Hot Plate Welding for Automotive Components Ventilation Ducts: A Comprehensive Guide
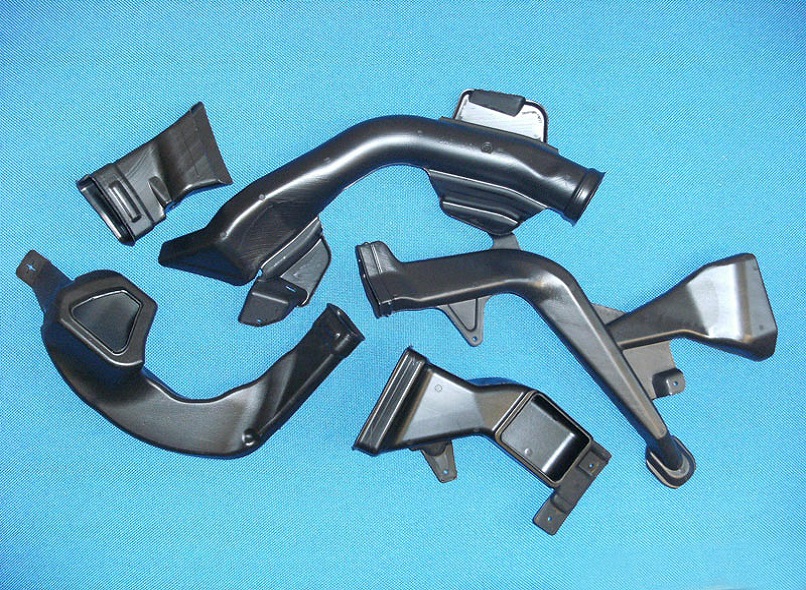
Hot plate welding is a widely used technique for joining plastic components in various industries. In the automotive sector, hot plate welding plays a crucial role in welding ventilation ducts and other components. This comprehensive guide will explore the process of hot plate welding, its applications in automotive components ventilation ducts, and the benefits it offers. So, let's dive in and understand the ins and outs of hot plate welding for automotive components ventilation ducts.
I. Understanding Hot Plate Welding
Hot plate welding, also known as mirror, platen, or butt welding, is a thermoplastic welding process used to join two plastic components. It involves heating the interface surfaces of the components using a heated metal plate, which melts the plastic. Once the components reach a molten state, they are pressed together under a specific pressure for a short period. This molecular motion creates a strong bond between the components. After cooling, the welded components fuse into a single piece, ensuring a reliable and durable weld.
The hot plate welding process can be divided into several steps:
- Preparation: The two plastic components to be welded are positioned on the hot plate welding machine.
- Heating: The hot plate is heated to a specific temperature, which varies depending on the type of plastic being welded.
- Melting: The heated hot plate is brought into contact with the interface surfaces of the plastic components, causing them to melt.
- Joining: Once the components reach a molten state, they are pressed together under a certain pressure, ensuring proper fusion.
- Cooling: After a designated cooling period, the welded components solidify, forming a strong bond.
II. Applications in Automotive Components Ventilation Ducts
In the automotive industry, ventilation ducts play a crucial role in maintaining a comfortable cabin environment. These ducts ensure the proper flow of air, allowing for efficient heating, ventilation, and air conditioning (HVAC) systems. Hot plate welding offers a reliable and efficient method for joining ventilation ducts and other plastic components in automotive applications.
a. Benefits of Hot Plate Welding for Ventilation Ducts
Hot plate welding provides several key benefits when used for welding automotive components ventilation ducts:
- Strong and Durable Joints: Hot plate welding creates robust and long-lasting joints, ensuring the integrity of ventilation ducts. The fusion of the plastic components results in a seamless and leak-proof connection.
- Design Flexibility: Hot plate welding allows for the joining of different shapes and sizes of ventilation ducts. This flexibility enables manufacturers to design complex duct systems that meet specific automotive requirements.
- Cost-Effective: Hot plate welding offers a cost-effective solution for joining ventilation ducts. The process is efficient and requires minimal post-welding processing, reducing production costs.
- High Production Efficiency: Hot plate welding machines can be customized to fit around the parts, making them ideal for welding small brackets or ports onto larger complex parts. This modular and configurable solution improves production efficiency and adaptability.
b. Automotive Components Suitable for Hot Plate Welding
Hot plate welding is commonly used in the automotive industry for welding various components, including:
- Underhood Ducts: Automotive underhood ducts, which are responsible for routing air to various engine components, often require hot plate welding. The meandering design of these ducts, along with the presence of ports and brackets, makes hot plate welding an ideal joining method.
- Tail Lamps: Tail lamps are essential safety components in vehicles, and hot plate welding ensures a secure and reliable connection between different parts of tail lamps.
- Automobile Washer Tanks: Hot plate welding is used in the assembly of automobile washer tanks, ensuring a watertight and durable connection.
- Automobile Battery Shells: With the growing demand for electric vehicles, hot plate welding plays a crucial role in joining battery shells, ensuring the integrity and safety of the battery packs.
III. Advantages of Hot Plate Welding
Hot plate welding offers several advantages over other joining techniques, making it a preferred choice in automotive components ventilation ducts welding:
- Precise and Consistent Results: Hot plate welding provides precise control over the welding process, resulting in consistent and high-quality welds. The temperature and pressure parameters can be accurately monitored and adjusted to ensure optimal welding conditions.
- Versatility: Hot plate welding can be used to join a wide range of thermoplastic materials, including polyethylene, polypropylene, polyvinyl chloride (PVC), and more. This versatility makes it suitable for various automotive applications.
- Strong and Reliable Joints: Hot plate welding creates strong and reliable joints that can withstand the demands of automotive environments. The fusion of the plastic components ensures a seamless connection without weak points or leaks.
- Efficiency: Hot plate welding offers fast cycle times, allowing for high-volume production. The process can be automated, further enhancing efficiency and reducing labor costs.
- Cost-Effective: Hot plate welding is a cost-effective joining method, as it eliminates the need for additional fasteners or adhesives. The process also minimizes post-welding processing, reducing overall production costs.
IV. Hot Plate Welding Equipment
Hot plate welding requires specialized equipment to achieve precise and efficient welds. There are various types of hot plate welding machines available, each designed to meet specific welding requirements. Some common features and components of hot plate welding equipment include:
- Hot Plate: The hot plate is the primary component responsible for heating the plastic components during the welding process. It is typically made of a high-quality metal with excellent heat conductivity.
- Temperature Control: Hot plate welding machines feature precise temperature control systems to ensure accurate heating and melting of the plastic components. These systems monitor and adjust the hot plate temperature throughout the welding process.
- Pressure Control: Pressure plays a crucial role in hot plate welding, as it ensures proper fusion and bonding of the plastic components. Hot plate welding machines incorporate pressure control mechanisms, such as hydraulic or pneumatic systems, to apply the required pressure during welding.
- Automation and Control Systems: Modern hot plate welding machines often feature advanced automation and control systems. These systems allow for precise control of various parameters, such as temperature, pressure, and welding time. They also enable process monitoring and data recording for quality control purposes.
- Safety Features: Hot plate welding machines prioritize operator safety by incorporating safety features such as interlocked safety doors, emergency stop buttons, and protective grating. These features ensure safe operation and minimize the risk of accidents.
V. Future Developments and Innovations
As the automotive industry continues to evolve, the demand for more advanced ventilation ducts and components will increase. Hot plate welding technology is also expected to evolve to meet these evolving demands. Some potential future developments and innovations in hot plate welding for automotive components ventilation ducts include:
- Improved Heating and Cooling Systems: Advancements in heating and cooling technologies will enhance the efficiency and precision of hot plate welding. This could include the development of faster heating and cooling cycles, allowing for increased production rates.
- Integration of Robotics: Robotic systems can be integrated into hot plate welding machines, automating the welding process and improving overall productivity. Robotic systems can handle complex welding tasks with precision and accuracy.
- Smart Welding Systems: The integration of sensors and monitoring systems can provide real-time feedback on welding parameters, ensuring consistent and high-quality welds. Smart welding systems can also detect defects or abnormalities during the welding process, leading to improved product quality.
- Material Advancements: The use of new and advanced thermoplastic materials in automotive components will require corresponding advancements in hot plate welding techniques. Research and development efforts will focus on optimizing the welding parameters for these new materials, ensuring reliable and durable joints.
VI. Conclusion
Hot plate welding plays a vital role in joining plastic components, including ventilation ducts, in the automotive industry. Its ability to create strong and durable joints makes it ideal for applications where reliable connections are essential. With ongoing advancements in hot plate welding technology and equipment, the future holds even greater potential for this joining technique. As the automotive industry continues to evolve, hot plate welding will continue to play a crucial role in ensuring the integrity and performance of ventilation ducts and other plastic components.