How to Perform Hot Plate Plastic Welding for Automotive Polyethylene Petrol Tanks Filler Pipes
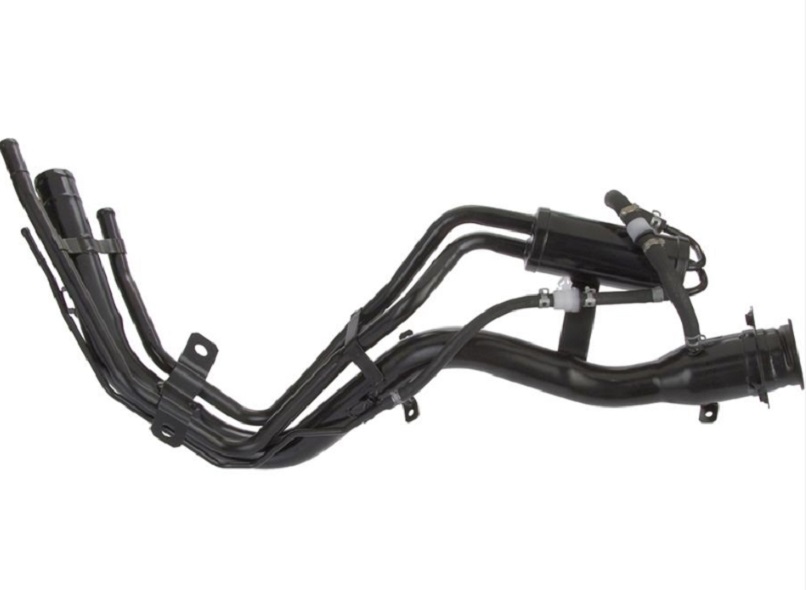
When it comes to joining thermoplastics, hot plate welding is a highly effective technique used in various industries, including automotive manufacturing. In particular, hot plate welding is commonly employed for welding automotive polyethylene petrol tanks filler pipes. This process involves using a hot plate plastic welder to melt and fuse the thermoplastic materials together, creating a strong and durable bond. In this article, we will explore the steps involved in performing hot plate plastic welding for automotive polyethylene petrol tanks filler pipes, as well as the advantages and disadvantages of this welding method.
Understanding Hot Plate Welding
Hot plate welding is a thermoplastic joining procedure that utilizes a heating principle to melt two thermoplastic workpieces at the joining area. The process involves applying a heated object, known as a hot platen, to the plastic halves of the part or product. The hot platen melts the thermoplastic material, which is then pressed together under pressure until it solidifies and forms a fusion. This technique is particularly suitable for challenging welding requirements, such as large welding sizes and complex geometric shapes.
Hot plate welding offers several advantages for automotive polyethylene petrol tanks filler pipes welding. Firstly, it has excellent plastic joining ability, making it ideal for welding thermoplastic materials with complex shapes and designs. Additionally, hot plate welding produces strong and airtight welds, ensuring the integrity and performance of the petrol tanks. It is also compatible with a wide range of plastic materials, allowing for versatility in automotive applications. Moreover, hot plate welding enables the joining of different materials with large differences in melting temperatures, making it suitable for welding automotive polyethylene petrol tanks filler pipes.
However, hot plate welding does have some limitations. It consumes a significant amount of power and has relatively long cycle times compared to other welding methods. Additionally, certain materials, such as nylon, may not yield satisfactory welding results due to carbonization. The process also generates smoke, which can cause pollution. Despite these drawbacks, hot plate welding remains a popular choice for automotive polyethylene petrol tanks filler pipes welding due to its stability, high welding performance, and cost-effectiveness.
The Basic Operation Process of Hot Plate Welding
The hot plate welding process for automotive polyethylene petrol tanks filler pipes involves several key steps:
- Loading Part: The plastic halves of the petrol tank filler pipes are loaded into the hot plate welding fixtures.
- Hot Platen In: The hot platens move forward, positioning themselves between the two plastic halves.
- Jig Close: The plastic halves are moved towards the hot platens under pressure from the hot plate welding fixtures.
- Hot Platen Melting: The hot platens heat the plastic parts at the joining area until they melt and form a molten line.
- Jig Open: Once the melting is complete, the plastic halves are separated from the hot platens by the fixtures.
- Fusing: The hot plate welding fixtures move towards each other, applying pressure to keep the molten plastic halves in contact.
- Jigs Re-open: After the appropriate fusing time, one of the jigs releases the welded parts, and the hot plate welding fixtures move apart.
- Unloading Parts: The welding plastic parts are removed from the hot plate welding fixtures.
These steps ensure the proper fusion and bonding of the plastic halves, creating a strong and secure weld for the automotive polyethylene petrol tanks filler pipes.
Selecting the Right Materials for Hot Plate Welding
In hot plate welding, it is crucial to select the appropriate thermoplastic material for welding automotive polyethylene petrol tanks filler pipes. The most common material used for these applications is high-density polyethylene (HDPE). HDPE is known for its excellent elasticity, chemical resistance, and strength-to-density ratio, making it a suitable choice for petrol tank filler pipes.
When choosing the material for hot plate welding, it is essential to consider its weldability and compatibility with the welding process. HDPE is a thermoplastic material that can be re-melted and re-shaped multiple times, making it ideal for hot plate welding. Other thermoplastics, such as polypropylene (PP), polyvinyl chloride (PVC), and chlorinated polyvinyl chloride (CPVC), may also be suitable for hot plate welding. It is important to ensure that the chosen material can withstand the welding temperatures and produce a reliable and durable weld.
Equipment and Safety Measures for Hot Plate Welding
To perform hot plate welding for automotive polyethylene petrol tanks filler pipes, specific equipment and safety measures are necessary. The following are key considerations:
Hot Plate Welding Equipment
Hot plate welding requires specialized equipment, including a hot plate plastic welder. It is recommended to use a reliable and high-quality welder to ensure consistent and precise welding results. The equipment should have temperature control capabilities to achieve the desired melting temperature for the chosen thermoplastic material. Additionally, the equipment should allow for pre-storing multiple welding procedures and have an intuitive man-machine interface for easy operation.
Safety Measures
Safety is of utmost importance in hot plate welding. The equipment should be equipped with protective measures such as a protective grating and a safety baffle to prevent scalding accidents. It is also essential to implement authority management, distinguishing between administrators and operators to ensure proper control and supervision of the welding process. The working table should be set at a suitable height for ergonomic operation, and the equipment should incorporate a two-hand start mechanism for added safety.
Conclusion
Hot plate welding is a highly effective method for joining thermoplastic materials, particularly for automotive polyethylene petrol tanks filler pipes welding. This process offers numerous advantages, including excellent plastic joining ability, strong and airtight welds, and compatibility with a wide range of plastic materials. While there are some limitations and considerations, such as power consumption and material compatibility, hot plate welding remains a popular choice in the automotive industry. By following the proper operation process, selecting the right materials, and ensuring equipment and safety measures, successful hot plate plastic welding can be achieved for automotive polyethylene petrol tanks filler pipes.