How to Use a Hot Plate Welding Machine for Fuel Tanks Made of Blow-Molded HDPE
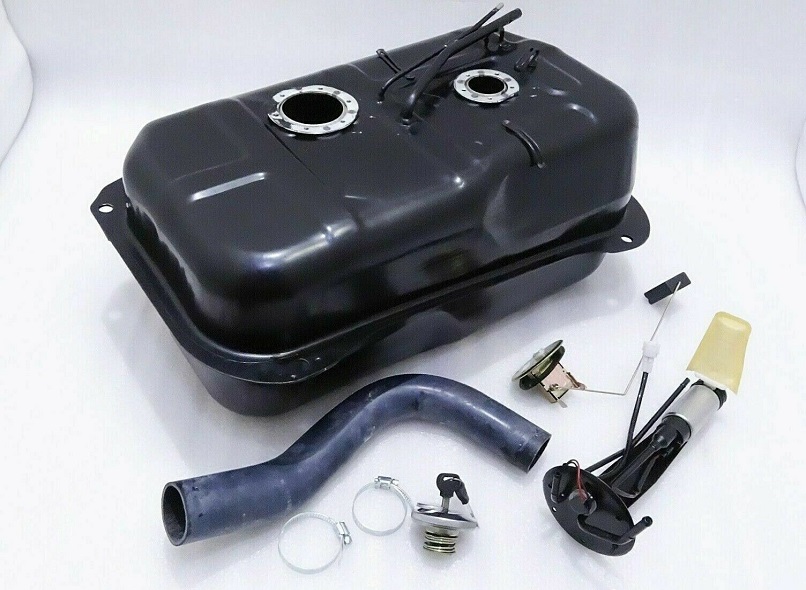
When it comes to creating fuel tanks, there are various materials and welding techniques available. One of the lesser-known methods is hot plate welding, a process that can be used to join parts made of blow-molded HDPE. In this article, we will explore the art of hot plate welding and its application in fabricating fuel tanks. We will discuss the benefits of using this technique, the steps involved in the welding process, and the considerations to keep in mind for successful fuel tank fabrication.
The Advantages of Hot Plate Welding
Hot plate welding offers several advantages that make it an attractive option for fuel tank fabrication. One of the key benefits is its ability to provide strong and reliable welds. The process involves heating the surfaces of the parts to be joined using a heated plate, which creates a molten layer. When the surfaces are pressed together, the molten layer solidifies, creating a robust bond.
Additionally, hot plate welding is suitable for HDPE, a material known for its resistance to petrol, including ethanol. HDPE is also easy to shape, cost-effective, and has a slight flexibility that prevents denting. These properties make it a suitable material for fuel tanks, and hot plate welding allows for precise and secure connections between HDPE parts.
Understanding the Hot Plate Welding Process
The hot plate welding process involves several steps that ensure a successful weld. Here is an overview of the process:
- Preparation: Before beginning the welding process, the parts to be joined must be properly prepared. This includes cleaning the surfaces to remove any contaminants that could affect the weld quality.
- Heating the Plate: The first step in hot plate welding is heating the plate to the appropriate temperature. The temperature depends on the material being welded and is crucial for achieving a proper bond.
- Clamping the Parts: Once the plate is heated, the parts to be welded are clamped onto the plate, ensuring that the surfaces to be joined are in contact with the heated plate.
- Heating and Melting: The heated plate transfers heat to the surfaces of the parts, causing them to soften and melt. The molten layers fuse together, creating a strong bond.
- Cooling and Solidification: After the desired welding time, the parts are removed from the heated plate and allowed to cool. As the molten layers solidify, the bond between the parts strengthens.
- Finishing: Finally, any excess material or flash is trimmed off, and the welded assembly undergoes quality checks to ensure it meets the required specifications.
Considerations for Successful Fuel Tank Fabrication
While hot plate welding is a reliable process, there are several considerations to keep in mind for successful fuel tank fabrication.
Material Selection
Choosing the right material is crucial for the durability and performance of the fuel tank. HDPE is a popular choice due to its resistance to petrol and ease of shaping. However, it's important to ensure that the HDPE used meets the necessary standards and regulations for fuel tank applications.
Design and Geometry
The design and geometry of the fuel tank play a significant role in its functionality and structural integrity. It is essential to consider factors such as the tank's shape, wall thickness, and reinforcement to prevent issues like oil canning or excessive flexing.
Welding Parameters
The welding parameters, including temperature, pressure, and welding time, must be carefully controlled to achieve optimal weld strength. These parameters may vary depending on the material being welded, so it's crucial to follow the manufacturer's guidelines and perform proper testing and validation.
Quality Control
Implementing robust quality control measures is essential to ensure the reliability and safety of the fuel tank. This can include non-destructive testing, visual inspection, pressure testing, and adherence to industry standards and regulations.
Hot Plate Welding Machine for Fuel Tanks Made of Blow-Molded HDPE
In this article, we will discuss the process of using a hot plate welding machine to assemble fuel tanks made of blow-molded HDPE. These fuel tanks typically consist of various components that need to be welded together, including clips, filler necks, vent lines, heat shield boss plugs, gas vent valves/roll over valves, breather nipples, and brackets.
By following the steps outlined below, you will be able to effectively and efficiently weld these parts together using a hot plate welding machine.
- Prepare the welding area: Ensure that the work area is clean and free of any debris. Place the fuel tank components in the correct positions for welding.
- Set up the hot plate welding machine: Adjust the temperature and pressure settings of the hot plate welding machine according to the specifications provided by the manufacturer and the material being used (blow-molded HDPE).
- Align the parts: Carefully align the parts to be welded together, ensuring that they fit snugly and securely.
- Welding process: Place the aligned parts on the hot plate of the welding machine. Apply pressure to hold the parts in place and initiate the heating process.
- Heating and melting: Allow the hot plate to heat the parts evenly until the HDPE material reaches its melting point. This will cause the parts to fuse together.
- Cooling and solidification: Once the desired fusion is achieved, remove the parts from the hot plate and allow them to cool and solidify. This will ensure a strong and durable weld.
- Quality check: Inspect the welded joints for any defects or imperfections. Conduct any necessary repairs or adjustments if required.
By following these steps, you will be able to effectively utilize a hot plate welding machine to assemble fuel tanks made of blow-molded HDPE. This welding technique ensures a reliable and long-lasting bond between the various components, resulting in high-quality fuel tanks.
Conclusion
Hot plate welding is a versatile and effective method for fabricating fuel tanks from blow-molded HDPE. With its ability to create strong and reliable welds, hot plate welding offers numerous advantages for fuel tank manufacturers. By carefully considering material selection, design, welding parameters, and quality control, manufacturers can create durable and high-performance fuel tanks that meet the stringent requirements of the industry.
So, if you're in the market for a custom fuel tank, consider the art of hot plate welding. It's a technique that combines precision, strength, and reliability, ensuring that your fuel tank will withstand the test of time. With the right materials, design, and welding expertise, you can have a fuel tank that not only meets your needs but exceeds your expectations.
Remember, safety is paramount when it comes to fuel tanks. Always consult with professionals and adhere to industry standards and regulations to ensure your fuel tank is built to the highest standards.