Ultrasonic Plastic Welding: Supermarket Electronic Anti-Theft Buckle Welding
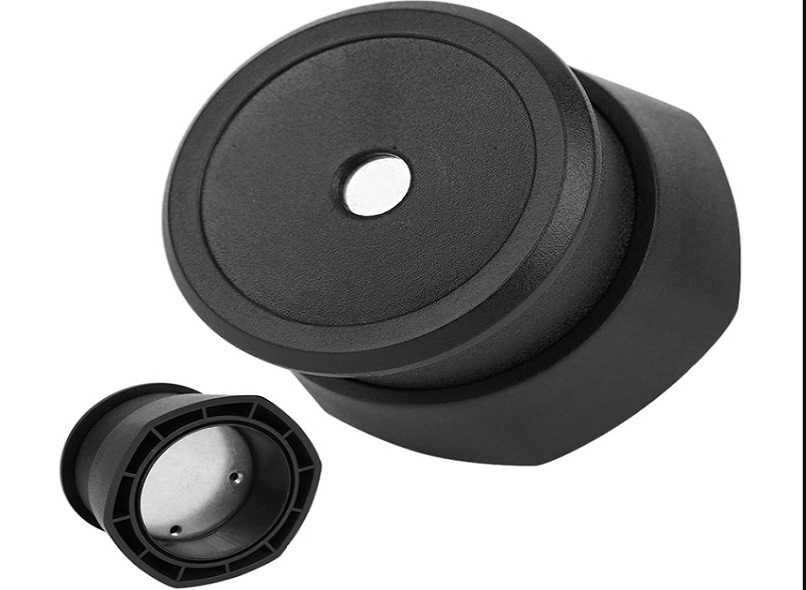
In the modern electronics industry, the requirements for components have become increasingly complex and diverse. From tightness and accurate dimensions to impeccable surface appearance, there are numerous quality criteria that need to be met. One method that has gained significant popularity in addressing these requirements is ultrasonic plastic welding. This cost-effective and reliable joining process ensures high degrees of production safety and reproducibility, making it an ideal choice for various applications, including welding Supermarket electronic anti-theft buckles.
In this comprehensive guide, we will explore the fundamentals of ultrasonic plastic welding and its application in the welding of Supermarket electronic anti-theft buckles. We will delve into the benefits, methods, and challenges associated with this technique. So, let's dive in and discover how ultrasonic plastic welding revolutionizes the welding process for Supermarket electronic anti-theft buckles.
1. The Basics of Ultrasonic Plastic Welding
The Science Behind Ultrasonic Plastic Welding
Ultrasonic plastic welding is based on the principle of utilizing high-frequency mechanical vibrations to generate heat and create a molecular bond between two plastic components. This process involves the conversion of electrical energy into mechanical vibrations through the use of a transducer. The transducer, typically made of piezoelectric material, converts the electrical energy into high-frequency vibrations.
These vibrations are then transferred to the welding tool, known as a horn or sonotrode. The horn amplifies the vibrations and applies them to the plastic components to be welded. As the horn applies pressure to the joint area, friction is generated, causing the plastic to soften and melt. Once the melting occurs, the pressure is maintained for a short period to allow for proper bonding.
Key Components and Equipment for Ultrasonic Plastic Welding
Successful ultrasonic plastic welding requires specialized equipment and components. The key components of an ultrasonic plastic welding system include:
- Transducer: The transducer converts electrical energy into mechanical vibrations.
- Horn or Sonotrode: The horn amplifies and transfers the vibrations to the plastic components.
- Anvil or Fixture: The anvil provides support and precise alignment of the plastic components during welding.
- Power Supply: The power supply generates the electrical energy required for the transducer to produce vibrations.
- Control Unit: The control unit regulates and monitors the welding process, including parameters such as amplitude, time, and pressure.
Advantages of Ultrasonic Plastic Welding
Ultrasonic plastic welding offers several advantages over traditional welding methods. Some of the key advantages include:
- Speed and Efficiency: Ultrasonic plastic welding allows for rapid joining of plastic components, resulting in high production speeds and increased efficiency.
- Strong and Reliable Joints: The molecular bond created by ultrasonic plastic welding produces strong and durable joints, ensuring the integrity and longevity of the welded parts.
- No Additional Materials: Unlike adhesive bonding or mechanical fastening methods, ultrasonic plastic welding does not require additional materials such as adhesives, screws, or rivets, reducing material costs and simplifying the assembly process.
- Clean and Aesthetic Finish: Ultrasonic plastic welding does not leave any visible marks or residue on the welded parts, resulting in a clean and aesthetically appealing finish.
- Versatility: Ultrasonic plastic welding can be used to join a wide range of plastic materials, including thermoplastics, without the need for additional surface preparation or pre-treatment.
- Automation and Integration: Ultrasonic plastic welding can be easily integrated into automated production lines, allowing for seamless integration with other manufacturing processes and improving overall productivity.
These advantages make ultrasonic plastic welding a preferred choice for various industries, including the welding of Supermarket electronic anti-theft buckles.