Hot Plate Welding Machine for Pallet: A Comprehensive Guide
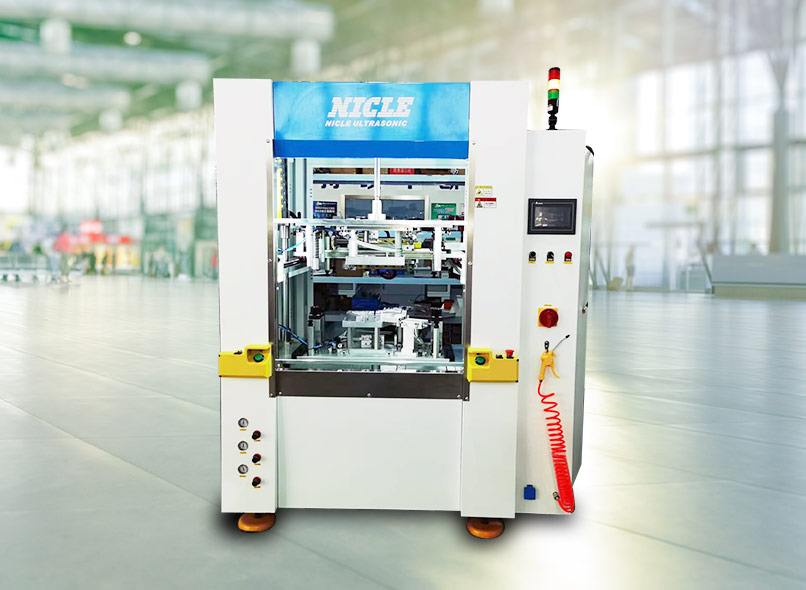
In today's fast-paced manufacturing industry, efficiency and precision are key factors for success. When it comes to joining plastic pallets, hot plate welding machines have emerged as a reliable and efficient solution. These machines utilize advanced technology to connect plastic components without damaging the surrounding material. In this comprehensive guide, we will explore the various aspects of hot plate welding machines for pallets, including their features, applications, and benefits.
Section 1: Understanding Hot Plate Welding
Hot plate welding is a thermal joining process that utilizes a temperature-controlled heat platen assembly. This assembly is inserted between two plastic parts to be joined. As the heat platen reaches the desired temperature, the plastic material softens, allowing for the fusion of the two parts. The process involves precise control of temperature, pressure, and cooling time to ensure a strong and durable weld.
Subsection 1.1: Advantages of Hot Plate Welding
Hot plate welding offers several advantages over other joining methods, making it a preferred choice for pallet manufacturing. Some key advantages include:
- Seamless and strong welds: Hot plate welding creates weld seams that are smooth and free from defects, ensuring the integrity and strength of the pallets.
- Versatility in material compatibility: Hot plate welding can join a wide range of plastic materials, including modified PP, HDPE, PE, and more. This versatility allows for flexibility in pallet design and application.
- Increased productivity: With automated hot plate welding machines, manufacturers can achieve high production rates, reducing manual labor and increasing overall productivity.
- Cost-effective: Hot plate welding eliminates the need for additional fasteners or adhesives, reducing material costs and simplifying the assembly process.
- Environmental-friendly: As hot plate welding does not require additional materials or consumables, it minimizes waste and contributes to a greener manufacturing process.
Subsection 1.2: Hot Plate Welding Process
The hot plate welding process involves several steps to ensure a successful weld. Here is a step-by-step overview of the process:
- Preparation: The two plastic parts to be joined are positioned in the holding fixtures of the hot plate welding machine.
- Heating: The heat platen, controlled by the machine's heating system, reaches the desired temperature for softening the plastic material.
- Contact: The heat platen moves between the two plastic parts, bringing them into contact with the heated surface.
- Fusion: The plastic material softens upon contact with the heat platen, allowing for fusion between the two parts.
- Welding Pressure: Holding fixtures apply pressure to ensure proper contact and fusion between the plastic parts.
- Cooling: After the desired welding time, the heat platen retracts, and the welded parts begin to cool and solidify, forming a strong bond.
- Completion: Once the cooling process is complete, the holding fixtures release the welded part, ready for further processing or use.
Section 2: Features of Hot Plate Welding Machines for Pallets
Hot plate welding machines for pallets come with various features that ensure optimal performance and precise control over the welding process. Let's explore some of the key features:
Subsection 2.1: Massive Ultra-Rigid Construction
To withstand the demands of continuous use, hot plate welding machines feature a robust tubular steel framework with leveling feet. This construction provides stability and precise tool alignment, ensuring consistent weld quality over extended periods.
Subsection 2.2: Hydraulic System with Proportional Valve Control
The hydraulic system in hot plate welding machines is equipped with a proportional valve control and linear position transducers. This setup allows for improved control and reduced machine and coating wear. Users can program variable tool mounting jaws, heat platen carriage pressures, and speeds, enhancing overall welding control and precision.
Subsection 2.3: Dual Heat Platen Halves with Servo-Electric Motion Control
Hot plate welding machines utilize dual heat platen halves with servo-electric motion control. This design enhances weld strength by increasing the speed of heat platen motion, minimizing open time between the melting and welding steps. Reduced open time ensures superior weld quality by preventing partial solidification or skin-over of the molten surfaces before contact.
Subsection 2.4: Digital Four-Zone Temperature Control via PLC
Precise temperature control is crucial in hot plate welding. Machines equipped with digital four-zone temperature control via a PLC (Programmable Logic Controller) ensure even heating and precise temperature control. Additionally, a heater burnout alarm feature halts machine operation in case of platen heater failure, preventing potential quality issues.
Subsection 2.5: Programmable Automatic Machine and Heat Platen Startup
Hot plate welding machines are designed for efficiency and convenience. The programmable automatic machine and heat platen startup feature allows users to program warm-up sequences for the heat platen and hydraulic system. This eliminates the need for manual warm-up and saves valuable production time.
Subsection 2.6: Allen Bradley CompactLogix PLC with PanelView Plus 7
The integration of an Allen Bradley CompactLogix PLC with a PanelView Plus 7 enhances the user interface experience. It simplifies parameter input and provides a graphical display for easy monitoring and adjustment of various welding parameters, such as pressure, speed, temperature, and alarms.
Subsection 2.7: Multi-Level Passcode Protection
Hot plate welding machines prioritize safety and security. Multi-level passcode protection limits parameter adjustment to qualified personnel, ensuring that only authorized individuals can modify critical welding settings. This feature reduces the risk of unauthorized changes and ensures consistent weld quality.
Subsection 2.8: Vent Hood with Exhaust Fan
Welding at high temperatures can generate smoke and particulate matter. Hot plate welding machines are equipped with a vent hood and exhaust fan system to evacuate airborne smoke and particulate, providing a clean and safe working environment for operators.
Section 3: Applications of Hot Plate Welding Machines for Pallets
Hot plate welding machines are widely used in various industries for welding plastic pallets. Some common applications include:
Subsection 3.1: Automotive Industry
In the automotive industry, hot plate welding machines are used to join plastic car body components, car doors, automotive instruments, car lights, bumpers, filters, and more. The precise and strong welds achieved through hot plate welding ensure the integrity and durability of these critical components.
Subsection 3.2: Electronics Industry
Hot plate welding machines play a vital role in the electronics industry, where they are used to join plastic parts of communication equipment, cordless phones, phone accessories, phone shells, battery cases, chargers, USB flash drives, memory cards, and more. The high precision and reliability of hot plate welding ensure the longevity and performance of electronic devices.
Subsection 3.3: Packaging Industry
In the packaging industry, hot plate welding machines are utilized to weld plastic trays, folders, albums, PP hollow plates, pen rings, ink cartridges, and other packaging materials. The seamless and strong welds achieved through hot plate welding enhance the structural integrity and visual appeal of packaging products.
Subsection 3.4: Household Appliances
Hot plate welding machines are employed in the production of various household appliances, including kitchen tools, safety helmets, cosmetics bottles, coffee kettles, cloth washing machines, air humidifiers, electric irons, vacuum cleaners, and more. The precise and reliable welds ensure the functionality and durability of these appliances.
Subsection 3.5: Medical Industry
Hot plate welding machines find applications in the medical industry, where they are used to join plastic parts of medical devices, watches, liquid bottles, air mattresses, clothing hangers, gardening supplies, shower nozzles, and more. The sterile and strong welds achieved through hot plate welding meet the rigorous standards of the medical industry.
Section 4: Choosing the Right Hot Plate Welding Machine for Pallets
Selecting the right hot plate welding machine for pallets is crucial for achieving optimal results. Here are some factors to consider when making your decision:
Subsection 4.1: Welding Capacity
Evaluate the welding capacity of the machine, including the maximum size of pallets it can accommodate and the range of plastic materials it can weld. Ensure that the machine meets your specific requirements and production needs.
Subsection 4.2: Automation and Control
Consider the level of automation and control offered by the machine. Look for features such as programmable settings, digital displays, and user-friendly interfaces that enhance ease of use and precision.
Subsection 4.3: Safety Features
Prioritize machines that offer safety features such as passcode protection, alarms, and interlocks to ensure operator safety and prevent any potential accidents.
Subsection 4.4: After-Sales Support and Service
Choose a reputable manufacturer or supplier that provides comprehensive after-sales support, including technical assistance, maintenance services, and spare parts availability. This ensures the longevity and reliability of your hot plate welding machine.
Conclusion
Hot plate welding machines have revolutionized the process of joining plastic pallets. Their advanced features, precise control, and versatility make them an indispensable tool in various industries. Whether in the automotive, electronics, packaging, household appliances, or medical industry, hot plate welding machines offer seamless and strong welds that ensure the integrity and durability of plastic pallets. By choosing the right machine and considering factors such as welding capacity, automation, safety, and after-sales support, manufacturers can optimize their production processes and achieve superior weld quality. Invest in a hot plate welding machine for pallets and experience the efficiency, reliability, and precision it brings to your manufacturing operations.
See more hot plate welding machine