Hot Plate Welding Machine for Clean Air Pipe Welding: A Comprehensive Guide
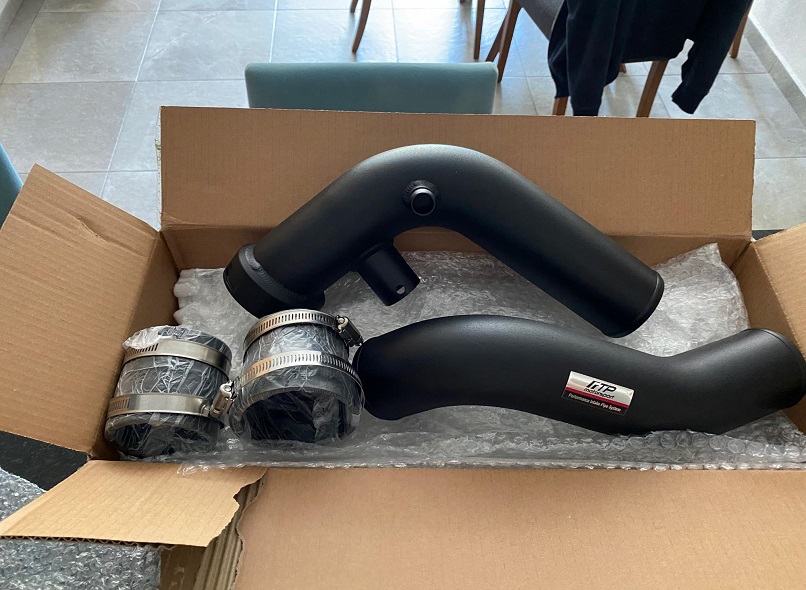
In the world of plastic welding, hot plate welding stands out as a versatile and reliable technique. It is particularly well-suited for joining thermoplastic parts, including clean air pipes. In this comprehensive guide, we will explore the process and benefits of using a hot plate welding machine for clean air pipe welding. We will delve into the technical details, applications, and advantages of this technique, providing you with the knowledge you need to make informed decisions about your welding projects.
Understanding Hot Plate Welding
Hot plate welding, also known as mirror welding, is a thermal welding technique used to join thermoplastic parts. It involves heating the joining surfaces of the parts to their melting temperature using a heated platen or mirror. Once the surfaces are molten, the parts are brought together and held under pressure until they fuse into a single, strong piece. This process ensures airtight and reliable welds.
Hot plate welding is highly versatile, allowing for the joining of both small and large parts, flat or contoured surfaces, and even combinations of hard and soft plastics. It excels in applications where other welding methods, such as ultrasonic welding or vibration welding, may not be suitable. Its ability to create strong, hermetically sealed joints makes it a preferred choice for critical applications like clean air pipe welding.
The Hot Plate Welding Process
The hot plate welding process can be broken down into six essential steps:
Step 1: Preparation and Fixturing
Before starting the welding process, proper preparation and fixturing are crucial. The parts to be welded are securely loaded into custom-made fixtures, ensuring precise alignment and support throughout the welding process. Fixturing plays a vital role in achieving accurate and repeatable welds.
Step 2: Heating the Joining Surfaces
A heated platen or mirror is positioned between the two parts to be welded. The fixtures close, compressing and melting the joining surfaces against the platen. Material displacement occurs only at the joint area, ensuring minimal waste and precise control over the welding process.
Step 3: Compression and Material Displacement
Compression and material displacement continue until precision hard-stops in the fixturing are met. Even after compression and displacement have stopped, thermal heat continues to conduct into the material, ensuring thorough melting and optimal weld strength.
Step 4: Reaching Molten Temperature
Once the joint area reaches the molten temperature required for welding, the fixtures open, and the heat platen is withdrawn from between the parts. At this stage, the surfaces are in a molten state, ready to be joined.
Step 5: Joining the Parts
The fixtures close again, forcing the two parts together until the hard-stops on the fixtures come into contact with each other. This ensures a proper fusion of the molten surfaces and creates a strong and airtight bond.
Step 6: Cooling and Finishing
After the welding process is complete, the parts are allowed to cool and solidify. Once cooled, the gripping mechanism in one of the fixtures releases the part, and the finished welded assembly can be removed.
Advantages of Hot Plate Welding for Clean Air Pipe Welding
Hot plate welding offers numerous advantages for clean air pipe welding, making it a preferred method in various industries. Let's explore some of the key benefits:
1. Strong and Airtight Welds
Hot plate welding creates robust and airtight welds, ensuring the integrity of clean air pipe systems. The fusion of the molten surfaces results in a seamless joint that can withstand high pressures and maintain leak-free operations.
2. Versatility in Pipe Sizes and Shapes
Clean air pipes come in various sizes and shapes, and hot plate welding can accommodate them all. Whether you are working with small or large diameter pipes, flat or contoured surfaces, hot plate welding provides the flexibility to join them effectively.
3. Excellent Compatibility with Thermoplastic Materials
Hot plate welding works well with a wide range of thermoplastic materials commonly used in clean air pipe systems. From polyethylene to polypropylene and beyond, this welding technique ensures compatibility and strong bonds between different thermoplastics.
4. Precise Alignment and Reproducibility
The use of custom-made fixtures in hot plate welding ensures precise alignment and reproducibility in clean air pipe welding. The fixtures securely hold the parts, maintaining accurate positioning throughout the welding process, resulting in consistent and high-quality welds.
5. Suitable for High-Volume Production
Hot plate welding machines can be easily integrated into automated production lines, making it an ideal choice for high-volume clean air pipe manufacturing. With automated loading, welding, and unloading, the process becomes efficient, cost-effective, and consistent.
6. Compatibility with Quality Control Measures
Hot plate welding allows for the implementation of quality control measures to ensure the reliability of clean air pipe welds. Non-destructive testing techniques, such as visual inspection, pressure testing, and leak testing, can be easily applied to verify the integrity of the welded joints.
Applications of Hot Plate Welding in Clean Air Pipe Welding
Hot plate welding finds extensive use in various industries for clean air pipe welding applications. Some common applications include:
1. HVAC Systems
Hot plate welding is widely employed in the assembly of HVAC systems, including ductwork, air vents, and air filtration components. It ensures secure and leak-free connections, enhancing the overall efficiency and performance of the system.
2. Industrial Ventilation
Clean air pipe systems play a crucial role in industrial ventilation, ensuring clean and safe working environments. Hot plate welding enables the construction of strong and airtight pipe assemblies, critical for maintaining proper ventilation and air quality in industrial settings.
3. Cleanrooms and Laboratories
Cleanrooms and laboratories require precise control over air quality. Hot plate welding is often used to fabricate clean air pipe systems in these environments to ensure the integrity of the air supply. The strong and reliable welds created by hot plate welding guarantee the absence of leaks or contaminants in critical areas.
4. Pharmaceutical and Biotechnology Industries
In pharmaceutical and biotechnology industries, clean air pipe systems are essential for maintaining sterile environments. Hot plate welding ensures the integrity of these systems, preventing any contamination or compromise in sterile conditions.
5. Food and Beverage Processing
Clean air pipe systems play a vital role in food and beverage processing, ensuring safe and hygienic production environments. Hot plate welding ensures that the pipe connections are secure, leak-free, and compliant with food safety regulations.
6. Semiconductor Manufacturing
Semiconductor manufacturing requires stringent control over air quality to prevent contamination. Hot plate welding is commonly used to fabricate clean air pipe systems in semiconductor cleanrooms, ensuring the integrity of the air supply and minimizing the risk of particle contamination.
Choosing the Right Hot Plate Welding Machine
Selecting the right hot plate welding machine is crucial for achieving optimal results in clean air pipe welding. Here are some factors to consider:
1. Machine Configuration
Hot plate welding machines come in various configurations, including vertical and horizontal platens. Vertical machines are suitable for manually loaded part halves, ensuring precise alignment during welding. On the other hand, horizontal machines are ideal for loose internal components and allow for easier automation.
2. Temperature Control and Monitoring
Temperature control and monitoring are critical for achieving consistent and reliable welds. Look for a hot plate welding machine with precise temperature control capabilities, ensuring accurate heating of the joining surfaces. Some advanced machines offer temperature monitoring and control for enhanced process control.
3. Welding Parameters
Consider the welding parameters offered by the machine, such as temperature range, heating time, and welding pressure. These parameters should align with the requirements of your clean air pipe welding application. Ensure that the machine provides flexibility in adjusting these parameters to accommodate different thermoplastic materials and pipe sizes.
4. Automation Capabilities
If you are working on high-volume production, automation capabilities can significantly enhance productivity and efficiency. Look for a hot plate welding machine that offers options for automated loading and unloading, as well as seamless integration into existing production lines.
5. Quality Control Features
Quality control is essential in clean air pipe welding. Look for machines that offer built-in quality control features, such as process monitoring, data recording, and the ability to perform non-destructive testing. These features ensure the integrity and reliability of the welded joints.
6. Service and Support
When investing in a hot plate welding machine, consider the reputation of the manufacturer and their after-sales service and support. Look for a company that provides comprehensive training, technical assistance, and readily available spare parts to ensure smooth operations and long-term reliability.
Conclusion
Hot plate welding machines offer an effective and reliable solution for clean air pipe welding. With their ability to create strong and airtight welds, precise alignment, and compatibility with a wide range of thermoplastic materials, hot plate welding machines ensure the integrity and performance of clean air pipe systems. By choosing the right machine and implementing proper quality control measures, you can achieve consistent and high-quality welds, ensuring safe and hygienic environments in various industries.