PP Ink Cartridge Welding
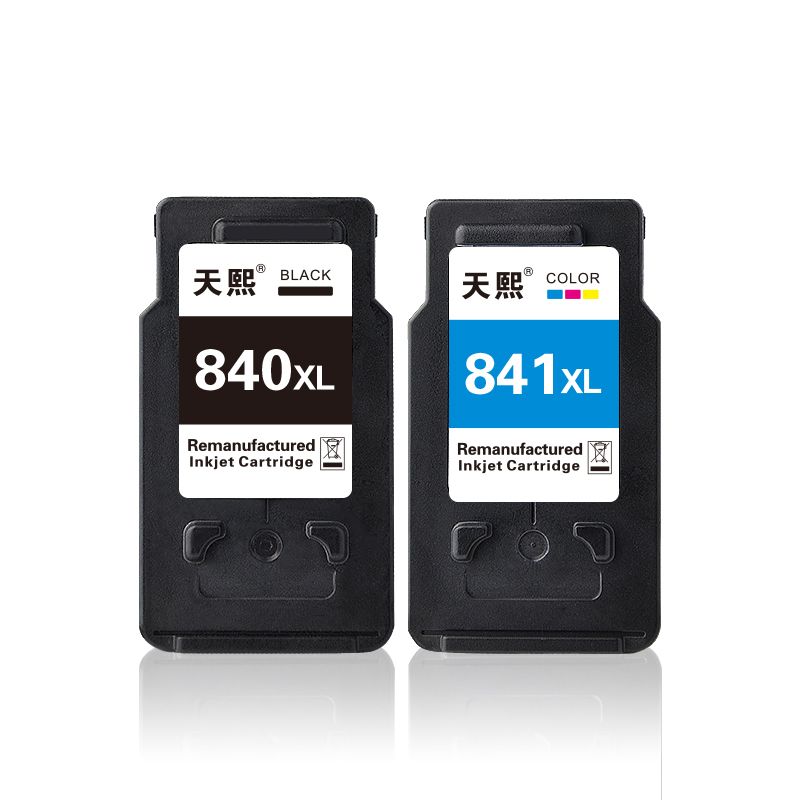
Working Principle of the PP Ink Cartridge Ultrasonic Welding Machine
The PP Ink Cartridge Ultrasonic Welding Machine operates by transforming a low-frequency electrical signal (15/20Hz) into high-frequency electrical energy (20KHz or 40KHz) using a transistor-based functional device.
This high-frequency energy is then supplied to a converter, which converts it into mechanical vibration energy suitable for ultrasonic welding. A voltage regulation device transmits the transformed mechanical energy to the welding machine's welding head.
The welding head is an acoustic device that directly transmits mechanical vibrations to the surfaces of the products being bonded. These vibrations create frictional heating between the bonding surfaces, causing the plastic to melt.
Once the molten material reaches the interface, the vibrations cease, and pressure is maintained briefly to allow the molten plastic to solidify, forming strong molecular bonds. This entire welding cycle typically completes in less than a second, yet the welding strength approaches that of a single, unified material.
Features of the PP Ink Cartridge Ultrasonic Welding Machine
Concentric Direct-Axis Design:
Prevents rear tilting, enhancing welding precision.
Imported Pneumatic Components:
Utilizes high-quality imported pneumatic parts for durability and longevity.
Adjustable Limiting Mechanism:
Equipped with a limit device for fine-tuning, ensuring uniform welding and increasing product pass rates.
Gear-Based Elevation and Descent:
Features a gear-driven up-and-down design for easy adjustments, facilitating smooth welding operations.
Four Horizontal Screw Adjusters for Transducer Groups:
Allows for convenient and accurate adjustments of the transducer assemblies.
Separate Speed Adjustment for Elevation and Descent:
Enhances work efficiency by independently controlling the ascent and descent speeds.
Overload Protection Circuit:
Incorporates overload protection for current and frequency.
Utilizes high-quality European and Japanese components, ensuring superior quality and strong output.
Three-Digit Digital Rotary Switch for Time Control:
Offers adjustable precision up to 1/100 of a second.
Simplifies adjustments and reduces failure rates.
Applications of the PP Ink Cartridge Ultrasonic Welding Machine
The Ultrasonic PP Ink Cartridge Welding Machine is specifically designed for welding PP ink cartridges, toner cartridges, and plastic outer shells of ink cartridges. By changing molds, it can also be applied to the following fields:
Motor Industry:
Transformers (e.g., oil transformers)
Batteries
Electronic rectifiers
Switch plugs
Relays
Chargers
Motor fan blades
Screw insertions
Home Appliance Industry:
Washing machine balance rings
Steam irons
Remote controls
Fan blades
Cosmetics Industry:
Lipstick shells
Cream containers
Makeup boxes
Food Industry:
Food containers
Thermoses
Meal boxes
Stationery Industry:
PP document folders
Pen holders
Staplers
Ink boxes
Photo albums
Electronics Industry:
Cassette tape cases
Computers
Electronic watches
VCRs
Disk drives
Ribbon tapes
Buzzers
Mobile phone cases
Monitor panels
Toy Industry:
Remote-controlled cars and boats
Plastic dolls
Water guns
Electronic pets
Transportation Industry:
Car light housings
Filters
Reflectors
Speedometers
Horns
Medical Industry:
Thermometers
Medium-efficiency bags
Blood filtration bags
Hose sealing ends
Daily Essentials:
Electric toothbrushes
Plastic lighters
Game consoles
Electric shavers
Thermos bottles
Teacups
Apparel Industry:
Embossing and stamping
Shoe upper rhinestone setting
Denim rhinestone setting
Shoe upper flattening
Punching and cutting
Summary
The PP Ink Cartridge Ultrasonic Welding Machine offers robust and versatile solutions for welding large, irregular, and specialized plastic products. The advanced temperature control, precise mechanical design, and high-quality components make it an essential tool across various industries, including automotive, electronics, home appliances, and more.
By addressing the limitations of traditional welding methods, these machines ensure high-quality, airtight, and durable welds, thereby enhancing product reliability and market competitiveness.