Plastic Hose Ultrasonic Sealing and Welding
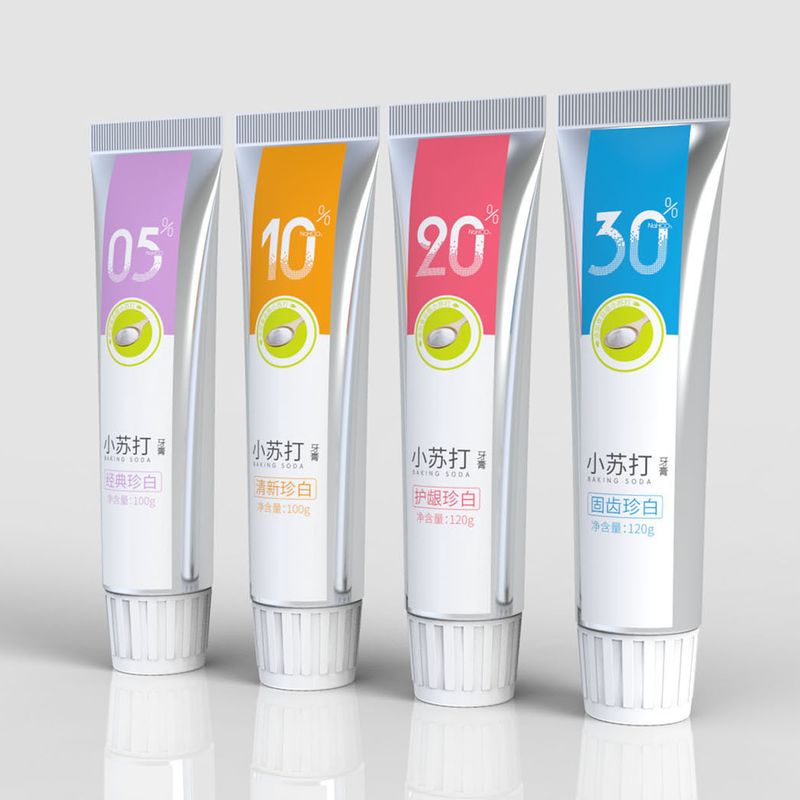
The Ultrasonic Plastic Hose End Sealing Machine utilizes advanced ultrasonic welding technology to effectively seal the ends of plastic hoses.
This machine is designed to handle a wide range of thermoplastic materials, ensuring high-quality, airtight, and watertight seals. It is particularly suited for industries such as pharmaceuticals, daily chemicals, food, and specialized sectors that require precise and reliable plastic hose sealing solutions.
Working Principle of the Ultrasonic Plastic Hose End Sealing Machine
The Ultrasonic Plastic Hose End Sealing Welding Machine operates through the following process:
Ultrasonic Signal Generation:
An ultrasonic generator produces a high-voltage, high-frequency electrical signal at 20KHz.
This signal is converted into mechanical kinetic energy by an ultrasonic converter.
Vibration Transmission:
The ultrasonic end sealing mold applies the vibration energy to the end of the plastic hose.
The friction generated between the surface and internal molecules of the hose creates heat.
Melting and Fusion:
As the temperature at the interface rises to the melting point of the hose material, the hose interface quickly melts.
The molten plastic fills the gaps between the interfaces.
Solidification:
Once the vibrations cease, the hose solidifies under consistent pressure, forming a strong, durable bond.
The welded joint achieves high standards of airtightness and watertightness.
Additionally, the sealing molds can be customized with patterns or logos, enhancing both the aesthetic appeal and functionality of the hose ends to meet commercial branding requirements.
Features of the Ultrasonic Plastic Hose End Sealing Machine
Complete Set of Original Pneumatic Components:
Equipped with genuine, high-quality pneumatic parts to ensure reliability and longevity.
Automatic Discharge Within 4 Seconds After Power Off:
Enhances safety by automatically discharging to over-voltage (OV) levels shortly after shutdown.
No Need for Welding Head Resonance Frequency Adjustment:
Maintains a stable resonance frequency without manual adjustments, simplifying operations.
Seamless Output Adjustment:
Features continuous, step-free output adjustment for precise control over welding parameters.
Clear Frequency Display:
Includes a frequency counter display for easy monitoring of the operating frequency.
Multiple Protections for Ultra-Fast Speed and Phase Current with Mold Abnormality Alarms:
Incorporates various protective mechanisms to safeguard against speed fluctuations, phase current issues, and mold abnormalities, ensuring safe and efficient operation.
Slow Charging and Automatic Frequency Calibration on Startup:
Gradually charges upon startup and automatically calibrates the frequency, delivering rapid power to complete the welding process swiftly and reducing the risk of product damage.
Customizable Sealing Molds:
Molds can be designed with specific patterns or logos to enhance the appearance and functionality of the sealed hose ends, catering to diverse commercial needs.
Working Principle of the Plastic Hot Plate Machine
Note: If the Plastic Hot Plate Machine is part of the same system or context, include it here. Otherwise, remove this section to maintain focus solely on the Ultrasonic Plastic Hose End Sealing Machine.
Applications of the Ultrasonic Plastic Hose End Sealing Machine
The Ultrasonic Plastic Hose End Sealing Machine is versatile and can be applied across various industries by simply changing molds. Key application areas include:
Pharmaceutical Industry:
Toothpaste tubes
Ointments
Medications
Daily Chemical Industry:
Cosmetics
Hair lotions
Food Industry:
Food containers
Jams
Industrial Products:
Ink
Paint
Glue
Specialized Sectors:
Composite tube packaging
This machine is particularly effective for sealing ends of PE (Polyethylene), PVC (Polyvinyl Chloride), and PP (Polypropylene) plastic hoses, ensuring excellent sealing quality suitable for high-demand applications.
Summary
The Ultrasonic Plastic Hose End Sealing Machine offers a robust and efficient solution for sealing the ends of plastic hoses and composite tubes. Key features such as original pneumatic components, automatic discharge, seamless output control, clear frequency display, multiple protective measures, and automatic frequency calibration ensure high-quality welds while minimizing the risk of damage to delicate products.
These attributes make it an indispensable tool for industries requiring precise and reliable ultrasonic welding for small-scale, high-precision applications.
With its user-friendly design, high production capacity, and flexible customization options, this welding machine is essential for optimizing manufacturing processes across multiple industries, including pharmaceuticals, daily chemicals, food, cosmetics, and more.
By leveraging advanced ultrasonic welding technology, Dizo ensures superior performance and reliability, meeting the stringent demands of modern manufacturing environments.