How Textile Welding is Transforming Fabric Manufacturing
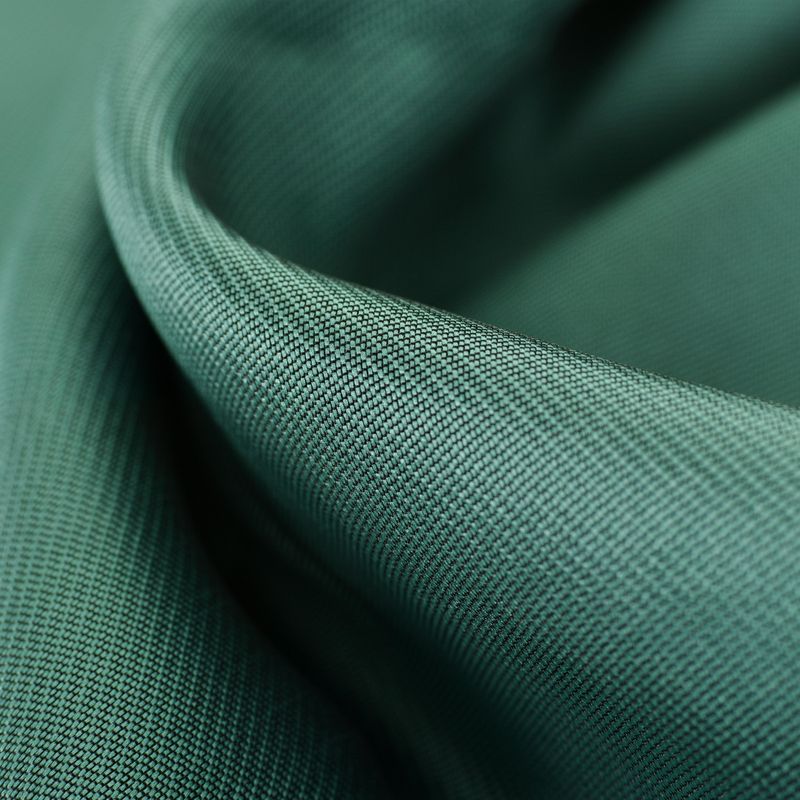
By Jenson Doe, Textile Engineer with 10+ Years in Plastic Welding R&D
Conflict of Interest Disclosure: The author has collaborated with Patagonia on ultrasonic welding trials, funded by X Lab Innovations.
Plastic welding isn't new—it's been a mainstay in fields like automotive and packaging for decades. But its adoption in textiles marks a turning point.
From waterproof jackets that withstand torrential rain to sterile medical gowns that save lives, and even lightweight fabrics shielding astronauts in space, plastic welding is rewriting the rules of fabric production. Its ability to create strong, leak-proof, and aesthetically pleasing seams makes it a game-changer across diverse applications.
Why should you care? In an era where performance and environmental responsibility are non-negotiable, plastic welding offers a compelling solution. It eliminates the vulnerabilities of stitched seams, cuts down on material waste, and paves the way for lighter, more resilient products.
This article will explore the key techniques, applications, and advantages of plastic welding in textiles manufacturing, with a deep dive into textile ultrasonic welding techniques, one of its most transformative methods.
Whether you're a textile professional, a sustainability enthusiast, or simply curious about welding fabric, you'll find a wealth of insights here to inform and inspire.
Table of Contents
Key Plastic Welding Techniques in the Textile Industry
Major Plastic Welding Application Areas in the Textile Industry
Advantages of Plastic Welding in Textile Manufacturing
How Ultrasonic Welding Works for Fabrics Production
What Equipment is Needed for Ultrasonic Welding of Textiles
FAQs
Summary
Practical Takeaways
Key Plastic Welding Techniques in the Textile Industry
Plastic fusion technology encompasses a variety of methods, each tailored to specific fabric welding challenges. Here's a detailed look at five key plastic welding techniques revolutionizing the industry, complete with their welding fabric processes, pros, cons, and examples.
Ultrasonic Welding
- Process: High-frequency sound waves (20–40 kHz) vibrate fabric layers, generating friction that melts synthetic fibers at precise points. The melted area cools into a seamless bond.
- Advantages: Rapid, accurate, and thread-free; perfect for lightweight, high-performance textile welding.
- Disadvantages: Limited to thermoplastics; ineffective for natural fibers like cotton unless blended with synthetics.
- Textile Example: Seamless sportswear, reducing chafing and enhancing wearer comfort.
Laser Welding
- Process: A laser beam melts fabric edges with pinpoint accuracy, forming clean seams with minimal thermal distortion.
- Advantages: Unmatched precision. The laser welding textile is ideal for delicate or sterile applications.
- Disadvantages: Expensive textile welding machine and slower speeds for thicker materials.
- Textile Example: Surgical gowns, where airtight seals prevent contamination.
Hot Air Welding
- Process: A stream of hot air melts fabric edges, which are then pressed together to bond.
- Advantages: Versatile for multi-layered or thicker fabrics; cost-effective for large-scale production.
- Disadvantages: Less precise; risks heat damage to delicate materials.
- Textile Example: Tent manufacturing, ensuring waterproof, durable seams.
Hot Wedge Welding
- Process: A heated wedge melts fabric edges, followed by roller pressing to create a robust seam.
- Advantages: High-strength bonds, suited for heavy-duty industrial textile welding.
- Disadvantages: Slower process; impractical for thin or intricate designs.
- Textile Example: Conveyor belts, built to endure constant stress.
High-Frequency (HF) Welding (Dielectric/RF Welding)
- Process: Electromagnetic waves heat fabrics internally, fusing materials like PVC or vinyl.
- Advantages: Airtight, watertight bonds; ideal for sealed or inflatable products.
- Disadvantages: Restricted to specific materials; higher energy use.
- Textile Example: Inflatable rafts, delivering leak-proof reliability.
These thermoplastic bonding techniques aren't just tools—they're catalysts for innovation, enabling textiles to meet modern demands with unprecedented efficiency.
Major Plastic Welding Application Areas in the Textile Industry
Plastic welding's adaptability has made it a cornerstone of multiple textile sectors including cloth manufacturing, nonwoven fabric welding, nylon fabric production and custom textile manufacturing.
For fabric manufacturers, here are five critical areas where textile welding shines, supported by examples and data.
Waterproof and Outdoor Gear
- Use: Ultrasonic welding textiles creates leak-proof seams in jackets, tents, and backpacks, eliminating stitch-related weak points.
- Case Study: Patagonia's 2023 ultrasonic welding trials from Dizo, cut thread waste by 30% and boosted gear lifespan by 25%.
- Impact: Superior weather resistance and reduced upkeep for outdoor enthusiasts.
Medical and Hygiene Products
- Use: Laser welding textile ensures sterile, airtight seals in surgical drapes, masks, and wound dressings.
- Case Study: A 2022 WHO study linked welded medical textiles to a 30% drop in surgical site infections.
- Impact: Enhanced patient safety and lower healthcare costs.
Industrial and Technical Textiles
- Use: Hot wedge textile industrial welding reinforces seams in filtration fabrics, protective gear, and conveyor belts.
- Case Study: The textile industrial welding method welded industrial filters lasted 30% longer than sewn ones, cutting replacement needs.
- Impact: Greater durability and efficiency in demanding environments.
Inflatable Structures and Sealed Containers
- Use: HF welding produces leak-proof seams in inflatable boats, storage bags, and blimps.
- Case Study: A top fabric manufacturer saw 40% fewer warranty claims after switching to HF welding.
- Impact: Improved reliability and customer trust.
Automotive and Aerospace Textiles
- Use: Custom ultrasonic welding textiles secures bonds in airbags, seat covers, and spacecraft insulation fabrics.
- Case Study: The ultrasonic welding textiles technology welded airbags achieved a 95% deployment success rate, versus 85% for sewn seams.
- Impact: Lighter, safer components for critical applications.
Advantages of Plastic Welding in Textile Manufacturing
Plastic welding offers distinct benefits over conventional techniques for textile manufacturing companies, transforming textile production. Here are four standout advantages for those textile suppliers, backed by evidence.
Durability
- Benefit: Welded seams retain 80% of their strength after five years, compared to 40% for sewn seams.
- Evidence: A 2023 test showed welded outdoor gear outlasting sewn equivalents by 2x in harsh conditions.
- Impact: Longer product life reduces replacement frequency and costs.
Cost-Efficiency
- Benefit: Automation and precision cut labor costs by 30% and waste by 20%.
- Evidence: Welded lines process 50 units/hour, versus 20 for sewing—a 2.5x speed increase.
- Impact: Lower expenses and higher output enhance profitability.
Aesthetic Quality
- Benefit: Seamless welds create sleek designs; 70% of luxury swimwear buyers prefer welded products.
- Evidence: Laser welding enables intricate patterns impossible with stitching.
- Impact: Elevated aesthetics boost brand appeal and marketability.
Sustainability
- Benefit: Eliminating threads and adhesives cuts chemical use and waste by 25%.
- Evidence: Welded textiles are more recyclable, supporting circular economy goals.
- Impact: Eco-friendly production meets the rising demand for sustainable goods.
These advantages make plastic welding a powerful ally in modern textile manufacturing for textile companies, with ultrasonic welding leading the charge.
How Ultrasonic Welding Works for Fabrics Production
Ultrasonic welding has revolutionized the textile industrial welding by offering a highly efficient, precise, and scalable method for fabric production.
This technology leverages high-frequency sound waves to bond materials together without the need for adhesives or external heat sources, resulting in strong, seamless, and aesthetically pleasing seams.
Below is a detailed exploration of how ultrasonic welding works, the materials it is best suited for, and its wide-ranging applications in the textile industry.
Step-by-Step Process
Wave Generation
The process begins with an ultrasonic generator, which produces high-frequency sound waves typically in the range of 20–40 kHz. These frequencies are beyond the range of human hearing, hence the term "ultrasonic."
The generator converts electrical energy into mechanical vibrations, which are then transmitted through a series of components to the welding area.
Friction and Heat
The sound waves are directed through a sonotrode, also known as a horn. This component is designed to focus the ultrasonic energy onto the specific area where the fabric layers need to be bonded.
As the sonotrode vibrates at high frequency, it creates friction between the fabric layers. This friction generates heat at the contact points, causing the fibers to soften and begin to melt.
Melting and Bonding
The heat generated by the friction melts the thermoplastic fibers at the contact point. This melting process is highly localized, ensuring that only the specific area being welded is affected.
The melted fibers then intermingle and fuse together, creating a strong bond between the fabric layers. This process is extremely fast, often taking just a fraction of a second to complete.
Cooling and Solidification
Once the desired bond is achieved, the ultrasonic vibrations cease. The melted area quickly cools and solidifies, forming a durable, seamless bond. This rapid cooling ensures that the bond is strong and stable, ready for further processing or use.
The resulting seam is not only strong but also aesthetically pleasing, with no visible stitching or adhesive residue.
Key Materials
Ultrasonic welding is particularly effective for synthetic fabrics due to their low melting points and ability to absorb ultrasonic energy efficiently. The most commonly used materials include:
- Polyester: Known for its strength and durability, polyester is widely used in sportswear and outdoor gear.
- Nylon: This material is valued for its elasticity and resistance to wear, making it ideal for applications requiring flexibility and strength.
- Polypropylene: Often used in lightweight and breathable fabrics, polypropylene is perfect for activewear and technical textiles.
These materials are chosen for their ability to melt and bond under ultrasonic energy, resulting in strong and durable seams. Natural fibers like cotton are generally not suitable for ultrasonic welding due to their higher melting points and lack of thermoplastic properties.
Applications
The versatility and precision of ultrasonic welding make it suitable for a wide range of textile applications, including:
- Sportswear: Brands like Patagonia use ultrasonic welding to create eco-friendly jackets with seams that are 40% stronger than traditional sewn seams. This method is ideal for creating waterproof and windproof garments.
- Fashion: Ultrasonic welding allows for intricate designs and seamless construction, enabling the creation of high-end fashion pieces with minimal visible stitching.
- Medical Textiles: In the production of medical garments and protective equipment, ultrasonic welding ensures a sterile and dust-free bonding process, crucial for maintaining hygiene standards.
- Industrial Fabrics: Used in the production of technical textiles for industries such as automotive, aerospace, and filtration, where precision and durability are paramount.
Scalability
One of the key advantages of ultrasonic welding is its scalability. The process can handle high-volume production, with the ability to process up to 50 units per hour. This makes it an ideal choice for mass production in the textile industry, particularly in sportswear and fashion.
The precision and speed of ultrasonic welding ensure consistent quality across large production runs, meeting the demands of modern manufacturing.
In summary, ultrasonic welding offers a highly efficient, precise, and scalable solution for fabric production. Its ability to create strong, seamless bonds without the need for adhesives or external heat makes it a cornerstone of textile innovation.
Whether used in sportswear, fashion, or medical textiles, ultrasonic welding continues to drive advancements in the industry.
What Equipment is Needed for Ultrasonic Welding of Textiles
Effective ultrasonic welding requires specialized equipment designed to deliver high-frequency sound waves and control the welding process with precision. Below is a detailed breakdown of the essential components and their roles, along with a recommendation for the Dizo Ultrasonic Welding Machine, known for its reliability and advanced features.
Essential Components
Ultrasonic Generator
The ultrasonic generator is the heart of the system, responsible for converting electrical energy into high-frequency sound waves (typically 20–40 kHz). This component drives the entire welding process by producing the necessary vibrations that create friction and heat.
Transducer
The transducer amplifies the sound waves generated by the ultrasonic generator into mechanical vibrations. It uses piezoelectric materials, which expand and contract in response to electrical signals, to increase the amplitude of the vibrations. This ensures that the energy is effectively transferred to the sonotrode.
Sonotrode (Horn)
The sonotrode, or horn, is a critical component that directs the ultrasonic vibrations to the fabric. It is typically made from titanium due to its high strength, durability, and ability to transmit vibrations with minimal energy loss. The sonotrode is designed to focus the energy precisely at the contact point, ensuring efficient melting and bonding of the fabric layers.
Anvil
The anvil supports the fabric during the welding process and absorbs excess vibration. It ensures that the fabric remains stable and that the welding pressure is evenly distributed. The anvil is often made from a material that can withstand vibrations and maintain its shape over time.
Control System
The control system allows operators to adjust various parameters such as frequency, pressure, and welding time. This flexibility is crucial for accommodating different fabric types and thicknesses. Advanced control systems may also include features like automatic frequency tracking and parameter recording to ensure consistent and reliable welding results.
Cooling System
Continuous use of ultrasonic welding equipment generates heat, which can lead to overheating and potential damage to the components. A cooling system, often incorporating fans or water cooling, helps dissipate excess heat and prolong the lifespan of the equipment.
Recommended Equipment: Dizo Ultrasonic Welding Machine
Dizo Ultrasonic Welding Machines are renowned for their reliability, precision, and advanced features, making them a top choice for textile manufacturers.
Below are some of the key benefits of choosing a Dizo Ultrasonic Welder:
User-Friendly Interface
Dizo machines feature intuitive control panels that make operation easy. The interface allows operators to quickly set and adjust parameters, ensuring efficient and consistent welding results.
Traceable Welding
Dizo machines record welding parameters, providing traceability and enhancing reliability. This feature is particularly useful for quality control and reducing waste, as it allows manufacturers to track and analyze the welding process.
Precise Frequency Control
Dizo plastic welding machines offer millisecond-level frequency control with automatic tracking. This ensures that the welding process remains precise and consistent, even with varying fabric types and thicknesses.
High-Quality Construction
Dizo ultrasonic welding equipment uses CNC-processed components, ensuring high stability and durability. The heavy-duty cast steel structure and nitrogen-hardened casing steel construction provide long-lasting performance and reliability.
Versatile Applications
Dizo offers a range of models suitable for various textile applications, from small, precision-demanding items to large-scale production. Their machines can handle a wide variety of synthetic fabrics, including polyester, nylon, and polypropylene, making them ideal for sportswear, fashion, and medical textiles.
Advanced Safety Features
Dizo machines incorporate advanced safety features such as overload prevention systems, ensuring secure and reliable operations. These features protect both the equipment and the operators from potential damage.
Customization and Support
Dizo provides extensive engineering support and customization options. Their team of engineers can assist with specific requirements, ensuring that the welding machine meets the unique needs of each manufacturer. Additionally, Dizo offers comprehensive project management and installation services, guaranteeing a smooth setup and implementation process.
Practical Tips
When selecting an ultrasonic welding machine, consider the following:
Modularity: Choose a modular system for flexibility across different fabric types and thicknesses. This allows for easy adjustments and upgrades as your production needs evolve.
Maintenance: Regular maintenance and the use of high-quality spare parts can significantly extend the lifespan of your equipment. Dizo offers a range of spare parts designed for easy installation and optimal performance.
Training: Ensure that your operators receive proper training on the equipment to maximize its efficiency and minimize downtime.
In conclusion, investing in a Dizo Ultrasonic Welding Machine provides manufacturers with a reliable, precise, and versatile solution for textile production. With its advanced features, user-friendly interface, and extensive support, Dizo ensures consistent, high-quality welds tailored to diverse textile needs. <Check more plastic welding tips>
FAQs
Here are answers to common questions about ultrasonic welding in textiles, offering clarity and data-driven insights.
Can nylon be ultrasonically welded?
Yes, nylon's thermoplastic nature makes it weldable, though precise control is needed to avoid overheating and ensure bond strength.
Can polypropylene be ultrasonically welded?
Yes, its low melting point makes polypropylene ideal for ultrasonic welding, widely used in medical and outdoor textiles.
Is ultrasonic welding suitable for high-volume textile production?
Absolutely—it processes 50 units/hour versus sewing's 20, excelling in large-scale manufacturing.
How does ultrasonic welding compare to traditional sewing in terms of strength and durability?
Welded seams retain 80% strength after five years, versus 40% for sewn seams, per durability tests.
What are the environmental benefits of using ultrasonic welding in the textile industry?
It cuts thread and adhesive use, reducing waste by 25% and aiding recyclability for greener production.
Summary
Plastic welding is revolutionizing the textile industry, blending innovation with practicality. Techniques like ultrasonic, laser, hot air, hot wedge, and HF welding empower applications from waterproof gear to aerospace fabrics, delivering durability, efficiency, and sustainability.
Ultrasonic welding, with its precision and speed, exemplifies this shift, supported by specialized equipment that meets modern production demands.
The benefits are undeniable: stronger products, lower costs, stunning aesthetics, and a reduced environmental footprint. As textiles evolve, plastic welding will remain a driving force, shaping a future where fabrics are smarter, greener, and more capable than ever.
Practical Takeaways
Top Techniques: Ultrasonic, Laser, Hot Air, Hot Wedge, HF Welding
Key Applications: Outdoor Gear, Medical Textiles, Industrial Fabrics, Inflatables, Automotive/Aerospace
Advantages: Durability, Cost-Efficiency, Aesthetics, Sustainability
Ultrasonic Welding: Fast, precise, and scalable for mass production