How Does Ultrasonic Welding Work? The Science Explained
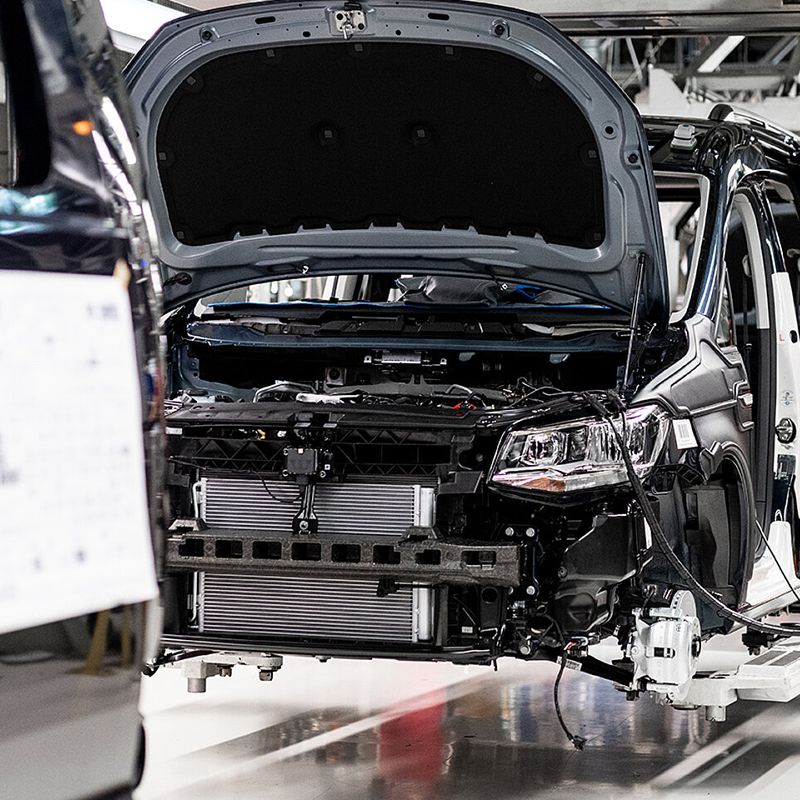
Have you ever wondered how plastic gadgets or metal components in everyday items like toys, car parts, or medical devices are joined so seamlessly? The answer lies in ultrasonic welding, a cutting-edge technology that uses high-frequency sound waves to bond materials without glue, screws, or heat.
Understanding how ultrasonic welding works is essential for industries that rely on precision and efficiency in joining materials. This article explores the science behind ultrasonic plastic welding, its core components, and its wide-ranging applications.
Table of Contents
The Science Behind Ultrasonic Welding
Core Components of an Ultrasonic Welder
How Does an Ultrasonic Welder Work? The Ultrasonic Welding Process
Plastic vs. Metal Welding: Adaptations in Ultrasonic Welding
Material Compatibility in Ultrasonic Welding
Advantages of Ultrasonic Welding Over Traditional Methods
Applications of Ultrasonic Welding
Safety and Best Practices in Ultrasonic Welding
Choosing the Right Ultrasonic Welding Machine
Conclusion: The Future of Ultrasonic Welding
The Science Behind Ultrasonic Welding
Before diving into the technical aspects of how ultrasonic welding machine works, it is crucial to understand its basic principles.
What is ultrasonic welding? Ultrasonic welding is a process that joins materials—primarily thermoplastics and some metals—by applying rapid mechanical vibrations. These vibrations generate localized heat, which causes the materials to soften and bond under controlled pressure.
Ultrasonic welding utilizes high-frequency sound waves (typically 20,000 to 40,000 vibrations per second, or 20-40 kHz) to join materials. These sound waves, inaudible to humans, create friction at the contact point between two materials, generating heat that melts and bonds them together. Once cooled, the materials form a solid, durable joint.
Think of it like rubbing your hands together quickly—they warm up due to friction. Similarly, ultrasonic welding of plastics focuses vibrations precisely where needed, melting only the contact area without affecting the rest of the material.
This process is fast, clean, and energy-efficient, making it ideal for modern manufacturing. Additionally, ultrasonic welding plastic machine setups offer high-speed production capabilities, making them ideal for mass manufacturing.
Core Components of an Ultrasonic Welder
To fully grasp how does an ultrasonic welder work, let's break down its core components:
An ultrasonic welder consists of several key components that work together to create strong, precise bonds:
- Generator: Converts standard electricity into high-frequency electrical energy, powering the welding cycle.
- Transducer: Transforms electrical energy into mechanical vibrations.
- Booster: Amplifies the vibrations, increasing their strength for effective welding.
- Horn (Sonotrode): Focuses the vibrations onto the welding area, ensuring precise energy delivery.
- Anvil: Holds the materials in place during welding, ensuring a clean and strong bond.
These ultrasonic welding components work in harmony to deliver the vibrations needed to melt and bond materials quickly and accurately. The process of how does ultrasonic sealing work follows the same principles, particularly in industries requiring airtight seals, such as food and medical packaging.
How Does an Ultrasonic Welder Work? The Ultrasonic Welding Process
To better understand how ultrasonic welding works, let's go through the step-by-step process:
The ultrasonic welding process can be broken down into the following steps:
- Material Preparation: Place the two pieces to be welded on the anvil.
- Applying Pressure: The horn presses down on the top piece, holding it firmly in place.
- Energy Conversion: The generator converts electricity into high-frequency energy, which the transducer turns into mechanical vibrations.
- Vibration Amplification: The booster increases the vibration strength.
- Energy Focus: The horn directs the vibrations to the contact point between the materials.
- Friction and Heat Generation: The rapid vibrations create friction, melting the materials at the contact point.
- Bond Formation: The melted materials cool and solidify, forming a strong bond.
- Completion: The horn retracts, and the welded part is removed.
This entire ultrasonic welding process often takes less than a second, making ultrasonic welding one of the fastest bonding methods available. This process, applied in ultrasonic welding thermoplastics, typically takes less than a second, making it a fast and efficient method for mass production.
Plastic vs. Metal Welding: Adaptations in Ultrasonic Welding
Ultrasonic welding of plastics is versatile, but the ultrasonic welding process differs for plastics and metals due to their unique properties.
Ultrasonic Welding for Plastics
- Energy Directors: Small raised features on plastic parts concentrate ultrasonic energy, ensuring precise melting and bonding.
- Material Compatibility: Thermoplastics, which melt and solidify under heat, are ideal for ultrasonic welding. Common examples include polyethylene (PE), polypropylene (PP), and ABS.
- Welding Parameters: Adjustments in amplitude, pressure, and welding time are necessary to achieve optimal results. <Check plastic welding tips>
Ultrasonic Welding for Metals
- Higher Energy Requirements: Metals require more energy due to their higher melting points and density.
- Surface Preparation: Cleaning metal surfaces to remove oxides and contaminants is crucial for strong bonds.
- Specialized Equipment: Custom horns and higher power settings are often needed for metal welding.
Material Compatibility in Ultrasonic Welding
When learning how ultrasonic welding works, understanding material compatibility is essential. Not all materials are suitable for ultrasonic welding. Not all materials respond equally well to the process, and selecting the right ones ensures strong, reliable bonds.
For ultrasonic welding plastic, thermoplastics are the best choice. These materials are the most compatible due to their ability to melt and reshape under heat, making them ideal for ultrasound welding.
Common thermoplastics used include:
- ABS (Acrylonitrile Butadiene Styrene): Widely used in automotive and electronic components.
- Polycarbonate (PC): Offers high impact resistance, ideal for medical devices.
- Polypropylene (PP): Commonly used in packaging and consumer goods.
- Polyethylene (PE): Suitable for applications requiring flexibility and durability.
When working with metals, ultrasonic sealing technology change slightly. Metals require higher energy input, and surface preparation is crucial. While softer metals like aluminum and copper can be ultrasonically welded, harder metals require alternative bonding methods.
Ultrasonic Welding Key Design Considerations
Energy Directors: Small ridges or bumps that focus ultrasonic energy for precise bonding.
Joint Design: Common designs include butt joints, shear joints, and tongue-and-groove joints, each suited for different applications.
Wall Thickness: Optimal thickness ranges from 0.5 to 5 mm for thermoplastics, ensuring strong bonds without warping
Advantages of Ultrasonic Welding Over Traditional Methods
Compared to other welding techniques, understanding how does sonic welding work highlights several key advantages:
- Speed: Most welds are completed in under a second, boosting production efficiency.
- Precision: Localized heat application ensures only the bonding area is affected.
- Energy Efficiency: Since external heat sources aren't required, energy consumption is minimized.
- Clean Process: No adhesives, solvents, or consumables are needed, reducing waste.
- Versatility: Works with a range of materials, particularly ultrasonic welding for plastics and even certain metals.
- Consistent Quality: Automated settings ensure repeatable results with minimal defects.
Whether for plastic to plastic welding or sealing delicate electronic parts, a ultrasonic welding machine provides a fast, clean, and cost-effective solution for modern manufacturing.
Applications of Ultrasonic Welding
Now that we know how do ultrasonic welders work, it's important to explore their practical applications across industries:
- Automotive Industry: Used for assembling plastic dashboards, airbag components, and fuel systems.
- Medical Sector: Essential for producing sterile, airtight seals in ultrasonic welding of plastics for surgical instruments, implantable devices, and diagnostic equipment.
- Consumer Electronics Manufacturing: Ensures precise bonding of delicate components in smartphones, laptops, and wearable tech.
- Packaging Industry: Utilized in how does ultrasonic sealing work to create leak-proof blister packs, food packaging, and tamper-evident seals.
- Textile Industry: Applied in seamless garment production, protective gear, and footwear.
- Aerospace Industry: Lightweight aircraft components and satellite parts ultrasonic welding.
- Home Appliances: Refrigerator shelves, washing machine panels, and vacuum cleaner parts.
Each industry benefits from the speed and precision of ultrasonic welding plastic technology, ensuring high-quality, repeatable results.
Safety and Best Practices in Ultrasonic Welding
Understanding how ultrasonic welding works also involves ensuring safety and efficiency during operations. Operators of ultrasonic welding plastic machines must follow strict safety guidelines to prevent accidents and ensure consistent quality.
- Hearing Protection: Since ultrasonic frequencies are above human hearing range, the equipment itself may generate noise that requires ear protection.
- Proper Training: Employees handling ultrasonic welders for plastics must receive adequate training to understand machine settings and avoid errors.
- Equipment Maintenance: Regular inspections ensure that the ultrasonic welding process remains efficient and that the machine components, such as the horn and transducer, function optimally.
- Workspace Cleanliness: Keeping the work area free from debris prevents contamination of ultrasonically welded parts and ensures strong bonds.
- Material Handling: Using compatible plastics and metals ensures proper fusion, reducing weak joints or failed bonds.
By implementing these best practices, manufacturers can optimize how ultrasonic welding machines work while maintaining a safe production environment.
Choosing the Right Ultrasonic Welding Machine
Ultrasonic welding is a revolutionary technology that offers speed, precision, and versatility across various industries. By understanding its principles, components, and applications, manufacturers can leverage this method to create strong, reliable bonds efficiently and safely.
Whether you're working with plastics or metals, ultrasonic welding provides a cleaner, faster, and more cost-effective solution compared to traditional methods.
To ensure consistent quality and reliable welds, advanced technology alone is not enough—you need a trusted partner with the right expertise and resources and invest the right ultrasonic welder for achieving strong and reliable bonds. <Learn how to use ultrasonic welder>
Dizo Global stands out as a leading provider of ultrasonic welding solutions, offering a combination of cutting-edge technology, proven expertise, and a strong focus on customer satisfaction.
With Dizo, you gain access to state-of-the-art equipment and tailored solutions designed to meet your specific welding needs. Their team of experts is dedicated to helping you achieve high-quality, problem-free results, ensuring your production processes run smoothly and efficiently.
- Material Compatibility: Ensure the machine supports ultrasonic welding thermoplastics or metals, depending on your production needs.
- Power and Frequency: The power output and frequency range affect how does an ultrasonic welder work for different materials.
- Automation Features: Some advanced ultrasonic welding plastic machines offer programmable settings for higher precision.
- Machine Size and Capacity: Choose a machine that fits your production scale, whether for small electronics or large automotive parts.
- Manufacturer Reputation: Trusted brands provide reliable machines with consistent performance and support.
Understanding how ultrasonic welding machines work helps businesses select the best equipment for their specific applications.
Conclusion: The Future of Ultrasonic Welding
Ultrasonic welding continues to transform industries by providing a fast, reliable, and environmentally friendly alternative to traditional bonding methods. With growing advancements in automation, material science, and energy efficiency, the future of ultrasonic welding of plastics and metals is promising.
By mastering how ultrasonic welding works and investing in high-quality equipment, businesses can enhance production efficiency, reduce costs, and maintain superior product quality. Whether in automotive, medical, electronics, or packaging industries, ultrasound welding remains a cornerstone of modern manufacturing.
Now that you understand how ultrasonic welding machines work, you can explore the best solutions for your specific needs. With the right technology and expertise, ultrasonic welding can take your production to the next level.
Don't let welding challenges hinder your progress. Contact Dizo Ultrasonic today to elevate your welding projects and experience the difference that a trusted partner can make. Whether you're working with plastics, metals, or specialized materials, Dizo has the tools and knowledge to deliver exceptional results for your business.