The Ultimate Guide to Hot Plate Plastic Welding for Crates Welding
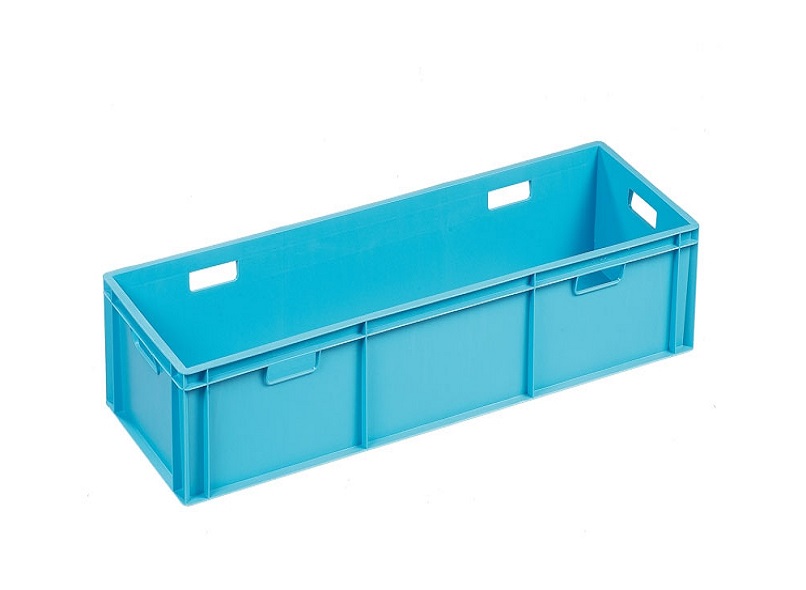
Plastic welding is a highly effective method for joining plastic parts together, and one popular technique is hot plate welding. This process uses a heated metal plate, also known as a hot plate, to melt the plastic parts and create a strong bond. In this comprehensive guide, we will explore the ins and outs of hot plate plastic welding specifically for crates welding. From the basics of the hot plate welding process to the advantages and applications, we'll provide you with all the information you need to become an expert in this field.
Understanding Hot Plate Welding
Hot plate welding, also known as heat contact welding or mirror welding, is a technique that involves heating the joining surfaces of plastic parts using a heated metal plate. The process consists of several stages, including heating, changeover, and joining. The hot plate, which is specially designed according to CAD data, plasticizes the surfaces to be joined, allowing them to become molten. Once the surfaces are heated, the hot plate is moved out of the joining area, and the melted surfaces are pressed together under pressure. As the plastic cools and solidifies, a strong and durable bond is formed.
Advantages of Hot Plate Welding
Hot plate welding offers numerous advantages that make it a preferred method for crates welding and other plastic joining applications. Firstly, hot plate welding allows for excellent compensation of workpiece fluctuations, resulting in consistent and reproducible welds. This is particularly beneficial when working with large-area joints or double shells commonly found in crate manufacturing. Additionally, hot plate welding enables the welding of combinations of hard and soft plastics, providing versatility in the construction of crates with varying material properties.
Another advantage of hot plate welding is the high strength of the welded joints. The process ensures a robust bond that can withstand rigorous use and environmental factors. The seams created through hot plate welding are also highly reproducible and can be hidden, resulting in aesthetically pleasing finished products. Moreover, hot plate welding machines can be automated, allowing for increased efficiency and reduced cycle times.
Types of Hot Plate Welding Machines
When it comes to hot plate plastic welding machines, there are various options available to suit different welding needs. Vimalssonic, a renowned manufacturer, offers a range of standard and customized hot plate welding machines for crate welding and other applications. Let's explore some of the different types:
1. Horizontal-Operated Hot Plate Welding Machine
The horizontal-operated hot plate welding machine is a popular choice for crate welding. It features a vertical heating element and horizontal feed axes for the workpieces. This design allows for precise alignment and welding of the crate components. The machine's horizontal orientation makes it suitable for joining large or bulky crate parts.
2. Vertical-Operated Hot Plate Welding Machine
In contrast to the horizontal-operated machine, the vertical-operated hot plate welding machine has a horizontally aligned heating element and vertical workpiece feed. This design is ideal for welding smaller crate components or parts that require a different orientation. The vertical-operated machine offers flexibility and ease of use in various crate welding applications.
3. Servo-Operated Hot Plate Welding Machines
Servo-operated hot plate welding machines provide advanced functionality for precise and efficient crate welding. These machines utilize a shuttle system that allows for accurate alignment of the components. With servo motor operation, these machines offer speed and precision welding, making them suitable for high-volume production. The servo-operated hot plate welding machines can handle both small and large crate components, thanks to their change-over setup incorporation.
4. Pneumatic-Operated Hot Plate Welding Machines
Pneumatic-operated hot plate welding machines are designed for welding large, flat components, such as automotive fuel tanks or washer tanks. These machines offer customizable options to fit specific production requirements. They utilize a hydraulic system to provide the necessary pressure for welding, ensuring high-quality welds for crate manufacturing.
5. Hydraulically Operated Hot Plate Welding Machines
Hydraulically operated hot plate welding machines are custom-designed to meet the specific needs of crate welding. These machines utilize hydraulic systems to provide the pressure required for welding. They are ideal for pressurized welding quality and can be tailored to meet the unique requirements of crate manufacturing.
Vimalssonic offers these hot plate welding machines, each designed to meet specific welding needs in crate manufacturing. Whether you require a standard machine or a customized solution, Vimalssonic has the expertise to provide you with a reliable and efficient hot plate welding machine.
How to Weld with a Hot Plate
Welding with a hot plate requires precision and careful execution. Here is a step-by-step guide on how to perform hot plate plastic welding for crates:
- Prepare the plastic parts: Ensure that the surfaces to be welded are clean and free from any contaminants. Proper surface preparation is essential for achieving strong and durable welds.
- Set up the hot plate welding machine: Depending on the specific hot plate welding machine you are using, follow the manufacturer's instructions to set up the machine. This may involve adjusting the temperature, pressure, and other parameters.
- Position the plastic parts: Place the plastic parts to be welded on either side of the hot plate. Make sure they are aligned correctly to ensure a precise weld.
- Heat the joining surfaces: Activate the hot plate to heat the joining surfaces of the plastic parts. The hot plate should be set to the appropriate temperature for the specific type of plastic being welded. The heating time will vary depending on the material and thickness of the parts.
- Remove the hot plate: Once the joining surfaces have reached the desired temperature and are molten, remove the hot plate from the joining area.
- Join the plastic parts: Quickly bring the heated parts together and apply pressure to create a strong bond. Hold the parts firmly in place until the molten plastic cools and solidifies.
- Allow the weld to cool: After joining the plastic parts, allow the weld to cool completely before handling or subjecting it to any stress.
- Inspect the weld: Carefully examine the weld for any defects or imperfections. Ensure that the weld is strong, free from voids, and meets the desired quality standards.
By following these steps and using the appropriate hot plate welding machine, you can achieve reliable and high-quality welds for crate manufacturing.
Advantages of Hot Plate Welding for Crates
Hot plate welding offers several advantages specifically for crate manufacturing. Let's explore the benefits in detail:
1. Strong and Durable Welds
Hot plate welding provides a strong and durable bond between plastic parts. This is crucial for crates, as they need to withstand heavy loads, rough handling, and various environmental conditions. The robust welds created through hot plate welding ensure that crates maintain their structural integrity and longevity.
2. Hermetic Sealing
In applications where airtightness is essential, hot plate welding excels. Crates used in industries such as food storage or hazardous material transportation often require hermetic sealing to prevent leakage or contamination. Hot plate welding creates seamless and reliable seals, ensuring the contents of the crates remain protected.
3. Versatility in Material Compatibility
Hot plate welding is compatible with a wide range of thermoplastic materials commonly used in crate manufacturing. Materials such as polyethylene, polypropylene, polycarbonate, ABS, and more can be effectively welded using hot plate welding techniques. This versatility allows manufacturers to choose the most suitable materials for their crates and still achieve strong and consistent welds.
4. Reproducible and Consistent Weld Quality
Hot plate welding provides reproducible and consistent weld quality, making it ideal for high-volume crate production. The process allows for precise control over welding parameters, resulting in uniform welds with minimal variation. This ensures that each crate meets the required quality standards, regardless of the production volume.
5. Aesthetic Appeal
Hot plate welding can create almost invisible weld seams, enhancing the overall appearance of the crates. This is particularly important for industries where aesthetics play a significant role, such as retail or consumer products. The ability to hide weld seams gives the crates a seamless and professional look.
Applications of Hot Plate Welding in Crate Manufacturing
Hot plate welding finds extensive use in crate manufacturing across various industries. Some common applications include:
- Storage and Transportation Crates: Hot plate welding is widely used to join plastic components in storage and transportation crates. The strong and durable welds ensure that the crates can withstand the rigors of handling and transportation.
- Food Storage Crates: Hot plate welding is crucial in the production of food storage crates, where hermetic sealing is essential to maintain the freshness and quality of the stored food items.
- Hazardous Material Crates: Crates used for storing and transporting hazardous materials require reliable and leak-proof seals. Hot plate welding ensures the integrity of these crates, preventing any leakage or contamination.
- Retail Display Crates: Hot plate welding allows for the creation of aesthetically pleasing retail display crates. The ability to hide weld seams ensures a seamless and professional look, enhancing the visual appeal of the crates.
- Agricultural Crates: Crates used in the agricultural industry, such as fruit and vegetable crates, benefit from the strength and durability provided by hot plate welding. The welds can withstand the weight of the produce and the demands of the agricultural environment.
These are just a few examples of how hot plate welding contributes to the manufacturing of high-quality and reliable crates for various industries.
Conclusion
Hot plate plastic welding is a versatile and effective method for joining plastic components, especially in crate manufacturing. With the ability to create strong, durable, and aesthetically pleasing welds, hot plate welding ensures the quality and performance of crates across various industries. By understanding the process, advantages, and applications of hot plate welding, manufacturers can make informed decisions and choose the right hot plate welding machine for their crate production needs. Embrace the power of hot plate plastic welding and take your crate manufacturing to new heights of quality and efficiency.