What is the Process of Hot Plate for HDPE Welding?
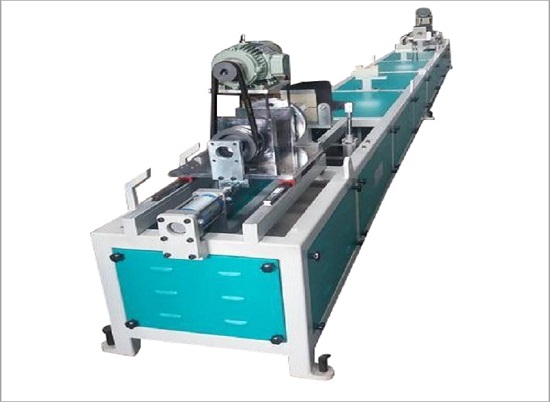
Introduction
Hot plate welding is a widely used technique for joining High-Density Polyethylene (HDPE) materials. It is commonly used in industries such as construction, plumbing, automotive manufacturing, and more. In this article, we will delve into the details of the hot plate welding process specifically for HDPE materials. We will explore the steps involved, the advantages of hot plate welding for HDPE, and its limitations in certain scenarios.
The Process
- Preparing the Materials:
- Before beginning the welding process, it is crucial to ensure that the HDPE materials to be joined are clean and free from any contaminants. This can be achieved by wiping the surfaces with a clean cloth or using a mild cleaning solution.
- Measure and cut the HDPE pieces to the desired size and shape using appropriate tools such as a ruler and a saw. It is important to ensure accuracy in the dimensions to achieve proper alignment during the welding process.
- Heating the Hot Plate:
- Turn on the hot plate welding machine and set it to the appropriate temperature for HDPE. The temperature required for HDPE welding typically ranges from 240 to 270 degrees Celsius.
- Wait for the hot plate to reach the desired temperature. Advanced hot plate welding systems may have temperature sensors or displays to ensure precise temperature control. These systems allow for better accuracy and consistency in the welding process.
- Clamping the Materials:
- Place the HDPE pieces to be welded on the hot plate, ensuring that the surfaces to be joined are in contact with the plate. Proper alignment of the pieces is crucial to ensure a strong and secure weld.
- Apply pressure using clamps or fixtures to hold the pieces in place during the welding process. Adjustable clamps or fixtures can be used to achieve the desired pressure and alignment. This ensures that the HDPE pieces are held firmly together during the fusion process.
- Heating and Melting:
- Allow the HDPE pieces to heat and melt on the hot plate. The heat from the hot plate softens the material, making it pliable for fusion.
- The melting temperature should be carefully controlled to avoid overheating or underheating, which can result in weak or incomplete welds. Temperature sensors or thermocouples can be used to monitor the melting process and ensure precise temperature control. This helps in achieving consistent and reliable welds.
- Joining the Materials:
- Once the HDPE pieces are adequately heated and melted, remove them from the hot plate. Be cautious as the material will be hot.
- Quickly bring the two melted surfaces together, ensuring proper alignment. The molten HDPE should be in contact with each other to facilitate fusion.
- Apply sufficient pressure to fuse the materials together. The pressure should be evenly distributed to ensure a strong bond. This can be achieved through the use of pneumatic or hydraulic systems that allow for precise pressure control.
- Cooling and Solidification:
- After the fusion, allow the welded joint to cool and solidify. The cooling process ensures the integrity and strength of the joint.
- The cooling time should be sufficient to allow the HDPE to solidify completely and achieve its maximum strength. It is recommended to follow the cooling time guidelines provided by the HDPE manufacturer. Proper cooling helps in preventing deformations and ensures the durability of the weld.
- Finishing:
- Trim any excess material from the welded joint, if necessary. This can be done using a sharp knife or trimming tool. The trimming ensures a clean and aesthetically pleasing finish.
- Inspect the weld for any defects or imperfections. Smooth out any rough edges or uneven surfaces to ensure a clean and visually appealing final product.
- Perform any required post-welding treatments, such as testing or coating, according to the specific requirements of the project. These additional steps help in ensuring the quality and functionality of the welded HDPE joint.
Advantages of Hot Plate Welding for HDPE
Hot plate welding for HDPE offers several advantages over other welding methods:
- Strong and Durable Joints: Hot plate welding creates robust and long-lasting connections between HDPE materials. The resulting welds are often stronger than the HDPE material itself, providing structural integrity and reliability.
- Versatility: Hot plate welding can be used to join HDPE materials of various shapes and sizes. Whether it's large pipes or small components, hot plate welding can accommodate different dimensions and geometries.
- Cost-Effective: The equipment and materials required for hot plate welding are relatively affordable compared to other welding techniques. This makes it a cost-effective choice for many manufacturers and fabricators.
- Consistency: The process ensures consistent and uniform welding results. The temperature control and pressure application in hot plate welding contribute to reliable and repeatable welds, reducing the chances of defects or weak joints.
Limitations of Hot Plate Welding for HDPE
While hot plate welding is a versatile and effective method for joining HDPE materials, it does have a few limitations:
- Equipment Requirements: Hot plate welding requires specialized machinery, including a hot plate welding machine and clamps or fixtures. These equipment may not be readily available in all settings, and manufacturers or fabricators may need to invest in them to utilize this technique.
- Surface Preparation: Proper cleaning and preparation of HDPE surfaces are crucial for achieving high-quality welds. Any dirt, oil, or contaminants on the surfaces can interfere with the fusion process and result in weak welds. Thoroughly cleaning the surfaces before welding is essential for optimal results.
- Thickness Limitations: Hot plate welding is most effective for HDPE materials with thicknesses ranging from 3mm to 25mm. If the material is too thin or too thick, alternative welding methods may be more suitable to ensure proper fusion and integrity of the joint.
Conclusion
Hot plate welding is a reliable and efficient method for joining HDPE materials. By following the outlined process and taking the necessary precautions, one can achieve strong and durable welds in various applications. Understanding the advantages and limitations of hot plate welding for HDPE will help manufacturers and fabricators make informed decisions and ensure successful welding projects. With its versatility, cost-effectiveness, and ability to produce consistent and reliable results, hot plate welding proves to be a valuable technique in the world of HDPE fabrication.