The Ultimate Guide to Using Hot Plate Welding Machines for Glove Boxes
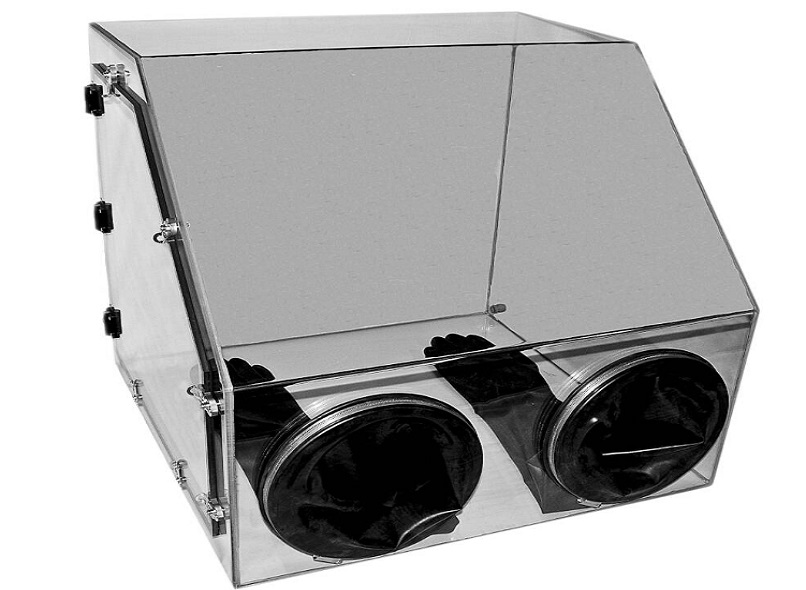
Hot plate welding is a widely used technique for joining thermoplastic parts, especially for large-area applications like glove boxes. This process involves heating the welding areas of the components through contact or radiant heat and then joining them under pressure. In this comprehensive guide, we will explore the various aspects of using hot plate welding machines for glove boxes, including the process, machine specifications, materials compatibility, safety features, ease of use and maintenance, and more.
Process Overview
Hot plate welding is also known as heat contact welding or mirror welding due to its functional principle. The process can be divided into several stages, starting with the plasticization of the joining surfaces using a mobile heating mirror. Once the surfaces are heated and softened, the mirror moves out of the joining area, and the melted surfaces are pressed together. The entire process involves three main steps: heating, positioning, and joining. Hot plate welding allows for excellent compensation of workpiece variations and produces reproducible and concealable welded joints with high strength.
Machine Specifications
When selecting a hot plate welding machine for glove boxes, it is important to consider the machine's specifications to ensure it meets your specific requirements. Some key specifications to consider include:
- Temperature Range: The machine should be capable of reaching temperatures suitable for your welding application. Standard machines typically offer a temperature range of 180°C to 350°C, but higher temperature options may be available for specialized applications.
- Machine Size: Choose a machine size that can accommodate the dimensions of your glove box components. Standard machines are available in various sizes, ensuring flexibility for different welding needs.
- Heating Element: The machine's heating element should provide uniform temperature distribution across the workspace. High-strength materials like aluminum, aluminum bronze, or steel are commonly used for hot plates.
- Cycle Time: Consider the cycle time of the machine, as shorter cycle times can increase productivity. Advanced drive technology and optimized programming can help minimize cycle times.
Materials Compatibility
Hot plate welding is compatible with a wide range of thermoplastic materials, making it suitable for various glove box applications. Commonly used materials include ABS, PP, POM, PC/ABS, PET, PES, PMMA, PPO, PSU, PVC, SAN, and PET. However, it is important to ensure that the hot plate welding machine is compatible with the specific materials you intend to weld. Different plastics may require different temperatures and heating times for successful welding.
Safety Features
Safety is a crucial consideration when operating any industrial machinery, including hot plate welding machines. Look for machines that come equipped with essential safety features such as:
- Emergency Stop Buttons: These buttons allow operators to quickly halt the machine's operation in case of emergencies.
- Protective Enclosures: Machines with protective enclosures provide an added layer of safety by preventing accidental contact with hot surfaces or moving parts.
- Overheat Protection: Machines should have built-in mechanisms to prevent overheating, ensuring safe and reliable operation.
Ease of Use and Maintenance
Choosing a hot plate welding machine that is user-friendly and easy to maintain can significantly impact productivity. Consider the following factors:
- Intuitive Operation: Look for machines that provide clear instructions and are easy to operate. Intuitive controls and user-friendly interfaces can help reduce the learning curve for operators.
- Maintenance Requirements: Inquire about the machine's maintenance needs, including cleaning procedures and the availability of replacement parts. Regular maintenance ensures optimal performance and extends the machine's lifespan.
Warranty and Support
Verify the warranty provided by the manufacturer and ensure it covers potential issues that may arise during the machine's initial operation. Additionally, inquire about technical support and the availability of spare parts. Reliable customer support can be invaluable in case of troubleshooting or repairs.
Cost and Budget
While budget is an important consideration, prioritize the quality and capabilities of the hot plate welding machine. Investing in a higher-quality machine may result in long-term cost savings by reducing downtime and repair costs. Compare prices from different manufacturers to ensure you are getting the best value for your investment.
Training and Documentation
Ask the manufacturer about training options and documentation provided. Adequate training can help operators effectively and safely use the machine. Detailed manuals and documentation can serve as valuable references for troubleshooting and maintenance.
Conclusion
Hot plate welding machines are essential tools for joining thermoplastic parts in glove box applications. By considering factors such as machine specifications, materials compatibility, safety features, ease of use and maintenance, warranty and support, cost and budget, and training and documentation, you can make an informed decision when selecting a hot plate welding machine for your glove box welding needs. Choose a machine that aligns with your specific requirements and enjoy efficient and reliable plastic welding processes. Invest in a high-quality machine, prioritize safety, and ensure proper training for operators to achieve successful hot plate welding operations.
Additional Information: The process of hot plate welding involves heating the joining surfaces of the plastic parts to be welded using a heated heating element. This process is commonly used in industries such as automotive, energy, pharmaceuticals, and heavy industry. The hot plate welding machines offered by various manufacturers, including FRIMO, are designed to meet specific application needs and offer features such as rapid tool change systems, automated solutions, and modular systems for optimal flexibility and productivity.