Ultrasonic Welding Boosters: Enhancing Efficiency and Precision in Plastic Joining
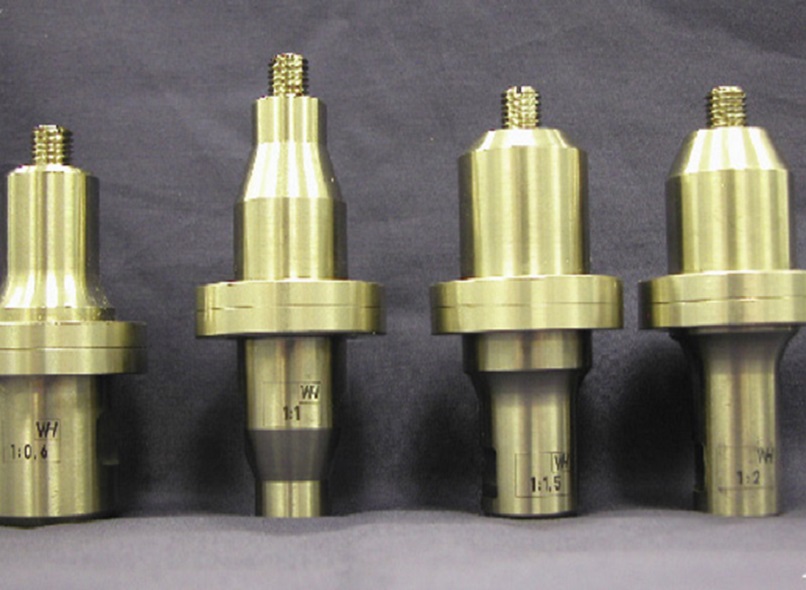
Ultrasonic welding is a cutting-edge technology that has revolutionized the field of plastic joining. This technique utilizes high-frequency ultrasonic vibrations to bond plastic materials together, eliminating the need for adhesives or external heat sources. At the heart of the ultrasonic welding process is the ultrasonic welding booster, a crucial component that amplifies and transmits vibrations from the ultrasonic transducer to the horn. In this article, we will explore the role of ultrasonic welding boosters in enhancing the efficiency and precision of plastic joining operations.
Understanding Ultrasonic Welding
Before delving into the specifics of ultrasonic welding boosters, let's first understand the basics of the ultrasonic welding process. Ultrasonic welding involves the application of high-frequency vibrations to the contact surfaces of plastic parts. These vibrations create frictional heat, softening the plastic materials and allowing them to fuse together under pressure. The result is a strong and seamless bond.
The Importance of Ultrasonic Welding Boosters
Ultrasonic welding boosters play a crucial role in the ultrasonic welding process. They are designed to amplify and focus the mechanical vibrations produced by the transducer, ensuring optimal energy transfer to the horn. By increasing the gain of the system, ultrasonic welding boosters enhance the efficiency and effectiveness of the welding process. However, it is important to strike the right balance, as excessive gain can lead to damage or deformation of the parts being welded.
The Function of Ultrasonic Welding Boosters
The primary function of an ultrasonic welding booster is to transmit amplified vibrations from the transducer to the horn. The booster is typically attached to the transducer and the horn using threaded attachments. It is important to select the appropriate booster geometry and material for each specific application, considering factors such as the materials being welded, the frequency of the ultrasonic vibration, and the size and shape of the horn.
Different Types of Ultrasonic Welding Boosters
Ultrasonic welding boosters come in a variety of shapes and sizes, with different materials used depending on the application requirements. Common materials for boosters include aluminum, titanium, and steel. The choice of booster material depends on factors such as the desired amplitude, durability, and compatibility with the welding environment. Manufacturers often provide a range of booster options to accommodate various welding needs.
Optimizing Ultrasonic Welding Boosters
To achieve optimal performance, it is essential to carefully optimize the ultrasonic welding booster. Factors such as booster geometry, material selection, and gain adjustment should be considered during the setup and calibration process. The goal is to ensure that the booster effectively amplifies the vibrations while maintaining the structural integrity of the welding system. This optimization process may involve fine-tuning the booster dimensions, experimenting with different materials, and adjusting the gain settings.
Advantages of Using Ultrasonic Welding Boosters
The use of ultrasonic welding boosters offers several advantages in plastic joining operations. Here are some key benefits:
- Enhanced Energy Transfer: Ultrasonic welding boosters increase the energy transfer from the transducer to the horn, resulting in improved welding efficiency and stronger welds.
- Increased Welding Speed: By optimizing the gain of the system, ultrasonic welding boosters enable faster welding cycles, leading to increased productivity.
- Improved Weld Quality: The precise amplification and transmission of vibrations by the booster contribute to consistent and reliable weld quality, reducing the risk of defects or weak joints.
- Versatility: Ultrasonic welding boosters can be customized and tailored to specific applications, accommodating a wide range of materials, joint designs, and welding requirements.
- Cost Savings: The enhanced efficiency and reliability provided by ultrasonic welding boosters can lead to cost savings by reducing the need for rework, minimizing material waste, and improving overall production efficiency.
Maintenance and Care of Ultrasonic Welding Boosters
Proper maintenance and care are essential for ensuring the longevity and optimal performance of ultrasonic welding boosters. Here are some key considerations:
- Regular Inspection: Inspect the booster for any signs of wear, damage, or corrosion. A visual inspection can help identify any issues that may affect the booster's performance.
- Cleaning: Keep the booster clean and free from debris or contaminants. Regular cleaning using appropriate methods and cleaning agents can help maintain the booster's functionality.
- Lubrication: If necessary, apply a suitable lubricant to the booster's threaded attachments to ensure smooth and secure connections.
- Calibration: Periodically calibrate the ultrasonic welding system, including the booster, to ensure accurate and consistent performance. Consult the manufacturer's guidelines for proper calibration procedures.
- Replacement: If the booster shows signs of significant wear or damage that cannot be repaired, it may be necessary to replace it. Consult with the manufacturer or a qualified technician for guidance on selecting and installing a new booster.
Conclusion
Ultrasonic welding boosters play a critical role in enhancing the efficiency and precision of plastic joining operations. By amplifying and transmitting vibrations from the transducer to the horn, these boosters optimize energy transfer and improve welding performance. With their ability to increase welding speed, improve weld quality, and offer versatility, ultrasonic welding boosters are indispensable tools in the field of plastic joining. By following proper maintenance and care practices, manufacturers can ensure the longevity and optimal performance of these essential components.