailored to the specific application, taking into account factors such as the type of plastic, part geometry, and weld requirements. The ideal parting line should be parallel to the force applied by the lifting table, and the joint design should allow for sufficient collapse distance to ensure a good weld. It is important to consider joint contours and avoid angles parallel to the direction of vibration, as they may result in weak welds. Additionally, parts should be rigid to prevent distortion during welding, and tall internal walls perpendicular to the vibration direction may require stiffening to ensure proper welding.
Testing and Validation
Before implementing vibration welding in production, it is essential to conduct thorough testing and validation. This includes evaluating weld strength, hermeticity, and dimensional accuracy. Various testing methods can be employed, such as destructive testing, non-destructive testing, and visual inspection. It is recommended to consult with vibration welding experts and perform feasibility studies to ensure the welding process meets the required specifications.
Applications of Vibration Welding
Vibration welding finds applications in various industries, including automotive, aviation, appliances, accessories, and medical. In the automotive sector, vibration welding is used for joining components such as door panels, intake manifolds, instrument panels, and fluid reservoirs. Aviation applications include HVAC ducts, air diverter valves, interior lighting, and overhead storage bins. Appliance manufacturers utilize vibration welding for dishwasher pumps, detergent dispensers, and vacuum cleaner housings. Other applications include chainsaw housings, power tools, surgical instruments, and medical devices.
Process Variants and Alternatives
While vibration welding is a highly effective method for joining thermoplastic parts, it is important to consider alternative techniques for specific applications. Ultrasonic welding, friction welding, laser welding, and hot plate welding are some of the alternatives to vibration welding. Each technique has its advantages and limitations, and the choice depends on factors such as material compatibility, part geometry, and production requirements.
Conclusion
Vibration welding is a reliable and cost-effective method for joining thermoplastic parts, offering numerous advantages such as strong welds, hermetic seals, and quick cycle times. By following proper design guidelines and considering factors such as material compatibility, joint design, and testing, manufacturers can ensure successful and durable vibration welds. Whether in the automotive, aviation, appliance, or medical industry, vibration welding provides a robust solution for creating permanent bonds in plastic components.
Remember to consult with experts in vibration welding and conduct thorough testing to optimize the process for your specific application. With proper design and implementation, vibration welding can revolutionize the production of plastic components, delivering strong and reliable results.