Hot Plate Welding Defects: Causes, Solutions, and Prevention
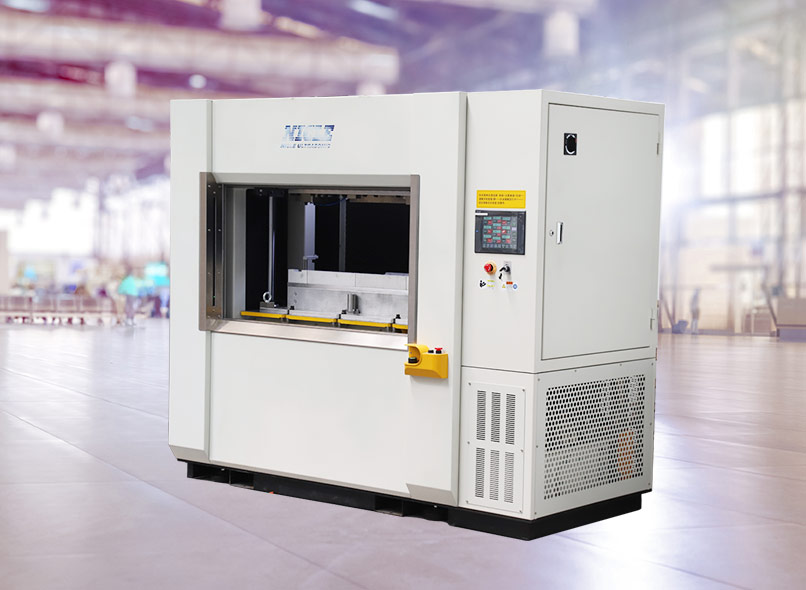
Hot plate welding is a widely used technique in the manufacturing industry for joining plastic components. It involves heating the joining surfaces of thermoplastic parts using a heated platen and then pressing them together to form a strong bond. While hot plate welding is generally a reliable method, it is not immune to defects that can compromise the quality and strength of the weld. In this article, we will explore common hot plate welding defects, their causes, and provide solutions and prevention strategies to ensure successful welds.
Types of Hot Plate Welding Defects
1. Incomplete Fusion
Incomplete fusion occurs when the molten plastic does not fully bond with the joining surfaces, resulting in weak or unreliable welds. This defect can be caused by several factors, including insufficient heating time, improper pressure, or contamination on the joining surfaces. To prevent incomplete fusion, it is crucial to ensure proper heating time, sufficient pressure during the welding process, and clean, uncontaminated joining surfaces.
2. Voids and Porosity
Voids and porosity are defects characterized by air pockets or gaps within the weld. They can weaken the structural integrity of the joint and make it susceptible to failure under stress. Voids and porosity can be caused by trapped air or moisture in the molten plastic, inadequate pressure during the welding process, or improper heating and cooling cycles. To minimize voids and porosity, it is important to thoroughly dry the plastic components before welding, apply sufficient pressure during the welding process, and follow proper heating and cooling cycles.
3. Burn Marks
Burn marks are discolorations or charring on the surface of the plastic components caused by excessive heat during the welding process. This defect can weaken the material and compromise the aesthetic appearance of the weld. Burn marks can occur when the hot plate temperature is too high or when the components are in contact with the hot plate for an extended period. To prevent burn marks, it is crucial to set the hot plate temperature within the recommended range and carefully control the heating and cooling cycles.
4. Warpage and Distortion
Warpage and distortion refer to the deformation or bending of the plastic components during the welding process. This defect can occur due to uneven heating, excessive pressure, or inadequate cooling. Warpage and distortion can compromise the fit and functionality of the final product. To minimize warpage and distortion, it is important to ensure uniform heating of the joining surfaces, apply balanced pressure during the welding process, and implement proper cooling techniques.
5. Weld Line Failure
Weld line failure occurs when the weld line, which is the interface where the molten plastic from the joining surfaces solidifies, fails to provide sufficient strength. This defect can be caused by improper pressure during the welding process, inadequate bonding between the molten plastic and the joining surfaces, or weak material properties. To prevent weld line failure, it is important to apply sufficient pressure during welding, ensure proper fusion between the molten plastic and the joining surfaces, and use high-quality materials with suitable mechanical properties.
6. Contamination
Contamination refers to the presence of foreign substances, such as dust, oil, or debris, on the joining surfaces or within the molten plastic. Contamination can lead to incomplete fusion, weak welds, or aesthetic issues. It is crucial to thoroughly clean the joining surfaces before welding and ensure a clean working environment to prevent contamination.
Solutions and Prevention Strategies
1. Proper Heating and Cooling Cycles
To avoid defects related to heating and cooling, it is essential to establish precise heating and cooling cycles. This includes setting the hot plate temperature within the recommended range, determining the appropriate heating and cooling times based on the material properties, and ensuring uniform heating and cooling of the joining surfaces.
2. Optimal Pressure Control
Applying the correct pressure during the welding process is crucial for achieving strong and reliable welds. It is important to carefully adjust the pressure to ensure proper fusion of the molten plastic and the joining surfaces without causing distortion or damage to the components.
3. Material Selection and Preparation
Choosing the right materials with suitable properties for hot plate welding is essential to minimize defects. Different thermoplastic materials have varying melting points, melt viscosities, and compatibility with each other. It is important to select materials that can be effectively welded together and properly prepare the joining surfaces to ensure clean and consistent welds.
4. Thorough Cleaning and Contamination Prevention
Proper cleaning of the joining surfaces and the surrounding environment is critical to prevent contamination-related defects. Thoroughly clean the components before welding to remove any dust, oil, or debris that could compromise the fusion of the molten plastic. Additionally, maintain a clean working environment to minimize the risk of contamination during the welding process.
5. Quality Control and Inspection
Implementing rigorous quality control measures and regular inspections can help identify and address potential defects early in the welding process. This includes visual inspections of the welds, testing the strength and integrity of the joints, and monitoring the process parameters to ensure consistency and adherence to specifications.
Conclusion
Hot plate welding is a widely used technique for joining plastic components, but it is not without its challenges. Understanding common hot plate welding defects, their causes, and implementing appropriate solutions and prevention strategies are essential for producing high-quality, reliable welds. By carefully controlling the heating and cooling cycles, applying optimal pressure, selecting suitable materials, preventing contamination, and implementing effective quality control measures, manufacturers can minimize defects and ensure successful hot plate welding operations.
Remember, successful hot plate welding requires expertise, precision, and attention to detail. By addressing and preventing common defects, manufacturers can achieve strong and durable welds, resulting in high-quality products that meet the desired specifications.
For more information on hot plate welding and other plastic welding techniques, please visit https://www.dizo-global.com/ or contact our expert team for personalized assistance.
See more hot plate welding machine