Hot Plate Welding Machines: Revolutionizing Headlights Welding
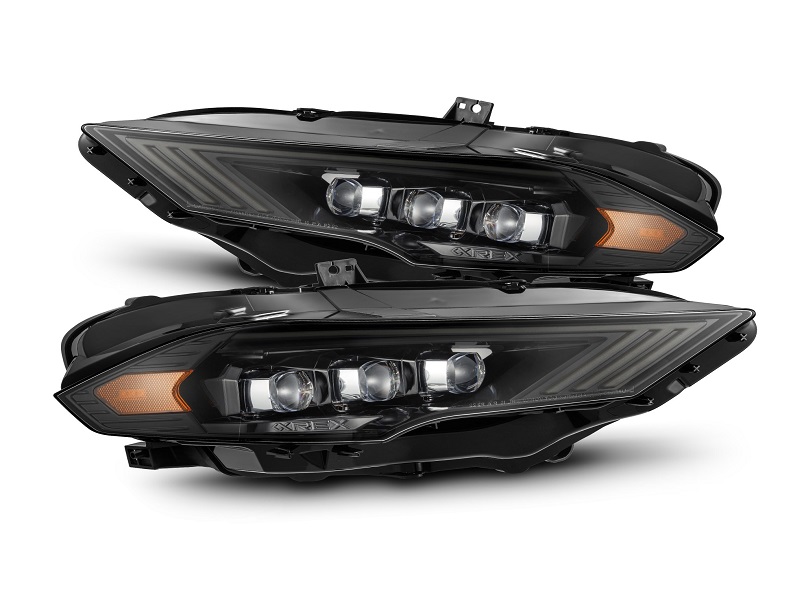
In the automotive industry, the process of joining plastic parts is of utmost importance, especially when it comes to headlights. The quality and durability of these components directly impact the safety and performance of vehicles. This is where hot plate welding machines come into play. These machines have revolutionized the process of headlights welding, providing strong, leak-tight joints in plastic assemblies with complex geometries. In this article, we will delve into the intricacies of hot plate welding machines and their role in ensuring high-quality headlights.
Understanding Hot Plate Welding
Hot plate welding is a versatile method for joining plastic parts, offering a range of benefits that set it apart from other welding techniques like ultrasonic welding and vibration welding. One of the key advantages of hot plate welding is its ability to weld both small and large parts, as well as flat and contoured ones. This makes it an ideal solution for assembling headlights, taillights, ductwork, manifolds, batteries, fuel tanks, filter housings, and coolant and fluid reservoirs in the automotive industry.
The Hot Plate Welding Process
The hot plate welding process involves several steps to ensure a strong and durable bond between the plastic parts. First, the two halves of the assembly are loaded into custom-made fixtures, which can be vertically or horizontally oriented, depending on the application. These fixtures are connected to linear slides powered by pneumatic cylinders, hydraulic cylinders, or servo-driven ballscrews, allowing precise control over welding force, speed, and displacement.
Once the parts are loaded, a heated platen moves in between the fixtures, pressing the parts against it for a set time. The heat from the platen melts a small portion of plastic around the edge of each part, creating a molten state that allows for fusion. Mechanical stops built into the fixtures and platen prevent excessive material melting. After the plastic has melted, the fixtures move apart, the platen withdraws, and the fixtures travel toward each other again. This step ensures that the melted edges fuse together as the plastic cools. Finally, the fixtures separate, and the assembly is unloaded.
Importance of Temperature Control
Temperature control is crucial in hot plate welding to achieve optimal results. The platen, typically made of aluminum, P20 mold steel, or aluminum-bronze, is heated using electric cartridges. Engineers can control the temperature in individual zones, allowing different parts of the assembly to receive varying amounts of heat. The choice of material for the platen depends on the application, with aluminum used for low-temperature applications and steel for high-temperature ones. Aluminum-bronze, on the other hand, offers faster heat recovery and is often preferred for high-volume applications.
Welding Contoured Parts
Contoured parts, such as the clear plastic covers for headlights, require special attention during the hot plate welding process. To weld these parts effectively, blocks of aluminum or steel, machined to match the shape of the parts, are attached to each side of the platen. The use of a nonstick coating, such as Teflon or chrome, on the tooling helps prevent the melted plastic from sticking. Maintaining consistent temperature across the entire contoured surface is crucial to ensure a seamless weld.
Parameters of Hot Plate Welding
Several parameters influence the hot plate welding process, including platen temperature, heating time, transition time, joining pressure, and holding time. The platen temperature typically ranges from 150 to 650°F, while heating time varies depending on the application, with amorphous materials melting faster than engineering-grade polymers. The pressure applied to the heated parts is minimal, ranging from 14 to 150 psi, and must be carefully controlled to avoid squeezing out excessive molten plastic and weakening the weld.
Advantages of Hot Plate Welding
Hot plate welding offers numerous advantages over other joining methods, making it a preferred choice for headlights welding. Some of these advantages include:
- Strong and leak-tight joints: Hot plate welding produces robust, leak-tight joints, ensuring the durability and integrity of the assembled headlights.
- Versatility: This welding technique is highly versatile and can be used to join a wide range of plastic parts, regardless of their size, shape, or complexity.
- Compatibility with different materials: Hot plate welding can be used with various thermoplastic materials, such as PP and PE, offering flexibility in material selection for headlights manufacturing.
- High-quality welds: The controlled heating and precise pressure application in hot plate welding result in high-quality welds with excellent sealing properties and mechanical strength.
- Cost-effective and efficient: Hot plate welding is a cost-effective and efficient solution for large-scale plastic welding, providing strong support to the manufacturing industry.
Conclusion
Hot plate welding machines have revolutionized the process of headlights welding in the automotive industry. With their ability to produce strong, leak-tight joints in plastic assemblies with complex geometries, these machines ensure the durability and performance of vehicle headlights. By understanding the hot plate welding process, the importance of temperature control, and the parameters that influence the quality of the welds, manufacturers can optimize their manufacturing processes and deliver headlights of the highest quality. With its versatility, compatibility with different materials, and cost-effectiveness, hot plate welding is a game-changer in the field of plastic assembly, providing reliable and efficient solutions for the automotive industry.