The Ultimate Guide to PVC Window Frames Welding with Hot Plate Welding Machine
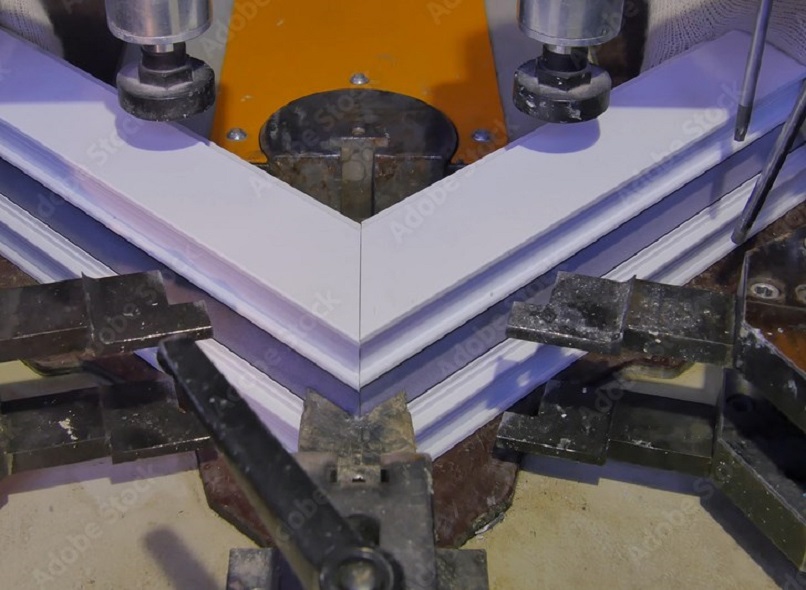
PVC window frames welding is a crucial process in the manufacturing of high-quality windows and doors. It ensures the durability and strength of the joints, providing a long-lasting solution for both residential and commercial applications. One of the widely used methods for welding PVC window frames is hot plate welding. In this comprehensive guide, we will explore the ins and outs of PVC window frames welding using a hot plate welding machine. From the basics of hot plate welding to the step-by-step process and best practices, you'll find all the information you need to master this technique. So, let's dive in!
Section 1: Understanding Hot Plate Welding
1.1 What is Hot Plate Welding?
Hot plate welding is a versatile method for joining two plastic parts, including PVC window frames, using a heated metal plate. It is also known as mirror, platen, or butt welding. This technique allows for the seamless fusion of plastic components by melting the interface surfaces and creating a strong bond.
1.2 Advantages of Hot Plate Welding for PVC Window Frames
Hot plate welding offers several advantages for welding PVC window frames:
- Versatility: Hot plate welding can weld small or large parts, flat or contoured ones, and even multiple assemblies simultaneously.
- Superior Strength: The resulting welds from hot plate welding are highly durable, providing excellent strength and structural integrity.
- Wide Application Range: Hot plate welding is widely used in various industries, including automotive, appliance manufacturing, and hardware, for assembling different components.
- Contoured Parts Joining: This technique enables the welding of contoured parts by using specially designed blocks attached to the platen.
1.3 When to Use Hot Plate Welding for PVC Window Frames
Hot plate welding is particularly suitable for PVC window frames welding due to its ability to handle the specific requirements of this application. Here are some instances where hot plate welding is the preferred choice:
- Joining Mullions and Transoms: Hot plate welding is ideal for joining mullions and transoms in PVC window frames, ensuring a strong and seamless connection.
- Ensuring Leak-Free Joints: PVC window frames require leak-free joints to ensure energy efficiency and weather resistance. Hot plate welding provides a reliable solution for achieving tight and secure joints.
- Contoured Profile Welding: If your PVC window frames have contoured profiles, hot plate welding allows for precise and uniform joining without compromising the shape or aesthetics.
Section 2: The Hot Plate Welding Process
Hot plate welding involves a series of steps to achieve a successful weld. Let's explore each step in detail:
2.1 Step 1: Loading the Assembly
The first step in hot plate welding is loading the two halves of the assembly into custom-made fixtures. The fixtures can be oriented vertically or horizontally, depending on the application. Vertical orientation is preferred for ease of loading, while horizontal orientation is suitable for assemblies with internal components or long, flexible parts.
2.2 Step 2: Heating the Platen
Once the assembly is loaded, the heated platen moves in between the fixtures. The platen, typically made of aluminum, P20 mold steel, or aluminum-bronze, is heated using electric cartridges. The temperature of the platen can be controlled based on the specific requirements of the PVC material being welded.
2.3 Step 3: Applying Pressure and Melting the Edges
The fixtures press the parts against the heated platen for a set time, causing a small portion of plastic around the edge of each part to melt. Mechanical stops built into the fixtures and platen prevent excessive material from being melted. The pressure applied and the displacement of the parts must be carefully controlled to ensure a strong and uniform weld.
2.4 Step 4: Cooling and Fusion of Melted Edges
After the plastic has melted, the fixtures move apart, and the platen withdraws. The fixtures then travel toward each other again, pressing the parts together. This holding time allows the melted edges to fuse together as the plastic cools. The duration of the holding time depends on the specific requirements of the PVC material and the size of the assembly.
2.5 Step 5: Unloading the Assembly
Once the fusion of the melted edges is complete, the fixtures separate again, and the assembly is unloaded. The finished PVC window frame is now ready for further processing or installation.
Section 3: Factors Affecting Hot Plate Welding
To achieve optimal results in hot plate welding for PVC window frames, several factors need to be considered. Let's explore these factors in detail:
3.1 Platen Temperature
The temperature of the heated platen plays a critical role in hot plate welding. It ranges from 150 to 650°F, depending on the specific PVC material and the desired welding parameters. For non-contact applications, where parts are held close to the platen without touching it, the platen temperature can be as high as 1,000°F.
3.2 Heating Time
The heating time required for melting the plastic edges varies depending on the PVC material and the size of the assembly. Amorphous materials melt faster than engineering-grade polymers. The heating time typically ranges from 1.5 seconds to 20 seconds.
3.3 Welding Pressure
The pressure applied during the welding process should be carefully controlled to avoid squeezing out excessive molten plastic from the joint. The optimal pressure range is typically between 14 and 150 psi, depending on the size and shape of the assembly.
3.4 Transition Time and Holding Time
The transition time, which is the time between removing the parts from the platen and pushing them together, should be kept as short as possible to maintain the molten state of the plastic. The holding time, on the other hand, is the duration during which the melted edges fuse together as the plastic cools. It typically lasts a few seconds.
Section 4: Best Practices for Hot Plate Welding PVC Window Frames
To ensure successful hot plate welding of PVC window frames, it is essential to follow best practices. Here are some tips to achieve optimal results:
4.1 Proper Fixture Alignment
Proper alignment of the fixtures is crucial for achieving precise and uniform welds. Ensure that the fixtures are securely connected to linear slides powered by pneumatic cylinders, hydraulic cylinders, or servo-driven ballscrews. This allows for precise control of welding force, speed, and displacement.
4.2 Selecting the Right Platen Material
The choice of platen material depends on the specific requirements of the application. Aluminum is suitable for low-temperature applications, while steel is preferred for high-temperature applications. Aluminum-bronze recovers heat faster and is often used in high-volume applications.
4.3 Maintaining Consistent Temperature
When welding contoured parts, use blocks of aluminum or steel machined to match the shape of the parts. Ensure that the temperature remains consistent throughout the entire block to ensure uniform heat distribution and fusion of the melted edges.
4.4 Quality Control and Traceability
Implement a robust quality control process to ensure the integrity of the welded PVC window frames. Regular checks on corner strength and adherence to process parameters are essential. Additionally, consider implementing a traceability system to track and record key welding parameters for future reference.
4.5 Operator Training and Safety
Ensure that operators are well-trained in the hot plate welding process and follow proper safety protocols. Provide them with the necessary personal protective equipment (PPE) and adhere to all relevant safety regulations to minimize the risk of accidents or injuries.
Section 5: Conclusion
Hot plate welding is a reliable and efficient method for welding PVC window frames. By following the proper techniques, implementing best practices, and considering the specific factors affecting the welding process, you can achieve high-quality, durable, and aesthetically pleasing welds. With the right hot plate welding machine and attention to detail, you can ensure the strength, durability, and longevity of your PVC window frames. So, embrace the power of hot plate welding and elevate the quality of your PVC window frame manufacturing process.