Ultrasonic Welding: Joining Different Plastics
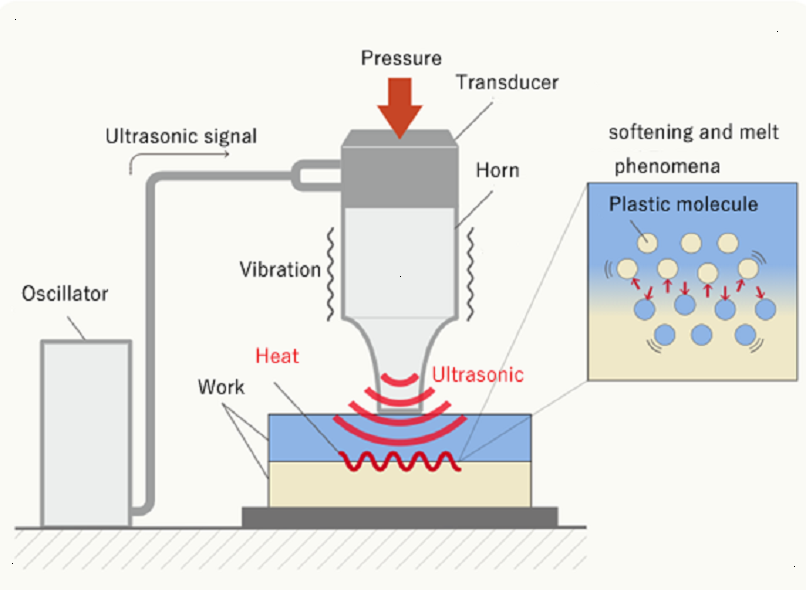
Ultrasonic welding is a very effective technique for connecting plastic parts, offering quick, cost-efficient, and dependable outcomes. By establishing robust molecular bonds between thermoplastic materials, ultrasonic welding presents several advantages compared to traditional bonding methods. One notable advantage is its flexibility in joining various plastics together, enabling the assembly of components made from different materials. This article will examine the ultrasonic welding process and delve into the specific factors to consider when welding different types of plastics.
Understanding Ultrasonic Welding Technology
Ultrasonic welding is a process that uses high-frequency mechanical motion to generate heat energy, creating a strong bond between plastics. This is achieved by exposing the plastic parts to high-frequency vibrations produced by an ultrasonic system. The vibrations are then transferred to a welding tool, called a sonotrode or horn, which applies pressure to the parts. As a result of the friction caused by the vibrations, heat is generated at the joint interface, causing the plastic to melt and form a molecular connection. The process is rapid, with welding times usually measured in fractions of a second.
The Suitability of Different Plastics for Ultrasonic Welding
Not all plastics are equally suitable for ultrasonic welding. The weldability of a plastic material depends on its thermal conductivity, rigidity, and elasticity. Thermoplastic materials are the most compatible with ultrasonic welding because they can be melted and solidified repeatedly without compromising their molecular structure. Among thermoplastics, amorphous materials are particularly well-suited for ultrasonic welding due to their gradual softening and melting behavior over a temperature range.
However, when it comes to joining different plastics, there are certain considerations to keep in mind. While dissimilar plastics generally cannot be successfully welded together, there are exceptions to this rule. For example, plastics with similar glass transition temperatures (Tg) and chemical compatibility can be welded together. One common example is the welding of PMMA (polymethylmethacrylate) to ABS (acrylonitrile butadiene styrene) because both materials are amorphous and possess similar Tg values.
Welding Different Types of Plastics
Thermoplastics: The Ideal Candidates
Thermoplastic materials are extensively used in ultrasonic welding because they can be melted and solidified repeatedly. They provide various options for joining different plastics. Some commonly welded thermoplastics include ABS, PC, PP, PE, PVC, PMMA, and POM. These materials possess favorable welding characteristics and can be reliably joined using ultrasonic welding techniques.
Elastomers and Resins: Limited Weldability
Elastomers and resins, however, do not have a strong compatibility with ultrasonic welding. Elastomers, known for their elastic properties, are generally not recommended for ultrasonic welding because they are difficult to weld. Resins, including amorphous and crystalline types, also have different levels of weldability. Amorphous resins like ABS and PMMA can be welded effectively, but crystalline resins need higher energy levels and more intricate joint designs for successful welding.
Joining Dissimilar Plastics
Joining two different plastics through ultrasonic welding is feasible with specific requirements. Key factors for a successful weld include similarity in Tg values and chemical compatibility. For example, ABS can be welded to acrylic or polycarbonate due to their compatible properties. However, it is worth noting that semi-crystalline plastics typically only allow welding with similar materials, which restricts the possibilities of joining dissimilar plastics.
Factors Affecting Ultrasonic Weldability
Several factors can affect the weldability of plastics in ultrasonic welding processes. These factors include additives, moisture content, and the presence of glass fibers or beads. Additives, such as fire retardants, can influence the weldability of plastics by impacting their degradation and processing properties. Moisture content, especially in polyamides, can result in the formation of gas bubbles and porous weld joints. The incorporation of glass fibers or beads can enhance the stiffness, toughness, and strength of plastics, thereby improving sound conductivity and weldability in semi-crystalline materials.
Joint Design Considerations
Effective joint design is essential for achieving the best results in ultrasonic welding. The design of the joint depends on factors such as the type of plastic, the shape of the parts, and the requirements of the weld. There are several commonly used joint designs in ultrasonic welding, each with its own advantages. These designs include butt joints, step joints, tongue and groove joints, shear joints, and criss-cross joints. The selection of the joint design depends on factors such as the type of plastics being welded, the desired strength of the weld, and the need for alignment and sealing.
Advantages and Disadvantages of Ultrasonic Welding Different Plastics
Ultrasonic welding offers many advantages for joining different plastics. The technology is fast, cost-effective, and reliable, resulting in strong and clean welds. By eliminating the need for fasteners or adhesives, ultrasonic welding simplifies part design and reduces assembly time and costs. Additionally, this process is more environmentally friendly compared to other bonding methods.
However, there are some limitations to consider when welding different plastics using ultrasonic welding. The power requirements may significantly increase when welding thicker or harder plastic parts, which can raise manufacturing costs. Certain plastics, such as semi-crystalline materials, may require more complex joint designs and higher energy levels for successful welding. The capabilities of the ultrasonic welding system may also limit the joint form and size range.
Conclusion
Ultrasonic welding is a flexible and efficient method for joining different plastics. By utilizing high-frequency vibrations and frictional heat, ultrasonic welding forms strong molecular bonds between thermoplastic materials. While not all plastics are equally suitable for ultrasonic welding, careful examination of material properties, joint design, and process parameters can ensure successful welds. With its advantages of speed, cost-effectiveness, and reliability, ultrasonic welding is widely utilized in various industries for joining plastic components. By comprehending the principles and considerations of ultrasonic welding, manufacturers can utilize this technology to achieve high-quality, durable, and efficient plastic assemblies.
See more ultrasonic welding diagram