Hot Plate Plastic Welding for HDPE Barrels: A Comprehensive Guide
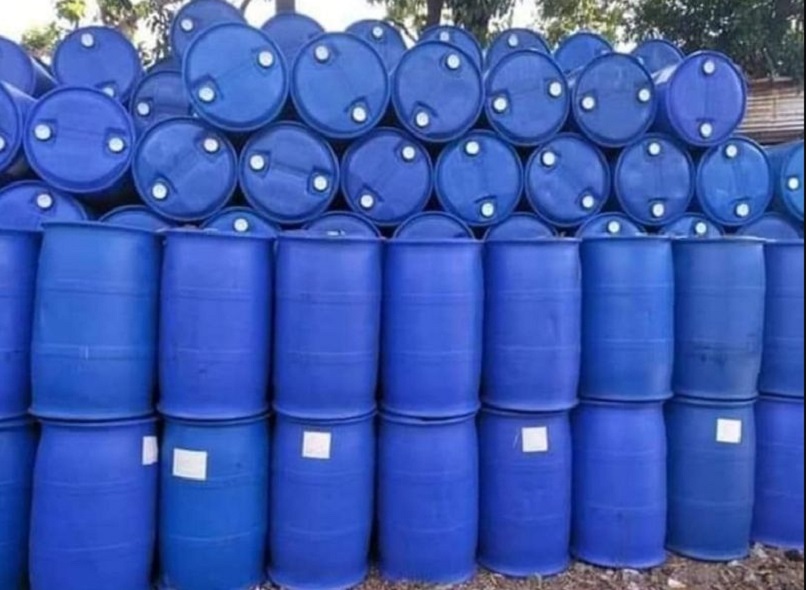
When it comes to joining lengths of HDPE (high-density polyethylene) barrels together, hot plate plastic welding is a reliable and efficient method. This process, also known as mirror, platen, or butt welding, is commonly used in various industries, including automotive applications and plumbing systems. In this comprehensive guide, we will explore the principles, equipment, techniques, and safety measures associated with hot plate plastic welding for HDPE barrels.
Understanding Hot Plate Plastic Welding
Hot plate welding involves using a heated metal plate, also known as a hot tool or hot plate, to heat and melt the interface surfaces of the thermoplastic parts. The process works by applying an axial load to the components during both the heating and joining phases. Once the interfaces are sufficiently melted or softened, the hot plate is removed, and the components are brought together under pressure to form a strong and durable weld.
Equipment and Setup
To perform hot plate plastic welding for HDPE barrels, you will need specific equipment and a proper setup. The following are key components of a typical hot plate welding setup:
1. Hot Plate Welding Machine
The hot plate welding machine is the central piece of equipment used in this process. It typically consists of a heated metal plate, power controls, and a clamping mechanism. The machine's design may vary, including pneumatic or servo-based variants, but the overall goal is to provide precise temperature control and apply the necessary pressure during the welding process.
2. Safety Measures
Safety is of utmost importance when working with hot plate plastic welders. Ensure the welding machine has interlocked safety doors with full guarding to maximize operator safety. Additionally, consider using safety curtains, safety doors, and two-hand push buttons with hardwire interlocks connected to a programmable logic controller (PLC). These safety features help prevent accidents and ensure a secure working environment.
3. Fixture Alignment and Changeover Time
Proper fixture alignment is crucial for achieving accurate and consistent welds. Look for hot plate welding machines that offer easy fixture alignment features, as this can significantly improve overall changeover time and productivity. Quick changeover concepts, such as the Singly Minute Exchange of Mold (SMED), allow for efficient swapping of molds or fixtures, further reducing downtime and increasing operational efficiency.
4. Temperature Control and Heating
Digital PID temperature control is essential for maintaining stable welding temperatures. This feature ensures precise control over the heating process, resulting in consistent and reliable welds. The hot plate welding machine should have a temperature control function that allows for multi-point independent temperature control, with an accuracy of up to ±2 degrees. This level of control ensures optimal weld quality.
Welding Process
Now that we understand the equipment and setup, let's delve into the actual hot plate plastic welding process for HDPE barrels.
1. Preparation
Before starting the welding process, ensure that the HDPE barrels are clean and free from any contaminants. Use rubbing alcohol and a clean rag to wipe down the surfaces that will be welded. This step is crucial for achieving proper fusion and preventing defects in the weld.
2. Heating the Hot Plate
Once the barrels are prepared, heat the hot plate to the appropriate temperature for HDPE welding. The recommended temperature for HDPE welding is typically between 250-280 degrees Celsius (482-536 degrees Fahrenheit). It is crucial to monitor and maintain the hot plate temperature within the specified range throughout the welding process.
3. Aligning the Barrels
Align the HDPE barrels precisely, ensuring that the welding surfaces are in contact with the hot plate. Apply gentle pressure to hold the barrels in place during the heating phase.
4. Heating Phase
During the heating phase, the hot plate transfers heat to the interface surfaces of the HDPE barrels. The heat softens the plastic, allowing it to blend together when pressure is applied.
5. Joining and Cooling Phase
Once the barrels reach the appropriate temperature, remove the hot plate and quickly bring the barrels together under pressure. Apply sufficient force to ensure a strong bond between the two barrels. Hold the barrels in place until the plastic cools and solidifies, forming a secure and durable weld joint.
6. Inspection and Quality Control
After the welding process is complete, inspect the weld joint to ensure it meets the desired quality standards. Look for any signs of defects, such as voids, incomplete fusion, or uneven surfaces. If any issues are identified, consider re-welding or making necessary adjustments to achieve the desired weld quality.
Advantages of Hot Plate Plastic Welding
Hot plate plastic welding offers several advantages for joining HDPE barrels:
- Strong and Durable Welds: The fusion of HDPE barrels using hot plate welding results in weld joints that are highly resistant to mechanical stress and environmental factors.
- No Filler Rod Required: Unlike other welding methods, hot plate plastic welding for HDPE barrels does not require the use of a filler rod. The heat and pressure alone are sufficient to create a robust weld joint.
- Versatility: Hot plate plastic welding can be used to join HDPE barrels of various shapes and sizes, providing flexibility in manufacturing and construction applications.
- Cost-Effective: Hot plate welding machines are available at different price points, making the process an affordable option for both small-scale and large-scale welding operations.
Safety Considerations
When performing hot plate plastic welding for HDPE barrels, it is crucial to prioritize safety. Here are some key safety considerations:
- Personal Protective Equipment (PPE): Always wear appropriate PPE, including heat-resistant gloves, safety glasses, and protective clothing, to protect yourself from potential hazards associated with the welding process.
- Ventilation: Ensure the welding area is well-ventilated to prevent the accumulation of harmful fumes. Hot plate welding can generate gases, so working in a well-ventilated area or using fume extraction systems is essential.
- Training and Certification: Proper training and certification in hot plate plastic welding techniques are vital to ensure safe and efficient operation of the welding equipment. Stay updated with industry best practices and safety guidelines to minimize the risk of accidents.
- Fire Safety: Hot plate welding involves the use of heat, which can pose a fire hazard. Keep fire extinguishers readily available and familiarize yourself with the appropriate firefighting techniques to prevent and manage potential fires.
Conclusion
Hot plate plastic welding is a reliable and efficient method for joining HDPE barrels. By following the proper techniques, utilizing suitable equipment, and prioritizing safety, you can achieve strong and durable welds in your HDPE barrel applications. Remember to adhere to safety guidelines and continue to enhance your knowledge and skills in hot plate plastic welding for optimal results.