Ultrasonic Welding of Polypropylene: A Comprehensive Guide
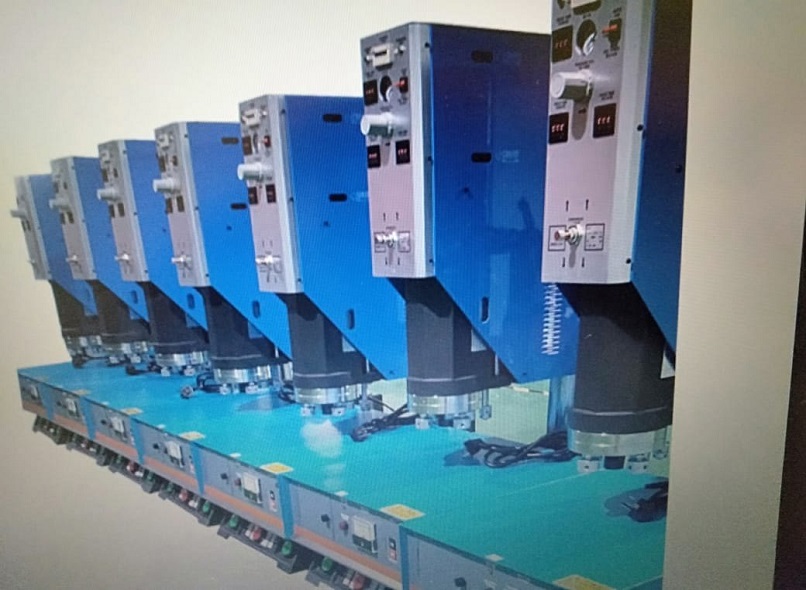
Ultrasonic welding is a highly effective method for joining thermoplastic components. In this guide, we will explore the specific application of ultrasonic welding on polypropylene (PP) materials. Polypropylene is a versatile and widely used thermoplastic known for its excellent chemical resistance, low cost, and high durability. Ultrasonic welding offers numerous advantages for welding polypropylene, but it's important to understand the process, material suitability, and potential challenges.
1. Introduction to Ultrasonic Welding
Ultrasonic welding is a technique used to join thermoplastic components by applying high-frequency mechanical vibrations to the parts. These vibrations generate friction, which creates heat and melts the surfaces in contact. As the melted material cools down, a solid weld joint is formed. The process involves the use of a vibrating metal tool, known as a horn, which is applied at a specific angle to the stationary plastic parts. Ultrasonic welding is widely used in various industries, including automotive, electronics, medical, and packaging.
2. Understanding Polypropylene (PP)
Polypropylene (PP) is a popular thermoplastic material known for its versatility and wide-ranging applications. It is a semi-crystalline polymer with both amorphous and crystalline regions in its molecular structure. Polypropylene offers excellent chemical resistance, high impact strength, and good dimensional stability. It is resistant to moisture, oils, and solvents, making it suitable for a wide range of environments. Polypropylene is commonly used in automotive parts, consumer products, packaging, and medical devices.
3. Advantages of Ultrasonic Welding
Ultrasonic welding offers several advantages for joining polypropylene components:
- Easily Automated Process: Ultrasonic welding can be easily integrated into automated production lines, ensuring consistent and efficient manufacturing.
- Cost-Effective: The process is generally inexpensive compared to other welding methods, making it ideal for high-volume production.
- Quick and Efficient: Ultrasonic welding is a fast process that can be completed in a single operation, saving time and increasing productivity.
- Widely Adopted in Mass Production: Ultrasonic welding is widely used in industries that require the manufacturing of small-scaled components in large quantities.
- No Contaminants: Ultrasonic welding does not introduce contaminants to the weld joints, making it suitable for applications in the medical industry.
- No Welding Fumes: Unlike other welding methods, ultrasonic welding does not produce welding fumes, eliminating the need for additional equipment for fume extraction.