Ultrasonic Welding: Revolutionizing the Packaging Industry
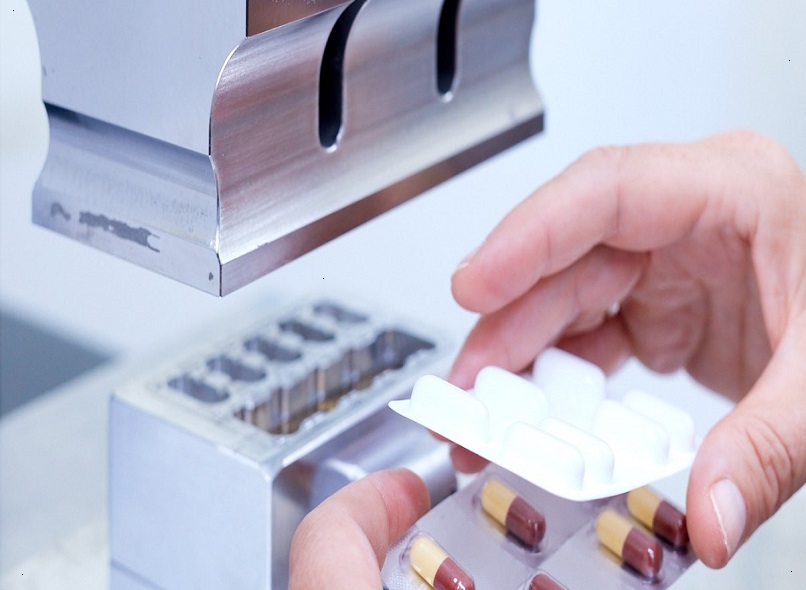
Innovation is driving the evolution of the packaging industry. Cutting-edge technologies continuously reshape the way we package, protect, and present products. Ultrasonic welding is one such technology that has found its way into the packaging industry, revolutionizing the way packages are sealed and offering many benefits. In this article, we explore ultrasonic welding and its applications, advantages, and impact on the packaging industry.
Understanding Ultrasonic Welding
Ultrasonic welding is a solid-state welding process that uses high-frequency ultrasonic vibrations to create a strong molecular bond between two materials. Unlike traditional welding methods that involve melting and fusing materials, ultrasonic welding is a non-destructive technique that works on thermoplastic materials.
The process includes three main components:
- Ultrasonic Welding Machine: This machine contains a transducer and a welding horn. The transducer converts electrical energy into high-frequency mechanical vibrations that are then transferred to the welding horn.
- Welding Horn: The welding horn amplifies the vibrations and applies them to the materials being welded. The horn's design is critical, as it determines the weld's quality.
- Materials: Ultrasonic welding is primarily used for thermoplastic materials. When high-frequency vibrations are applied to these materials, they create friction and heat, causing the materials to fuse together.
Applications in the Packaging Industry
Ultrasonic welding has found numerous applications in the packaging industry, including:
1. Sealing Packaging Materials
Ultrasonic welding is used to seal various types of packaging materials, including blister packs, clamshells, and flexible pouches. The precise control it offers over the sealing process ensures airtight and leak-proof seals, which are crucial for preserving the integrity of products, particularly in the food and pharmaceutical sectors.
2. Tamper-Evident Packaging
Ultrasonic welding is used to create tamper-evident seals that clearly show if a package has been tampered with. This feature is highly valued in industries where product safety is paramount, such as the pharmaceutical and food industries.
3. Custom Packaging Solutions
Ultrasonic welding enables the creation of custom packaging solutions with intricate designs and shapes. This flexibility is especially beneficial for products that require unique packaging, helping them stand out on the shelves and enhancing brand visibility.
4. Reducing Packaging Waste
Efficiency in packaging is a growing concern due to environmental awareness. Ultrasonic welding allows for precise sealing, minimizing excess material, and reducing packaging waste. This aligns with the sustainability goals of many companies and the global trend towards eco-friendly packaging.
5. Inserting Components
Ultrasonic welding can be used to secure components in place effectively, such as desiccants or promotional inserts, ensuring they remain where they are intended to be throughout the product's shelf life.
Advantages of Ultrasonic Welding in Packaging
Ultrasonic welding offers several significant advantages over traditional methods, driving its adoption in the packaging industry:
1. Speed and Efficiency
Ultrasonic welding is a high-speed process that can complete seals in a matter of seconds. This efficiency is invaluable in industries with high production demands, such as food and beverage.
2. No Consumables
Ultrasonic welding does not require consumables like adhesives, tapes, or solvents, unlike adhesive-based sealing methods. This not only reduces ongoing costs but also eliminates the risk of contamination that can occur with adhesive-based sealing.
3. Clean and Eco-Friendly
Ultrasonic welding is a clean process with no emissions of fumes or pollutants. This makes it an environmentally friendly choice and aligns with sustainability goals.
4. Consistent Quality
The precision of ultrasonic welding ensures consistent quality in seals and packaging, reducing the likelihood of defects and product recalls.
5. Tamper-Proof Seals
The tamper-evident seals created through ultrasonic welding provide added security and reassurance to both consumers and manufacturers.
6. Versatility
Ultrasonic welding can be used with a wide range of packaging materials, making it a versatile choice for various industries.
7. Customization
The technology allows for intricate designs and shapes, enabling unique and eye-catching packaging solutions.
Challenges and Considerations
While ultrasonic welding offers numerous benefits, there are some challenges and considerations that need to be addressed:
1. Material Compatibility
Ultrasonic welding works best with thermoplastic materials. Compatibility issues may arise when working with other materials, such as metals or certain types of plastics.
2. Initial Investment
The cost of acquiring and setting up ultrasonic welding equipment can be relatively high. However, the long-term benefits often outweigh the initial investment, especially for high-volume production.
3. Maintenance
Regular maintenance is required to ensure the welding equipment continues to operate efficiently. This includes cleaning the welding horn and checking for wear and tear.
4. Operator Training
Operators need to be trained in using ultrasonic welding equipment effectively to achieve the desired results. Proper training is essential to ensure consistent quality.
5. Design Considerations
Designing packaging for ultrasonic welding may require adjustments to accommodate the welding process. This should be taken into account during the packaging design phase.
Future Trends and Innovations
The packaging industry is continually evolving, and ultrasonic welding is no exception. Here are some future trends and innovations to watch for:
1. Smart Packaging
The integration of sensors and electronics into packaging is on the rise. Ultrasonic welding can play a role in creating these smart packaging solutions, where functionality and aesthetics merge seamlessly.
2. Sustainable Materials
As the world becomes more environmentally conscious, there's a growing demand for sustainable packaging materials. Ultrasonic welding will continue to be instrumental in working with these materials, which may include biodegradable plastics and plant-based alternatives.
3. Robotics and Automation
The use of robotics and automation in packaging is increasing. Ultrasonic welding equipment can be integrated into automated packaging lines, further enhancing efficiency and precision.
4. Nanotechnology
Nanotechnology may find applications in ultrasonic welding, allowing for even more precise and controlled welding processes, especially at the micro-scale.
5. Advanced Quality Control
Advanced quality control systems, including artificial intelligence and machine learning, may be integrated with ultrasonic welding machines to monitor and maintain consistent quality.
Ultrasonic welding has emerged as a game-changer in the packaging industry. Its ability to create strong, efficient, and tamper-proof seals, along with its versatility and environmental friendliness, make it a valuable addition to the packaging process. While there are challenges to consider, the long-term benefits far outweigh the initial investment.
As the packaging industry continues to innovate and prioritize sustainability, ultrasonic welding is expected to play an increasingly prominent role. From smart packaging to sustainable materials, this technology will continue to shape the way we package and present products to consumers, ensuring both functionality and aesthetics are met with precision and efficiency. The future of packaging looks brighter than ever, thanks to ultrasonic welding.