FIND INDUSTRY SOLUTIONS WITH ULTRASONIC
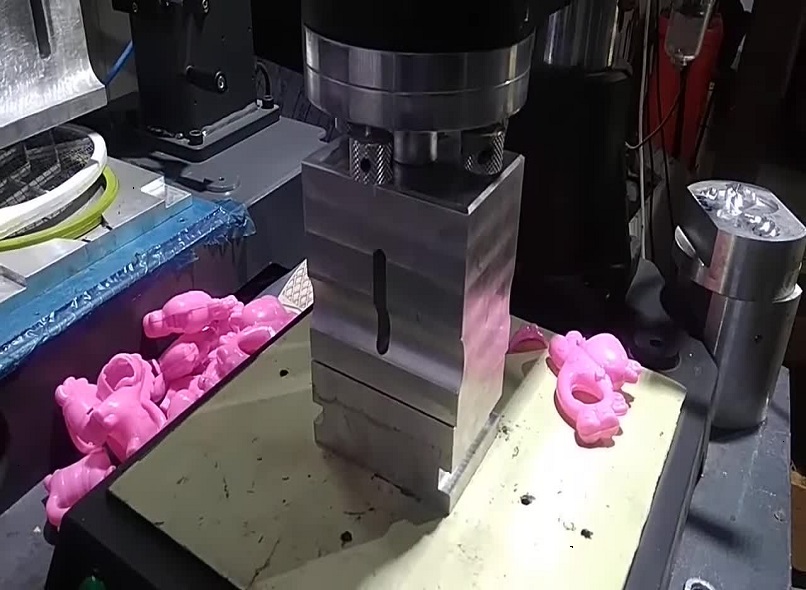
In today's fast-paced industrial landscape, finding efficient and reliable solutions is essential. Ultrasonic plastic welding is a technology that has been revolutionizing various industries. This process offers precision, speed, and cost-effectiveness, making it an attractive choice for businesses worldwide.
What is Ultrasonic Plastic Welding?
Ultrasonic plastic welding is a bonding process that uses high-frequency ultrasonic vibrations to join thermoplastic materials. This process eliminates the need for adhesives, solvents, or additional hardware, making it environmentally friendly and cost-effective. This technology has found applications in various industries:
- Automotive Industry: Ultrasonic plastic welding is used to assemble intricate components like dashboards, air ducts, and even lighting fixtures. The ability to create strong bonds with intricate geometries ensures safety and reliability.
- Electronics: Ultrasonic welding is indispensable in the assembly of microelectronics, ensuring precise connections without compromising delicate components within.
- Medical Devices: Ultrasonic welding is used to create airtight seals in medical devices such as catheters, IV bags, and surgical instruments. This process ensures a sterile environment and patient safety.
- Packaging: Ultrasonic welding is used in the production of blister packs, clamshells, and even flexible packaging. It allows for strong seals without compromising the visual appeal of the packaging.
- Consumer Goods: Ultrasonic plastic welding allows manufacturers to create seamless and tamper-proof connections, enhancing product reliability and safety.
- Aerospace: Ultrasonic welding is used to create lightweight yet robust structures, ensuring that critical components remain intact even in the harshest conditions.
- Textiles: Ultrasonic welding is used to create seams and bonds in fabrics, enhancing the durability and functionality of products like sportswear and outdoor gear.
Benefits of Ultrasonic Plastic Welding
Many industries have adopted ultrasonic plastic welding due to the numerous benefits it offers:
- Speed: Ultrasonic welding is incredibly fast, with cycles measured in milliseconds. This rapid production speed allows businesses to increase their output and meet growing market demands efficiently.
- Precision: The technology provides exceptional precision, ensuring that even the most delicate components are bonded accurately. This precision translates into consistent product quality.
- Cost-Effective: Ultrasonic welding can significantly cut production costs over time by eliminating the need for adhesives and reducing energy consumption. Its reliability also reduces the likelihood of costly rework.
- Clean and Eco-Friendly: Ultrasonic welding is a clean process, not producing fumes, emissions, or hazardous waste, making it an environmentally friendly choice.
- Strong and Durable: The bonds created by ultrasonic welding are exceptionally strong and durable, ensuring that products can withstand the rigors of their intended applications, enhancing safety and longevity.
- Design Flexibility: Ultrasonic plastic welding is highly adaptable to different material types, shapes, and sizes, making it ideal for industries with varying product requirements.
- Reduced Maintenance: Ultrasonic welding machines are known for their reliability and low maintenance requirements, resulting in less downtime and higher productivity.
Challenges and Considerations
While ultrasonic plastic welding offers numerous advantages, it's important to consider some challenges and factors before implementing it:
- Material Compatibility: Not all materials are suitable for ultrasonic plastic welding, and compatibility should be carefully assessed. If necessary, material additives or pre-treatments may be required.
- Design Complexity: While ultrasonic welding is versatile, extremely intricate designs may pose challenges. Consulting with experts in the field is advisable for such cases.
- Quality Assurance: Ensuring consistent quality requires precise control over welding parameters, proper training, and regular maintenance of equipment.
- Regulatory Compliance: In industries like medical devices and aerospace, strict regulations govern manufacturing processes. Ultrasonic plastic welding processes should comply with these regulations.
- Initial Investment: Acquiring and setting up ultrasonic welding equipment can require an initial investment. However, the long-term cost savings often outweigh this upfront expense.
Ultrasonic plastic welding is a technology that has become a cornerstone across numerous industries, providing fast, precise, cost-effective, and eco-friendly solutions. Its ability to create strong and durable bonds, its adaptability to various materials, and its low maintenance requirements make it a sustainable solution for the future.
In a world where innovation is the key to success, ultrasonic plastic welding stands as a testament to the power of technology in addressing the complex challenges of modern industry. Whether in the automotive, electronics, medical, or any other sector, this technology is proving to be a game-changer, helping businesses discover solutions that drive their growth and success.