How to Check Vibration Welding Parameters?
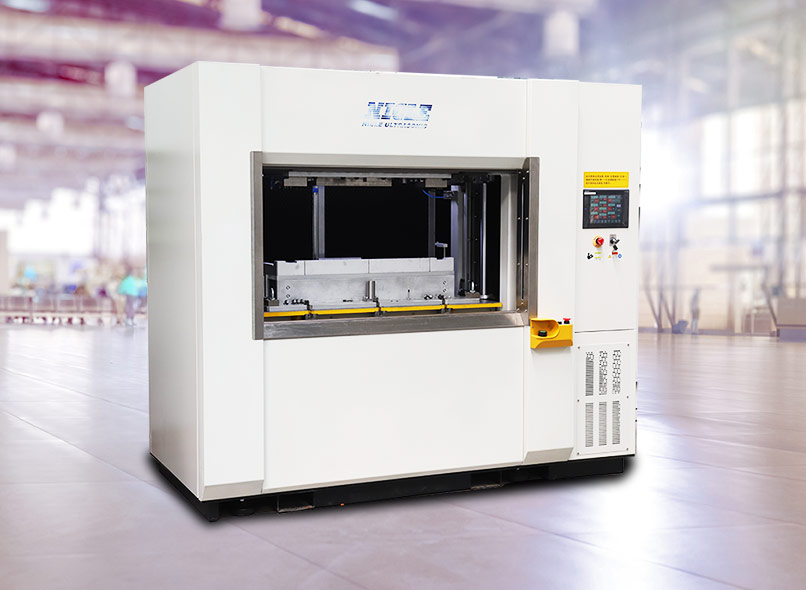
To ensure the success of a vibration welding process, it is essential to carefully check and adjust the parameters involved. Follow these steps to check the vibration welding parameters:
- Parameter Configuration: Start by ensuring that the parameter settings for the vibration welding process are properly configured. This includes the initial setup of the welding machine and selecting the appropriate parameters for the specific materials being joined.
- Vibration Amplitude: Verify that the vibration amplitude is set to the desired level. The amplitude refers to the maximum displacement of the vibrating tool or the welding horn. It plays a crucial role in determining the energy input into the joint. By adjusting the amplitude, welders can control the level of vibration transmitted to the materials, which directly impacts the depth and intensity of the weld. It is important to find the right balance, as excessive amplitude can lead to material damage or even failure, while insufficient amplitude may result in incomplete fusion.
- Vibration Frequency: Check the frequency of the vibration. Frequency refers to the number of cycles per second and is typically measured in hertz (Hz). The frequency determines the speed at which the materials are vibrated, affecting the overall welding time and the quality of the weld. Higher frequencies generally result in faster welding times but require precise control to avoid overheating or inadequate fusion. Lower frequencies, on the other hand, may allow for better heat dissipation but can lead to longer welding cycles. Adjust the frequency based on the material being welded and the desired welding outcome.
- Pressure Control: Confirm that the pressure applied during the vibration welding process is within the specified range. Pressure is an essential parameter that significantly influences the success of vibration welding. The pressure applied ensures proper contact between the materials and promotes heat generation. It is typically measured in kilopascals (kPa). The optimal pressure depends on various factors such as the material properties, joint design, and desired weld strength. Insufficient pressure may result in poor fusion and weak welds, while excessive pressure can cause material deformation or even material ejection. Carefully monitor and adjust the pressure to achieve the desired welding outcome.
- Welding Time Optimization: Time is a crucial parameter that cannot be overlooked in vibration welding. The duration of the welding process determines the time the materials are subjected to vibration and pressure. Welding for too short a time may result in incomplete fusion, whereas welding for too long can lead to excessive heat generation, material degradation, or even damage to the welding equipment. Welders must carefully optimize the welding time based on the specific materials being joined to ensure proper fusion and a reliable weld. Consider factors such as material thickness, joint design, and the desired quality of the weld when determining the appropriate welding time.
- Temperature Control: Temperature control is another important aspect of vibration welding. The temperature at which the vibration welding process is performed can vary depending on the materials being joined. It is crucial to consider the melting point and thermal properties of the materials to avoid overheating, thermal degradation, or inadequate fusion. Welders often employ various techniques such as preheating or controlling the cooling rate to achieve the desired temperature profile during the welding process. Monitor the temperature closely and make necessary adjustments to maintain optimal welding conditions.
- Material Composition and Surface Preparation: Apart from the primary parameters, the material composition and surface preparation also play a significant role in the vibration welding process. Different materials may require specific parameter adjustments. Consider factors such as the chemical composition, surface condition, and cleanliness of the materials being joined. Ensure that surfaces are properly prepared, free from contaminants, and have suitable roughness for effective welding.
- Welding Tool Design: The design and condition of the welding tool can impact the vibration welding process. Ensure that the tool is in good condition, properly aligned, and suitable for the specific welding application. The tool design should facilitate proper contact and transfer of vibration to the materials being welded.
By following these steps and considering all the relevant factors, you can effectively check the vibration welding parameters and ensure the successful execution of the welding process.
Parameter Settings for Vibration Welding Process
To achieve optimal results in vibration welding, it is crucial to understand and control the different parameters that influence the welding process. These parameters not only determine the quality and strength of the resulting weld but also impact the overall efficiency and productivity of the welding operation.
Here are the key parameters that need to be considered for the parameter settings in vibration welding:
- Amplitude: The amplitude refers to the maximum displacement of the vibrating tool or the welding horn. It plays a vital role in determining the energy input into the joint. By adjusting the amplitude, welders can control the level of vibration transmitted to the materials, which directly impacts the depth and intensity of the weld. It is important to find the right balance, as excessive amplitude can lead to material damage or even failure, while insufficient amplitude may result in incomplete fusion.
- Frequency: Frequency refers to the number of cycles per second and is typically measured in hertz (Hz). The frequency determines the speed at which the materials are vibrated, affecting the overall welding time and the quality of the weld. Higher frequencies generally result in faster welding times but require precise control to avoid overheating or inadequate fusion. Lower frequencies, on the other hand, may allow for better heat dissipation but can lead to longer welding cycles.
- Pressure: Pressure is an essential parameter that significantly influences the success of vibration welding. The pressure applied during the vibration welding process is vital for achieving proper contact between the materials and promoting heat generation. It is typically measured in kilopascals (kPa). The optimal pressure depends on various factors such as the material properties, joint design, and desired weld strength. Insufficient pressure may result in poor fusion and weak welds, while excessive pressure can cause material deformation or even material ejection.
- Time: Time is a crucial parameter that cannot be overlooked in vibration welding. The duration of the welding process determines the time the materials are subjected to vibration and pressure. Welding for too short a time may result in incomplete fusion, whereas welding for too long can lead to excessive heat generation, material degradation, or even damage to the vibration welding equipment. Welders must carefully optimize the welding time based on the specific materials being joined to ensure proper fusion and a reliable weld.
- Temperature: Temperature control is another important aspect of vibration welding. The temperature at which the welding process is performed can vary depending on the materials being joined. It is crucial to consider the melting point and thermal properties of the materials to avoid overheating, thermal degradation, or inadequate fusion. Welders often employ various techniques such as preheating or controlling the cooling rate to achieve the desired temperature profile during the vibration welding process.
In addition to these primary parameters, other factors such as material composition, surface preparation, and welding tool design can also influence the vibration welding process. It is essential to consider these factors and fine-tune the parameters accordingly to achieve optimal results.
In conclusion, the parameters of vibration welding, including amplitude, frequency, pressure, time, and temperature, play a critical role in determining the success and quality of the vibration welding process. By understanding and effectively controlling these parameters, welders can ensure the reliable joining of materials, achieve high-quality welds, and enhance the overall efficiency of the welding operation.