Ultrasonic Welding Copper Wire
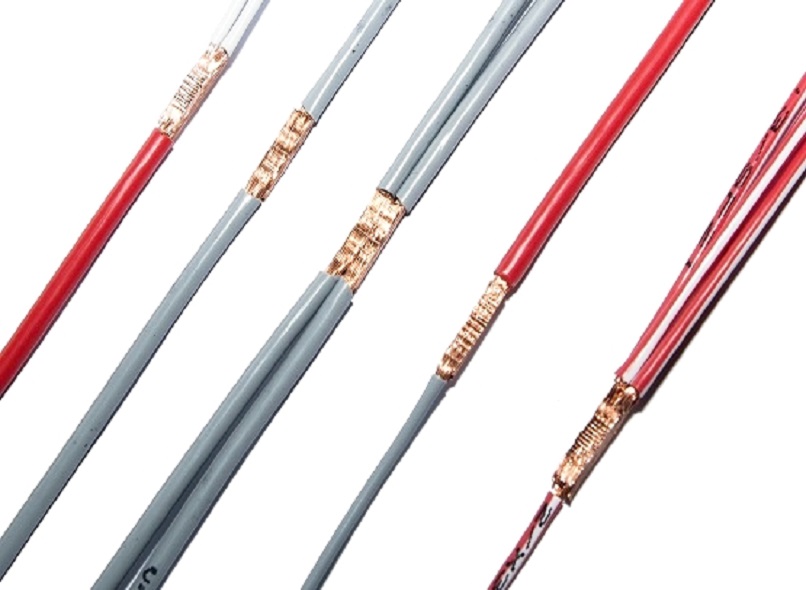
Ultrasonic welding has become a widely used technique for joining copper wires in different industries. This advanced technology provides several advantages compared to traditional welding methods like crimping or resistance welding. In this article, we will delve into the process of ultrasonic welding copper wire, its applications, benefits, and the tools utilized for this purpose.
What is Ultrasonic Welding?
Ultrasonic welding is a method that utilizes high-frequency vibrations to generate heat and establish a solid-state bond between two materials. When it comes to copper wire, ultrasonic welding enables the combination of multiple wires or the connection of wires with terminals or conductive contacts. This technique provides numerous benefits, including top-notch weld joints, precise control over the process, and energy efficiency.
Advantages of Ultrasonic Welding Copper Wire
Ultrasonic welding of copper wire offers several advantages that make it a preferred choice in various industries. Let's explore some of the key benefits:
- High-Quality Weld Joints: Ultrasonic welding creates strong, surface molecular bonds that result in high-quality weld joints. These bonds ensure excellent electrical conductivity and durability.
- Process Control: Ultrasonic welding allows for precise control over the welding process, ensuring consistent and reliable results. The parameters such as pressure, amplitude, and duration can be adjusted to achieve the desired weld quality.
- Energy Efficiency: Compared to traditional welding methods, ultrasonic welding consumes significantly less energy. This makes it a more environmentally friendly and cost-effective option.
- No Additional Materials Required: Unlike other welding techniques, ultrasonic welding of copper wire does not require additional materials such as flux or solder. This simplifies the welding process and reduces material costs.
- Versatility: Ultrasonic welding can be used to join various types of copper wires, including tinned copper wires and bare copper wires. This versatility makes it suitable for a wide range of applications.
Applications of Ultrasonic Welding Copper Wire
Ultrasonic welding of copper wire has a wide range of applications across various industries. Some of the main areas where this technique is utilized include:
1. Automobiles
In the automotive industry, ultrasonic welding is commonly used for wire harness assembly. Wire harnesses are utilized to connect electrical components in vehicles, and ultrasonic welding guarantees dependable and long-lasting connections. As the number of electrical components in automobiles continues to rise, there is an increasing demand for ultrasonic welding in this industry.
2. Electronics
Ultrasonic welding is also used in the electronics industry for producing electronic devices and appliances. It allows for the reliable joining of copper wires, ensuring effective electrical conductivity. From home appliances to office automation equipment and communication devices, ultrasonic welding plays an important role in the manufacturing process.
3. Aerospace
The aerospace industry relies on dependable and long-lasting connections for electrical systems. Ultrasonic welding of copper wire offers the required strength and conductivity for wiring applications in aircraft. This technology guarantees the integrity of electrical connections, which enhances the overall safety and performance of aerospace systems.
4. Manufacturing
Ultrasonic welding is widely used in the manufacturing sector for wire assembly and component integration. It is applied in factory automation equipment, where reliable connections are essential for efficient operation. The use of ultrasonic welding for copper wire allows for the smooth integration of components, improving overall manufacturing productivity.
5. Medical Equipment
The medical industry depends on accurate and efficient electrical connections in different medical devices and equipment. Ultrasonic welding of copper wire guarantees the dependability and safety of these connections. Medical equipment manufacturers utilize this technology to achieve superior welds in important applications.
Ultrasonic Welding Tools for Copper Wire
To perform ultrasonic welding of copper wire, specialized tools are required. These tools are designed to deliver precise vibrations and control the welding process effectively. Let's explore some of the commonly used ultrasonic welding tools for copper wire:
- Ultrasonic Wire Splicers: Ultrasonic wire splicers are specifically designed for joining copper wires. These tools generate high-frequency vibrations that create a solid-state bond between the wires. The resulting weld joint exhibits excellent electrical conductivity and durability.
- Welding Machines: Ultrasonic welding machines are used for larger-scale applications where multiple wires or components need to be joined. These machines provide the necessary power and control to perform ultrasonic welding effectively.
- Process Controllers: Process controllers play a crucial role in ultrasonic welding. They allow for precise adjustment of welding parameters, such as pressure and amplitude, ensuring optimal weld quality and process control.
- Sonotrodes: Sonotrodes are essential components of ultrasonic welding tools. They transmit vibrations to the copper wires, facilitating the welding process. Sonotrodes come in various shapes and sizes to accommodate different wire sizes and configurations.
Conclusion
Ultrasonic welding of copper wire provides several benefits in terms of weld quality, process control, energy efficiency, and versatility. This advanced technology is used in various industries, including automotive, electronics, aerospace, manufacturing, and medical equipment. By using the appropriate ultrasonic welding tools, one can achieve reliable and long-lasting connections, ensuring the efficient functioning of electrical systems. Embracing ultrasonic welding of copper wire opens up opportunities for innovative applications and improves the overall productivity and reliability across different industries.
See more application of ultrasonic welding