Ultrasonic Plastic Welding for Car License Plate Light Welding
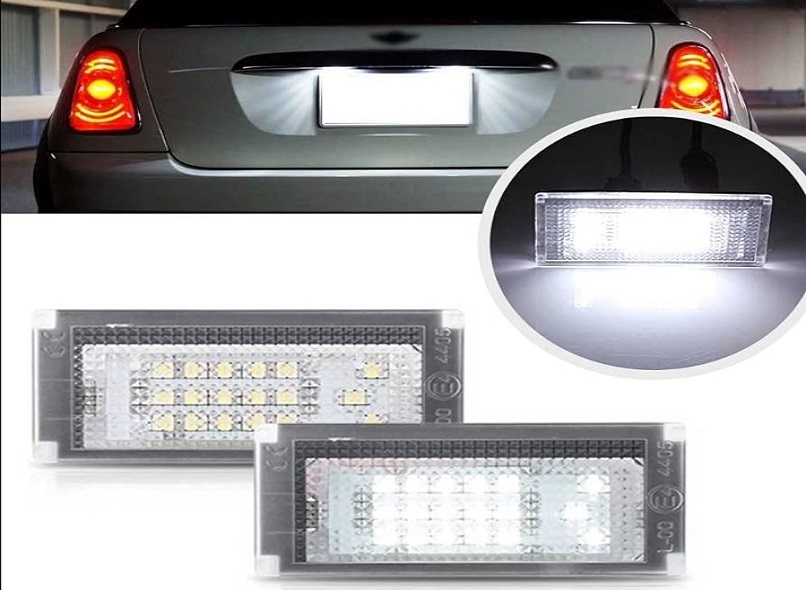
Ultrasonic plastic welding has emerged as a reliable and efficient method for assembling various components in the automobile industry. One particular application where this technology shines is in the welding of car license plate lights. In this article, we will explore the benefits of ultrasonic plastic welding for car license plate light assembly and delve into the specific techniques and machines used in this process.
The Importance of Car License Plate Lights
Before we dive into the details of ultrasonic plastic welding, let's understand the significance of car license plate lights. These seemingly small components play a crucial role in ensuring the safety and legality of vehicles on the road. License plate lights provide visibility to the license plate, allowing law enforcement officers to identify vehicles even in low-light conditions. It is essential for these lights to be tightly sealed and functional to avoid any legal issues.
Ultrasonic Welding Technology in the Automotive Sector
Ultrasonic welding technology has gained popularity in the automotive sector due to its ability to produce high-quality, tightly sealed welds without the need for additional materials. This technology is commonly used for assembling external and interior lights in vehicles, including car license plate lights.
External Lights Assembly
Ultrasonic welding is widely used to assemble external lights on vehicles. Components such as the third brake light, reflectors, plate lighting, and blinkers can be securely welded using ultrasonic technology. This process ensures that the lights are tightly sealed and resistant to environmental factors.
Interior Lights Assembly
Ultrasonic welding is also employed for assembling interior lights in vehicles. Whether it's the ceiling lights, doors, or other interior lighting components, ultrasonic technology provides a reliable method for joining these parts together.
Welding Machines for Car License Plate Lights
To achieve precise and efficient welding of car license plate lights, specialized machines and equipment are required. Let's explore some of the key welding machines used in this process.
OMEGA 4 A
The OMEGA 4 A welding machine is designed specifically for automotive applications, including car license plate light assembly. This machine offers advanced features and capabilities to ensure accurate and durable welds. With its customizable settings, it can be tailored to meet the specific requirements of different license plate light designs.
OMEGA 4 S
Another machine in the OMEGA 4 series, the OMEGA 4 S, is also suitable for car license plate light welding. This machine provides enhanced control and precision, allowing for seamless integration of license plate light components. Its versatility makes it an ideal choice for manufacturers in the automotive industry.
OMEGA 4 X
The OMEGA 4 X welding machine is known for its exceptional performance in welding large-sized parts. This machine is capable of handling the welding of car license plate lights efficiently, ensuring a tight seal and long-lasting durability. Its advanced technology enables manufacturers to achieve high-quality welds without the need for additional materials.
Welding for Vibration-Sensitive Applications
While ultrasonic welding is the preferred method for most automotive applications, there are instances where Ultrasonic plastic welding is more suitable. Vibration-sensitive components, such as airbag parts, electronic components, and aesthetic parts, require a different approach to assembly. Ultrasonic plastic welding, combined with techniques like punching or pin riveting, offers a reliable solution for joining these materials.
Welding Machines for Vibration-Sensitive Applications
To cater to the unique requirements of vibration-sensitive applications, specific welding machines are available. Let's take a closer look at a couple of these machines.
10/30 Welding Device
The 10/30 Ultrasonic plastic Welding Device is designed for precision welding in vibration-sensitive applications. This device combines Ultrasonic plastic welding with cold-forming to achieve high-quality assemblies. Its compact design and adjustable settings make it a versatile tool for various automotive components.
20/40 Welding Device
The 20/40 Ultrasonic plasticWelding Device offers similar capabilities to the 10/30 device but with increased power and larger welding capabilities. This device is suitable for more demanding vibration-sensitive applications that require precise and reliable welding. Its ergonomic design ensures ease of use and consistent results.
Conclusion
Ultrasonic plastic welding has revolutionized the assembly of car license plate lights and other components in the automotive industry. Its ability to produce tightly sealed welds without the need for additional materials has made it a preferred choice for manufacturers. Whether it's the external lights or interior lighting, ultrasonic technology ensures the durability and functionality of these crucial automotive components.
In addition to ultrasonic welding, Ultrasonic plastic welding offers an alternative for vibration-sensitive applications. By combining Ultrasonic plasticwelding with techniques like punching and pin riveting, manufacturers can achieve high-quality assemblies for these specific components.
With the advancements in welding machines and equipment, manufacturers have access to reliable and efficient tools for car license plate light welding and other automotive applications. These machines, such as the OMEGA 4 series and Ultrasonic plasticwelding devices, provide the precision and control needed to produce consistent and durable welds.
As the automotive industry continues to evolve, ultrasonic plastic welding and Ultrasonic plasticwelding will play an integral role in ensuring the seamless assembly of car license plate lights and other critical components. By embracing these technologies, manufacturers can enhance the safety, performance, and aesthetics of vehicles on the road.