Ultrasonic Welding for New Energy Components
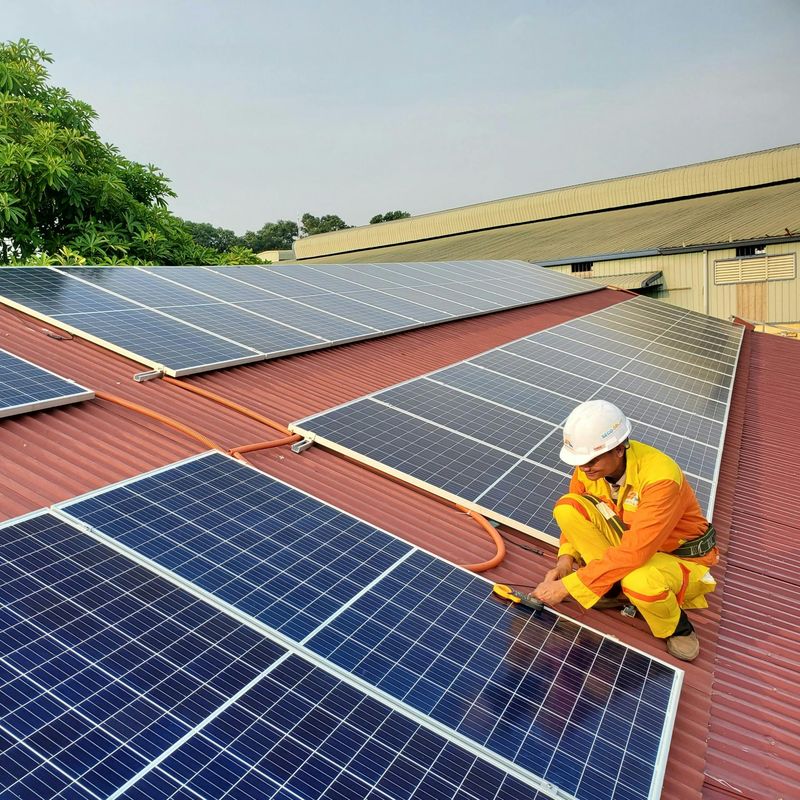
The global demand for sustainable energy solutions has reached unprecedented levels. As climate change concerns intensify and fossil fuel resources dwindle, the renewable energy industry has emerged as a cornerstone of global environmental initiatives. Solar, wind, and hydrogen power technologies have transformed from alternative options into essential components of our energy infrastructure.
At the core of this transformation lies plastic welding technology—an innovative manufacturing process quietly revolutionizing renewable energy component production.
The renewable energy sector is flourishing on all fronts. Solar installations now extend from rooftops to vast solar farms, while wind turbines increasingly populate both land and sea horizons. Hydrogen-powered vehicles are steadily gaining market share in traditional transportation. This remarkable expansion demands manufacturing techniques that are reliable, cost-effective, and scalable.
Plastic welding has emerged as the ideal solution, offering a sophisticated method for joining polymer components without traditional adhesives or mechanical fasteners. This innovation both streamlines manufacturing and enhances product performance.
How does plastic welding technology strengthen different segments of the renewable energy industry for renewable energy manufacturers? Let's examine this technological breakthrough in detail.
Table of Contents
Industry Pain Points and Welding Technology
Plastic Welding in Solar Module Manufacturing and Recycling
Plastic Welding in Wind Turbine Production
Plastic Welding in the Manufacturing of Batteries and Fuel Cells
Advantages of Plastic Welding in the New Energy Industry
Types of Plastic Welding Techniques Used in the New Energy Industry
The Role of Ultrasonic Plastic Welding in Sustainable Manufacturing
New Energy Plastic Parts Custom Welding Solutions from Dizo
Performance Degradation of Photovoltaic Backsheets
Visual Optimization Proposals
Future Outlook of Plastic Welding in Renewable Energy
FAQs
Final Thoughts
Industry Pain Points and Welding Technology
Application Scenarios | Defects of Traditional Solutions | Welding Solutions |
---|---|---|
Solar Junction Boxes | Aging of adhesives leads to electric leakage and potential safety hazards | Ultrasonic welding achieves molecular-level fusion for permanent, weather-resistant bonds |
Fuel Cell Bipolar Plates | Metal gaskets increase weight and compromise efficiency | Laser welding of engineering plastics reduces weight by 40% while maintaining structural integrity |
Plastic Welding in Solar Module Manufacturing and Recycling
The Problem with Traditional Adhesive-Based Joining
Solar junction boxes are vital components in solar panel systems, connecting individual solar cells and protecting electrical connections from environmental factors. While traditional adhesive-based joining methods have been widely used, their limitations have become increasingly apparent through field experience.
For solar energy storage companies, these components face severe environmental challenges in solar module manufacturing. Solar panels endure extreme temperature fluctuations, persistent humidity, and intense UV radiation. These environmental stressors gradually compromise adhesive integrity, triggering performance issues.
As adhesives deteriorate, their ability to seal critical electrical connections diminishes significantly. The consequences are serious: electric leakage creates safety hazards while reducing operational efficiency and system lifespan. This affects the return on investment for solar farms and poses risks to maintenance personnel.
Ultrasonic Welding: A Superior Alternative
Ultrasonic welding technology has transformed solar module manufacturing. This sophisticated ultrasonic welding new energy components process works like molecular choreography: precisely controlled vibrations at 20,000 Hz interact with polypropylene's (PP) semi-crystalline structure.
The material's amorphous regions, having lower melting points, selectively absorb this vibrational energy and undergo controlled melting. This precise thermal transformation allows polymer chains from both surfaces to intermingle, creating a molecular-level fusion bond.
For solar pv manufacturers, this advanced manufacturing process yields remarkable results. It creates exceptionally durable bonds that withstand all environmental challenges. Whether facing intense summer heat or prolonged monsoon exposure, ultrasonic-welded solar junction boxes maintain their structural and functional integrity.
This outstanding durability ensures reliable performance in solar module manufacturing, keeping solar panels at optimal electricity generation efficiency throughout their extended lifespan. Consequently, solar farms operate more efficiently, with reduced maintenance costs and increased productivity.
Plastic Welding in Wind Turbine Production
Plastic welding is particularly important in wind turbine production, especially when bonding new energy plastic components like the blades, which combine fiberglass and thermoplastic polymers.
Hot gas welding and vibration welding techniques help create strong joints while maintaining the flexibility and weight of the materials, which is crucial for wind turbine performance.
For wind turbine suppliers, the advantages of plastic welding in wind turbines include:
- Durability: Seals created through welding protect components from weather elements like rain, UV exposure, and temperature fluctuations.
- Cost-Effectiveness: Plastic welding eliminates the need for mechanical fasteners and adhesives, saving both material and labor costs.
- Design Flexibility: It allows renewable energy storage companies to create custom parts for turbines with specific aerodynamic and structural requirements.
A common misconception in wind turbine manufacturing is that maximizing weld strength always leads to better performance. However, this oversimplified approach can significantly affect blade aerodynamics in unexpected ways.
Wind turbine blades require carefully engineered aerodynamic profiles to optimize wind energy capture efficiency. The presence of overly strong or irregularly distributed welds can disrupt these carefully designed smooth surfaces, creating unwanted turbulence patterns.
These patterns not only increase aerodynamic drag but also substantially reduce overall turbine efficiency. To address this, renewable energy manufacturing companies need to find a delicate balance between structural integrity and aerodynamic performance. They can use sophisticated welding techniques that achieve optimal strength while preserving the blade's critical aerodynamic properties.
For instance, some renewable energy manufacturers now use computational fluid dynamics (CFD) simulations to predict the impact of different welding patterns on aerodynamics and adjust their welding processes accordingly.
Plastic Welding in the Manufacturing of Batteries and Fuel Cells
The Weight Problem with Traditional Designs
Fuel cells represent a groundbreaking technology in renewable energy, particularly in hydrogen-powered vehicles. Their bipolar plates serve essential functions: distributing reactant gases (hydrogen and oxygen) to the electrodes while collecting and channeling the electrical current generated during the electrochemical reaction.
However, traditional designs face a significant challenge due to their reliance on metal gaskets for sealing. While metal gaskets provide reliable sealing, they add considerable weight to hydrogen-powered vehicles.
In vehicle performance, every gram matters. Greater mass requires more energy for movement, directly affecting overall efficiency. The combined weight of metal gaskets throughout the fuel cell stack compromises the vehicle's performance and range, limiting practicality and increasing operational costs.
Laser Welding of Engineering Plastics: The Solution
Laser welding of engineering plastics offers an elegant solution to this challenge in fuel cells production. This state-of-the-art process uses precisely controlled laser beams to achieve molecular-level fusion of specialized plastic materials in bipolar plates, creating hermetically sealed joints without metal gaskets.
The advantages in batteries production are remarkable. Advanced plastic materials combined with laser welding achieve a 40% reduction in bipolar plate weight compared to traditional designs.
This significant decrease in mass enhances energy efficiency for hydrogen-powered vehicles, improving performance while contributing to environmental sustainability in renewable energy semiconductor manufacturing. As a result, these vehicles can travel longer distances per hydrogen tank, increasing their market competitiveness.
Advantages of Plastic Welding in the New Energy Industry
From solar panels to wind turbines and energy storage systems, the applications of ultrasonic welding new energy plastic parts are vast and diverse. In this section, we will explore the key advantages that plastic welding brings to the new energy sector.
1. Durability and Strength
Plastic welding ensures robust, long-lasting joints that are crucial for components exposed to harsh conditions, such as UV radiation, temperature fluctuations, and weathering. Ultrasonic welding for new energy plastic parts is ideal for applications like solar modules and wind turbine production, where long-term performance is important.
The airtight seals created during welding processes protect against water ingress, contamination, and material degradation, ensuring the longevity of new energy components.
2. Energy Efficiency
The precision of plastic welding helps reduce energy loss by creating airtight seals in components like batteries and fuel cells, improving overall system efficiency. Well-welded solar module components capture more sunlight, and battery enclosures minimize energy loss during storage.
Additionally, ultrasonic welding for new energy plastic parts is highly energy-efficient for renewable energy manufacturers, as it requires minimal energy compared to traditional joining methods, reducing manufacturing costs and environmental impact.
Cost Reduction in Lithium-Ion Battery Packs
According to BloombergNEF's analysis, plastic welding technology has transformed lithium-ion battery pack manufacturing costs. By eliminating conventional joining materials like adhesives and mechanical fasteners, manufacturers save an average of $17 per kilowatt-hour.
The benefits extend beyond material costs. Plastic welding streamlines production, reducing assembly time and labor requirements. This combination of cost savings and enhanced efficiency makes plastic welding attractive for battery manufacturers.
Tesla's battery engineers have praised plastic welding in their production, noting its role in reducing costs while maintaining high standards.
Dizo's Customized Solution for a Photovoltaic Enterprise
Dizo, a pioneer in plastic welding technology, demonstrates its transformative potential through customized solutions. In one case study, Dizo implemented a tailored welding solution for a photovoltaic enterprise, achieving a 25% improvement in component encapsulation efficiency.
This enhancement improved component protection, extended operational lifespan and boosted performance. The solution also reduced wind turbine production and solar module manufacturing costs while strengthening the renewable energy storage companies's market position.
Through such customized approaches, Dizo helps renewable energy manufacturing companies maintain their competitive edge.
Sustainable Closed-Loop
Traditional Recycling Process (Fragmentation and Sorting)
The conventional approach to recycling photovoltaic panels involves multiple steps. It starts with collecting end-of-life panels, followed by mechanical fragmentation. The sorting process uses magnetic separation for metallic components and density-based methods for plastics and glass.
However, due to modern photovoltaic panels' complex composition, this traditional approach achieves only a 58% material recovery rate, losing significant valuable materials to waste.
Plastic-Welding-Based Recycling Process (Hot-Plate Welding Separation Method)
The innovative plastic-welding-based recycling process marks a significant advance in material recovery. This approach uses hot-plate welding technology in reverse, enabling precise component separation while maintaining material integrity.
After separation and sorting, the system achieves an 82% material recovery rate. This improvement minimizes waste while promoting circular economy principles in renewable energy manufacturing.
5. Design Flexibility
Plastic welding enables wind turbine suppliers and solar pv manufacturers to create custom-designed parts, including complex shapes and sizes, for advanced energy systems. The flexibility of welding new energy plastic parts makes it possible to optimize the performance of components like wind turbine blades and solar panels.
This versatility allows engineers to push the boundaries of design and functionality in renewable energy systems.
6. Faster Production Times
The efficiency of plastic welding technologies, such as ultrasonic welding for new energy plastic parts, leads to significantly faster fuel cells production and wind turbine production rates.
New energy plastic parts welders can produce high-quality, reliable ultrasonic welding new energy plastic parts in a fraction of the time required for manual fastening or adhesive application. This speed supports the scaling up of renewable energy manufacturing processes to meet the increasing demand for clean energy technologies. <See how to use plastic welders>
7. Improved Safety
Strong, durable plastic welding new energy plastic parts ensure the safety of components in renewable energy systems. Welding new energy plastic parts like battery cases and fuel cells creates reliable, airtight seals that prevent leaks, contamination, and short circuits, reducing the risk of system failures.
In summary, plastic welding, particularly ultrasonic welding for new energy plastic parts, offers a range of advantages that make it a perfect fit for the new energy industry. Whether it's in solar panel manufacturing, wind turbine production, battery production, or fuel cells, plastic welding plays an indispensable role in the future of clean energy technologies.
Types of Plastic Welding Techniques Used in the New Energy Industry
There are several types of plastic welding techniques, each with its own advantages and specific applications. Below, we explore some of the most commonly used methods of plastic welding in the renewable energy sector.
1. Ultrasonic Welding
Ultrasonic welding is one of the most widely used plastic welding techniques in the new energy industry. This method uses high-frequency sound waves to generate heat, which melts the plastic and creates a strong bond between two parts. The process is quick and precise, making it ideal for high-volume manufacturing.
Applications in New Energy:
- Solar Panel Assembly: Used to weld components like frame structures and junction boxes without damaging delicate parts.
- Battery Manufacturing: Perfect for welding battery enclosures and connectors, ensuring airtight seals.
- Fuel Cells: Helps create strong, leak-proof seals in fuel cell assemblies.
2. Vibration Welding
Vibration welding uses high-frequency mechanical vibrations to heat and melt the plastic parts, allowing them to be fused together. The vibration creates friction between the surfaces, causing localized heating that leads to a bond. This technique is highly efficient for welding larger plastic parts.
Applications in New Energy:
- Wind Turbines: Commonly used in the production of rotor blades and housing components that require strong and durable joints.
- Battery Pack Assemblies: Ensures tight, secure connections in energy storage systems.
3. Hot Plate Welding
Hot plate welding involves heating a metal plate to a high temperature and using it to melt the surfaces of the plastic parts that need to be joined. Once the surfaces are molten, the parts are pressed together to form a solid bond. This method is effective for joining large, thick plastic parts.
Applications in New Energy:
- Wind Turbine Components: Useful for welding large plastic components like enclosures and support structures.
- Solar Module Manufacturing: Used for welding large plastic frames or covers.
- Battery Cases: Ideal for creating strong, sealed battery enclosures to protect sensitive components.
4. High-Frequency Welding
High-frequency welding, also known as radio frequency (RF) welding, utilizes high-frequency electromagnetic waves to generate heat and melt the plastic. This method is particularly effective for joining thermoplastic materials with high dielectric properties.
Applications in New Energy:
- Solar Panel Components: Often used in welding backsheet materials and protective covers in solar modules.
- Fuel Cells: Commonly employed for creating airtight seals in fuel cell systems.
5. Laser Welding
Laser welding uses a focused beam of light to generate heat at the point of contact between two plastic surfaces, melting the material and fusing the parts together. This technique provides a high degree of precision and is often used when aesthetics and clean seams are required.
Applications in New Energy:
- Battery Manufacturing: Ideal for creating precise and hermetic seals in battery systems and electrical connectors.
- Fuel Cells: Used to weld components like bipolar plates and membrane electrode assemblies (MEAs) with high precision.
6. Hot Gas Welding
Hot gas welding involves using heated air or gas to melt the plastic at the point of welding. This method is particularly suitable for welding thermoplastic materials that require careful control of temperature and flow.
Applications in New Energy:
- Wind Turbines: Used for welding plastic-based parts like nacelle covers and mounting brackets.
- Solar Panel Backsheets: Ensures strong, durable seals without affecting the integrity of sensitive components.
Each plastic welding technique has its own set of advantages and is suited for specific applications within the new energy industry. By choosing the appropriate technique for each application, manufacturers can improve production efficiency, reduce costs, and contribute to the continued development of sustainable energy solutions.
The Role of Ultrasonic Plastic Welding in Sustainable Manufacturing
Ultrasonic plastic welding has become a game-changer in sustainable renewable energy semiconductor manufacturing, particularly in the new energy industry. This high-tech method uses ultrasonic sound waves to generate heat and join plastic materials without the need for additional adhesives or fasteners.
Why Ultrasonic Welding is Sustainable
Ultrasonic welding is known for its minimal environmental impact, making it a top choice in the renewable energy sector. Here's why:
1. No Need for Consumables: Unlike other welding methods that require adhesives, soldering materials, or fillers, ultrasonic welding doesn't rely on additional consumables.
2. Energy Efficiency: The process is highly energy-efficient, consuming less power compared to traditional welding techniques like hot plate or vibration welding. The fast, localized heating minimizes energy consumption, making it ideal for renewable energy manufacturing.
3. Reduced Material Waste: Ultrasonic welding new energy plastic parts produces a small amount of heat, which helps prevent the surrounding materials from being damaged. This precision reduces the amount of scrap material produced and minimizes waste.
4. No Toxic Emissions: Since ultrasonic welding new energy plastic parts doesn't require the use of toxic chemicals or solvents, it produces fewer harmful emissions, contributing to cleaner air and safer working conditions.
New Energy Plastic Parts Custom Welding Solutions from Dizo
Dizo offers advanced ultrasonic welding solutions for new energy plastic parts, catering to industries like solar, wind, battery, and fuel cell production. With a focus on solar module manufacturing,
Dizo new energy plastic parts welders ensure precise, durable welds for components such as junction boxes and backsheet films, improving performance and minimizing environmental impact.
For wind turbine production, Dizo's hot plate and vibration welding techniques provide strong, weather-resistant joints for parts like rotor blades and nacelle covers, reducing maintenance costs.
In batteries production and fuel cells production, Dizo's ultrasonic welding guarantees leak-proof seals and structural integrity, optimizing safety and efficiency.
By offering custom solutions for new energy plastic components welding machines, Dizo supports sustainable, cost-effective manufacturing in the renewable energy sector, making it a trusted partner for solar energy storage companies looking to create high-performance, eco-friendly products.
Performance Degradation of Photovoltaic Backsheets
In a comprehensive study by Fraunhofer ISE, researchers subjected both welded and adhesively bonded photovoltaic backsheets to rigorous testing conditions at 85% relative humidity. The investigation revealed significant vulnerabilities in adhesively bonded back sheets.
Their hygroscopic adhesive materials showed a strong tendency to absorb atmospheric moisture, resulting in a progressive weakening of the crucial bonds between back sheet layers. This degradation manifests in multiple failure modes: compromised electrical insulation, elevated water vapor transmission rates, and ultimately, accelerated performance deterioration.
In contrast, welded back sheets, with their sophisticated molecular-level fusion joints, showed remarkable resistance to moisture exposure. These advanced components maintained excellent structural integrity throughout the testing period, with minimal increases in water vapor transmission rates.
Their electrical insulation properties also remained consistently within specified operational parameters for much longer. This comprehensive data analysis provides strong evidence for the superior performance of plastic-welded back sheets in high-humidity environments, particularly highlighting their enhanced durability and sustained functionality under challenging atmospheric conditions.
Visual Optimization Proposals
3D Animated Visualization of Fuel Cell Stack Welding Process
A sophisticated 3D animated infographic would offer an unprecedented view of the intricate fuel cell stack welding process. Starting with a detailed static representation of individual fuel cell components, the animation would methodically highlight their precise geometrical specifications, dimensional characteristics, and material compositions, giving viewers a comprehensive understanding of each critical element.
As the animation progresses, it would show the highly precise component alignment procedures necessary for optimal welding results.
The welding process visualization would include detailed slow-motion sequences, with innovative 3D cutaway perspectives that reveal the complex molecular-level interactions during the procedure. In the case of laser welding applications, the animation would illustrate the precisely controlled laser beam as it systematically melts the plastic surfaces.
Viewers would observe the intricate process of polymer chain entanglement and fusion, leading to the formation of extremely strong molecular bonds. Strategic color-coding schemes would be used to distinguish various materials and different welding stages, making this sophisticated process accessible and understandable to a wide range of audiences, from industry experts to engineering students.
Comparative Infographic of Installation Durations and Lifecycle Costs
A comprehensive timeline-based infographic would provide a detailed comparative analysis of installation durations and lifecycle cost metrics for adhesive, bolt-based, and welding methods. The horizontal axis of the timeline would cover the entire operational lifespan of components, from initial installation to end-of-life considerations.
In the installation time analysis section, precisely scaled bars would show the comparative duration requirements for each joining method. Traditional adhesive-based approaches usually require long initial setup times due to specific curing and drying requirements.
In contrast, welding methods are more efficient as they eliminate these waiting periods. Bolt-based solutions require significant time for precise alignment and systematic tightening procedures.
For a comprehensive lifecycle cost analysis, an integrated line graph would be overlaid on the timeline, tracking detailed metrics such as material costs, maintenance requirements, and replacement costs. Adhesive-based solutions typically have lower initial material costs but higher maintenance costs due to potential bond failure.
Bolt-based systems have moderate to high initial investments and intermediate maintenance requirements. Welding systems, although requiring a significant upfront equipment investment, offer better long-term cost efficiency due to their exceptional durability and minimal maintenance needs.
Carefully selected color schemes would ensure that these complex cost relationships are easy to understand at a glance.
Radar Chart for Comparing Welding/Adhesive/Bolt Solutions
A radar chart can be used to compare the strength, cost, and durability of welding, adhesive, and bolt solutions. The chart would have axes representing each of these key dimensions. Welding solutions might show high scores in strength and durability, with a medium score in cost (due to the initial equipment investment).
Adhesive solutions could have a low score in durability, a medium score in cost (initially), and a relatively low score in strength. Bolt-based solutions might have a medium score in strength, a medium-high score in cost, and a medium score in durability. This visual representation would quickly show the relative advantages and disadvantages of each method.
Heatmap of Efficiency Improvements by Geographic Region
A heatmap can display the efficiency improvements achieved by using plastic welding technology in different geographic regions. Regions with higher solar radiation or stronger wind resources might show more significant efficiency improvements. For example, sunny regions like the deserts of the southwestern United States or the Sahara Desert in Africa could have a high efficiency improvement rate when using plastic-welded solar panels.
Coastal regions with strong wind resources, such as the coast of Norway or the Great Lakes region in North America, could show substantial efficiency gains in wind turbine applications. The heatmap would use colors to represent the degree of efficiency improvement, making it easy to see where the technology has the most significant impact.
Plastic welding technology has become an essential part of the renewable energy sector, providing solutions that combine exceptional durability with outstanding operational efficiency in various applications, including solar panels, wind turbines, batteries, and fuel cells. Modern welding techniques, such as ultrasonic, vibration, hot plate, and laser methods, offer unprecedented levels of precision, durability, and energy efficiency, far surpassing traditional joining approaches.
Industry leaders like Dizo, through their innovative customized solutions and new energy plastic parts welder, are fundamentally changing the sustainability landscape of the renewable energy sector while reducing environmental impact. As renewable energy technologies continue to evolve rapidly, plastic welding remains a critical enabler for optimizing the performance and operational longevity of these sophisticated systems.
To quantify the potential impact of advanced welding technologies on clean energy production in your specific geographic location, we invite you to explore our comprehensive "Welding Technology Impact Calculator". This sophisticated tool processes local solar radiation or wind energy data to generate detailed projections of enhanced clean energy output achievable through the implementation of advanced welding techniques.
This analytical tool not only shows the transformative potential of plastic welding in renewable energy applications but also provides practical insights into its benefits in your specific operational context.
We strongly encourage the dissemination of this valuable technical information across professional networks and social media platforms. By increasing awareness of the transformative applications of plastic welding in renewable energy systems, we can all contribute to the adoption of sustainable technologies.
Let's work together to promote these innovative technological solutions and create a more sustainable and environmentally conscious future.
Future Outlook of Plastic Welding in Renewable Energy
As the renewable energy industry advances toward a more sustainable future, plastic welding technology will play an increasingly pivotal role. The continuous drive for cost-effectiveness, improved performance, and enhanced durability in renewable energy systems will further fuel the demand for advanced plastic welding techniques.
Technological Advancements on the Horizon
Nanocomposite Welding: Scientists are exploring nanocomposite materials in plastic welding for renewable energy applications. These materials, containing nanoparticles dispersed within a polymer matrix, offer increased strength, improved thermal stability, and enhanced chemical resistance.
For solar module manufacturing, welding nanocomposite-based components could create panels that better resist environmental degradation, extending their lifespan. The welding process requires specialized techniques to ensure the proper integration of nanoparticles and polymer matrix at the molecular level.
Automated and Smart Welding Systems: The future promises widespread adoption of automated and smart welding systems in renewable energy manufacturing. These systems use sensors to monitor and adjust welding processes in real time.
In wind turbine blade manufacturing, automated welding robots can detect material irregularities and variations in plastic layer thickness. The system automatically adjusts welding speed, temperature, and pressure to ensure consistent, high-quality welds—improving manufacturing efficiency while reducing manual errors.
Multi-Material Welding: Renewable energy components often combine multiple materials. Future plastic welding technology will develop methods to seamlessly join different types of plastics and bond plastics to metals or ceramics.
In hydrogen fuel cells, for instance, plastic bipolar plates must bond with metal current collectors. New welding techniques will create strong, hermetic bonds between these dissimilar materials, ensuring efficient fuel cell operation.
New Frontiers in Renewable Energy Applications
Geothermal Energy Systems: Geothermal energy harnesses heat from Earth's interior. Plastic welding enables the manufacturing of geothermal pipes and heat exchangers that must withstand high temperatures and corrosive environments.
Welded high-performance plastics create lightweight, corrosion-resistant components with excellent thermal insulation properties, improving system efficiency and reducing maintenance costs.
Wave Energy Converters: The ocean offers vast renewable energy potential through wave energy converters. Plastic welding creates buoyant structures and connecting components that withstand harsh marine conditions, including strong waves, saltwater corrosion, and temperature fluctuations.
Global Impact and Industry Collaboration
Increasing Accessibility in Developing Regions: Plastic welding technology makes renewable energy more accessible in developing regions. Cost-effective manufacturing of renewable energy components reduces the overall cost of solar panels, wind turbines, and other systems.
In sub-Saharan Africa, where reliable energy access remains challenging, plastic-welded solar panels offer affordable, sustainable power for off-grid communities.
Collaboration between Academia, Industry, and Research Institutions: Advancing plastic welding in renewable energy requires collaboration across sectors. Academic institutions conduct fundamental research on new materials and techniques, while research institutions develop practical solutions.
Industry partners implement these innovations in large-scale manufacturing. The collaboration between MIT and Vestas in developing advanced wind turbine manufacturing techniques exemplifies such partnerships, leading to new patents in plastic welding for renewable energy applications.
FAQs
What types of plastics can be welded?
Many types of plastics can be welded, depending on the specific welding technique used. Some of the most common plastics that can be welded include Polypropylene (PP), Polyethylene (PE), Polyvinyl Chloride (PVC), Acrylonitrile Butadiene Styrene (ABS), Polycarbonate (PC), Polyamide (PA) and Polyethylene Terephthalate (PET).
Is plastic welding environmentally friendly?
Yes, plastic welding can be environmentally friendly. Unlike traditional adhesive bonding, plastic welding does not rely on chemicals or solvents, which are often harmful to the environment.
Additionally, many plastic welding techniques, such as ultrasonic welding and laser welding, use minimal energy and can be performed without generating excess waste.
What are the main challenges of recycling plastic in solar panels?
Recycling plastic from solar panels can be challenging due to the complex design and materials used in their construction. Some of the main challenges include:
- Separation of Materials
- Contamination
- End-of-Life Management
What are the most common plastic welding techniques used in renewable energy applications?
Some of the most commonly used plastic welding techniques in the renewable energy sector include ultrasonic welding, vibration welding, hot plate welding, and laser welding.
How does plastic welding contribute to energy efficiency in solar modules?
Plastic welding can enhance the energy efficiency of solar modules by ensuring that all components are securely joined without compromising their performance. Some key contributions include strong seals, durability and reduced energy loss.
Final Thoughts
In conclusion, plastic welding technology is vital in the renewable energy sector, providing durable and efficient solutions for components in solar panels, wind turbines, batteries, and fuel cells.
Advanced techniques like ultrasonic, vibration, hot plate, and laser welding offer precision, durability, and energy efficiency. <Learn plastic welding tips>
Custom solutions from industry leaders, such as Dizo, help improve sustainability and reduce environmental impact. As renewable energy technologies advance, ultrasonic welding new energy components remains key in optimizing performance and longevity.
Looking for high-quality ultrasonic welding new energy plastic parts solutions? Contact Dizo for a custom quote and see how our advanced technologies can enhance your energy-efficient products. Let's build a sustainable future together with Dizo new energy plastic components welding machines!