Ultrasonic Welding of Nylon
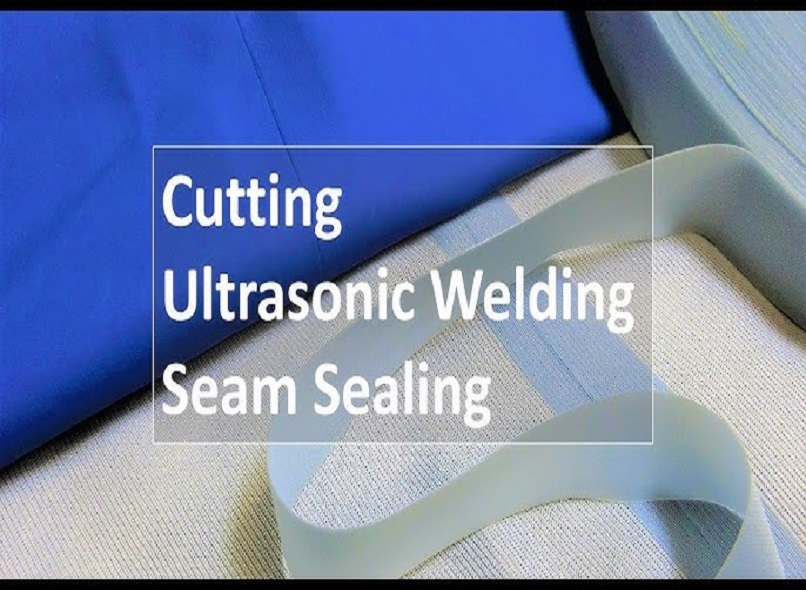
Ultrasonic Welding: A Comprehensive Guide
Ultrasonic welding is an efficient and reliable technique for joining thermoplastic materials. In this guide, we will explore the process of ultrasonic welding nylon, covering material suitability, welding techniques, design considerations, and more. Whether you are new to ultrasonic welding or seeking to enhance your knowledge, this guide will provide you with valuable insights and practical tips.
1. Introduction to Ultrasonic Welding
Ultrasonic welding is a process that utilizes high-frequency mechanical motion to generate heat and join thermoplastic materials. The process involves converting high-frequency electrical energy into mechanical motion, which creates frictional heat at the mating surfaces of the plastic components. This heat causes the plastic material to melt and form a molecular bond between the parts. The entire process is carried out using specialized equipment, including a horn or sonotrode, which applies pressure and energy to fuse the plastic parts together.
Ultrasonic welding offers numerous advantages, including fast and repeatable results, cost-effectiveness, and the elimination of fasteners and adhesives. It simplifies part design, reduces weight and assembly time, and allows for the creation of hermetically tight enclosures. With proper design and execution, ultrasonic welding can ensure strong and durable bonds between nylon components.
2. Material Suitability for Ultrasonic Welding
When considering ultrasonic welding nylon, it is crucial to assess the material's suitability for the process. Nylon is a versatile thermoplastic material that can be effectively welded using ultrasonic techniques. However, it is essential to understand the specific type of nylon being used, as different types may exhibit variations in welding behavior.
Nylon with a more amorphous structure, such as polyphenylene oxide (PPO) and acrylonitrile butadiene styrene (ABS), is generally easier to weld ultrasonically. These materials soften gradually over a temperature range, allowing for efficient welding. On the other hand, semi-crystalline nylons, like polyvinyl chloride (PVC), cellulose acetate (CA/B/P), and polyolefins, may pose challenges due to their narrow glass transition temperature range and limited compatibility with other materials.
It's important to note that ultrasonic welding is most effective when welding similar thermoplastic materials together. Welding dissimilar materials requires careful consideration of factors such as chemical compatibility, melt flow index (MFI), and melt temperatures. Ensuring that the materials being joined have compatible properties will significantly increase the likelihood of successful welds.
3. Techniques for Ultrasonic Welding Nylon
Ultrasonic welding of nylon can be achieved using various techniques, including linear welding, torsional welding, and shear joints. Each technique has its advantages and is suitable for different applications and material combinations.
- Linear Welding: This is the most common method for ultrasonic welding nylon, typically performed at frequencies of 20 kHz or 40 kHz. It involves applying high-frequency vibrations in a linear motion to the plastic parts, creating frictional heat at the joint interface. Through careful design of the joint configuration and the use of energy directors, strong and reliable welds can be achieved.
- Torsional Welding: A less common but highly efficient technique, torsional welding utilizes minimal component stress and is suitable for joining nylon components with complex geometries. By applying high-frequency vibrations in a rotational motion, torsional welding creates frictional heat and promotes molecular bonding between the parts. This technique is particularly advantageous for minimizing stress on delicate or sensitive components.
- Shear Joints: Specifically designed for semi-crystalline materials like nylon, shear joints are used when a traditional energy director is not suitable. Shear joints involve pressing the side walls of opposing parts together, allowing the material to flow and create a strong bond. This technique is particularly useful when joining dissimilar materials or components with limited energy director options.
4. Design Considerations for Ultrasonic Welding
Successful ultrasonic welding of nylon relies heavily on careful design considerations. The joint design plays a critical role in achieving optimal assembly results. Several factors should be taken into account when designing the mating pieces, including the type of plastic, the part's shape, and the requirements of the weld.
A uniform contact area, a small initial contact area, and a means of alignment are the three fundamental requirements in joint design. To concentrate the ultrasonic energy in a small region, incorporating an energy director into the design is crucial. An energy director is a raised region with a triangular cross-section that focuses the frictional heat at specific points.
Various energy director designs can be used, depending on the specific requirements of the application. Common designs include butt joints, step joints, tongue and groove joints, criss-cross joints, and textured surface joints. Each design offers unique advantages in terms of joint strength, alignment, and resistance to flash formation.
5. Advantages and Limitations of Ultrasonic Welding Nylon
Ultrasonic welding nylon offers numerous advantages over other joining methods. It eliminates the need for fasteners and adhesives, reducing assembly time, costs, and the number of components required. The process is fast, repeatable, and reliable, ensuring consistent and high-quality welds. Ultrasonic welding also enables the creation of hermetically tight enclosures, making it suitable for applications requiring air-tight seals.
However, it is important to consider the limitations of ultrasonic welding nylon. The process is most effective for joining thermoplastic materials, and compatibility between the materials is crucial for successful welds. Semi-crystalline nylons may pose challenges due to their limited compatibility with other materials and narrow temperature range for effective welding. Additionally, the geometry and complexity of the parts being joined may impact the feasibility and efficiency of ultrasonic welding.
6. Common Challenges and Troubleshooting Tips
While ultrasonic welding nylon is generally a reliable process, challenges may arise that require troubleshooting and problem-solving. Some common challenges include insufficient joint strength, flash formation, material degradation, and inadequate weld formation.
To address these challenges, several troubleshooting tips can be employed. These include optimizing the welding parameters such as amplitude, pressure, and welding time, ensuring proper alignment and contact between the parts, and carefully selecting compatible materials. Adjusting the design of the energy director, optimizing the cooling time, and identifying and addressing any equipment or tooling issues can also help overcome welding challenges.
7. Applications of Ultrasonic Welding Nylon
Ultrasonic welding of nylon finds applications in various industries. It is commonly used in the automotive sector for joining components such as instrument panels, bumpers, spoilers, and fluid reservoirs. The process is also utilized in the manufacturing of domestic appliances, durable household products, and technical plastics applications.
The ability of ultrasonic welding nylon to create strong and durable bonds makes it suitable for a wide range of applications. It is particularly advantageous in industries where hermetic sealing, reduced assembly time, and cost-effectiveness are essential requirements.
8. Best Practices for Successful Ultrasonic Welding
To ensure successful ultrasonic welding of nylon, several best practices should be followed. These include thorough material compatibility testing, proper cleaning and preparation of the parts, optimization of welding parameters, and regular maintenance and calibration of the ultrasonic welding equipment.
Additionally, ensuring proper joint design, including the use of energy directors or suitable alternative joint configurations, is essential. Conducting thorough process validation and monitoring, as well as implementing quality control measures, can help maintain consistent and reliable welds.
9. Industry Examples and Case Studies
To showcase the practical applications and benefits of ultrasonic welding nylon, let's explore a few industry examples and case studies.
Automotive Industry: In the automotive industry, ultrasonic welding nylon is commonly used for joining instrument panels, bumpers, and fluid reservoirs. The ability to create strong and durable bonds ensures the structural integrity and longevity of these components.
Consumer Goods: Ultrasonic welding nylon is employed in the manufacturing of consumer goods such as household appliances, lawn mowers, and technical plastic products. The process allows for efficient assembly, reduced production costs, and improved product performance.
Case studies illustrating successful ultrasonic welding nylon applications and the resulting benefits will further highlight the practical advantages of this joining method.
10. Conclusion
Ultrasonic welding of nylon offers a reliable and efficient method for joining thermoplastic materials. With proper design considerations, material compatibility, and adherence to best practices, ultrasonic welding can provide strong and durable bonds, reducing assembly time, costs, and the need for additional fasteners or adhesives.
By understanding the process, material suitability, design considerations, and troubleshooting techniques, manufacturers can harness the full potential of ultrasonic welding nylon in various industries. Whether in automotive, consumer goods, or other applications, ultrasonic welding offers a versatile and cost-effective solution for joining nylon components.
With this comprehensive guide, you are now equipped with the knowledge and insights to implement ultrasonic welding nylon effectively and optimize your assembly processes. Embrace the benefits of ultrasonic welding and unlock new possibilities in joining thermoplastic materials.
See more ultrasonic sealing