Hot Plate Welding TPU: A Comprehensive Guide for Strong and Durable Bonds
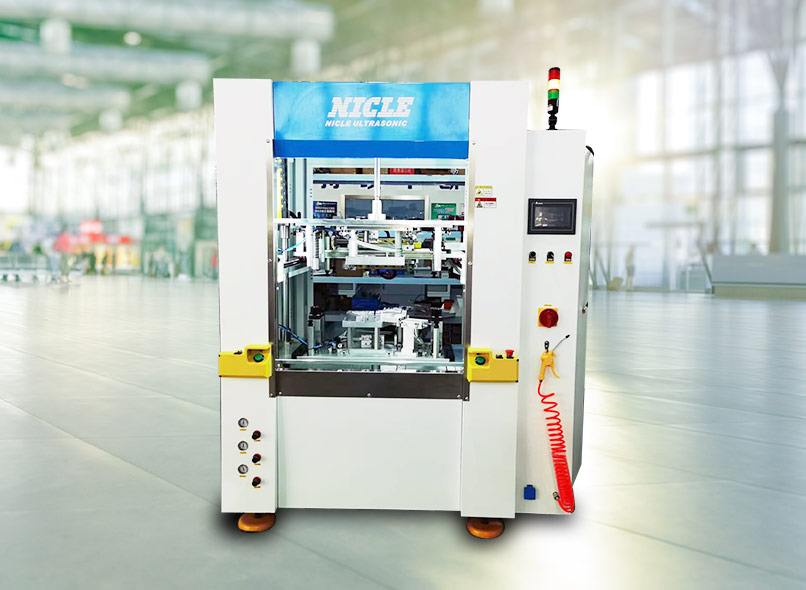
In the world of plastic welding, hot plate welding stands out as a reliable and effective method for joining thermoplastic parts. This technique, also known as heated tool welding, utilizes a heated platen to melt the joining surfaces of two thermoplastic components, creating a permanent and strong bond. In this comprehensive guide, we will explore the process of hot plate welding, its advantages, applications, and other pertinent information related to this technique, with a specific focus on hot plate welding TPU (thermoplastic polyurethane). So, let's dive in!
Understanding Hot Plate Welding
The Process of Hot Plate Welding
Hot plate welding involves several distinct phases that ensure a successful weld. The process starts with the matching phase, where the geometry of the weld surfaces is aligned with the theoretical welding plane. The weld surfaces then come into contact with the heated platen, which is typically maintained at a temperature range of 30 to 100 °C above the melting temperature of the material. This conduction of heat causes the weld surfaces to conform to the desired geometry and removes any surface irregularities that could impact the weld quality.
After the matching phase, the heating phase begins. During this phase, the weld region is heated conductively until it reaches a molten state without substantial displacement of the material. The viscosity of the melted material can be controlled by adjusting the temperature of the hot plate and the heating time. To prevent the molten plastic from sticking to the hot plate, it is often coated with materials like PTFE.
Once the heating phase is complete, the change-over phase follows. In this phase, the parts are retracted from the hot plate, the plate is quickly moved away, and the parts are brought together. This change-over must be swift to prevent excessive cooling of the molten region.
The final phase of hot plate welding is the welding/forging phase. During this phase, the two molten surfaces are pressed together, facilitating intermolecular diffusion of the plastic molecules. This diffusion creates a strong bond through entanglement, resulting in a robust joint. The necessary welding pressure depends on factors such as the melt viscosity, wall thickness of the parts, and typically ranges between 0.025 and 0.05 MPa. This pressure is maintained as the material cools and resolidifies, ensuring the formation of a secure and durable weld.
Advantages of Hot Plate Welding
Hot plate welding offers several advantages that make it a popular choice for joining thermoplastic parts. Firstly, it provides excellent compensation for workpiece fluctuations, allowing for precise and reproducible welding results. The process is versatile and can be used with a wide range of thermoplastics, including TPU. Additionally, hot plate welding is capable of producing strong, airtight welds, making it suitable for applications where leak-proof seals are required.
One of the key advantages of hot plate welding is its ability to join materials with different melting points and melt viscosities. This makes it possible to weld combinations of hard and soft plastics together, expanding the range of applications where this technique can be utilized. Furthermore, hot plate welding is particularly effective for large-area joints or double shells, making it ideal for applications involving larger components.
Applications of Hot Plate Welding
Hot plate welding finds extensive use in various industries and applications. In the automotive industry, hot plate welding is employed for joining components such as ABS tail light housings to PMMA or PC lenses. The strong and durable welds produced by hot plate welding ensure the integrity of these critical components. Additionally, hot plate welding is utilized in the assembly of fuel tanks, battery cases and lids, carburetor floats, coolant and washer fluid reservoirs, and ventilation ducts.
Beyond the automotive industry, hot plate welding is commonly employed in the production of PVC window frames, dishwasher spray arms, medical needle disposal boxes, steam iron reservoirs, PP transport pallets, and HDPE barrels. Its versatility allows it to be used in various manufacturing sectors, where it proves to be a reliable method for joining plastic parts.
Hot Plate Welding TPU: Special Considerations
Welding TPU with Hot Plate Welding
Thermoplastic polyurethane (TPU) is a unique material that requires special considerations when using hot plate welding. TPU is a versatile polymer known for its excellent elasticity, durability, and resistance to abrasion. When welding TPU, it is crucial to select the appropriate temperature range to avoid damaging the material. Typically, temperatures below 500°F are recommended, as higher temperatures can compromise the integrity of TPU.
Hot plate welding TPU involves carefully controlling the temperature and heating time to ensure the material reaches the desired molten state without causing degradation. The use of Teflon-coated platen inserts or Teflon cloth can prevent adhesion between the TPU and the hot plate, allowing for smooth and clean welds. It is essential to ensure the welding parameters are well-calibrated to achieve optimal results when working with TPU.
Advantages of Hot Plate Welding TPU
Hot plate welding provides several advantages when welding TPU. The process allows for the creation of strong and reliable welds in TPU components. The resulting joints exhibit excellent tensile strength, ensuring the integrity of the final product. Moreover, hot plate welding TPU ensures airtight seals, making it suitable for applications requiring leak-proof connections.
TPU's unique properties, such as its high elasticity and flexibility, make it an ideal material for hot plate welding. The process does not compromise TPU's inherent characteristics, allowing the material to retain its elasticity and durability. This makes hot plate welding a preferred method for joining TPU components in various industries, including automotive, footwear, and medical.
Applications of Hot Plate Welding TPU
Hot plate welding TPU finds wide-ranging applications in industries where the material's unique properties are desired. In the automotive sector, TPU is utilized for components such as air ducts, gaskets, and seals. Hot plate welding ensures the secure bonding of TPU parts, providing superior performance and longevity.
The footwear industry also benefits from hot plate welding TPU. TPU is commonly used in shoe soles and other components that require flexibility and durability. Hot plate welding ensures that these TPU parts are securely joined, contributing to the overall quality and longevity of the footwear.
In the medical field, hot plate welding TPU is employed for various applications, including medical device components, wearable medical devices, and surgical equipment. The airtight seals produced by hot plate welding are crucial in maintaining the sterility and functionality of these medical products.
Conclusion
Hot plate welding is a reliable and effective method for joining thermoplastic parts, including TPU. By carefully controlling temperature, pressure, and time, hot plate welding creates strong, durable, and airtight welds. This technique finds extensive use in various industries, including automotive, footwear, and medical, where the integrity of the welds is critical.
When working with TPU, special considerations must be taken to ensure optimal results. By selecting appropriate temperature ranges, utilizing Teflon-coated platen inserts, and calibrating welding parameters, hot plate welding TPU can effectively join TPU components while preserving their unique properties.
Hot plate welding TPU offers numerous advantages, including the ability to produce strong and reliable welds, airtight seals, and compatibility with TPU's elasticity and durability. These advantages make hot plate welding TPU a preferred method for joining TPU components in a wide range of applications.
In conclusion, hot plate welding TPU provides a reliable and versatile solution for joining thermoplastic parts, allowing manufacturers to create durable and high-quality products across various industries. Its ability to produce strong and airtight welds, combined with TPU's unique properties, makes it an ideal choice for applications where the integrity of the weld is paramount.
See more hot plate welding