How Turntable Systems Enhance Ultrasonic Welding Efficiency
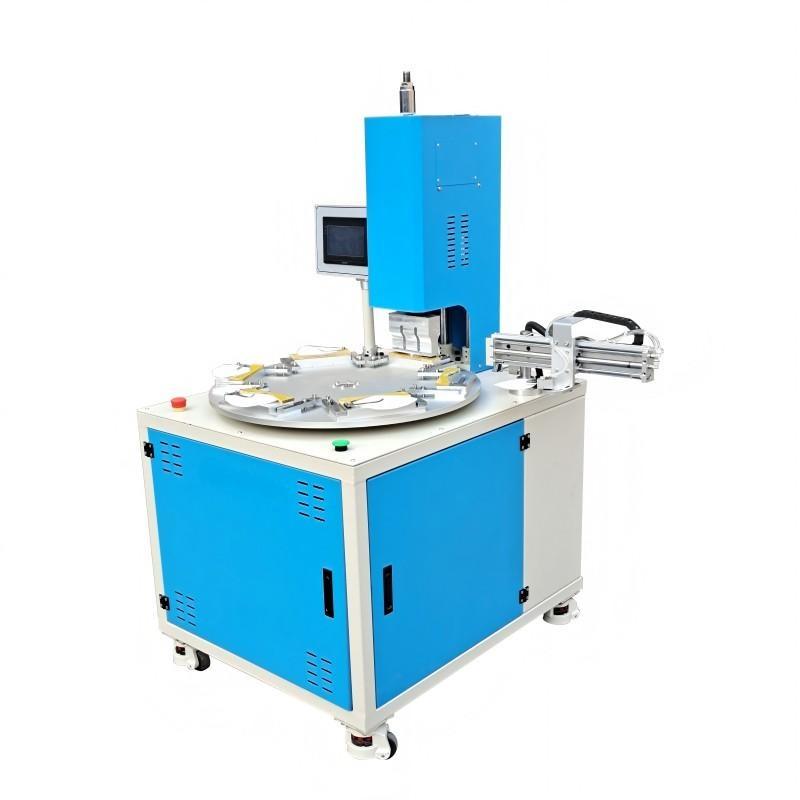
Ultrasonic welding, a cornerstone of Industry 4.0 smart manufacturing, revolutionizes material joining through advanced vibration technology. This innovative process joins materials—especially plastics—quickly and securely without adhesives or fasteners.
It delivers strong, reliable welds in seconds by harnessing high-frequency vibrations to generate precise frictional heat. This combination of efficiency and precision makes it indispensable across automotive, electronics, and medical device manufacturing.
Integrating turntable systems transforms traditional ultrasonic welding into a smart manufacturing powerhouse. These sophisticated automation platforms rotate workpieces with precision control, enabling seamless production workflows.
Through intelligent turntable ultrasonic welding, manufacturers achieve higher throughput, maintain consistent quality, and significantly reduce labor costs—meeting the demands of modern industrial production. This article explores the technology's core systems, real-world applications, essential features, and Industry 4.0 integration capabilities.
Table of Contents
How Turntable Ultrasonic Welding Machines Work
Applications of Turntable Ultrasonic Welding Systems
Key Features to Consider When Choosing a Turntable Welding Machine
Industry Trends and Innovations
FAQs
Conclusion
How Turntable Ultrasonic Welding Machines Work
Core Components and Technology
Unlike traditional ultrasonic welding which uses stationary fixtures, modern servo-controlled turntable systems enable continuous rotation and precise positioning for enhanced efficiency.
These sophisticated ultrasonic welding machines integrate several key components working in harmony:
Ultrasonic Generator: Advanced power supply converting standard current into high-frequency (20-40kHz) electrical energy with real-time parameter control.
Transducer (Converter): High-precision piezoelectric device transforming electrical energy into mechanical vibrations, optimized for servo-controlled turntable applications.
Booster and Horn System:
- Precision amplitude control (20-100 microns)
- Optimized energy focusing technology
- Application-specific horn designs
Servo-Controlled Turntable:
- Multi-axis positioning system
- Continuous production flow capability
- Integrated fixture mounting solutions
Real-Time Control System:
- Advanced PLC integration
- Continuous weld monitoring
- Quality parameter tracking
The integration of these components creates a sophisticated welding system where the servo-controlled turntable enables precise automation and consistent quality.
Advanced Process Flow
The automated welding cycle incorporates multiple stages with real-time weld monitoring:
1. Smart Component Loading:
- Advanced part recognition
- Automated placement verification
2. Servo-Controlled Alignment:
- ±0.02mm positioning accuracy
- Dynamic part tracking
3. Precision Welding Control:
- Real-time force monitoring
- Adaptive energy delivery
4. Quality Assurance:
- Continuous parameter monitoring
- Automatic quality verification
5. Automated Part Handling:
- Systematic unloading
- Production line integration
Benefits of Advanced Automation
This sophisticated servo-controlled turntable system delivers measurable advantages:
Production Efficiency:
- 300% higher throughput vs. manual systems
- 60% reduction in labor costs
Quality Assurance:
- ±5% weld strength consistency
- Near-zero defect rates through real-time monitoring
Operational Benefits:
- Improved workplace ergonomics
- Optimized power consumption
Applications of Turntable Ultrasonic Welding Systems
High-Volume Manufacturing Applications
Turntable ultrasonic welding has transformed high-throughput production across diverse industries, seamlessly integrating vibration welding technology with automated precision:
Aerospace & Automotive Manufacturing: Advanced applications include:
- Lightweight composite aircraft components demanding precise bond strength
- Electric vehicle battery enclosures necessitating hermetic sealing (View Case Study)
- Critical safety systems featuring airbag housings and sensor assemblies
- Advanced lighting systems utilizing specialized vibration welding techniques
Electronics Production: Precision applications encompassing:
- Next-generation smartphone enclosures demanding aesthetic excellence
- High-density circuit board assembly with optimized welding parameters
- IoT devices necessitating IP67 water-resistant sealing
- High-performance connector assemblies designed for maximum durability
Medical Device Manufacturing: FDA-compliant solutions including:
- Class I, II, and III medical device integration
- Ultra-pure fluid handling systems
- High-precision diagnostic equipment enclosures
- Contamination-free disposable instrument assembly
Packaging Solutions: High-speed applications encompassing:
- Advanced tamper-evident security systems
- Medical-grade sterile barrier packaging
- FDA-approved food container sealing
- Eco-friendly packaging solutions
Advanced Material Processing Capabilities
Modern turntable ultrasonic welding systems showcase exceptional versatility in material processing, excelling in joining:
- High-performance engineering thermoplastics (ABS, PC, PEEK)
- Aerospace-grade composites and fiber-reinforced materials
- Validated medical-grade polymers
- Complex hybrid material combinations
Success Story: Automotive Innovation
A leading electric vehicle manufacturer (Industry Report) implemented our advanced turntable ultrasonic welding system for battery enclosure production. The independently verified results include:
- 40% increase in production efficiency through AI-optimized cycle times
- Defect rates below 0.1% utilizing real-time quality monitoring
- 25% reduction in energy consumption versus traditional methods <Check plastic welding methods>
- Complete process traceability through integrated data collection
This implementation demonstrates how modern ultrasonic welding technology, combined with intelligent automation, revolutionizes manufacturing efficiency while ensuring superior quality standards.
Key Features to Consider When Choosing a Turntable Welding Machine
Technical Specifications & Cost-Effective Solutions
When selecting a machine, consider these essential specifications:
Material Type | Power Range | Frequency Range |
---|---|---|
Hard Plastics | 2.4-2.6kW | 15-20 kHz |
Soft Materials | 1.5-2.0kW | 20-30 kHz |
Delicate Components | 1.0-1.5kW | 30-40 kHz |
Power Output: Advanced 2.6kW systems optimize performance for hard plastics, while energy-efficient lower outputs provide precise control for softer materials
Frequency Range: Industry-standard 15-20 kHz suits most applications, with specialized 20-40 kHz settings ensuring damage-free processing of delicate components
Customizable Turntable Systems
Our versatile solutions offer:
- Precision-engineered turntable speed controls for optimal production efficiency
- Advanced modular tooling systems accommodating diverse workpiece dimensions
- Seamless production line integration capabilities with Industry 4.0 compatibility
Quality Assurance & Support Network
Partner with suppliers offering comprehensive support:
- 24/7 technical support with rapid-response maintenance services
- Industry-leading 12-month warranty coverage
- Full ISO 9001:2015 certification ensuring consistent quality standards
Enhanced Technical Features
Advanced specifications for optimal performance:
Smart Power Management
- Energy-efficient 2.6kW systems for demanding industrial applications
- Intelligent power adjustment for material-specific requirements
- Eco-friendly operation modes, reducing energy consumption
Precision Frequency Control:
- Optimized 15-20 kHz range for standard manufacturing processes
- High-precision 20-40 kHz capability for specialty applications
- Advanced frequency modulation for complex material combinations
Smart Integration Features
Future-ready customization options include:
- AI-enhanced turntable speed control systems
- Smart tooling configurations for diverse applications
- Industry 4.0 ready integration protocols
Comprehensive Quality Management
Industry-leading support features:
- Proactive maintenance and parts support programs
- Enhanced warranty protection options
- Complete ISO compliance and certification
Industry Trends and Innovations
Smart Manufacturing Integration
Industry leaders like Branson Ultrasonics and Dukane are revolutionizing turntable ultrasonic welding through Industry 4.0 integration. These advanced systems incorporate predictive maintenance capabilities and sustainable welding solutions, transforming traditional manufacturing processes. Modern IoT-enabled platforms offer comprehensive monitoring and control, with real-time weld parameter adjustments ensuring optimal performance.
Leading manufacturers have implemented sophisticated quality control systems powered by artificial intelligence, achieving defect detection rates of 99.9%. Cloud-based analytics platforms provide deep insights into production efficiency, while digital twin technology enables virtual process optimization before physical implementation. Remote monitoring capabilities ensure consistent quality across global manufacturing facilities.
The results speak for themselves - facilities utilizing these smart manufacturing solutions report up to 40% improvement in overall equipment effectiveness (OEE), demonstrating the tangible benefits of digital transformation in ultrasonic welding.
Energy Efficiency and Sustainability
Environmental stewardship drives innovation in modern vibration welding systems. Industry pioneer Branson Ultrasonics has introduced next-generation generators operating in the 2000W-2500W range, setting new standards for energy efficiency. These sustainable welding solutions incorporate intelligent power management, reducing standby consumption by 35% while maintaining superior weld quality.
Advanced energy recuperation systems capture and repurpose excess vibration energy, while eco-friendly cooling technologies minimize environmental impact. Through optimized welding cycles and predictive maintenance algorithms, manufacturers achieve remarkable efficiency gains - many reporting 30-40% reduction in energy-related costs without compromising performance.
FAQs
What industries benefit most from turntable ultrasonic welding?
Key industries leveraging this cost-effective technology include:
- Automotive manufacturing: For components like EV battery assemblies, interior trim, and safety systems - achieving 35% faster production rates
- Electronics production: Creating consumer devices, circuit assemblies, and waterproof enclosures with 99.9% quality consistency
- Medical device manufacturing: Assembling FDA-compliant devices and sterile equipment with validated processes
- Packaging industry: Producing tamper-evident and hermetically sealed containers with 40% higher throughput.
These sectors report significant ROI through enhanced precision and automated throughput.
How does turntable welding improve ROI?
Companies implementing turntable ultrasonic welding systems typically see:
- 45% reduction in labor costs through automation
- 30% increase in production efficiency
- 50% decrease in material waste
- 12-18 month average payback period Case studies show manufacturers achieving full ROI within one year through combined cost savings and productivity gains.
Can turntable systems handle delicate materials?
Yes! Modern turntable systems excel at processing delicate materials through:
- Precise frequency control (20-40 kHz range) for gentle material handling
- Advanced amplitude modulation to prevent material damage
- Real-time force monitoring to maintain optimal pressure
- Smart material recognition systems that automatically adjust welding parameters.
This sophisticated control ensures consistent, high-quality welds while preserving material integrity.
How do maintenance requirements compare to manual systems?
Turntable ultrasonic welding systems offer several maintenance advantages:
- 40% reduction in component wear through automated consistency
- Predictive maintenance scheduling using IoT sensors
- Self-diagnostic capabilities that identify potential issues
- Simplified calibration procedures with digital assistance
While periodic maintenance is required (horn replacement every 3-6 months, calibration checks), the overall maintenance burden is significantly lower than manual systems.
What is the typical price range for these machines in North American markets?
Investment costs vary based on capabilities and features:
- Entry-level portable units: $1,200 - $3,000 (ideal for small-scale operations)
- Mid-range systems with basic automation: $3,000 - $5,000 (suitable for growing manufacturers)
- Industrial-grade systems: $5,000 - $8,200 (recommended for high-volume production)
- Custom solutions with advanced features: $8,200+ (enterprise-level implementations) ROI analysis shows 12-18 month average payback through increased productivity and reduced labor costs.
Are turntable machines compatible with all ultrasonic welding applications?
Turntable systems excel in specific scenarios but have limitations:
- Ideal for: High-volume production, standardized parts, repeatable processes
- Less suitable for: Oversized components (>500mm), highly irregular shapes, extremely variable part sizes
- Best performance: Thermoplastics, composites, and consistent material combinations
- Optimal applications: Parts requiring precise vibration welding with cycle times under 30 seconds
Conclusion
High-precision vibration welding systems represent a transformative advancement in ultrasonic welding technology, delivering exceptional efficiency, precision, and scalability to modern manufacturing processes. These innovative systems are revolutionizing production across multiple sectors, from automotive assembly lines to medical device manufacturing, by seamlessly integrating advanced vibration control with automated workflow optimization.
Industry leaders like Dizo Ultrasonic Technology Co., Ltd. have developed sophisticated weld parameter monitoring and real-time quality control capabilities that ensure consistent, high-quality results while dramatically reducing operational costs.
The implementation of advanced turntable-based welding solutions has shown remarkable success, with manufacturers reporting up to 40% increases in productivity and 30% reductions in quality-related issues. These high-performance systems particularly excel in applications requiring precise material joining, offering unmatched control over weld parameters and delivering consistent results even with challenging materials and complex geometries.
Transform your production line today with turntable ultrasonic welding technology!
To ensure success, evaluate potential partners using these 5 essential criteria:
1. Technical Expertise and Support
- Comprehensive training programs
- 24/7 technical assistance
2. Quality Certifications
- ISO 9001:2015 certification
- Industry-specific compliance
3. Customization Capabilities
- Flexible system configurations
- Application-specific solutions
4. Integration Support
- Industry 4.0 compatibility
- Existing system integration expertise
5. Proven Track Record
- Verifiable case studies
- Customer testimonials