How to Use Plastic Welder to Weld Plastic Together
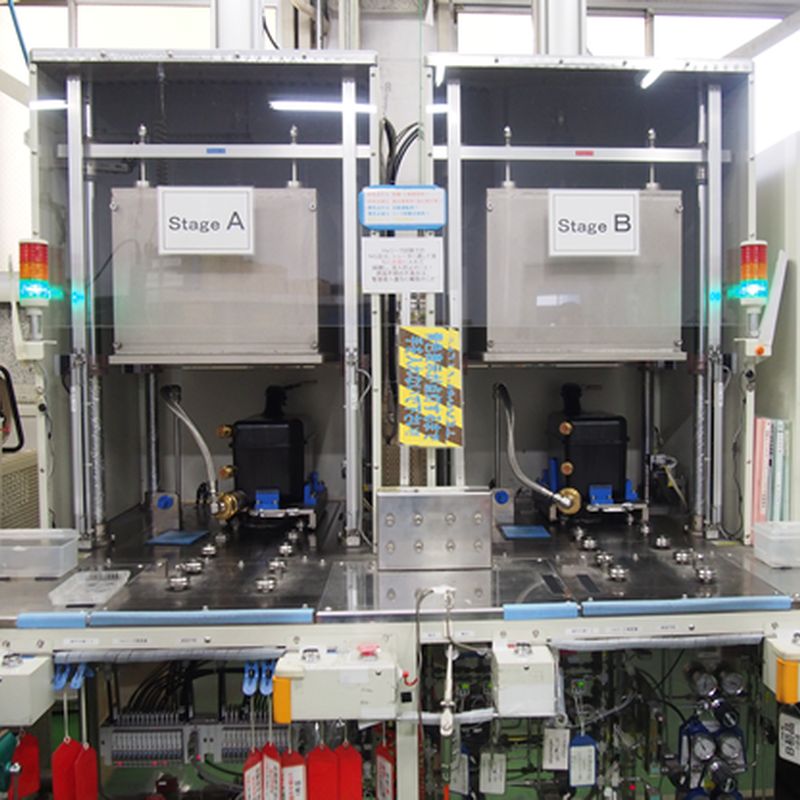
Plastic welding is an essential process for joining plastic together, used across industries from DIY projects to manufacturing. This guide helps both DIY enthusiasts and professionals master plastic joining techniques through practical steps.
Here, we'll take you through the different types of plastic welding techniques, the essential plastic welding machines you'll need, and a step-by-step guide on how to use a plastic welder effectively.
We'll also cover how does plastic welding work and some safety tips to help you get the best results from your plastic welding process.
Table of Contents
Types of Plastic Welding Techniques
Essential Plastic Welding Equipment
Step-by-Step Guide to Using a Plastic Welding Machine
Safety Precautions When Using Plastic Welders
FAQs
Conclusion
Types of Plastic Welding Techniques
There are several plastic welding techniques, each suited for different types of plastic materials and specific welding needs. Let's explore the most common methods of plastic welding to help you choose the best way to weld plastic together for your project.
Ultrasonic Welding
Ultrasonic welding uses high-frequency sound waves to generate heat, melting and joining plastic together. This precise method excels with small components, particularly in electronics and medical device manufacturing. For example, when producing small electronic enclosures, ultrasonic welding creates strong bonds while protecting delicate internal components.
Hot Plate Welding
Hot plate welding uses a heated metal plate placed between two plastic pieces to be joined. The parts are pressed against the plate until they melt and bond. This plastic welding method works well for large components, especially in automotive manufacturing where it joins large parts like bumpers with reliable strength.
Vibration Welding
Vibration welding creates frictional heat through mechanical vibrations where plastic parts meet, melting and bonding them together. It excels at joining large, complex-shaped parts. A 2025 automotive industry report shows vibration welding handles 68% of car bumper repairs, thanks to its effectiveness with irregular surfaces.
Hot Air Welding
Hot air welding directs a hot air stream to melt plastic edges, which are then pressed together to bond. This plastic welding techniques work with many plastics, from PVC to polyethylene, making it popular for both DIY and professional repairs. A common application is fixing plastic garden hoses, where it quickly seals leaks.
Extrusion Welding
Extrusion welding feeds plastic rods or filaments through a heated nozzle, melting and applying them to join pieces. This plastic welding method suits larger, thicker parts, especially in construction for welding pipes and sheets. Its ability to add material during welding creates strong joints for heavy-duty uses.
Laser Welding
Laser welding delivers precise heat to melt plastic at the weld joint. Its accuracy makes it ideal for electronics manufacturing, such as welding mobile phone casings. In packaging, it creates clean, strong bonds essential for product integrity.
Hot Riveting
Hot riveting combines heated metal rivets with plastic joining techniques. While less common, it serves specific needs where mechanical fasteners complement heat welding. These plastic joining techniques particularly suits industrial equipment requiring high structural strength.
Essential Plastic Welding Equipment
Can plastic be welded together? To successfully weld plastic together, having the right plastic welding equipment is crucial. Using the proper tools ensures that you achieve strong, reliable plastic welds.
Below, we've outlined the essential items you'll need to get started with using a plastic welder.
Plastic Welding Machine
- Hot Air Welders: Ideal for hot air welding techniques. These welders offer temperature control for precise operation, with adjustable heat settings to match different plastic materials.
- Extrusion Welders: These plastic welding machines extrude plastic material through a heated nozzle, creating thick, strong joints.
- Ultrasonic Welders: Designed for smaller, delicate components using high-frequency sound wave welding.
Plastic Welding Rods
Plastic welding rods are essential for fusing plastic parts. Available in materials like polyethylene, PVC, and polypropylene, you must match the rod type to your plastic.
For instance, PVC pipes require PVC-compatible welding rods for strong bonds.
Heat Gun (for Hot Air Welding)
A heat gun delivers concentrated hot air to melt plastic at joints. Temperature and airflow settings vary by material—thin sheets need gentle heat and airflow, while thicker plastics require higher temperatures and stronger airflow.
Welding Nozzles
Welding nozzles direct heat from guns or extrusion welders. They come in various sizes and shapes to control airflow and heat distribution. Narrow nozzles suit precision work, while wider ones cover larger areas.
Plastic Scraper
A plastic scraper cleans surfaces before welding, removing dirt, debris, and old adhesives that could compromise the weld. Always clean parts thoroughly before joining.
Protective Gloves
Heat-resistant gloves made of Kevlar or leather are essential for handling hot plastic and equipment. They prevent burns while providing a secure tool grip.
Safety Glasses
Safety glasses or goggles protect against flying debris and hot plastic. Wear them throughout the welding process, especially during high-temperature work.
Clamps or Clamping Jigs
Clamps secure plastic parts during cooling and bonding, ensuring proper alignment and preventing weak welds. Hold pieces firmly until the weld cools completely.
Thermometer or Temperature Control
Precise temperature control is crucial for techniques like a hot plate or hot air welding. Use a thermometer or built-in controls to monitor heat. For PVC welding, the American Welding Society recommends 600°F (315°C) for even melting.
Cleaning Solution
Clean surfaces thoroughly before welding to remove oils, dirt, and contaminants. Use plastic-appropriate cleaners—for example, mild detergent solutions work well for polyethylene.
Step-by-Step Guide to Using a Plastic Welding Machine
Now that you have the right tools, it's time to get started with the plastic welding process! How do you use a plastic welder? Here are simple steps to guide you how to use a plastic welding machine effectively.
This guide will walk you through each stage, from preparing your materials to finishing your weld.
Step 1: Preparation of Materials
Clean the Plastic Surfaces: Use a plastic scraper or cleaning solution to remove dirt, oils, and debris from the surfaces you intend to weld. Contaminants weaken the bond, so thorough cleaning is crucial. For example, when welding a plastic container, clean it thoroughly inside and out.
Cut the Plastic to Size: Ensure plastic parts are sized correctly with smooth edges. This ensures perfect fit during welding. When cutting plastic sheets for a DIY project, use a sharp utility knife or plastic-cutting saw for clean, accurate cuts.
Check Compatibility: Ensure welding rods or filler material match your plastic type. This is crucial for materials like PVC, polypropylene, or polyethylene. For instance, when welding a PVC pipe, use PVC-specific welding rods.
Step 2: Setting Up the Machine
Set the Temperature: Adjust to the recommended temperature for your plastic type and plastic welding technology. Consult the machine's manual for specific settings. For example, when using a hot air welder on polyethylene, set to 450°F (232°C).
Load the Welding Rod: If using a welding rod, load it according to manufacturer instructions. Ensure rod compatibility with your plastic material. For extrusion welders, insert the rod carefully into the feeder mechanism.
Attach Nozzles or Accessories: Install the appropriate nozzle or welding tip. For heat guns, select narrow nozzles for detailed work or wider ones for larger areas.
Step 3: Performing the Weld
How does plastic welding work? Below are the details:
Position the Plastic Parts: Align pieces where you want the weld. Use clamps or jigs as needed for proper positioning. For pipe welding, use a pipe-welding jig for perfect alignment.
Apply Heat: Turn on the machine and apply heat evenly across the weld joint. With hot air or extrusion welding, maintain steady movement. For ultrasonic welding, the machine controls the process automatically.
Fuse the Pieces: Apply appropriate pressure as the plastic melts and fuses. In hot plate welding, press parts against the heated plate until they bond. With handheld extrusion welders, press the extruded plastic gently onto the joint.
Monitor the Weld: Watch for proper melting and bonding. Avoid overheating, which weakens welds or burns plastic. Reduce heat immediately if the plastic browns or smokes.
Step 4: Cooling and Finishing Touches
Allow the Weld to Cool: Let the welded plastic cool and harden. Avoid touching hot welds. Cooling time varies from minutes to hours, depending on size and thickness.
Remove Clamps: After cooling and solidification, remove clamps or jigs for a clean, finished weld.
Inspect the Weld: Check for imperfections like cracks, gaps, or weak spots. Use a magnifying glass for detailed inspection. Perform additional welding or smoothing if needed.
Trim Excess Material: Remove any excess plastic with a scraper or cutter for a professional finish.
Safety Precautions When Using Plastic Welders
Plastic welding involves high temperatures and powerful machinery, so it's essential to prioritize safety at all stages of the process. By following the right safety precautions, you can avoid accidents and ensure that your plastic welding project goes smoothly.
Here are some key safety tips to keep in mind:
Wear Protective Gear
- Heat-Resistant Gloves: Essential for handling hot plastic and equipment. These protect your hands from burns while providing a secure grip on tools. Always wear them when operating a plastic welder.
- Safety Glasses or Goggles: Protect your eyes from hot plastic particles, fumes, and dust during welding. These are essential for every welding project.
- Long-Sleeved Clothing: Wear flame-resistant long sleeves to protect your skin from heat and molten plastic splashes.
- Closed-Toe Shoes: Wear sturdy, closed-toe shoes to protect your feet from falling tools and hot plastic.
Work in a Well-Ventilated Area
Use Fume Extractors: When working with plastics that produce harmful fumes (like PVC), use a fume extractor or exhaust fan to direct fumes away from your breathing area.
Work Outdoors if Possible: Ensure proper ventilation with windows or exhaust fans when working indoors. For toxic plastics, work outdoors or in a dedicated space with good airflow.
Keep the Work Area Clean and Organized
- Clear the Area of Flammable Materials: Remove nearby flammable items like paper, wood, or chemicals to prevent fire hazards.
- Keep Tools and Equipment Organized: Store tools, rods, and plastic welding machines properly to prevent tripping hazards and improve efficiency.
- Use Heat Shields: When welding near sensitive surfaces, use protective barriers to prevent accidental burns or heat damage.
Be Cautious with the Welding Machine
- Turn Off the Machine After Use: Power down the machine when not in use to prevent overheating and electrical accidents.
- Check for Malfunctions: Regularly inspect for damage to power cords, nozzles, or temperature controls. Stop using and repair the machine if issues arise.
- Keep the Machine Dry: Never use the machine with wet hands or in damp environments to prevent electrical shock.
Follow Manufacturer Instructions
- Temperature Settings: Set the correct temperature for your specific plastic type. Consult the manual for proper settings.
- Proper Rod and Material Compatibility: Use welding rods and filler materials that match your plastic-type to ensure strong welds.
- Machine Maintenance: Follow the recommended maintenance schedule to ensure safe operation and extend machine life.
Keep Fire Extinguishers Nearby
Use a Class ABC Fire Extinguisher: Keep an accessible, well-maintained ABC fire extinguisher ready for all types of fires, including plastic fires.
Never Leave the Welding Machine Unattended
Stay with the machine while it's running to prevent accidents and monitor the welding process. This helps avoid burns, electrical issues, and other hazards.
FAQs
Find out how to use plastic welding machine related questions. We answer your questions here.
How do I choose the right plastic welding machine?
When selecting a plastic welding machine, consider these key factors: the type of plastic (PVC, PP, PE), material thickness, welding method (hot air, ultrasonic, vibration), and operation scale (manual vs. automated).
Evaluate the power requirements, temperature control features, ease of use, maintenance needs, and the type of welding joint needed. For instance, if you work primarily with thin plastic sheets requiring precision, an ultrasonic welder would be your best option.
What temperature should a plastic welder be?
Plastic welding temperatures range from 350°F to 750°F (177°C to 399°C), varying by plastic type. The American Welding Society (AWS) recommends 600°F (315°C) for PVC and 450°F (232°C) for polyethylene.
Always consult your manufacturer's specifications for the optimal temperature for your specific material and follow the best way to weld plastic together as mentioned above.
What are the common mistakes to avoid in plastic welding?
Key mistakes in plastic welding include incorrect temperature settings (causing poor fusion or degradation), uneven welding speed (resulting in weak seams), improper joint preparation (leading to poor weld quality), and insufficient pressure (creating gaps or weak bonds). For instance, using too low a temperature will result in a weak joint that fails easily.
What materials can be welded using a plastic welding machine?
Plastic welding machines work with various thermoplastics including PVC (Polyvinyl Chloride), PE (Polyethylene), PP (Polypropylene), ABS (Acrylonitrile Butadiene Styrene), HDPE (High-Density Polyethylene), and LDPE (Low-Density Polyethylene).
These materials are essential in automotive, construction, and packaging industries. For example, automotive manufacturers frequently use PP welding for interior components.
How to identify and fix common plastic welding problems?
Weak/Inconsistent Welds: Caused by incorrect temperature, speed, or pressure.
Solution: Adjust settings and ensure clean surfaces before rewelding.
Burnt Plastic: Results from overheating.
Solution: Lower the temperature to match your material.
Warping/Distortion: Caused by rapid overheating.
Solution: Reduce temperature or slow down the heating process.
Porous Welds: Results from poor fusion or contamination.
Solution: Clean surfaces thoroughly and use compatible filler material.
Conclusion
Plastic welding offers a versatile and efficient way to join plastic materials. By mastering various plastic welding techniques, using appropriate equipment, and following safety protocols, you can achieve professional results. With practice and proper preparation, your plastic welding projects will be both safe and effective.
How do you use a plastic welder? Remember to select the right plastic welding machine for your materials, use appropriate temperatures, and allow sufficient cooling time for strong, lasting results.
Dizo Global's ISO-certified machines are trusted by automotive manufacturers worldwide for precision welding. Whether you're tackling DIY household repairs or industrial-scale projects, our equipment meets your needs.
Consider exploring eco-friendly options like recycled plastic welding rods, and stay informed about emerging technologies such as infrared welding, which offers non-contact joining methods. Continuous learning and adaptation will keep you at the forefront of plastic welding, making your projects both functional and environmentally responsible.
Now you have learned how to use a plastic welder. With the plastic welding technology mastered, you can confidently approach any plastic repair or fabrication project. Get started today to create strong, durable plastic welds.