The Role of Hot Plate Welders in Modern Plastic Pallet Manufacturing
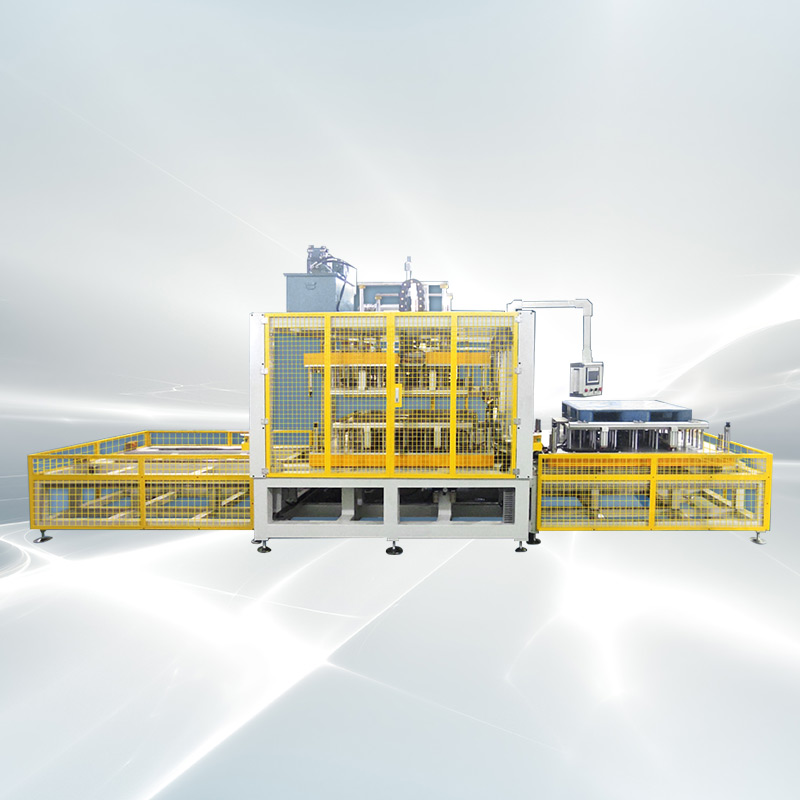
Plastic pallets are the backbone of modern supply chains, valued for their durability, lightweight design, and affordability. But what ensures these pallets can handle the most challenging jobs? It all comes down to precision manufacturing and reliable equipment like the hot plate welder.
Manufacturers face the most crucial challenge of creating welds that resist heavy loads and challenging environmental factors. Weak welds during manufacturing will lead to pallet failure, along with damaged goods at higher costs and potential safety risks.
Hot plate welders prove their worth in such applications. The welding machines produce durable welded seams that enhance plastic pallet durability so supply chains maintain their operational efficiency.
Want to know how hot plate welding is changing plastic pallet manufacturing? Keep reading to learn how this process works and how it can improve your manufacturing!
Table of Contents
What are Hot Plate Welders?
Advantages of Using Hot Plate Welders for Plastic Fabrication
The Need for Hot Plate Welders in Plastic Pallet Manufacturing
Key Features of Dizo's Hot Plate Welders
The Future of Hot Plate Welding in Plastic Pallets
Concluding Thoughts
FAQs
What are Hot Plate Welders?
Hot plate welders function as industrial machines that fuse thermoplastic components through surface heat application to a hot plate, followed by mechanical joint formation after material cooling. Hot plate welding equipment find extensive use in manufacturing because they enable manufacturers to create plastic joints with security and airtight seals.
Moreover, hot plate welding enables thermoplastic component fusion through its thermal method, which blends surfaces using heated metal plates before combining parts with a permanent bond after cooling.
Hot Plate Welding requires three essential procedures, including heating the materials on the hot plate until they melt and then pressing them together until they solidify.
Two plastic parts need to be placed on a heated hot plate operating between 180–400°C until the surfaces attain melt state. The operating hot plate moves away after completion. The molten surfaces align during controlled pressure applications to be joined properly during their cooling stage.
Features and Components of Hot Plate Plastic Pallet Welders
Hot plate plastic pallet welders, such as those offered by Dizo Global, are engineered with advanced technology to deliver power and reliable welding solutions.
Here are some of the standout features and components that make these machines ideal for plastic pallet manufacturing:
1. Precision Heating Elements
The hot plate welder is equipped with highly accurate heating plates that ensure even heat distribution. This uniformity minimizes defects and ensures that every weld is strong and consistent, meeting industry standards for durability.
2. Adjustable Temperature Controls
Advanced temperature control systems allow manufacturers to customize the heat settings based on the type of plastic material being welded. This versatility ensures compatibility with a wide range of thermoplastics.
3. Sturdy Machine Frame
Built with a durable and stable frame, the hot plate welder is designed to support the demanding requirements of large-scale pallet manufacturing. The strong structure prevents vibration during operation, ensuring precision.
4. Automated Operation
Many hot plate plastic pallet welders feature automated functions to improve efficiency and reduce manual intervention. This includes automatic cycle times and programmable welding parameters, streamlining the production process.
5. Versatile Clamping Systems
These machines come with flexible clamping systems that can accommodate various pallet sizes and designs. Adjustable clamps ensure secure positioning of the parts, resulting in reliable and seamless welds.
6. Advanced Safety Features
Safety remains a top priority, and these welders include features such as thermal insulation, emergency stop buttons, and protective enclosures to safeguard operators during operation.
Advantages of Using Hot Plate Welders for Plastic Fabrication
Hot plate welders function as dependable tools that construct durable plastic welds, which manufacturers rely on for their applications requiring tough yet strong connections. The following benefits explain why manufacturers select this equipment for their operations:
The hot plate welding machines are ideal for sealing components since they create total air and liquid-tight connections. Plastic fuel tanks and chemical containers require leak-resistant seals since leaks are unacceptable. A hot plate welder forms an airtight connection that surpasses other joining methods.
These machines have an unexpectedly basic structure compared to other expectations. There are no fancy lasers or ultrasonic vibrations, just good old-fashioned heat and pressure. Users benefit from these machines because they function reliably, require less maintenance than advanced options, and have low operating expenses.
The Need for Hot Plate Welders in Plastic Pallet Manufacturing
Hot plate welders play a crucial role in ensuring consistent and durable bonds between plastic components, making them indispensable in the manufacturing of high-quality pallets.
Challenges in Producing Durable Plastic Pallets
Plastic pallets must be strong and reliable. They go through rough handling and heavy loads. Cracks or weak joints can cause failures. This creates problems for manufacturers and end users. Ensuring durability is a big challenge in the production process.
This resource offers valuable insights and practical tips that can help beginners master the art of welding more effectively.
Why Traditional Methods Fall Short?
Traditional joining methods, like adhesives or screws, have limits. Adhesives may weaken over time or with temperature changes. Screws can create stress points and are not always precise. These methods often fail to provide consistent strength and lasting bonds.
How Does DIZO Hot Plate Welding Address These Challenges?
DIZO hot plate welders provide a strong solution. They create tough, seamless joints. The process is precise and ensures consistent results.
Welds made with these machines can handle heavy loads and tough conditions. This improves product quality and reduces failures. Manufacturers can produce durable pallets with greater confidence.
Key Features of Dizo's Hot Plate Welders
Dizo provides industry-leading hot plate welders to automate plastic pallet creation through their rugged, heavy-duty equipment. The following features make these Dizo welders stand apart in the plastic pallet manufacturing industry:
1. High-Strength Joint
Dizo's industrial welders possess tank-like strength, which suits the demanding requirements of pallet manufacturing.
The welders produced by Dizo feature industrial-grade steel frames that withstand both heavy loads and intense vibrations. This equipment stays solid while welding both thick pallet leg pieces and large deck panels. That's Dizo!
2. Precision Heating-No Guesswork
The process of toasting bread often results in one side overcooked while the other remains cool. Welders at Dizo operate their machines without the manual temperature control method.
The machines feature heated plates with dual-temp control down to ±1°C precision to ensure complete pallet melting across all sections. No weak spots, no drama.
3. Smarter Than Your Average Welder
The machines offer touchscreen interfaces that function similarly to premium tablet operating systems to let you store various pallet fabrication methods called "recipes".
Swap from a nestable to a rackable pallet? Pressing a preset button allows you to skip repeat processes instead of creating wheel reinvention efforts.
4. Power That Doesn't Quit
When you require fusing extremely substantial HDPE under intense pressure conditions, what do you do?
Hydraulic or servo-driven presses in Dizo systems bring industrial muscle that operates without human exhaustion. The welding equipment works just as well with recycled plastic materials. Welders easily adjust to any situation without complaining.
Time is Money
Dizo provides quick-change tooling capabilities. Thus, running new pallet designs should never require substantial machine downtime periods.
Dizo provides users with quick and contamination-free system changes through its replaceable mold system together with PTFE-coated plates. Less sticking, more welding.
Safety That Works
Operational elements such as hot plates and hydraulics combined with hot plastic feel like they belong in an action sequence. The machines from Dizo feature integrated emergency stops with heat shields and automatic cooling systems, which maintain safety for your shop facility and keep OSHA satisfied.
The Future of Hot Plate Welding in Plastic Pallets
Plastic pallets will remain in industrial use because they offer numerous advantages over wooden and cardboard alternatives. Plastic pallets provide superior strength compared to cardboard, and they are more efficient to sanitize in addition to their lower weight than wood pallets.
Hot plate welding operates at new levels when supply chains develop smart systems because sustainability requirements become mandatory. Here's what's coming:
1. Set it and Forget it Principle
The new generation of hot plate automation systems works on a basic "set it and forget it" principle. A welding machine will adapt to tasks while working without human intervention. Hot plate machines of the future will use AI sensors that automatically control temperature and pressure at the moment, so operators will eliminate the need for manual adjustment.
A pallet design modification or unpredictable behavior of recycled materials causes what to happen to the welding equipment and process. Before the slightest problem arises, the welder automatically adjusts itself.
2. Green Machines for Green Pallets
The growing market demand for sustainable pallets makes hot plate welding a perfect choice for creating complete recycled plastic products. Modern welders can now perform strong connections on recyclable plastic materials, including low-quality plastic from grocery bags.
Bonus? Energy-efficient induction heating systems present a 30 percent reduction in power use, which would optimize industrial operations through economical and environmentally sustainable manufacturing practices.
3. Pallets That Talk Back
Of what use is basic pallet welding when you have the opportunity to upgrade the pallet? Tomorrow's welding procedures should add RFID or IoT sensors to pallets, which will function as smart tracking objects that locate and measure pallet conditions.
Hot plate welding forms imperceptible joints that defend electronic components from damage by preventing wire detachments and exterior casing fractures.
4. Speed Without Sacrifice
New mold development, along with fast-cooling technology systems, is reducing hot plate welding cycle times. The production of stable pallets without joint failure would occur at the same rapid pace as vibration-welded pallets through hot plate welding technology.
5. Hybrid Welding? Why not?
Hot plate welding becomes effective when working with lasers or ultrasonics to apply precise reinforcement on difficult designs. Welding the whole pallet with hot plates for strength allows lasers to apply extra insurance to high-stress corners.
Concluding Thoughts
Hot plate welders have transformed the manufacturing of plastic pallets, delivering unparalleled strength, precision, and durability. By forming seamless joints without the need for adhesives or screws, they offer manufacturers a dependable and efficient solution.
This innovation not only increases product quality but also lowers costs associated with maintenance and production inefficiencies. For industries that demand durable, high-performance pallets, hot plate welding has become a cornerstone of the manufacturing process.
Additionally, the industrial equipment facility of Dizo Global allows companies to view and customize various technological solutions.
FAQs
Why are hot plate welders essential for producing durable and reliable plastic pallets?
Hot plate welders make it easy to create strong, seamless joints without needing adhesives or screws. They're all about boosting durability, reliability and making production more efficient.
What unique innovations do Dizo's hot plate welders offer compared to traditional methods?
Dizo hot plate welders offer precise temperature control and faster cycle times, ensuring stronger, welding joints. With versatile clamping systems, advanced safety features, and energy efficiency, these machines are the ideal choice for plastic pallet manufacturing.
How can manufacturers upgrade their processes with Dizo Global's hot plate welding solutions?
Our welders make manufacturing easier by creating high-quality, seamless joints with minimal waste. At Dizo Global, we provide customized solutions to fit a variety of industrial needs, ensuring they work perfectly with your materials and applications.