The Ultimate Guide to Hot Plate Welding Machines for Circuit Board Welding
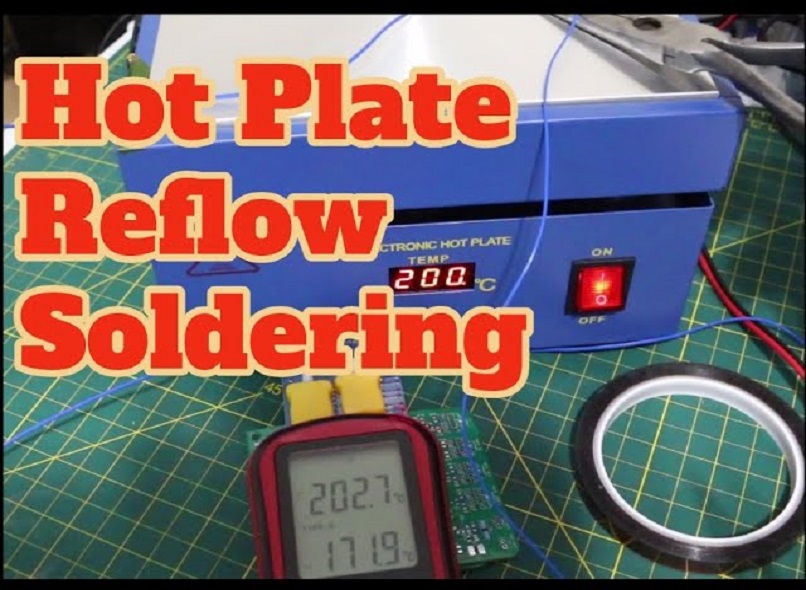
In the fast-paced world of electronics manufacturing, the welding process plays a crucial role in connecting electronic components to printed circuit boards (PCBs). One of the most effective methods for PCB welding is hot plate welding. This innovative technique uses a heated platen to melt and soften the joint interface, creating a clean and durable bond between the components and the PCB. In this comprehensive guide, we will explore the intricacies of hot plate welding machines and their application in circuit board welding. From understanding the process to choosing the right equipment, we will provide you with all the information you need to master hot plate welding and achieve flawless PCB assemblies.
Section 1: What is Hot Plate Welding?
Hot plate welding is a joining solution that enables the welding together of virtually any shaped part, including those with contoured parting lines, internal walls, and free-standing walls. This versatile process offers several advantages, such as the ability to weld difficult geometries and the elimination of consumables like glues, solvents, and adhesives.
Subsection 1.1: The Hot Plate Welding Process
Hot plate welding utilizes a heated platen with heat inserts that are cut to match the shape of the weld plane. The plastic parts that will be joined are pressed against the heated plate, causing them to melt and soften along the entire joint interface. Once the plastic parts reach the desired temperature, they are immediately pressed together to complete the weld. This direct thermal contact process ensures a clean and strong bond between the components and the PCB.
Subsection 1.2: Applications of Hot Plate Welding
Hot plate welding is frequently chosen for applications where hermetic seals, uniform weld flash, or multiple parts per cycle are required. The flexibility of this process permits a wide latitude in designing parts. It finds applications in various industries, including automotive, appliance manufacturing, hardware, and medical devices. In the automotive industry, hot plate welding is used to assemble headlights, taillights, ductwork, manifolds, batteries, fuel tanks, filter housings, and coolant and fluid reservoirs. Appliance manufacturers utilize hot plate welding to assemble spray arms for dishwashers, agitators and balance rings for washing machines, brushes for vacuum cleaners, and reservoirs for steam irons. Even the hardware industry benefits from hot plate welding, employing it to weld window and door frames. Medical device manufacturers use hot plate welding to assemble sharps containers and foot massagers. This versatile process can even be used to create large assemblies, such as barrels, pallets, and crates.
Section 2: Advantages of Hot Plate Welding Machines for Circuit Board Welding
Hot plate welding machines offer several advantages for circuit board welding, making them a preferred choice for many electronic manufacturers.
Subsection 2.1: Precise Control and Process Data Acquisition
One of the key advantages of hot plate welding machines is the precise control they offer over tooling position, velocity, force, and acceleration. This level of control ensures accurate and consistent welding results, leading to high-quality PCB assemblies. Additionally, modern hot plate welding machines are equipped with advanced data acquisition capabilities, enabling comprehensive process monitoring and analysis. Engineers can gather valuable data on parameters such as temperature, pressure, and displacement, facilitating process optimization and quality control.
Subsection 2.2: Flexibility in Design
Hot plate welding machines provide great flexibility in designing circuit boards. The direct thermal contact process allows for the welding of complex geometries and the joining of parts with contoured parting lines, internal walls, and free-standing walls. This versatility opens up new possibilities in PCB design, enabling engineers to create innovative and efficient electronic products.
Subsection 2.3: Clean and Strong Welds
Hot plate welding machines produce clean and strong welds, ensuring reliable connections between electronic components and PCBs. The direct thermal contact process allows for the complete melting and softening of the joint interface, resulting in a tight and durable bond. The absence of adhesives or consumables eliminates the risk of weak welds or contaminants, enhancing the overall quality and longevity of the PCB assembly.
Subsection 2.4: Cost-Effectiveness
Hot plate welding machines offer cost-effective solutions for circuit board welding. The elimination of consumables, such as glues, solvents, and adhesives, reduces material costs and simplifies the production process. Additionally, the precise control and process data acquisition capabilities of hot plate welding machines contribute to process optimization, reducing waste and improving overall operational efficiency.
Section 3: How to Choose the Right Hot Plate Welding Machine for Circuit Board Welding
Choosing the right hot plate welding machine is crucial for achieving successful circuit board welding. Several factors should be considered when selecting a machine for your specific needs.
Subsection 3.1: Welding Capacity and Size
The welding capacity and size of the hot plate welding machine should align with your circuit board welding requirements. Consider the size and quantity of the PCBs you will be working with, as well as the complexity of the welds. Ensure that the machine can accommodate the desired welding area and has sufficient heating capacity to meet your production demands.
Subsection 3.2: Temperature Control and Precision
Temperature control is a critical factor in hot plate welding. Look for a machine that offers precise temperature control and stability. The ability to accurately set and maintain the desired temperature ensures consistent and high-quality welds. Consider machines with advanced temperature control features, such as digital controllers and thermocouple sensors, to achieve optimal results.
Subsection 3.3: Heating Element and Material Compatibility
The heating element of the hot plate welding machine should be compatible with the materials used in your circuit boards. Different materials have varying melting points and thermal properties, so ensure that the machine can heat the platen to the required temperature for your specific application. Additionally, consider the material compatibility of the machine itself, ensuring that it can withstand the heat and pressure of the welding process.
Subsection 3.4: Automation and Control Options
Automation and control options are important considerations, especially for high-volume production. Look for hot plate welding machines that offer automation features, such as automatic cycle start and digital controllers. These features can streamline the welding process, improve efficiency, and reduce the risk of human error. Additionally, consider machines with data acquisition capabilities, allowing for real-time monitoring and analysis of process parameters.
Subsection 3.5: Safety Features
Safety should always be a top priority when working with hot plate welding machines. Look for machines that have built-in safety features, such as temperature sensors, emergency stop buttons, and safety interlocks. These features help prevent accidents and protect both operators and the equipment.
Section 4: Conclusion
Hot plate welding machines have revolutionized circuit board welding, offering precise control, flexibility, and cost-effectiveness. By leveraging the advantages of hot plate welding machines, electronic manufacturers can achieve flawless PCB assemblies with clean and strong welds. When choosing a hot plate welding machine, consider factors such as welding capacity, temperature control, material compatibility, automation options, and safety features. With the right machine and a comprehensive understanding of the hot plate welding process, you can ensure the success of your circuit board welding projects and deliver high-quality electronic products to your customers.