Ultrasonic Welding Energy Director: A Comprehensive Exploration
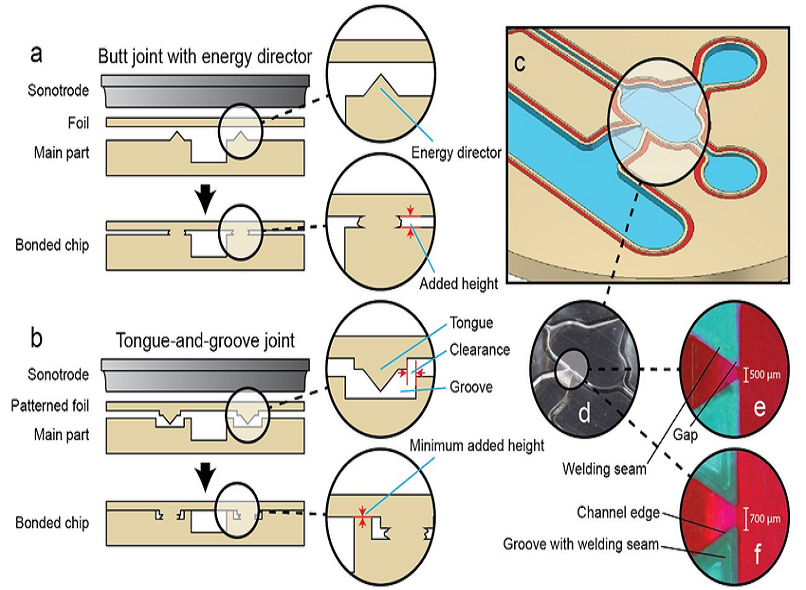
Ultrasonic welding is a widely used technique in the manufacturing industry for joining plastic parts. It offers numerous advantages, including fast cycle times, strong welds, and the ability to weld a wide range of plastic materials. One crucial design feature in ultrasonic welding is the energy director. In this article, we will delve into the concept of an energy director in ultrasonic welding, exploring its purpose, design considerations, advantages, and applications.
Understanding Ultrasonic Welding
Before diving into the specifics of the energy director, let's first understand the basics of ultrasonic welding. Ultrasonic welding is a joining technique that utilizes high-frequency vibrations to create frictional heat at the joint interface, causing the plastic to melt and form a bond. The key components of an ultrasonic welding system include a power supply, a transducer, a horn, and an anvil.
When the power supply generates high-frequency electrical energy, it is converted into mechanical vibrations by the transducer. These vibrations are then transmitted to the horn, which amplifies and focuses them onto the joint area. The anvil provides support and pressure to hold the parts together during the welding process.
The Role of an Energy Director
An energy director is a design feature incorporated into the plastic parts to be welded. Its primary function is to concentrate and direct the ultrasonic energy to the desired welding location. By doing so, it facilitates the melting of the plastic and enables the formation of a strong and reliable weld.
The energy director acts as a sacrificial material, absorbing the energy and heating up quickly. This localized heating creates a melting zone at the joint interface, allowing the two parts to fuse together. The shape, size, and location of the energy director play a crucial role in the weld quality and strength.
Design Considerations for Energy Directors
To ensure successful ultrasonic welding, careful consideration must be given to the design of the energy director. Several factors come into play when determining the optimal shape, size, and location of the energy director. Let's explore some of these design considerations:
1. Shape:
Energy directors are commonly triangular or trapezoidal in shape. This geometry allows for efficient energy transfer and optimal melting of the plastic. The specific shape chosen depends on the application and the materials being welded.
2. Size:
The height, width, and length of the energy director are critical factors in achieving a strong and consistent weld. The height should be at least half the thickness of the thinnest section of the part, while the length should be at least twice the height. These dimensions ensure sufficient energy absorption and create a well-defined melting zone.
3. Location:
The positioning of the energy director is crucial for effective energy transfer and weld strength. It should be placed in a location that allows for maximum energy concentration at the joint interface. Additionally, the energy director should be free from any defects or voids that could weaken the weld.
Advantages of Energy Directors
Energy directors offer several advantages over other types of plastic welding techniques. Let's explore some of these advantages:
1. Consistent Weld Quality:
Energy directors provide a consistent and reliable weld, with minimal variation from part to part. This consistency is particularly important in high-volume manufacturing environments, where precision and repeatability are key.
2. Faster Cycle Times:
Due to the concentrated energy transfer, energy directors enable faster melting and cooling of the plastic. This results in shorter cycle times, increasing productivity and reducing manufacturing costs.
3. Minimal Flash:
Flash refers to excess material that is produced during the welding process. Energy directors help reduce the formation of flash, resulting in cleaner and more aesthetically pleasing welds.
4. Versatility:
Energy directors can be used to weld a wide variety of plastic materials, including those that are typically difficult to bond using other methods. This versatility makes them an ideal choice for various applications and industries.
Applications of Energy Directors
Energy directors find applications in numerous industries where ultrasonic welding is employed. Some notable applications include:
1. Automotive Industry:
Energy directors are used in the assembly of automotive components such as interior trim, door panels, and electrical connectors. They ensure secure and reliable connections, even in demanding automotive environments.
2. Medical Devices:
In the medical industry, energy directors play a vital role in joining plastic components of medical devices. The high precision and strength of the welds are crucial for ensuring the safety and effectiveness of medical equipment.
3. Consumer Electronics:
Energy directors are utilized in the assembly of consumer electronic products, including mobile phones, laptops, and household appliances. They provide strong and durable connections, ensuring the longevity of the devices.
4. Packaging Industry:
In the packaging industry, energy directors are employed to join plastic packaging components, such as blister packs and clamshell packaging. The precise and reliable welds ensure product integrity and security.
Conclusion
In conclusion, the energy director is a critical design feature in ultrasonic welding. It plays a vital role in focusing and directing the ultrasonic energy to the desired welding location, facilitating the formation of strong and durable welds. Energy directors offer numerous advantages, including consistent weld quality, faster cycle times, and versatility in joining a wide range of plastic materials. Their applications span across various industries, contributing to the assembly of automotive components, medical devices, consumer electronics, and packaging materials. As ultrasonic welding continues to evolve, energy directors remain an essential element in ensuring the efficiency and effectiveness of the process.