Ultrasonic Welding for Optical Fiber Spool: Revolutionizing Composite Manufacturing
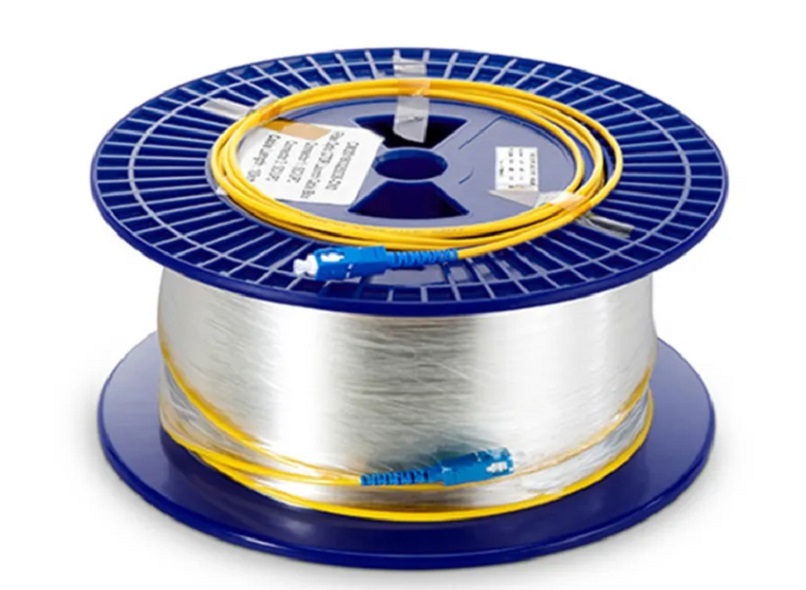
In the world of composites, fiber reinforced plastics (FRP) have gained immense popularity for their exceptional strength-to-weight ratio and versatility. Among the various types of FRP, the use of ultrasonic welding technology has revolutionized the fabrication of optical fiber spools. By combining thermoplastic or thermoset polymers with carbon or glass fibers, manufacturers can create lightweight, durable, and high-performance composite materials. This article explores the process of ultrasonic welding for optical fiber spools, its advantages, applications, and the future of this technology.
Understanding Ultrasonic Welding
The Basics of Ultrasonic Welding
Ultrasonic welding is a well-established technique used in industrial applications for welding, deforming, and joining thermoplastic polymer materials. The process utilizes high-frequency mechanical vibrations to generate heat, which then softens the materials and allows them to fuse together. Ultrasonic welding offers several advantages over traditional welding methods, including faster cycle times, energy efficiency, and the ability to join dissimilar materials.
Ultrasonic Welding of Fiber Reinforced Plastics
The application of ultrasonic welding in the fabrication of fiber reinforced plastics (FRP) has gained significant attention. FRP composites, such as carbon fiber reinforced plastics (CFRP) and glass fiber reinforced plastics (GFRP), offer exceptional strength and durability. By employing ultrasonic welding, manufacturers can create composite materials with precise fiber orientation and enhanced mechanical properties.
Advantages of Ultrasonic Welding for Optical Fiber Spools
Ultrasonic welding for optical fiber spools offers numerous advantages that make it an attractive choice for composite manufacturers. Let's explore some of these key benefits:
1. Lightweight and High-Strength
One of the main advantages of using ultrasonic welding for optical fiber spools is the ability to create lightweight components without compromising strength. CFRP, in particular, exhibits a tensile strength-to-density ratio that is more than four times higher than that of steel. By replacing traditional materials with CFRP, manufacturers can significantly reduce the weight of components while maintaining mechanical resilience.
2. Enhanced Design Flexibility
Ultrasonic welding allows for greater design flexibility in the fabrication of optical fiber spools. The process enables the joining of intricate shapes and complex geometries, opening up new possibilities in component design. Manufacturers can create customized logos, packaging, and graphic designs, providing a unique identity to their products.
3. Efficient Production Process
With ultrasonic welding, the production process for optical fiber spools becomes highly efficient. The cycle time for this process is typically just a few seconds, resulting in faster production rates and increased productivity. Additionally, the required investment costs for ultrasonic welding equipment are relatively low compared to other manufacturing methods.
4. Energy Efficiency
Compared to traditional fabrication processes for CFRP, ultrasonic welding consumes significantly less energy. The localized heating of the material during the ultrasonic welding process minimizes energy waste. This energy-efficient characteristic makes ultrasonic welding an environmentally friendly choice for composite manufacturing.
5. Cost-Effective Solution
While CFRP may have higher material costs compared to traditional materials, the overall cost-effectiveness of using ultrasonic welding for optical fiber spools is undeniable. The weight reduction achieved with CFRP can lead to substantial savings in transportation costs. Moreover, the ability to repair and recycle CFRP components reduces long-term maintenance expenses.
Applications of Ultrasonic Welding for Optical Fiber Spools
The application of ultrasonic welding for optical fiber spools extends to various industries where lightweight, high-strength, and durable components are essential. Let's explore some of the key applications of this technology:
1. Aerospace Industry
The aerospace industry has been at the forefront of utilizing ultrasonic welding for optical fiber spools. CFRP components offer significant weight savings and high mechanical performance, making them ideal for aircraft structures. Ultrasonic welding enables the fabrication of complex aerospace components, such as fuselages, wings, and interior fittings, with precision and efficiency.
2. Automotive Industry
In the automotive industry, the demand for lightweight materials has increased due to the emphasis on fuel efficiency and reduced emissions. Ultrasonic welding for optical fiber spools allows manufacturers to produce lightweight and strong components for vehicles, including body panels, chassis parts, and interior components. The use of CFRP in automobiles improves fuel economy and enhances overall vehicle performance.
3. Renewable Energy Sector
The renewable energy sector, particularly wind energy, has seen a rise in the application of ultrasonic welding for optical fiber spools. Composite materials, such as CFRP, are used in the production of wind turbine blades to withstand the harsh environmental conditions. Ultrasonic welding ensures the integrity and strength of the blade components, contributing to the efficient generation of renewable energy.
4. Medical Equipment
In the medical industry, ultrasonic welding has found applications in the fabrication of lightweight and durable components for medical equipment. From surgical instruments to prosthetics, CFRP components offer enhanced strength and stability. Ultrasonic welding enables the precise assembly of these components, ensuring their reliability and longevity.
Future Developments and Innovations
The field of ultrasonic welding for optical fiber spools is continuously evolving, with ongoing research and development activities aimed at further enhancing the technology. Here are some of the potential future developments and innovations in this field:
1. Advanced Material Combinations
Researchers are exploring the use of different fiber materials, such as carbon and glass fibers, in combination with various thermoplastic polymers. By optimizing the material combinations, manufacturers can tailor the mechanical properties of the composite to specific applications. This flexibility opens up new possibilities for lightweight and high-performance components.
2. Continuous Ultrasonic Fabrication
Efforts are being made to develop continuous ultrasonic fabrication processes for optical fiber spools. This approach eliminates the need for semi-finished CFRP products, streamlining the manufacturing process and reducing material waste. Continuous fabrication enables high-volume production and offers cost advantages, making it an attractive prospect for composite manufacturers.
3. Improved Process Efficiency
Researchers are working on optimizing process parameters and equipment designs to further improve the efficiency of ultrasonic welding for optical fiber spools. This includes advancements in ultrasonic frequency, amplitude control, and tooling designs. By fine-tuning these factors, manufacturers can achieve higher production rates and improved product quality.
4. Recycling and Sustainability
The issue of recycling and sustainability is gaining attention in the field of composite manufacturing. Efforts are being made to develop recycling methods for CFRP components fabricated using ultrasonic welding. By enabling the recycling of composite materials, manufacturers can reduce waste and environmental impact, making the technology more sustainable.
Conclusion
Ultrasonic welding for optical fiber spools has revolutionized the field of composite manufacturing. This technology offers numerous advantages, including lightweight and high-strength components, enhanced design flexibility, and cost-effectiveness. The applications of ultrasonic welding range from aerospace and automotive industries to renewable energy and medical equipment. With ongoing research and development, the future of ultrasonic welding for optical fiber spools looks promising, with advancements in material combinations, continuous fabrication, process efficiency, and sustainability. As this technology continues to evolve, it will play a crucial role in shaping the composite industry and driving innovation.