Understanding Linear Vibration Welding: A Complete Overview
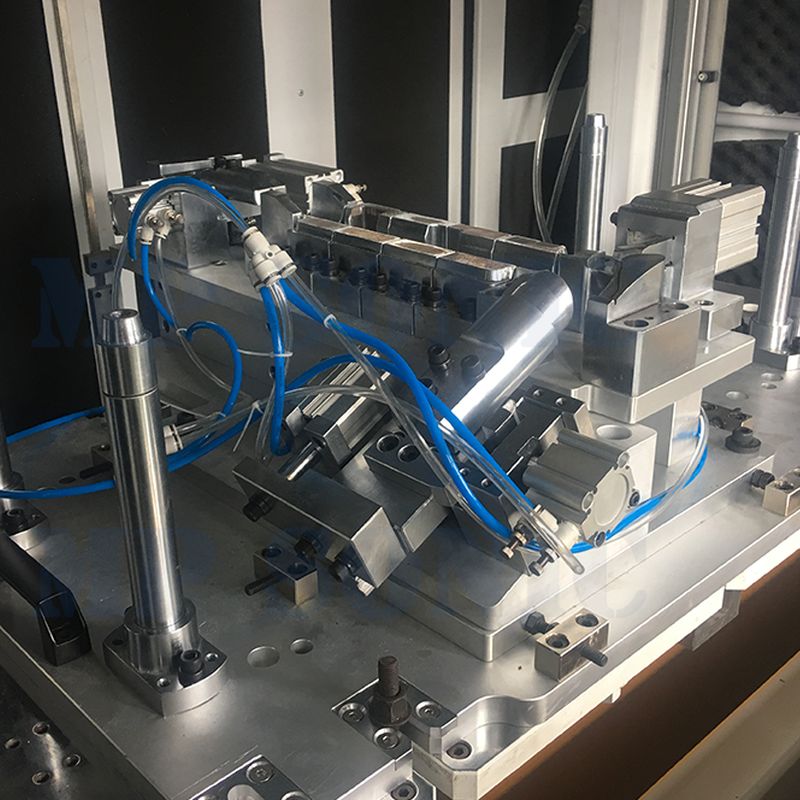
Welcome to our comprehensive guide on Vibration Welding. In this section, we introduce a method that is both innovative and practical for joining plastic parts. We aim to help you learn all about vibration welding and why it is such a valuable process in today's manufacturing world.
Table of Contents
Introduction: What is Vibration Welding
How Does Vibration Welding Work?
Types of Vibration Welding
Vibration Welding Advantages and Limitations
Applications of Vibration Welding
Vibration Welding vs. Ultrasonic Welding
Vibration Welding Design Considerations
Common Challenges and Solutions
Future Trends in Vibration Welding
Conclusion
Introduction: What is Vibration Welding
Vibration welding joins thermoplastic materials by generating heat through friction, eliminating the need for additional adhesives or fasteners.
This welding method is widely used in industries such as automotive and appliance manufacturing for its efficiency, cost-effectiveness, and versatility. It produces strong, durable joints while minimizing waste and environmental impact.
How Does Vibration Welding Work?
Vibration welding is a process that uses controlled vibrations and pressure to join thermoplastic parts.
The Process Step-by-Step
Step 1: Preparation
First, we prepare the parts that need to be welded. We place the pieces into a fixture to hold them securely in the right position.
We also clean the surfaces so they are free from dust or debris. Clean surfaces are crucial because they help create a strong weld.
Step 2: Applying Pressure
Next, we apply pressure to the parts. This pressure is important because it forces the parts into contact with one another.
The tight contact allows the vibration process to create friction. Without enough pressure, the parts would not meet properly, and the weld could be weak.
Step 3: Generating Vibrations
After the parts are in place and pressure is applied, the machine begins to vibrate them. The vibrations occur at high frequency and in a controlled manner.
There are different ways to move the parts, and these motions create friction at the interface of the two surfaces. The friction is key because it generates the heat needed for welding. As the surfaces heat up, they start to melt at the edges.
Technical Details: Frequency and Amplitude
The vibration frequency and amplitude play crucial roles in the welding process. Higher vibration frequencies typically generate heat more quickly, while larger amplitudes can create more intense friction over a larger surface area.
For example, a higher frequency may be suitable for thin or delicate parts, while a larger amplitude is often used for thicker or more robust materials. The combination of these settings determines the amount of heat generated and the uniformity of the weld.
Step 4: Formation of the Weld
Once the friction creates enough heat, the melted material from both parts mixes together. When the machine stops vibrating, the melted material cools down quickly.
The cooling process allows the melted surfaces to fuse, forming a strong bond. We ensure that the cooling phase is well-managed. If cooling happens too fast or too slow, the quality of the weld might be affected.
The Role of Friction and Heat
Friction is the driving force in vibration welding. It turns movement into heat.
Heat softens the surface of the thermoplastic material. This softened surface then bonds together when it cools.
In addition, the machine settings—such as vibration frequency and amplitude—are carefully controlled. These settings are adjusted based on the type of plastic and the specific requirements of the weld. Our modern machines ensure consistency and precision throughout the process.
Why This Process Works
- Efficiency: The process is fast and requires no extra materials like glues or fasteners.
- Strength: The bond created is strong and reliable because the melted surfaces join seamlessly.
- Versatility: Vibration welding can be used on various shapes and sizes, making it a flexible choice for many industries.
Overall, vibration welding is a reliable method used in many manufacturing industries. It allows us to create strong, neat, and efficient joints.
We use each step carefully to ensure that every weld meets high quality standards. This explanation shows the clear steps involved, from preparation to the final cooling phase.
Types of Vibration Welding
Linear Vibration Welding
Linear vibration welding is a process that uses a back-and-forth motion to create friction between two parts. This technique is particularly effective for joining parts with flat or simple geometries.
The linear motion ensures that only the designated area heats up, making it ideal for applications where precision is required. It is widely used in industries that demand consistent weld quality and minimal material waste.
Orbital Vibration Welding
Orbital vibration welding uses a circular or orbital motion to generate friction. This method is especially useful for welding parts with curved or intricate shapes.
The circular motion allows for even heat distribution along the entire welding area, which is crucial for achieving a uniform bond. This technique is preferred when working with complex geometries, as it minimizes the risk of overheating specific areas and ensures a stronger bond.
Both linear and orbital vibration welding methods have distinct benefits. Linear vibration welding is excellent for precise, straight-line joints, while orbital vibration welding is well-suited for curved or complex shapes.
Understanding these differences is essential for selecting the right method for specific manufacturing needs.
Vibration Welding Advantages and Limitations
Vibration welding offers many benefits for manufacturers, but it also has some limitations that we must consider.
Advantages of Vibration Welding
1. Process Advantages
Strong and Durable Welds: One of the biggest advantages of vibration welding is that it creates very strong joints. The process uses friction to generate heat that melts the material surfaces.
When the melted surfaces cool down, they form a bond that is both robust and reliable. This strength makes the welds ideal for parts that must endure stress and movement.
Efficiency in Large Parts Manufacturing: Vibration welding is extremely efficient when working with large parts. Because the process is fast and does not require additional materials such as adhesives or fasteners, it helps reduce production time.
This efficiency is especially beneficial in industries like automotive and appliance manufacturing, where speed and quality are both important.
Precision and Repeatability: The process allows us to focus heat only on the joint area, which minimizes damage to the surrounding material.
Once the machine is set up correctly, vibration welding can produce consistent and repeatable welds. This predictability is key to high production standards.
2. Economic Advantages
Cost-Effectiveness: Another significant benefit is the cost savings. The absence of extra materials, along with lower energy consumption compared to some other welding methods, makes vibration welding a cost-effective choice.
Manufacturers can reduce material costs and lower their energy bills, which contributes to overall savings.
3. Environmental Advantages
Environmentally Friendly Process: We appreciate that vibration welding is environmentally friendly. The process produces very little waste and does not use harmful chemicals.
This clean method is a good fit for companies that are looking to lower their environmental impact while maintaining high-quality production.
Limitations of Vibration Welding
1. Material Compatibility Issues
Despite its many benefits, vibration welding works best with specific thermoplastics. Not all materials are suitable for this process.
Some plastics may not melt uniformly, leading to weak joints. We must carefully select compatible materials to ensure a strong and reliable weld.
2. Design Constraints
The process also has limitations when it comes to design. Vibration welding is most effective for parts with flat or simple geometries.
When working with very complex shapes or curves, the technique may not produce the best results. Designers and engineers need to adjust their designs to meet the requirements of this welding method.
3. Potential for Burr Formation
Sometimes, the welding process can create burrs or extra material along the weld line. These burrs may require additional finishing work, which can add time and cost to the production process.
We need to manage this risk by optimizing machine settings and part design.
4. Equipment Sensitivity and Maintenance
Vibration welding machines are sensitive to factors like vibration frequency and amplitude. Small changes in these settings can affect weld quality.
Skilled operators and regular maintenance are essential to keep the process running smoothly and to avoid unexpected issues.
Applications of Vibration Welding
Automotive Manufacturing
In the automotive industry, vibration welding speeds up automotive production. For example, it reduces cycle time by 30% compared to traditional methods. This efficiency lowers production costs.
Manufacturers also save on material costs by eliminating adhesives and fasteners. Strong welds ensure parts like dashboards and door panels can withstand daily use, improving product durability.
Appliance Manufacturing
In appliance manufacturing, vibration welding improves joint strength by 25%.
This reduces the risk of leaks and failures in products like refrigerators and washing machines. The clean, waste-free process also helps companies meet sustainability goals.
Electronics and Consumer Goods
For electronics, vibration welding is precise and reliable. It achieves a 99% defect-free production rate for small, delicate components.
This reduces waste and rework, saving costs while meeting high-volume demands.
Medical Devices
In the medical device industry, vibration welding creates strong, sterile joints. It reduces the risk of device failure by 40%, enhancing patient safety.
The process aligns with strict hygiene standards, ensuring products meet regulatory requirements.
Packaging Industry
In packaging, vibration welding creates secure, tamper-evident seals. It achieves a 100% consistency rate, protecting the integrity of packaged products.
The process's speed increases production throughput by 20%, meeting higher demand efficiently.
Vibration Welding vs. Ultrasonic Welding
In this section, we compare two popular welding methods: vibration welding and ultrasonic welding. Both techniques join plastic parts, but they work in different ways.
Frequency and Amplitude
Vibration Welding:
- Frequency: This method uses lower frequencies. It means the parts move back and forth at a slower pace compared to ultrasonic welding.
- Amplitude: Vibration welding uses higher amplitude, which means the movement is larger and helps create more friction over a larger area.
Ultrasonic Welding:
- Frequency: Ultrasonic welding uses very high frequencies, often above 20,000 vibrations per second (20 kHz). This high speed creates quick, intense bursts of energy.
- Amplitude: The amplitude in ultrasonic welding is very low, meaning the parts move only a little bit. This small movement is enough to create heat without damaging delicate components.
Key Takeaway: The difference in frequency and amplitude means that vibration welding is great for larger parts where more energy is needed, while ultrasonic welding works best for smaller, more precise parts.
Suitable Applications
Vibration Welding
- Large Components: We use this method for larger parts found in automotive and appliance manufacturing.
- Heavy-Duty Bonds: It is ideal when strong, durable joints are required, especially where the parts must bear heavy loads.
- Simple Geometries: It works best with flat or simple shapes.
Ultrasonic Welding
- Small and Delicate Parts: This method is perfect for tiny components in electronics, medical devices, or packaging.
- Precision: It is used where a quick, precise weld is needed without generating too much heat that might harm sensitive parts.
- Complex Designs: Ultrasonic welding can be adapted for intricate designs where minimal movement is important.
Vibration Welding Design Considerations
When planning a vibration welding project, several key design principles must be considered to ensure successful and high-quality welds.
These principles include joint design, material selection, and part geometry. By referencing the types of vibration welding discussed in Section 3 (Linear and Orbital Vibration Welding), we can better understand how these principles apply in practical scenarios.
Joint Design
Joint design is crucial for effective vibration welding. It ensures that parts are held securely and that the welding process produces a strong bond. Here are some important considerations:
1. Edge Preparation: The surfaces where the two parts meet must be smooth and clean. If the edges are rough or uneven, the friction may not generate enough heat to create a strong weld.
2.Joint Geometry: The shape of the joint should allow for even heat distribution. Simple, flat joints are often ideal because they promote uniform friction, as seen in linear vibration welding. For complex or curved parts, orbital vibration welding may be more suitable due to its ability to distribute heat evenly along the joint.
3. Alignment: Perfect alignment is essential to avoid weak spots. Precise fixtures or jigs can help hold parts in place during welding.
4. Surface Area: Increasing the surface area of the joint can enhance bond strength by generating more friction.
Material Selection
Material selection is equally important, as it can determine the success of the welding process. Key considerations include:
- Thermoplastic Compatibility: Vibration welding works best with thermoplastics that have similar melting points and compatible chemical properties. This ensures a uniform weld, as demonstrated in both linear and orbital welding applications.
- Material Thickness:Thicker materials may require adjustments in machine settings (e.g., vibration frequency and pressure) to ensure proper heat distribution. For example, in linear vibration welding, thicker parts may need higher pressure to generate sufficient friction.
- Heat Sensitivity: Materials must be able to withstand the heat generated during welding without deforming or degrading. This is especially important in orbital welding, where heat is distributed over a larger area.
Part Geometry
The shape and complexity of the components being welded can affect overall weld quality. Considerations include:
- Simple Shapes vs. Complex Shapes: Simple, flat shapes are easier to weld using linear vibration welding due to uniform friction. In contrast, complex or curved parts benefit from orbital vibration welding, which can follow the contour of the part and ensure even heating.
- Edge Thickness: Consistent edge thickness helps achieve a uniform weld by ensuring even heating and cooling.
- Fixture Design:Fixtures must support the part geometry and ensure even pressure application across the weld. This is critical in both linear and orbital welding processes.
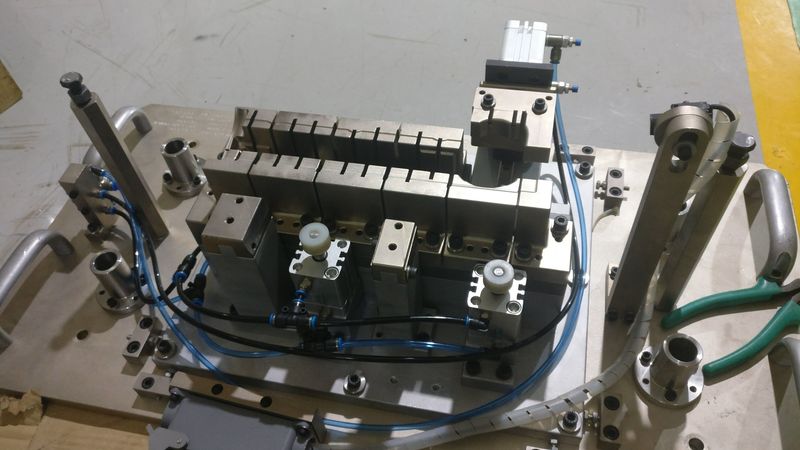
Practical Tips for Better Welding Quality
- Testing and Prototyping: Conduct tests and create prototypes to identify and resolve design issues before final production.
- Adjustable Machine Settings: Use machines with adjustable settings for frequency, amplitude, and pressure to tailor the process to different materials and geometries.
- Collaboration with Engineers: Designers, engineers, and technicians should collaborate to optimize all design factors, from joint design to material selection, ensuring the best possible welding outcomes.
Common Challenges and Solutions
In this section, we focus on the common challenges that arise during vibration welding and offer practical solutions. By addressing these issues clearly, we can improve our welding process and achieve high-quality, consistent results.
Common Challenges
Burr Formation
One of the most frequent issues is burr formation. Burrs are small, unwanted pieces of extra material that stick out along the weld line.
They occur when the heat is not evenly distributed or when the movement of the parts is not perfectly controlled. Burrs can weaken the overall joint and may require additional finishing work if left unaddressed.
Misalignment of Parts
Another challenge is the misalignment of the parts before welding. If the parts do not align perfectly, the pressure applied may be uneven, resulting in weak spots in the weld and inconsistent bonding.
Ensuring that the parts fit together correctly is essential for a strong, durable joint.
Inconsistent Machine Settings
Maintaining consistent pressure, vibration frequency, and amplitude is crucial. Even slight deviations in these settings can lead to poor weld quality.
Variations in the machine's performance, or using equipment that is not regularly calibrated, can result in unstable welds.
Surface Contamination
The presence of dust, grease, or other contaminants on the material surfaces can interfere with the welding process.
When surfaces are not thoroughly cleaned, the bond formed can be compromised, leading to a weaker joint that might fail under stress.
Thermal Overload or Underload
Achieving the perfect temperature during the welding process is a balancing act. If too little heat is generated, the materials may not melt adequately, leading to a weak weld.
Conversely, too much heat can cause damage to the parts or degrade the material properties. This challenge requires careful monitoring of the process.
Material Incompatibility
Not all materials are suitable for vibration welding. Some thermoplastics may have incompatible melting points or chemical properties, leading to poor bond strength or inconsistent weld quality.
Selecting the wrong materials can result in production delays and increased costs.
Solutions and Best Practices
Preventing Burr Formation
- Control Settings: We adjust the vibration amplitude and duration to ensure uniform heat distribution.
- Regular Maintenance: Keeping the equipment well-maintained helps avoid fluctuations that might cause burrs.
- Trial Runs: Testing on sample pieces allows us to fine-tune settings before full production.
Ensuring Proper Alignment
- Quality Fixtures: We use high-quality fixtures and jigs to secure parts in perfect alignment.
- Double-Checking: Always verify the setup before starting the welding process to avoid misalignment issues.
Optimizing Machine Settings
- Calibration: Regular calibration of the equipment ensures that the pressure, frequency, and amplitude remain within optimal ranges.
- Digital Controls: Utilizing machines with digital controls helps maintain consistency throughout the welding process.
Maintaining Clean Surfaces
- Pre-Weld Cleaning: We thoroughly clean all parts to remove dust, grease, and other contaminants.
- Clean Work Environment: Keeping the work area clean also helps prevent surface contamination.
Monitoring Heat Levels:
- Temperature Sensors: Installing temperature sensors and monitoring devices allows us to track heat generation in real time.
- Data Logging: Recording data during the welding process can help us quickly adjust settings to prevent thermal overload or underload.
Addressing Material Incompatibility
- Pre-Selected Material Database: Develop a database of compatible materials to ensure that only suitable thermoplastics are used.
- Material Testing: Conduct material compatibility tests before production to verify that the selected materials will produce a strong and consistent weld.
- Consultation with Suppliers: Work closely with material suppliers to select thermoplastics with similar melting points and chemical properties.
By addressing these specific challenges and implementing the corresponding solutions, we can enhance the reliability and efficiency of the vibration welding process, ensuring high-quality and consistent results.
Future Trends in Vibration Welding
Integration with Advanced Technologies
Smart Manufacturing
One of the major trends is the integration of vibration welding with smart manufacturing systems. This means that sensors and real-time monitoring tools will be built into welding machines.
These sensors will measure temperature, pressure, and vibration frequency in real time, allowing operators to adjust settings on the fly. With digital controls and data analytics, we can achieve greater precision and consistency in our welds.
Automation
As automation becomes more advanced, vibration welding machines will be able to operate with minimal human intervention. Automated systems can reduce errors and improve productivity, which is especially important in high-volume production environments.
Industry 4.0
The rise of Industry 4.0 brings interconnected systems that can share data seamlessly.
Vibration welding equipment will likely be integrated into these smart factories, ensuring that every stage of the production process communicates and collaborates. This connectivity leads to better quality control and quicker adjustments when needed.
Environmental and Material Innovations
Eco-Friendly Processes
Environmental concerns are pushing the industry toward more sustainable practices. In the future, vibration welding will likely adopt eco-friendly methods by reducing energy consumption and minimizing waste.
We expect new technologies to improve energy efficiency and allow for recycling of materials used in the welding process.
Advanced Materials
Research is also leading to the development of new thermoplastic materials that are easier to weld. These materials will be designed to melt uniformly and form stronger bonds.
As material science evolves, we may see more applications of vibration welding in industries that require highly durable and lightweight components.
Enhanced Design and Customization
Customized Welding Profiles
Future trends point to the use of artificial intelligence (AI) to create customized welding profiles. AI can analyze different parts and suggest optimal settings for vibration frequency, amplitude, and pressure. This means that each weld can be tailored specifically to the materials and design requirements, leading to fewer defects and higher-quality products.
User-Friendly Software
Advancements in software will also make it easier for operators to design and test welding processes virtually. With simulation tools, we can predict potential issues and fine-tune the welding process before even touching the machine. This leads to fewer errors and more efficient production cycles.
Conclusion
In summary, our exploration of vibration welding has highlighted its strategic value in modern manufacturing, from its fundamental principles to the emerging trends that are driving its evolution. As an essential technique for creating strong, reliable joints, vibration welding offers significant advantages in efficiency, precision, and cost-effectiveness.
However, the challenges of precise alignment, controlled heat distribution, and consistent large-scale production demand innovative and reliable solutions.
Dizo emerges as a leader in this domain, offering unparalleled expertise and advanced tools that address these challenges effectively. Their state-of-the-art equipment ensures precise control over vibration frequency, amplitude, and pressure, delivering high-quality welds every time.
With comprehensive support and customized solutions tailored to unique manufacturing needs, Dizo stands out as the ideal partner for optimizing production processes and driving industrial excellence.
As the manufacturing landscape continues to evolve, embracing advanced technologies like vibration welding is crucial for staying competitive. We encourage you to leverage Dizo's innovative solutions to enhance your production capabilities, ensure consistent quality, and unlock new growth opportunities.
Choose Dizo as your trusted partner and take a step forward in shaping the future of manufacturing excellence.