Plastic Welding Solutions for Medical Device Manufacturing
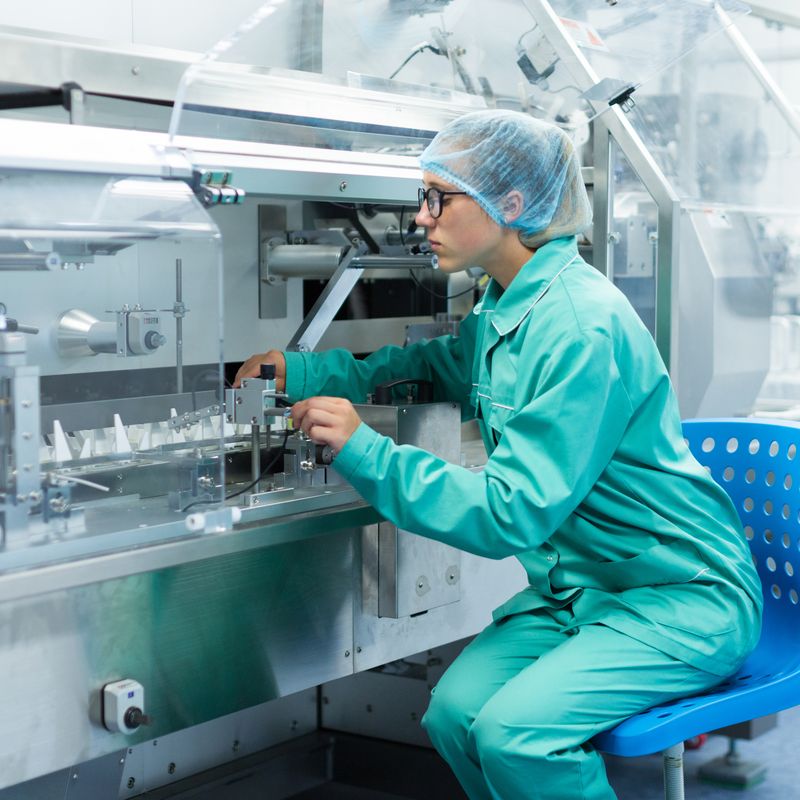
Plastic welding is a process that ensures precision, durability, and safety for critical medical devices. From in-vitro diagnostics (IVD) to surgical instruments and drug delivery systems, plastic welding is pivotal in creating the high-performance components required for medical technology including the manufacturing for medical devices.
In this article, we will explore the different plastic welding technologies for medical device manufacturers, the best materials, the applications, the benefits to the medical device component manufacturers, how to select the right plastic welding solution for medical devices, and the quality control of plastic welding.
Table of Contents
Different Plastic Welding Technologies for Medical Devices Plastic Parts
Which Materials Used in Medical Device is Best for Plastic Welding
Applications of Plastic Welding in Medical Device Manufacturing
Benefits of Plastic Welding for Medical Device Component Manufacturers
Selecting the Right Plastic Welding Solution for Medical Devices
Quality Control in Plastic Welding for Medical Devices
Choosing The Right Ultrasonic Welding Partner - Dizo
FAQs
Conclusion
Different Plastic Welding Technologies for Medical Devices Plastic Parts
When manufacturing for medical devices, selecting the right plastic welding technology is significant for ensuring safety, performance, and longevity. Below, we explore the different plastic welding technologies commonly used in the medical device manufacturing: Ultrasonic Welding, Laser Welding, Gas Tungsten Arc Welding (TIG), and Resistance Welding.
Ultrasonic Welding
Ultrasonic welding uses high-frequency sound waves to melt plastic at the joint interface, creating precise, secure bonds. It's ideal for manufacturing small, intricate parts like surgical tools and diagnostic devices. Advantages include fast cycle times, no need for consumables, and clean, strong joints.
Ultrasonic welding machines provide fast cycle times, eliminate the need for consumables, and create clean, strong joints without additional adhesives or fasteners.
Laser Welding
Laser welding uses focused laser beams to melt and fuse plastic components with high precision. The laser processing for medical device manufacturing is perfect for medical devices that require fine, intricate welds, such as pacemakers or microfluidic systems.
The benefits are minimal heat distortion and excellent control over the welding process, with the use of specialized laser plastic welding equipment in the laser processing for medical device manufacturing.
Gas Tungsten Arc Welding (TIG)
Gas Tungsten Arc Welding (TIG) is a more traditional method, using a tungsten electrode to generate heat for fusing plastics in the medical device manufacturing. Though more common for metals, TIG welding can be applied to certain medical device plastic components, offering strong, durable joints with excellent heat control.
Resistance Welding
Resistance welding generates heat by passing an electrical current through the plastic material. It's best for thicker parts used in medical devices like housings for diagnostic equipment or prosthetics.
This plastic welding method is energy-efficient, cost-effective, and ideal for high-volume production.
Each of these technologies offers specific advantages depending on the plastic welding equipment's requirements, material type, and media device plastic parts production needs. Selecting the right plastic welding solution ensures high-quality, reliable medical devices.
Which Materials Used in Medical Device is Best for Plastic Welding
In medical device manufacturing, choosing the right materials is essential for ensuring performance, safety, and biocompatibility. Several types of plastics are commonly used in medical device plastic welding, each with unique properties suitable for different applications.
1. PET (Polyethylene Terephthalate)
PET is widely used in medical device manufacturing due to its excellent strength, clarity, and chemical resistance. It is commonly used for packaging, diagnostic equipment, and medical containers.
PET is suitable for ultrasonic and laser welding due to its ability to form strong, reliable joints without compromising material integrity.
2. PVC (Polyvinyl Chloride)
PVC is another popular material in medical device manufacturing, particularly for applications requiring flexible and durable components. It is used in items like tubing, catheters, and medical bags.
PVC can be welded through methods like ultrasonic welding and hot plate welding, creating secure seals that prevent contamination and leaks.
3. TPU (Thermoplastic Polyurethane)
TPU is valued for its flexibility, durability, and resistance to wear, making it ideal for medical devices that need to withstand harsh environments. It is commonly used for wearable medical device manufacturing, such as braces and bandages, and for fluid management systems. TPU can be welded using ultrasonic and vibration welding techniques, ensuring tight, strong bonds.
Applications of Plastic Welding in Medical Device Manufacturing
Below are some key applications of plastic welding in the medical device manufacturing:
In-Vitro Diagnostics (IVD)
In-vitro diagnostic devices require high precision and secure assembly to ensure accurate results. Plastic welding technologies like ultrasonic and laser welding are used to assemble parts of diagnostic equipment, including test kits, reagent containers, and sample chambers.
Respiratory
Plastic welding is essential in producing components for respiratory devices, such as ventilators, oxygen masks, and breathing tubes. The welding process ensures airtight seals that prevent leaks and contamination, critical for the safety of patients.
Drug Delivery
Drug delivery systems, such as infusion pumps, inhalers, and transdermal patches, rely on secure plastic welding to join media device plastic components, ensuring that medications are delivered accurately and without leaks. Ultrasonic and laser welding are commonly used in this sector.
Surgical Instruments
Plastic welding is used in manufacturing surgical instruments, such as handles, grips, and lightweight tool bodies. The process creates strong, durable joints that can withstand the sterilization processes without compromising performance.
Wearables & PPE
Medical wearables, including smart devices that monitor health, and personal protective equipment (PPE) like face shields and surgical masks, benefit from plastic welding. This technology ensures the integrity and strength of these lightweight, flexible devices.
Dialysis & Fluid Management Devices
Dialysis and fluid management devices use plastic components that must be securely welded to prevent leaks and contamination. Plastic welding methods like hot plate and ultrasonic welding ensure strong bonds in systems like dialysis machines and intravenous (IV) sets.
Packaging
Packaging for medical devices needs to meet strict standards of hygiene and safety. Plastic welding is also critical in creating tamper-proof seals for sterile packaging, ensuring the safety and integrity of medical devices during transport and storage.
Benefits of Plastic Welding for Medical Device Component Manufacturers
Plastic welding offers a range of crucial benefits for medical device component manufacturers as follows:
Enhanced Durability
Plastic welding ensures strong, seamless bonds between parts, offering superior durability compared to traditional methods like adhesives or screws.
Medical devices, such as drug delivery systems, surgical instruments, and respiratory equipment, must withstand mechanical stress, environmental conditions, and repeated sterilization processes.
Welded joints are resistant to wear, leakage, and deformation, ensuring long-lasting performance even under harsh conditions.
Compliance and Safety
Plastic welding can help medical device manufacturers meet stringent regulatory standards, such as those set by the FDA and ISO. Welded joints provide hermetic sealing, preventing leaks that could compromise device functionality or patient safety.
This is especially important in devices involving fluids, such as dialysis machines and drug delivery systems. Furthermore, welded media device plastic parts are free of adhesives, which can pose contamination risks, ensuring safer, more hygienic products.
Cost Efficiency
Plastic welding eliminates the need for additional materials like adhesives, fasteners, and seals, reducing overall production costs. With reduced material waste and fewer components, medical equipment manufacturers can achieve lower unit costs while maintaining high-quality standards.
Additionally, plastic welding techniques, such as ultrasonic and laser welding, are faster, optimizing media device production times and contributing to cost savings in high-volume manufacturing environments.
Speed and Automation
Plastic welding offers rapid cycle times and the potential for automated processes, increasing production speed and efficiency. With automation in medical device manufacturing, plastic medical device manufacturers can produce large quantities of medical devices with minimal labor, reducing the time-to-market for critical medical products.
This high-speed production is essential for meeting demand in the fast-paced medical sector.
Selecting the Right Plastic Welding Solution for Medical Devices
This section explains how to select the right plastic welding solution in medical device manufacturing.
Material Compatibility
Different plastics used in medical devices—such as PET, PVC, TPU, and polycarbonate—require specific welding techniques for optimal results. Material compatibility is a top consideration, as not all welding methods work equally well with every type of plastic.
For example, ultrasonic welding is ideal for thermoplastics like ABS and PVC, while laser welding is preferred for materials like polycarbonate, providing precise, high-quality welds without excessive heat.
Weld Strength
The strength of the welded joints is a critical factor for the functionality of medical devices. Devices such as infusion pumps or respiratory equipment need strong, durable seals to prevent leaks and ensure the device's long-term reliability.
Techniques like ultrasonic welding provide precise, high-strength bonds for small, delicate components, while hot plate welding or RF welding may be used for larger or more complex parts requiring more robust joins.
Cycle Time
Plastic medical device manufacturers must also consider cycle time, as speed is crucial for high-volume production. Ultrasonic welding machines offer fast cycle times, making it ideal for producing small components in large quantities, such as drug delivery devices or diagnostic tools.
On the other hand, laser welding, while slower, may be more suitable for high-precision applications like surgical instruments, where accuracy is the priority over speed.
By carefully considering material compatibility, weld strength, and cycle time, medical device parts manufacturers can select the most suitable welding method to meet the unique needs of medical device production.
Quality Control in Plastic Welding for Medical Devices
Quality control is important in plastic welding for automation in medical device manufacturing. The following testing methods are used to ensure the integrity and consistency of welds, especially in high-volume production settings.
Methods for Testing Weld Strength
- Pull Tests: These tests measure the force required to separate welded components, assessing the weld's strength. This is critical for ensuring that joints in devices like infusion pumps or fluid management systems can withstand stress.
- Leak Tests: Used to check for air or fluid leaks in welded parts, leak tests are vital for medical devices like respiratory equipment or drug delivery systems that require airtight or watertight seals. The test involves pressurizing or submerging the part to detect leaks, ensuring no defects or gaps compromise the functionality of plastic welded components.
- Optical Inspections: Visual inspection methods, such as high-resolution cameras, are employed to detect surface defects or misalignments in the welds. This is especially useful for transparent medical components like surgical instruments and diagnostic devices that rely on precise and clean plastic welding.
Ensuring Consistency in High-Volume Production
In large-scale production, maintaining consistent weld quality is essential. Medical manufacturing companies use process controls to regulate welding parameters like temperature and pressure, minimizing errors and ensuring consistent results across batches.
Plastic welding suppliers can provide reliable and efficient plastic welding equipment to ensure these parameters are adhered to. Automated systems also monitor these parameters in real-time, ensuring that ultrasonic welding machines and other plastic welding machines provide quality welds with repeatable results throughout the production process.
Automated Solutions for Quality and Repeatability
Automation is a key driver of consistent quality in plastic welding. Robotic arms, AI-driven data analytics, and vision systems are employed to continuously monitor and adjust welding conditions.
These technologies reduce human error and ensure high-quality welds for medical devices, improving both efficiency and repeatability in production. Whether using an ultrasonic plastic welder or other specialized plastic welding equipment, automation ensures that plastic welding is precise, reliable, and cost-effective.
In summary, effective quality control methods—pull tests, leak tests, and optical inspections—ensure the integrity of plastic welds in manufacturing for medical devices. Automation ensures consistency and repeatability, vital for high-quality, compliant, and reliable devices.
Choosing The Right Ultrasonic Welding Partner - Dizo
Working with a trusted provider can ensure reliable and efficient welding solutions. Dizo is a recognized leader in the manufacturing of ultrasonic welding equipment. So, choosing Dizo as your ultrasonic welding partner is a wise decision.
Ultrasonic Welder from Dizo
Dizo's ultrasonic welding systems are engineered for high precision, providing consistent and durable welds on medical-grade plastics. Their ultrasonic plastic welding machines are designed to meet the stringent quality and safety standards required in the medical field, ensuring each weld is strong, clean, and reliable.
The systems are equipped with cutting-edge technology, including advanced control features, to optimize the welding process, ensuring repeatable results in high-volume production environments.
One of the standout features of Dizo's ultrasonic welders is their versatility in handling a wide range of materials used in manufacturing for medical devices. The plastic welding machines are designed to accommodate varying plastic types, making them a go-to solution for medical equipment manufacturers working with different types of medical device plastics, such as PVC, PET, and TPU.
This versatility in ultrasonic plastic welding ensures medical manufacturing companies can achieve the required quality for different plastic materials used in their devices.
Key Components of Ultrasonic Welding Equipment
Dizo's ultrasonic welding systems include several key components that contribute to their efficiency and reliability:
- Transducer: Converts electrical energy into mechanical vibration, initiating the ultrasonic welding process in plastic welding machines.
- Booster: Amplifies the ultrasonic energy and focuses it on the workpiece.
- Horn (Sonotrode): Directs the concentrated ultrasonic energy into the plastic parts being welded, ensuring precise, localized heating.
- Controller: Provides real-time monitoring and control of welding parameters, allowing manufacturers to adjust settings for optimal weld quality.
- Weld Fixture: Holds the parts in place during the welding process to ensure proper alignment and consistency.
Cooperating with Dizo can gain access to cutting-edge technology and expert support to ensure the quality and safety of medical devices through reliable plastic welding solutions.
FAQs
What are the requirements for plastic welding?
Plastic welding requires the correct choice of plastic welding technology, proper material compatibility, and optimal plastic welding machine settings (temperature, pressure, and time). For medical devices manufacturing, compliance with industry standards and regulations is also essential.
What materials can be ultrasonic welded?
Ultrasonic welding is suitable for a wide range of thermoplastic materials, including PVC, PET, TPU, and other medical-grade plastics commonly used in devices such as respiratory equipment, drug delivery systems, and diagnostic tools.
How to determine the plastic type for welding?
The plastic type can be determined by examining the material's properties, including its melting point, molecular structure, and compatibility with ultrasonic energy. It's best to consult with the manufacturer or a plastic welding supplier to ensure compatibility.
How do I know if welding is for me?
If a medical device manufacturing involves the joining of thermoplastic materials and requires high precision, durability, and strong bonds, ultrasonic welding could be a good fit. Consulting with a plastic welding partner can help you evaluate your needs.
What happens to the plastic material during the process of ultrasonic welding?
During ultrasonic welding, high-frequency sound waves create rapid vibrations that generate localized heat at the plastic interface, melting the material and forming a strong bond as it cools.
Conclusion
In conclusion, plastic welding has become an integral part of medical device manufacturing, offering medical device manufacturers the ability to create high-quality, durable, and safe products.
Also there are many challenges for medical device manufacturers. By choosing to collaborate with Dizo, both battery manufacturers for medical devices and disposable medical devices manufacturers can obtain tailored plastic welding solutions designed specifically for medical products.
Dizo's expertise and advanced ultrasonic welding equipment can help enhance the performance and safety of medical devices significantly.