Ultrasonic Plastic Welding for PP Material Water Cup Buckle Welding
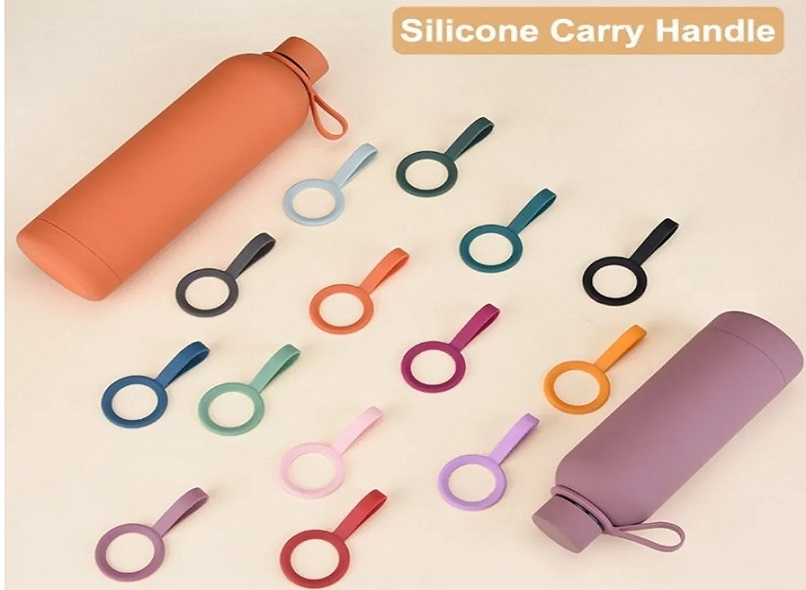
Ultrasonic plastic welding is a widely used technique for joining thermoplastic materials. One specific application of this welding method is the PP material water cup buckle welding. In this article, we will explore the process of ultrasonic plastic welding and its relevance to PP material water cup buckle welding. We will discuss the benefits of this technique, the equipment required, and the steps involved in achieving a successful weld. So, let's dive in!
1. Introduction
PP material water cup buckle welding is a critical process in the manufacturing of water cups. Properly welded buckles ensure the strength and durability of the cups, preventing leakage and maintaining the overall quality of the product. Ultrasonic plastic welding offers an efficient and reliable solution for this specific welding requirement. Let's explore how this technique works.
2. Understanding Ultrasonic Plastic Welding
Ultrasonic plastic welding is a process that uses high-frequency mechanical vibrations to create heat and bond thermoplastic materials. The principle behind this technique is the conversion of high-frequency electrical energy into high-frequency mechanical motion. This mechanical motion generates friction and heat at the interface of the materials, causing them to melt and form a molecular bond. Ultrasonic plastic welding is widely used in various industries due to its versatility and effectiveness.
3. Benefits of Ultrasonic Plastic Welding
Ultrasonic plastic welding offers several advantages over traditional welding methods. Some of the key benefits include:
- Strong and reliable welds: Ultrasonic plastic welding creates robust and durable welds that exhibit high strength and integrity.
- Fast and efficient: This welding technique enables rapid joining of thermoplastic materials, resulting in increased productivity.
- No additional materials required: Unlike adhesive bonding or mechanical fastening, ultrasonic plastic welding does not require additional materials such as adhesives or fasteners.
- Aesthetically pleasing welds: Ultrasonic plastic welding produces welds with a clean and seamless appearance, enhancing the overall visual appeal of the final product.
- Cost-effective: The elimination of additional materials and the high-speed nature of the process make ultrasonic plastic welding a cost-effective solution for joining thermoplastic materials.
4. PP Material Water Cup Buckle Welding
PP (polypropylene) is a commonly used thermoplastic material in the manufacturing of water cups. PP material water cup buckle welding involves joining the buckle component to the cup body using the ultrasonic plastic welding technique. This welding process ensures a secure and leak-proof connection, guaranteeing the quality and functionality of the water cup.
5. Equipment Required for PP Material Water Cup Buckle Welding
To perform PP material water cup buckle welding, the following equipment is required:
- Ultrasonic welding machine: This machine generates the high-frequency vibrations necessary for the welding process.
- Horn or sonotrode: The horn directs the vibrations to the welding area, applying pressure and creating friction between the materials.
- Anvil or fixture: The anvil supports the cup body during the welding process, ensuring proper alignment and stability.
6. Step-by-Step Guide for PP Material Water Cup Buckle Welding
The process of PP material water cup buckle welding involves the following steps:
- Preparation: Ensure that the cup body and buckle components are clean and free from any contaminants or debris.
- Alignment: Position the buckle component on the cup body, ensuring proper alignment and fit.
- Fixturing: Secure the cup body in the anvil or fixture, holding it firmly in place.
- Horn placement: Position the horn or sonotrode above the buckle component, ensuring proper contact with the materials.
- Welding parameters: Set the welding parameters on the ultrasonic welding machine, including amplitude, time, and pressure, based on the specific requirements of the PP material and buckle design.
- Welding process: Activate the ultrasonic welding machine, initiating the high-frequency vibrations. The vibrations create friction and heat at the interface of the materials, causing them to melt and form a bond.
- Cooling and solidification: After the welding process is complete, allow the weld to cool and solidify, ensuring the formation of a strong and reliable joint.
- Inspection: Inspect the weld for any defects or inconsistencies, ensuring that it meets the required quality standards.
7. Troubleshooting Common Issues
During the PP material water cup buckle welding process, several issues may arise. Here are some common problems and their possible solutions:
- Incomplete weld: Insufficient pressure or improper welding parameters may result in an incomplete weld. Adjust the pressure and welding parameters accordingly.
- Burn marks or discoloration: Excessive heat or prolonged welding time can cause burn marks or discoloration. Optimize the welding parameters and reduce the welding time to prevent this issue.
- Weak weld: Insufficient amplitude or pressure can lead to a weak weld. Increase the amplitude and pressure to enhance the strength of the joint.
- Misalignment: Improper alignment of the buckle component and cup body can result in a flawed weld. Ensure precise alignment before initiating the welding process.
8. Safety Precautions
When performing PP material water cup buckle welding or any other ultrasonic plastic welding, it is essential to follow proper safety precautions. Some key safety measures include:
- Using appropriate personal protective equipment (PPE) such as gloves and safety glasses.
- Ensuring proper ventilation in the welding area to avoid inhalation of fumes or vapors.
- Adhering to the manufacturer's guidelines for the safe operation of the ultrasonic welding machine.
- Regular maintenance and inspection of the equipment to prevent malfunctions or hazards.
9. Applications of Ultrasonic Plastic Welding
Ultrasonic plastic welding finds application in various industries and products, including:
- Automotive industry: Welding of interior and exterior plastic components, such as dashboards, door panels, and bumpers.
- Medical industry: Assembly of medical devices, such as syringes, IV sets, and blood filters.
- Consumer electronics: Joining of plastic parts in electronic devices, such as mobile phones, laptops, and remote controls.
- Packaging industry: Sealing and welding of plastic packaging containers, such as bottles, jars, and blister packs.
- Textile industry: Bonding of synthetic fabrics and non-woven materials for the production of garments and home textiles.
10. Conclusion
Ultrasonic plastic welding offers an efficient and reliable solution for PP material water cup buckle welding. This technique provides numerous benefits, including strong and durable welds, fast and efficient joining, and aesthetically pleasing results. By following the step-by-step guide and implementing proper safety measures, manufacturers can achieve high-quality welds and ensure the functionality and integrity of water cups. Ultrasonic plastic welding is a versatile process with applications across various industries, making it an indispensable tool for joining thermoplastic materials.