Ultrasonic Plastic Welding for Electric Vehicle Alarm: Enhancing Safety and Efficiency
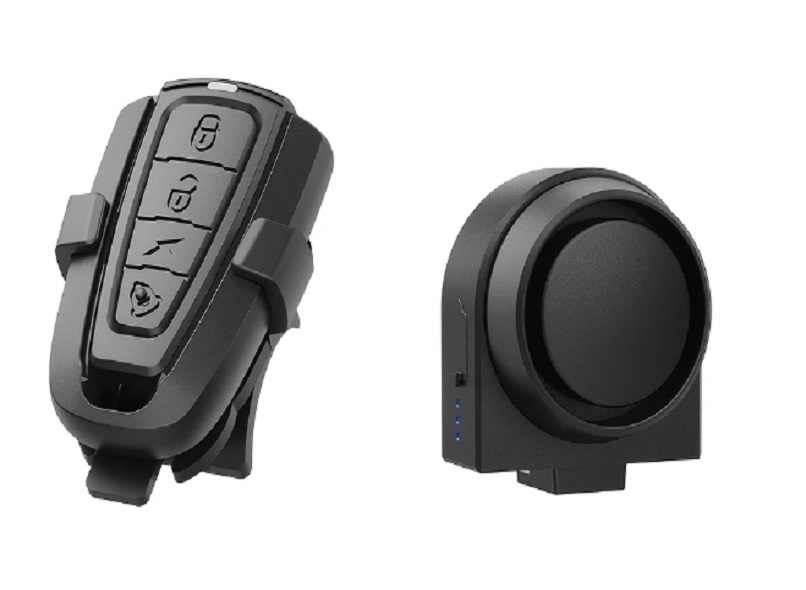
In the rapidly evolving world of electric vehicles (EVs), safety and efficiency are paramount. One crucial aspect of EV manufacturing is the welding process, particularly when it comes to the assembly of components like electric vehicle alarms. Ultrasonic plastic welding has emerged as a cutting-edge technology for securely bonding plastic components in electric vehicles, ensuring reliable performance and enhancing safety measures. This article explores the benefits and considerations of ultrasonic plastic welding in the context of electric vehicle alarms.
Understanding Ultrasonic Plastic Welding
Ultrasonic plastic welding is a technique that utilizes high-frequency vibrations to create frictional heat between thermoplastic materials. These vibrations generate localized melting, which, upon cooling, forms a strong molecular bond between the components. This process is particularly well-suited for joining plastic parts in electric vehicle alarms, providing a secure and durable connection.
Advantages of Ultrasonic Plastic Welding
- Enhanced Safety: Ultrasonic plastic welding eliminates the need for additional adhesives or mechanical fasteners, reducing the risk of component detachment in electric vehicle alarms. This ensures that the alarm system remains intact during the vehicle's operation, enhancing safety for both the driver and passengers.
- Improved Efficiency: The high-speed nature of ultrasonic plastic welding enables rapid assembly of electric vehicle alarms, increasing production efficiency. With daily output reaching up to 6000 pieces, manufacturers can meet the growing demand for electric vehicles without compromising on quality or performance.
- Cost-Effectiveness: Ultrasonic plastic welding eliminates the need for additional materials like screws or adhesives, reducing production costs. This streamlined process also minimizes labor requirements, saving manufacturers time and resources.
Precautions for Ultrasonic Plastic Welding in Electric Vehicle Alarms
While ultrasonic plastic welding offers numerous benefits, it is essential to follow specific precautions to ensure optimal safety and quality during the welding process.
Battery Precautions
- High-Voltage Battery Disconnection: Before initiating the ultrasonic plastic welding process, it is crucial to disconnect both the 12-volt battery and the high-voltage battery service disconnect. This precautionary measure ensures that the welding process does not interfere with the electrical components of the electric vehicle alarm.
- Handling Damaged Batteries: In the event of a collision or damage to the high-voltage battery, it is essential to treat the battery as potentially unstable. Technicians should avoid direct contact with damaged batteries or high-voltage wiring harnesses to minimize the risk of electrocution or combustion.
- Safe Storage and Disposal: If the battery has been punctured or damaged, it should be isolated at least 50 feet away from flammable materials. Some batteries can be challenging to extinguish once on fire, emphasizing the importance of proper storage and disposal procedures.
Welding Safety
When performing ultrasonic plastic welding on electric vehicle alarms, it is vital to adhere to welding safety practices, both for the 12-volt system and the high-voltage battery system.
- Disabling the High-Voltage System: Prior to initiating the welding process, it is crucial to disable the high-voltage system as per the automaker's repair information. This can be achieved by removing the hybrid battery service disconnect, ensuring the safety of technicians and preventing inadvertent reinstallation of removed components.
- Multiple Disabling Methods: Different automakers may have specific procedures for disabling the high-voltage system. Technicians should familiarize themselves with the recommended disabling methods outlined in the OEM Hybrid and Electric Vehicle Disable Search tool developed by I-CAR.
- Personal Protective Equipment (PPE): Welding on electric vehicle alarms requires the use of proper PPE, including rubber and leather gloves, boots, face shields, and safety glasses. Technicians should undergo comprehensive training and follow all OEM high-voltage disable procedures and safety precautions.
Conclusion
Ultrasonic plastic welding offers significant advantages in the assembly of electric vehicle alarms, ensuring both safety and efficiency. By eliminating the need for additional components and providing a reliable bond, this advanced welding technique enhances the overall performance and durability of electric vehicle alarm systems. However, it is crucial to follow the recommended precautions when working with high-voltage batteries and adhere to welding safety practices. By combining these measures, manufacturers can continue to innovate and improve the quality of electric vehicle alarms, contributing to the advancement of the electric vehicle industry as a whole.
Additional Information: Ultrasonic plastic welding is a versatile technology that can be applied to a wide range of materials commonly used in electric vehicle alarms, including ABS, PE, PC, PVC, PP, nylon, and acrylic. Manufacturers can customize equipment and molds according to specific material requirements, ensuring optimal performance and compatibility.
Tone of Voice: The tone of this article should be informative, professional, and authoritative. It should convey a sense of expertise and provide practical guidance to readers involved in the manufacturing or repair of electric vehicle alarms. The language should be clear and concise, avoiding unnecessary jargon while maintaining a technical focus.