Plastic Welding Solutions for Home Appliances Manufacturers
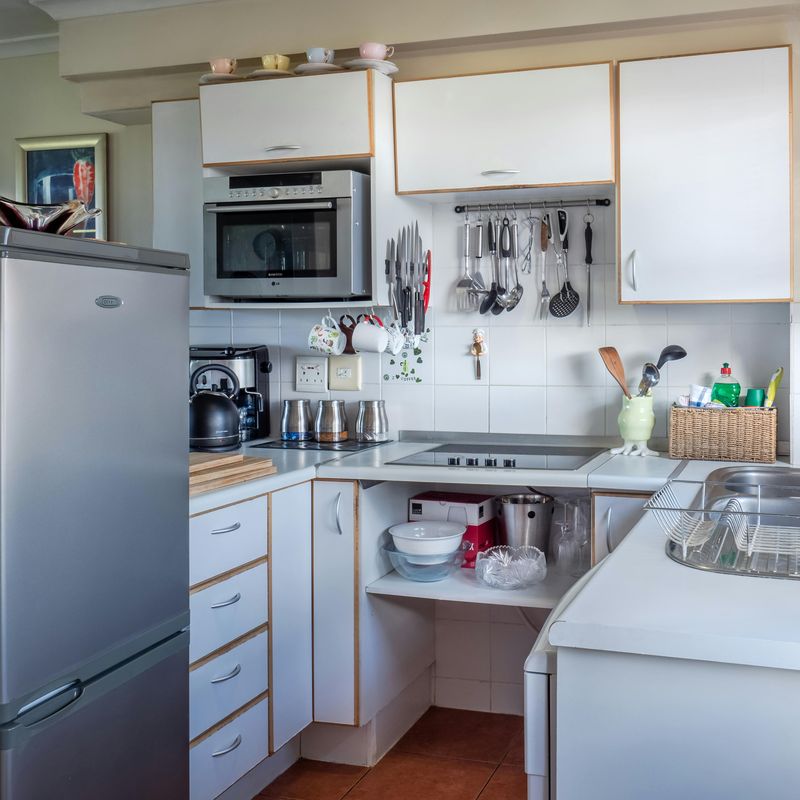
Manufacturers often use plastic welding to make home appliances strong and reliable. This plastic welding process can join plastic parts together without using screws or glue, making the final product durable and easy to produce.
In this article, we'll look at different plastic welding methods, where they are used in home appliances, and why plastic welding is a great solution for home appliance manufacturing.
Whether you are making large household appliances like dishwashers or small ones like microwave ovens, understanding plastic welding can improve your production process and product quality.
Table of Contents
What is Plastic Welding?
Types of Welding Technologies for Home Appliances
Applications of Plastic Welding in Large Home Appliances
Applications of Plastic Welding in Small Home Appliances
Benefits of Plastic Welding for Home Appliance Manufacturers
Choosing the Right Welding Method for Your Home Appliance
8. Key Factors Influencing Welding Success
Adapted Plastic Welding Machines from Dizo for Home Appliances
FAQs on Plastic Welding for Home Appliances
Final Thoughts
What is Plastic Welding?
Plastic welding is a process used to join plastic parts by applying heat or pressure to create a strong bond between them. Unlike traditional adhesives or mechanical fasteners, plastic welding equipment creates a strong, durable bond by melting the surfaces of the plastic parts and then cooling them to form a seamless joint.
This plastic welding process is highly effective for various plastic materials, such as thermoplastics, which can be melted and re-solidified multiple times.
Types of Welding Technologies for Appliances
Plastic welding in home appliance manufacturing uses different plastic welding methods, each designed for specific plastic parts and materials.
The three most common plastic welding methods are Ultrasonic Welding, Hot Plate Welding, and Vibration Welding. Each method has its benefits, such as speed, accuracy, and cost savings, making them important for home appliance manufacturers.
Ultrasonic Welding
Ultrasonic welding uses high-frequency ultrasonic vibrations to generate heat at the interface of plastic parts. This heat melts the material, allowing the components to fuse. It is widely used for small, intricate parts, such as buttons, control panels, and housings.
Ultrasonic welding is fast, precise, and energy-efficient, offering minimal material deformation and no need for additional consumables. So, ultrasonic welding is a preferred choice for home appliance manufacturers seeking high-quality plastic welding solutions for delicate household appliance components.
Hot Plate Welding
Hot plate welding involves heating a plastic part using a heated plate until the material becomes soft. The heated parts are then pressed together, forming a strong bond. This method is ideal for larger parts like appliance housings and covers, where uniform heat distribution is critical.
Hot plate welding provides reliable, high-strength joints, but it is slower compared to ultrasonic welding. Household appliance manufacturers often prefer plastic welding machine suppliers who offer tailored solutions for specific househole appliance parts.
Hot plate welding continues to be essential for water tank welding in appliances like washing machines and water heaters.
Vibration Welding
Vibration welding uses mechanical vibrations to generate heat and join plastic parts. One part is held stationary, while the other is moved back and forth at a high frequency. This motion causes friction, generating the heat needed to melt the plastic at the joint.
Vibration welding is used for parts with large surface areas and offers a strong bond with minimal deformation. It's commonly used in manufacturing large household appliance parts, such as washing machine panels and air conditioner components.
As household appliance manufacturers continue to seek plastic welding solutions that balance strength and cost, vibration welding remains a critical process for creating durable appliance parts.
Applications of Plastic Welding in Large Home Appliances
Plastic welding is important in the manufacturing of large home appliances, ensuring the strength, durability, and functionality of essential components.
From refrigerators to dishwashers, platic welding solutions are essential for creating robust joints in key parts such as reservoirs, water tanks, and housings. Below are some common applications of plastic welding in large home appliances:
Refrigerators
For refrigerators manufacturers, they use plastic welding to create sealed compartments and secure parts like water reservoirs, trays, and insulation sections. These components must withstand temperature fluctuations and prevent leaks, making plastic welding machines crucial for achieving tight, reliable seals.
The precision of these plastic welding solutions is vital for those refrigerators manufacturers who need to maintain energy efficiency and preventing fluid leakage in cold environments.
Washing Machines
Plastic welding technology is used in washing machines for joining components like water tanks, housings, and control panels. Plastic welding machines ensure that these components are securely bonded, maintaining the appliance's reliability.
The use of hot plate welding technologies helps in creating bonded seals that are essential for water tank welding in washing machines.
Dryers
In dryers, plastic welding is applied to join parts such as housing, ducts, and internal compartments. Strong, reliable welds are essential to handle the heat and mechanical stresses involved in drying clothes.
These plastic welded joints also contribute to the aesthetic appeal of the appliance, ensuring smooth and seamless finishes. Custom welding machines are often employed for specific parts that require unique designs or performance standards.
Dishwashers
Plastic welding in dishwashers is used to form sealed, watertight compartments. It ensures that the water tanks, pump housings, and door seals are securely welded together.
These excellent joints are essential for preventing water damage and improving the durability and performance of the dishwasher. Ultrasonic welding machines are frequently used in these applications for their speed and precision in handling small, intricate components.
Reservoir Tanks
Plastic welding is widely used for joining reservoir tanks in various home appliances, including water heaters, coffee machines, and humidifiers.
Plastic welding machine suppliers offer solutions that help ensure these reservoir tanks are leak-proof and durable. The process is critical for maintaining the appliance's functionality over time, preventing failures or damage.
Applications of Plastic Welding in Small Home Appliances
Plastic welding is indispensable in the manufacturing of small home appliances, where precision, durability, and functionality are key to creating reliable products.
In these appliances, welding ensures strong bonds in components that require both resilience and a seamless finish. Below are some common applications of plastic welding in small appliances:
Blenders
In blenders, plastic welding is used to join the plastic housing, motor cover, and lid securely. It helps create strong seals that prevent fluid from escaping during blending.
The use of ultrasonic welding machines ensures precise, high-quality joints that contribute to the overall strength and durability of the blender. These welding solutions also allow for a clean, smooth finish that enhances the blender's visual appeal.
Coffee Makers
Plastic welding in coffee makers is applied to parts such as the water reservoir, pump housing, and base. These plastic components are often subjected to high temperatures and pressure, requiring strong and reliable joints.
Plastic welding ensures airtight seals that prevent water and coffee grounds from escaping, ensuring optimal performance and preventing malfunctions.
Vacuums
Plastic welding is a key factor that must be considered in the joining of vacuum cleaner components such as the dustbin, filter housing, and motor covers. It ensures that the parts remain securely fastened during use and can withstand the mechanical forces of vacuuming.
Good seals are also critical in preventing dust and debris from escaping, enhancing both performance and cleanliness. Plastic welding equipment like ultrasonic welding machines helps ensure precise bonding in these parts.
Weed Whackers and Chainsaws
In garden tools like weed whackers and chainsaws, plastic welding is used to join housing components, fuel tanks, and covers.
These plastic parts are exposed to harsh outdoor conditions, including vibrations, temperature fluctuations, and physical stress. Plastic welding ensures that the parts stay securely in place and can withstand the rigors of frequent use, providing durability and strength.
Iron Water Reservoirs
For appliances like steam irons, plastic welding is used to create safe seals in the water reservoirs. This ensures that water stays inside the reservoir, enhancing the safety and effectiveness of the steam iron.
The plastic welding process also allows for a seamless, smooth surface that improves the aesthetic appeal of the appliance.
Benefits of Plastic Welding for Home Appliance Manufacturers
Plastic welding offers a variety of advantages for manufacturers in the home appliance industry. This technology ensures that appliance parts are securely bonded, durable, and capable of withstanding daily use.
Below, we discuss the key benefits of plastic welding solutions for household appliance manufacturers, including strength and durability, environmental benefits, cost efficiency, and customization.
Strength and Durability
Plastic welding creates strong, permanent bonds between plastic parts, resulting in joints that can withstand mechanical stress, temperature fluctuations, and environmental conditions.
This is particularly important for appliances that undergo heavy use, such as washing machines and refrigerators, where components like reservoirs, tanks, and housings need to be durable and resistant to wear.
With the help of advanced plastic welding equipment, ultrasonic welding machines, and hot plate welders, manufacturers can ensure the structural integrity of these parts, helping to extend the lifespan of the appliances and reduce the risk of breakdowns.
Environmental Benefits
Plastic welding is an environmentally friendly solution compared to traditional methods like adhesives or screws. It does not require additional consumables, such as glue or fasteners, which helps to reduce material waste.
Moreover, plastic welding uses less energy and produces fewer emissions, contributing to a more sustainable manufacturing process. It also enables the use of recyclable materials, further reducing the environmental impact of appliance production.
Cost Efficiency
Plastic welding can significantly reduce manufacturing costs. This technology eliminates the need for additional materials such as adhesives, fasteners, and sealants, leading to savings on raw materials.
Additionally, plastic welding machines, such as ultrasonic welders and hot plate welding machines, offer a fast and efficient process, allowing for high-volume production without sacrificing quality. The reduced labor costs and fewer steps in the assembly process further contribute to cost savings for appliance manufacturers.
Customization
Plastic welding offers flexibility in design and customization. Manufacturers can weld parts in a variety of shapes and sizes, enabling the creation of complex components with intricate designs. This is particularly useful for appliances that require custom enclosures or specialized parts.
Whether it's for aesthetic purposes or to meet specific functionality requirements, plastic welding allows manufacturers to create tailor-made welding solutions for their products, improving both performance and appearance.
Choosing the Right Welding Method for Your Home Appliance
Selecting the appropriate welding method for a home appliance depends on various factors, such as the part size, material type, production volume, and specific functional requirements.
The choice of plastic welding solution can have a significant impact on the quality, durability, and cost-efficiency of the final product.
Below, we explore key factors to consider when choosing the right plastic welding method for your appliance and present some real-world case studies of successful welding applications in popular home appliances.
Factors to Consider When Selecting a Welding Technique
Part Size and Complexity
The size and complexity of the parts to be welded should be considered in determining the welding method. For small, intricate parts with tight tolerances, ultrasonic welding is often ideal due to its precision.
On the other hand, for larger, bulkier parts like refrigerator body panels or washing machine housings, methods like hot plate welding or vibration welding are more suitable as they provide strong and secure joints on larger surfaces.
Material Type
The type of plastic material being welded influences the welding method chosen. Different plastics (such as ABS, polycarbonate, or polypropylene) have varying melting points and require different heat treatments.
For example, laser welding works well for thermoplastic materials and offers precise, high-quality welds, while vibration welding is ideal for materials with different melting points that need to be joined securely.
Production Volume
The scale of production also impacts the choice of welding technique. For high-volume production, methods like ultrasonic welding or spin welding are faster and more efficient, providing quick turnarounds.
For smaller production runs, methods such as hot plate welding may be more suitable, as they are less expensive and still offer strong bonding.
Key Factors Influencing Welding Success
Successful plastic welding for home appliances depends on several key factors: material compatibility, welding parameters, joint design, and troubleshooting common issues. Here's a brief overview of each factor:
Material Compatibility and Preparation
Material compatibility is essential for a successful weld. Different plastics have unique properties, so ensuring that the materials being welded are compatible is crucial. Additionally, proper preparation of the materials by cleaning and removing contaminants like oils or dust is necessary to ensure strong fusion.
The Role of Temperature, Pressure, and Welding Speed
- Temperature: The correct heat level is essential to avoid material degradation or incomplete bonding. Too much heat can cause damage, while too little may result in weak joints.
- Pressure: Proper pressure ensures that the parts are held together firmly without distortion. Too much pressure can damage the parts, while too little may result in weak bonds.
- Welding Speed: The welding speed must be optimized. Too fast may cause incomplete welding, and too slow can lead to overheating or material damage.
Importance of Joint Design
The joint design impacts energy transfer during welding. Proper geometry, such as butt, lap, or overlap joints, ensures uniform heat and pressure distribution, leading to stronger, more durable joints. A well-designed joint enables a solid, cohesive bond, essential for load-bearing or critical components.
Troubleshooting Common Issues
Several common issues may arise, such as:
- Misalignment: Incorrectly aligned parts can result in weak or incomplete welds.
- Improper Pressure: Calibration of pressure is critical for achieving strong, uniform welds.
- Moisture: Trapped moisture in plastic materials can cause poor bonding. Pre-drying materials help prevent this issue.
By addressing these factors, manufacturers can ensure high-quality, durable welds in home appliances.
Adapted Plastic Welding Machines from Dizo for Home Appliances
Dizo offers advanced plastic welding machines designed to meet the needs of home appliance manufacturers. Below are three key welding machines: Ultrasonic Welder, Hot Plate Welder, and Vibration Welder.
Ultrasonic Welder
Ultrasonic welding uses high-frequency vibrations to melt plastic parts. It's ideal for small, delicate components like blender housings and vacuum cleaner parts.
- Advantages: Precise, low power consumption, minimal heat.
- Best for: Small, intricate components.
Hot Plate Welder
Hot plate welding uses a heated metal plate to fuse plastic parts. It's best for larger parts like washing machine panels and refrigerator doors.
- Advantages: Strong joints, and precise temperature control.
- Best for: Larger components needing robust welds.
Vibration Welder
Vibration welding uses high-frequency vibrations to melt plastic parts through friction, making it efficient for high-volume production.
- Advantages: Fast cycle times, and minimal thermal stress.
- Best for: Heavy-duty parts, high-volume manufacturing.
Dizo plastic welding machines ensure high precision and durability, offering solutions for a wide range of appliance applications.
FAQs on Plastic Welding for Home Appliances
Plastic welding plays a crucial role in joining components in home appliances. Below are some frequently asked questions to help clarify common concerns.
How Can You Tell if Plastic is Weldable?
To determine if plastic is weldable, check for material compatibility, melting point, and surface cleanliness. Common weldable plastics include ABS, PVC, and polypropylene. Ensure the plastic has a uniform thickness and is free from contaminants like oils or dirt, which can affect the welding process.
Can PVC Plastic Be Welded?
Yes, PVC (Polyvinyl Chloride) can be welded using techniques like hot air, extrusion, and solvent welding. It is popular in applications like piping and storage tanks due to its low melting point and strong bond strength.
Can LDPE and HDPE Be Welded Together?
While LDPE (Low-Density Polyethylene) and HDPE (High-Density Polyethylene) share similarities, they present challenges when welded together because of different molecular structures. It's best to use the same type of polyethylene for stronger, more reliable joints.
What Materials Cannot Be Welded?
Certain materials are difficult or impossible to weld. Polystyrene is brittle and has low heat resistance, making it challenging to weld.
Fluoropolymers (e.g., PTFE) and polycarbonate also pose difficulties. Metals like aluminum cannot be welded with standard plastic welding methods without specialized plastic welding equipment.
Final Thoughts
Plastic welding is a key process in creating durable, affordable, and dependable home appliances. It is vital for securely bonding plastic parts in both large and small appliances, delivering numerous advantages in terms of efficiency, strength, and cost-effectiveness.
By selecting the right plastic welding solutions, household appliance manufacturers can achieve superior product quality, streamline production, and meet the growing demand for sustainable, high-performance appliances.