The Future of Tail Light and Lens Manufacturing: Harnessing the Power of Vibration Welding
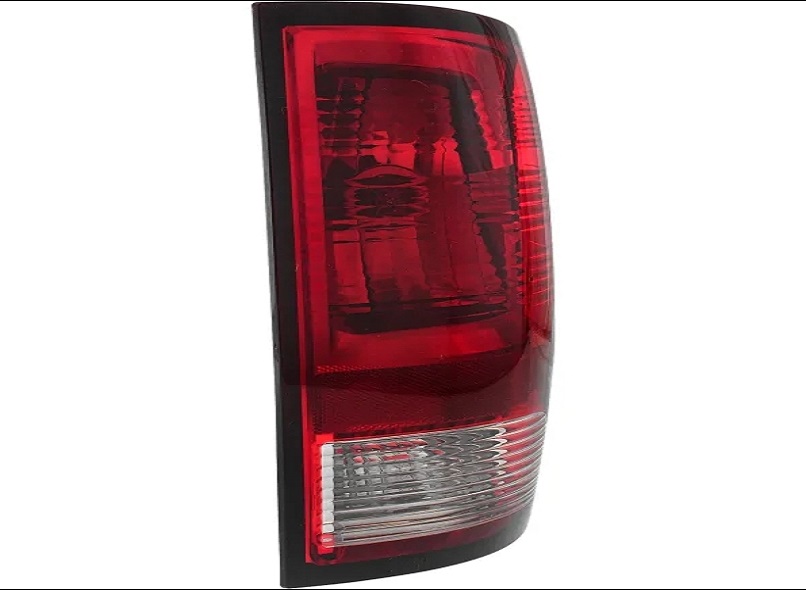
Automotive design has undergone a significant transformation over the years, with lights becoming more than just a functional necessity. Today, they serve as a design element, enhancing the aesthetics of the vehicle. One such component is the tail light and lens, the manufacturing of which has seen a shift towards using advanced techniques like vibration welding. This article delves into the world of tail light and lens manufacturing, focusing on the role of vibration welding in this process.
What is Vibration Welding?
Vibration welding is a groundbreaking technique that uses frictional heat to bond thermoplastic components. It involves holding two components in contact under pressure and vibrating them against each other. The heat generated by this friction melts the polymer where the parts join. The pressure, controlled by the machine, forces the melted plastic to flow away from the welding area, resulting in a smooth, hermetically sealed weld.
The Advent of Hybrid Vibration Welding
A more recent development in this field is hybrid vibration welding. This innovative technique incorporates an infrared (IR) preheat phase before the vibration process, softening the weld ribs and reducing the amount of particulate flash generated. The IR preheat phase involves bringing the two components near an infrared heating element to preheat the weld joint. Once the weld lines have begun to melt, the emitter is removed, the two parts are brought together under pressure, and a gentle vibration begins.
Advantages of Vibration Welding
Opting for vibration welding as your thermoplastic bonding technique comes with numerous advantages:
- Highly Customizable: Vibration welding machines are highly customizable, capable of meeting specific needs.
- Clean Weld Joint: Hybrid vibration welding minimizes particulate flash, enhancing weld aesthetics.
- Quality Assurance: The components used in these machines are from world-leading suppliers, ensuring safety and prompt availability of spares worldwide.
- Easy Maintenance: The strategic placement of components and the latest-generation electronic components make tooling maintenance and setup operations easier.
- User-friendly Interface: The graphical interface is intuitive, making language selection, parameter adjustment, and user-configured I/O as easy as the touch of a button.
- Ergonomic Loading: To minimize strain on the operator, the loading/unloading area is as close to the operator as possible, offering a shorter loading distance than any other machines in its class.
The Role of Vibration Welding in Tail Light and Lens Manufacturing
Tail light and lens manufacturing has seen a significant shift towards vibration welding due to its efficiency and versatility. Manufacturers can use this technique to bond complex shapes and sensitive electronic components without causing damage. The process also improves weld aesthetics, reduces particulate flash, and can handle materials that vary in hardness or structural consistency, such as composites.
In tail light manufacturing, vibration welding is used to assemble complex one-piece assemblies that can measure up to 1400 mm from side to side with complex multi-dimensional contours. The assemblies also house sensitive electronics such as sensors, radar devices, and cameras, along with the associated circuit boards and wiring, which are all safely welded using this technique.
Vibration Welding Machines: The Power Behind the Process
The success of vibration welding lies in the machines used. These machines are highly customizable and come with a range of features that make the process more efficient and effective. Some of these features include real-time tuning, wide rear opening, quick vibration stop, and easy maintenance.
Manufacturers can choose from several different hybrid vibration welder models, depending on their specific needs. These models range from small and efficient ones, ideal for welding small to medium size taillights, intake manifolds, and glove boxes, to larger ones capable of welding large rear lamps, intake manifolds, spoilers, etc.
Conclusion
As the automotive industry continues to evolve, so does the manufacturing process of its components. Tail light and lens manufacturing has embraced the power of vibration welding, harnessing its benefits to produce high-quality, aesthetically pleasing products. This innovative technique promises a bright future for tail light and lens manufacturing, contributing to the ever-evolving landscape of automotive design.
With the right vibration welding machine and a well-optimized process, manufacturers can take their tail light and lens manufacturing to new heights, ensuring their products stand out in the competitive automotive market.
The future of tail light and lens manufacturing lies in sophisticated techniques like vibration welding, promising efficiency, aesthetics, and quality in every product.