Hot Plate Plastic Welding: The Perfect Solution for Automotive Hydraulic Reservoirs Welding
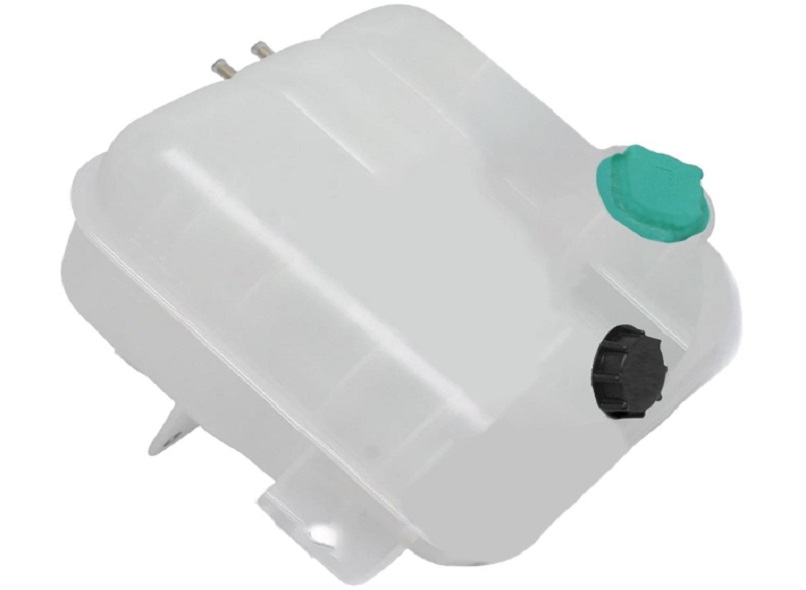
In the world of automotive manufacturing, hot plate plastic welding has emerged as a highly effective method for joining plastic components, especially in the welding of automotive hydraulic reservoirs. This innovative technique utilizes a heated metal plate to melt and join plastic parts, creating a strong and durable bond. With its ability to produce consistent and reliable welds, hot plate plastic welding has become the preferred choice for automotive manufacturers, ensuring leak-free and efficient hydraulic systems.
In this comprehensive guide, we will explore the intricacies of hot plate plastic welding, particularly in the context of automotive hydraulic reservoirs welding. We will delve into the various benefits, applications, and considerations associated with this technique. By the end, you will have a thorough understanding of why hot plate plastic welding is the perfect solution for automotive hydraulic reservoirs welding.
Benefits of Hot Plate Plastic Welding
Hot plate plastic welding offers numerous advantages that make it an ideal choice for welding automotive hydraulic reservoirs. Let's explore some of the key benefits:
1. Strong and Durable Welds
One of the primary advantages of hot plate plastic welding is its ability to create strong and durable welds. The heated metal plate ensures that the plastic parts reach the optimal temperature for fusion, resulting in a bond that is resistant to stress, vibration, and leakage. This makes hot plate plastic welding particularly suitable for automotive hydraulic reservoirs, where the integrity of the welds is crucial for maintaining the efficiency and reliability of the hydraulic system.
2. Compatibility with Various Plastic Materials
Hot plate plastic welding is compatible with a wide range of plastic materials commonly used in automotive applications, such as polyethylene, polypropylene, PVC, and more. This versatility allows manufacturers to weld different types of plastic components, including automotive hydraulic reservoirs, without the need for separate welding techniques for each material.
3. Hermetic and Airtight Seals
In the automotive industry, achieving hermetic and airtight seals is essential, especially in hydraulic systems. Hot plate plastic welding excels in creating seals that are not only strong but also airtight. This makes it an ideal choice for welding automotive hydraulic reservoirs, where maintaining the integrity of the hydraulic fluid is crucial for optimal system performance.
4. Uniform Bonding
Hot plate plastic welding ensures a uniform bond between the plastic components, regardless of variations in thickness or composition. This is particularly advantageous in automotive hydraulic reservoirs welding, where consistent and reliable welding is necessary to prevent any potential leaks or failures in the hydraulic system.
5. Suitable for Large and Complex Parts
Hot plate plastic welding is a versatile technique that can be used to join both large and complex plastic parts. This makes it particularly suitable for automotive hydraulic reservoirs welding, as these reservoirs often have intricate designs and require precise welding to ensure proper functionality.
Hot Plate Plastic Welding Process
To fully understand the benefits and applications of hot plate plastic welding in automotive hydraulic reservoirs welding, it is essential to grasp the process involved. Let's take a closer look at the steps involved in hot plate plastic welding:
1. Preparation
Before starting the welding process, proper preparation is crucial. This includes cleaning and preparing the surfaces of the plastic components to be welded. Any contaminants, such as dirt, oil, or grease, should be removed to ensure a strong and reliable bond.
2. Heating the Hot Plate
The next step is to heat the hot plate to the desired temperature. The temperature will depend on the specific plastic material being welded. It is essential to follow the manufacturer's guidelines and recommendations for the optimal temperature range.
3. Placing the Plastic Components
Once the hot plate reaches the desired temperature, the plastic components to be welded are placed on either side of the hot plate. The components should be positioned correctly to ensure proper alignment and contact with the hot plate.
4. Melting and Fusion
As the hot plate heats the plastic components, the plastic material begins to soften and melt. The heat is carefully controlled to avoid overheating or burning the plastic. Once the plastic reaches the ideal melting point, the hot plate is removed, and the components are quickly brought together and held under pressure to facilitate fusion.
5. Cooling and Solidification
After fusion, the welded components are allowed to cool and solidify. This ensures that the bond between the plastic parts is strong and durable. The cooling time may vary depending on the specific plastic material and the size and complexity of the components.
6. Finishing and Inspection
Once the welded components have cooled and solidified, any excess plastic or flash is removed to achieve a clean and finished appearance. The weld is then inspected to ensure its quality, strength, and integrity. Any defects or imperfections are addressed before the components are deemed ready for further assembly or use in the hydraulic system.
Applications of Hot Plate Plastic Welding in Automotive Hydraulic Reservoirs
Hot plate plastic welding finds extensive applications in automotive hydraulic reservoirs welding. Here are some key areas where this technique is commonly used:
1. Hydraulic Reservoir Assembly
Hot plate plastic welding is employed in the assembly of automotive hydraulic reservoirs. The welding process ensures that the reservoir is securely sealed, preventing any leakage or contamination of the hydraulic fluid. The hermetic and airtight seals created through hot plate plastic welding guarantee the integrity and efficiency of the hydraulic system.
2. Repair and Maintenance
In addition to assembly, hot plate plastic welding is also used for repair and maintenance of automotive hydraulic reservoirs. If a reservoir develops cracks or damage over time, hot plate plastic welding can be utilized to repair the damaged areas. The strong and durable welds created through this technique restore the reservoir's functionality and extend its lifespan.
3. Customization and Modifications
Hot plate plastic welding allows for customization and modifications of automotive hydraulic reservoirs to meet specific requirements. Manufacturers can easily incorporate additional components or fittings into the reservoir through hot plate plastic welding, enhancing its functionality and compatibility with the overall hydraulic system.
Selecting the Right Hot Plate Plastic Welder for Automotive Hydraulic Reservoirs Welding
When it comes to automotive hydraulic reservoirs welding, selecting the right hot plate plastic welder is crucial to ensure optimal results. Here are some important factors to consider when choosing a hot plate plastic welder for automotive hydraulic reservoirs welding:
1. Welding Machine Type
There are different types of hot plate plastic welders available in the market, each designed for specific applications and production requirements. Consider the type of automotive hydraulic reservoirs you will be welding and choose a welder that is suitable for your specific needs.
2. Welding Machine Features
Evaluate the features and capabilities of the hot plate plastic welder. Look for features such as precise temperature control, adjustable welding parameters, user-friendly interface, and safety features. These features will ensure ease of operation, consistent weld quality, and safe working conditions.
3. Welding Machine Durability
The durability and reliability of the hot plate plastic welder are crucial for long-term use. Consider the quality of the machine's construction, the reputation of the manufacturer, and the availability of spare parts and technical support. Investing in a durable and reliable hot plate plastic welder will ensure consistent and efficient welding of automotive hydraulic reservoirs.
4. Welding Machine Customization Options
Some hot plate plastic welders offer customization options to meet specific requirements. Consider whether you need any custom features or modifications for your automotive hydraulic reservoirs welding. Discuss these requirements with the manufacturer to ensure that the welder can be tailored to your specific needs.
5. Cost and Return on Investment
Evaluate the cost of the hot plate plastic welder and compare it with the features and benefits it offers. Consider the long-term return on investment, taking into account the efficiency, quality, and durability of the welder. It is important to strike a balance between cost and performance to make an informed decision.
Conclusion
Hot plate plastic welding has revolutionized the automotive industry, particularly in the welding of automotive hydraulic reservoirs. Its ability to create strong and durable welds, compatibility with various plastic materials, and suitability for large and complex parts make it the perfect solution for automotive hydraulic reservoirs welding.
By understanding the benefits, applications, and considerations associated with hot plate plastic welding, manufacturers can make informed decisions when selecting a hot plate plastic welder for automotive hydraulic reservoirs welding. With the right welder, they can achieve consistent, reliable, and efficient welds, ensuring the integrity and performance of the hydraulic systems in automotive applications.
Investing in hot plate plastic welding technology not only guarantees high-quality welds but also contributes to the overall efficiency and reliability of automotive hydraulic systems. As technology continues to advance, hot plate plastic welding will play an increasingly significant role in the automotive industry, driving innovation, and enhancing the performance of hydraulic systems in vehicles.
So, embrace the power of hot plate plastic welding and elevate your automotive hydraulic reservoirs welding to new heights of precision and quality.