Hot Plate Welding Tool
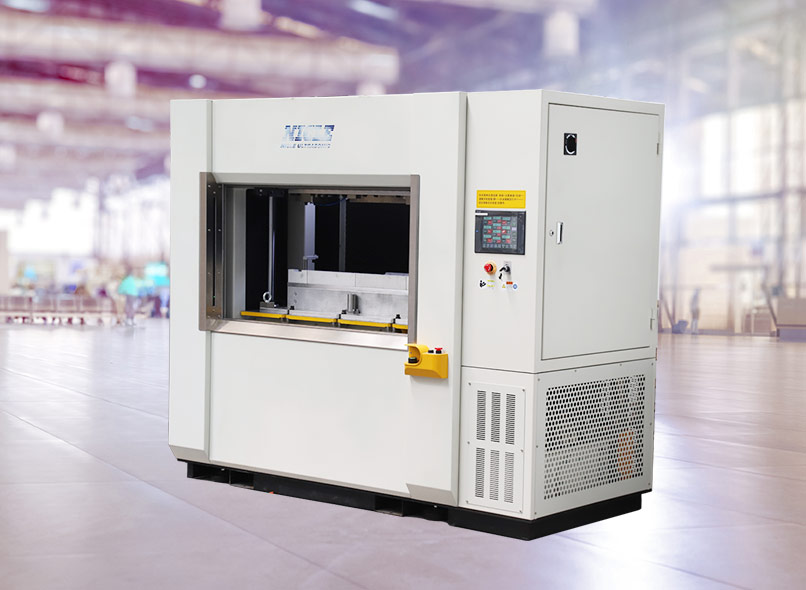
Hot plate welding is a thermal welding technique used to join thermoplastic parts together. It involves the use of a heated platen to melt the joining surfaces of the parts, which are then pressed together to form a strong and durable bond. This process is widely used in various industries due to its ability to produce air-tight and hermetic seals. In this article, we will explore the different aspects of hot plate welding, including its history, process, applications, and advantages.
History of Hot Plate Welding
Hot plate welding has been in use since the early 1930s, primarily for joining PVC materials. However, it gained popularity in the 1960s with the rise of polyolefins, which are difficult to bond using adhesives. Over the years, various welding associations and organizations have developed specifications and guidelines for hot plate welding, including the Deutscher Verband fuer Schweissen (DVS), the American Welding Society (AWS), and the Comité Européen de Normalisation (CEN).
The Hot Plate Welding Process
Hot plate welding involves several distinct phases: matching, heating, changeover, and welding/forging. During the matching phase, the geometry of the weld surfaces is adjusted to the theoretical welding plane. The parts are then brought into contact with the heated tool, and the heat is conducted into the weld surfaces, causing them to soften and melt. After the heating phase, the parts are removed from the heated tool, and the tool is retracted. In the welding/forging phase, the molten surfaces of the parts are pressed together, creating a strong molecular bond. The weld is then allowed to cool and solidify, completing the hot plate welding process.
Advantages of Hot Plate Welding
Hot plate welding offers several advantages over other joining methods. One of the key benefits is its ability to weld large-area plastic parts, including those with complex geometries. It also eliminates the need for consumables such as glues, solvents, and adhesives, making it a cost-effective and environmentally friendly option. The process allows for the creation of hermetic seals and uniform weld flashes. Additionally, hot plate welding provides excellent compensation for workpiece variations, ensuring consistent and reproducible welds.
Applications of Hot Plate Welding
Hot plate welding is commonly used in a wide range of industries for various applications. In the automotive industry, it is used to weld ABS tail light housings to lenses made of PMMA or PC. It is also employed in the assembly of fuel tanks, battery cases and lids, coolant and washer fluid reservoirs, and ventilation ducts. Other applications include the assembly of PVC window frames, dishwasher spray arms, medical needle disposal boxes, steam iron reservoirs, PP transport pallets, and HDPE barrels. The flexibility of hot plate welding allows for the joining of different thermoplastics and the welding of combinations of hard and soft plastics.
Hot Plate Welding Equipment
To perform hot plate welding, specialized equipment is required. Companies like Extol offer a range of hot plate welding machines, including configurable standard hot plate welders and custom solutions. These machines feature servo-driven platens for precise force, velocity, and displacement control, ensuring consistent melt and seal profiles. The Rapid Conductor model, for example, is known for its fast platen motion and short cycle times. It is equipped with three servo-driven platens that deliver accurate velocity, force, and displacement control. The Compact Fusion model, on the other hand, is a smaller benchtop configuration ideal for smaller assemblies and limited-space environments.
Factors Affecting Hot Plate Welding
Several factors can affect the success of hot plate welding. Temperature, melt time, transition time, weld/seal time, melt depth, weld/seal depth, melt force, and weld/seal force are critical parameters that must be carefully controlled. The temperature of the heated platen should be set according to the melting temperature of the material being welded. The pressure applied during the welding process must be sufficient to ensure a strong molecular bond but not excessive to avoid deformation of the parts. The duration of the heating, changeover, and welding phases must also be optimized to achieve the desired weld quality.
Hot Plate Welding Techniques
Hot plate welding can be performed using different techniques depending on the specific requirements of the application. Conventional hot plate welding, high-temperature hot plate welding, and non-contact hot plate welding are some of the common variants. Conventional hot plate welding is the most widely used technique, while high-temperature hot plate welding allows for shorter cycle times. Non-contact hot plate welding, although less commonly used, offers the advantage of no residue on the platen and no material discoloration.
Material Considerations in Hot Plate Welding
Hot plate welding is suitable for almost any thermoplastic material, with particular suitability for softer, semi-crystalline thermoplastics like PP and PE. The welding parameters must be adjusted according to the specific material properties to achieve optimal results. Dissimilar materials can also be hot plate welded if they have similar melting points and melt viscosities. However, it is essential to ensure that the materials are chemically compatible to avoid any undesired reactions.
Conclusion
Hot plate welding is a versatile and reliable method for joining thermoplastic parts. Its ability to create strong and air-tight welds makes it a preferred choice in various industries. With precise process controls and the right equipment, hot plate welding can produce high-quality welds with excellent reproducibility. Whether it's in automotive, construction, or other manufacturing sectors, hot plate welding offers a cost-effective and environmentally friendly solution for creating durable and reliable plastic assemblies.
See more hot plate welding applications