Car Plastic Tank Hot Plate Welding: Process, Benefits & Tips
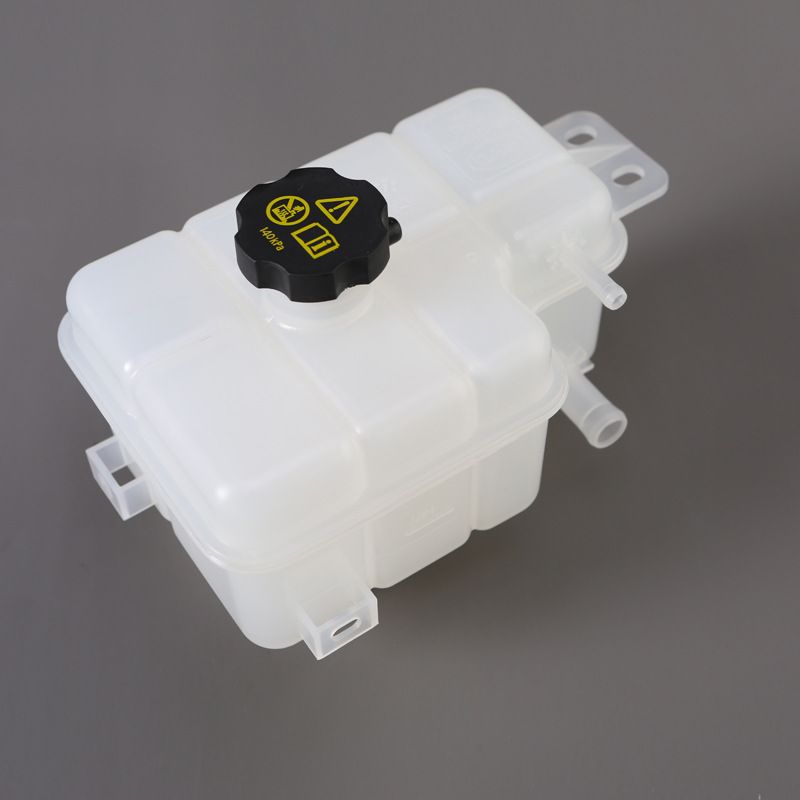
Hot plate welding is a common and reliable way to join plastic parts. For car plastic tank welding, it creates strong and durable bonds that can handle pressure and stop leaks. This welding method is popular in manufacturing because it's fast and produces great results.
For this purpose, industries need a car plastic water tank welding machine. Industries commonly implement hot plate plastic welding as their standard industrial method to unite thermoplastic components. A heated plate heats the mating surfaces of two plastic components before they are pressed together, allowing a strong bond to form upon cooling.
This guide will explain what a car plastic tank welding machine is in simple terms. You'll learn the basics, how it works, and why it's useful. Whether you work with cars or just want to know how to make a plastic water tank, this guide will give you easy-to-understand information.
Table of Contents
What is Car Plastic Tank Hot Plate Welding?
Working Steps of Car Plastic Hot Plate Water Tank Welding Machine
Advantages of Using Plastic Tank Hot Plate Welding Machine
Features of Dizo's Car Plastic Tank Hot Plate Welder
Step-by-step Car Plastic Tank Welding Process
Common Water Tank Welding Mistakes and How to Avoid Them
The Bottom Line
FAQs
What is Car Plastic Tank Hot Plate Welding?
Hot plate welding technology is used to fuse plastic fuel tanks, coolant reservoirs, or washer fluid tanks by melting their edges against a heated plate and then pressing them together for a strong, leak-proof seal.
The hot plate welder is an industrial welder that combines plastic automobile components including pp tanks, hdpe tanks, pvc tanks (poly tanks) by heating their edges on a temperature-adjustable plate before fusing them with pressure. The two plastic tank pieces receive fixture-mounted clamping.
Furthermore, the joining surfaces undergo melting when exposed to the temperature-regulated hot plate, which operates between 200–300°C. The hot plate retracts quickly. The pressed molten edges cool down before they become a single watertight element.
Working Steps of Car Plastic Hot Plate Water Tank Welding Machine
For seamless plastic gas tank welding, the following are the primary steps of plastic weld for gas tanks that are performed in fuel tank fabrication:
Clamping
Business-grade thermoplastic components must be firmly attached to specific positional fixtures or jigs during plastic welding water tank. Correct alignment, along with welded part stabilization, remains possible through this method. Between the two plastic components, they need to bond an operator who positions a plate at high heat temperature.
The hot plate warms the mating surfaces until they become meltable. The welder manages temperature, pressure, and heating duration according to material specifications.
Joining Phase
Under controlled pressure, the two surfaces are brought into contact with each other. During the joining process, molecular diffusion forms between the melted plastics, which results in their fusion and creates a strong bond.
Cooling & Solidification
The plastic tank welding require pressure during its cooling period until the joining zone attains a solid shape. The operator removes the part by opening the fixtures.
Plate Removal
The hot plate moves back when the desired melting stage becomes ready.
Advantages of Using Plastic Tank Hot Plate Welding Machine
The following are the advantages of using storage tank hot plate welding technology in water tank fabrication:
- Strong and Durable Joints: The plastic tank hot plate welder creates secure and long-lasting joints, ensuring the plastic tanks stay reliable over time.
- Efficient Manufacturing: This fuel tank welding method helps save time by quickly producing high-quality tanks without delays.
- Leak-Proof Seals: The water tank welding process ensures perfect seals, preventing any fuel or liquid leaks in the tanks.
- Safe to use: The gas tank welding equipment is designed with safety in mind, making it user-friendly and reducing risks during operation.
Features of Dizo's Car Plastic Tank Hot Plate Welder
The car plastic tank hot plate welders from Dizo deliver precise plastic gas tank welding capabilities for automotive plastic fuel tanks, as well as reservoirs and large plastic components. The following list describes the major characteristics of these machines used for tank fabrication and welding:
High-Precision Welding Technology
Automotive plastic tanks receive leak-resistant tight welds through this application. The plastic gas tank welding equipment provides equal heat distribution, which leads to uniform welding results.
Advanced Temperature Control
Digital PID temperature controllers for accurate heat regulation. Plastic materials avoid reaching dangerously high or low temperatures during the manufacturing process.
Robust Construction & Durability
The plastic welding machine for gas tank includes a framework built to withstand industrial environments. The plastic welding water tank system includes extended heating plates, which endure repeated use.
Customizable Welding Solutions
Users can adjust their welding parameters regarding time and temperature, along with pressure levels for various plastic materials like HDPE, poly and PP. The controls work efficiently with different tank dimensions and forms.
Automated & Semi-Automated Options
PLC-controlled systems for repeatable, high-quality welds. Robotic arm capabilities exist for automated part movement in specific model types.
Energy Efficiency
The integration of energy-efficient heating technology lowers production expenses. The faster heating and cooling processes increase manufacturing efficiency.
Safety Features
The poly tank welding, pp tank welding, and hdpe tank welding system includes safety mechanisms to detect overheating conditions and emergency stop situations. The hot plate welding equipment includes insulated panels that shield operators from burns.
Applications
The devices serve three main functional areas, which include fuel storage in automotive vehicles, fluid storage in reservoirs, and large plastic storage containers. Suitable for HDPE, PP, and other thermoplastic materials.
After-Sales Support
Technical support, along with maintenance services and spare parts availability, is commonly provided by Dizo. These welders are suitable for automotive manufacturers and plastic tank producers that require structurally robust welding solutions.
Step-by-step Car Plastic Tank Welding Process
The following is the process through which this plastic water tank welder works:
Step 1. Safety First
Hot plate welders must protect themselves by using a welding helmet combined with protective gloves and boots alongside long sleeves. Maintain your work environment and keep it ventilated it prevent fumes from building up. Keep a fire extinguisher nearby.
Step 2. Prepare the Metal
Use either a wire brush or grinder to clean off rust from metal surfaces and eliminate any paint or dirt buildup. Clamp the pieces together if needed.
Step 3. Set Up the Welder
Select a plastic tank welding machine from the stick, MIG, and TIG options.
Step 4. Using the Strike the Arc (stick or TIG welding)
Touch the electrode (stick) or tungsten (TIG) to the metal surface before swiftly raising it for an arc creation.
Step 5. Start Welding
Make sure the torch or electrode maintains an approximately 15–20-degree angle. Travel at a controlled speed through direct paths or smaller orbital motions to liquefy the metal while adding a filler rod (if used).
Step 6. Fill the Joint
The flow of melted metal from the electrode or filler rod should bridge the space between joint pieces. Then, stop fuel tank welding by lifting the torch or electrode away from the workpiece.
Step 7. Let It Cool
Let the plastic weld for gas tank cool down naturally without using water to expedite the process.
Step 8. Clean the Weld
The removal of slag (black crust) requires either a chipping hammer (for stick welding) or a wire brush.
Common Water Tank Welding Mistakes and How to Avoid Them
For plastic oil tank manufacturers, car plastic storage tank hot plate welding appears simple, yet minor mistakes will break the entire welding process. The basic solutions explained below address the typical mistakes that occur during car plastic parts hot plate welding:
1. Wrong Temperature Setting
When the heat becomes excessive, it results in the plastic melting into a ruinous state.
Fix: Determine the plastic type, whether PP or ABS, and choose proper temperature settings that range between 200–300°C.
2. Dirty or Oily Plastic
The presence of grease, as well as dust and mold release agents, creates weld weaknesses.
Fix: Use isopropyl alcohol wipes to clean off both parts before welding commences.
3. Rushing the Melt
Extracting parts from the hot plate prematurely results in a weak bond.
Fix: Continue by leaving the plastic on the plate until it becomes shiny while barely drooping.
4. Uneven Pressure
Strong force application will lead to extruded plastic from the connection point.
Fix: The machine needs correct adjustment to press the parts with steady force.
5. Skipping Alignment Checks
Weak and ugly welds will result from misaligned parts.
Fix: Follow the provided alignment pins or jigs for machines that incorporate this feature.
6. Ignoring Cooling Time
One error involves the early movement of the part because this action creates warped or cracked joints.
Fix: The welding process requires natural cooling for a minimum of one minute or according to material specifications.
7. Wrong Plastic
Mix The attempt to connect different plastic materials like PP to ABS results in consistent failure when welding.
Fix: Match the materials! Use recycling codes or perform a trial weld to verify if welding the materials is possible.
8. Letting the Plate Get Gunky
Using burnt plastic destroys the plate's functionality, which results in uneven heating and contamination sources.
Fix: A brief silicone or PTFE coating application should be used to stop materials from sticking.
9. No PPE (Personal Protective Gear)
Accidental contact with the hot plate or inhaling fume vapors will produce physical pain.
Fix: It is best to work in a ventilated area when handling dirty plastic during the melting process.
10. Not Testing the Weld
A part could fail later because of incorrectly assuming its strength.
Fix: Gently test the piece with bends because any cracking or peeling requires you to redo the work.
The Bottom Line
In conclusion, the Car Plastic Tank Hot Plate Welder is a reliable and efficient solution for plastic tank manufacturing durable and safe plastic fuel tanks. Its ability to create leak-proof seals, save time, and ensure user safety makes it an essential tool in the industry.
This advanced technology simplifies the production process while delivering high-quality results for plastic oil tank manufacturers. Dizo provides various welding solutions according to your needs and offers after-sales support for their solutions. A range of various payment options is accepted.
FAQs
What types of plastic materials are compatible with the Dizo Car Plastic Tank Hot Plate Welder?
Thermoplastics like PP, PE, ABS, PC, PET, PMMA, PVDF, and PVC are compatible with the Dizo automotive plastic tank welding machine.
How can I ensure consistent weld quality?
To obtain consistent weld quality with the Dizo car plastic water tank welding machine, many factors are involved, including temp control, optimal pressure, and regular machine maintenance.
What maintenance does the hot plate welder require?
The hot plate welder's daily maintenance includes cleaning the hot plate, checking temperature accuracy, and inspecting heating elements. The weekly maintenance includes lubing the moving parts, tightening fixtures and fasteners, and inspecting the hydraulic and pneumatic systems.
What safety measures should I follow while using the equipment?
A user operating the welding machine must be equipped with proper protective gear to avoid burns and electric shocks. Proper ventilation should be at the place of welding. First aid kits must be nearby.