Exploring the Significance of Ultrasonic Weld Flaw Detectors in Weld Inspection
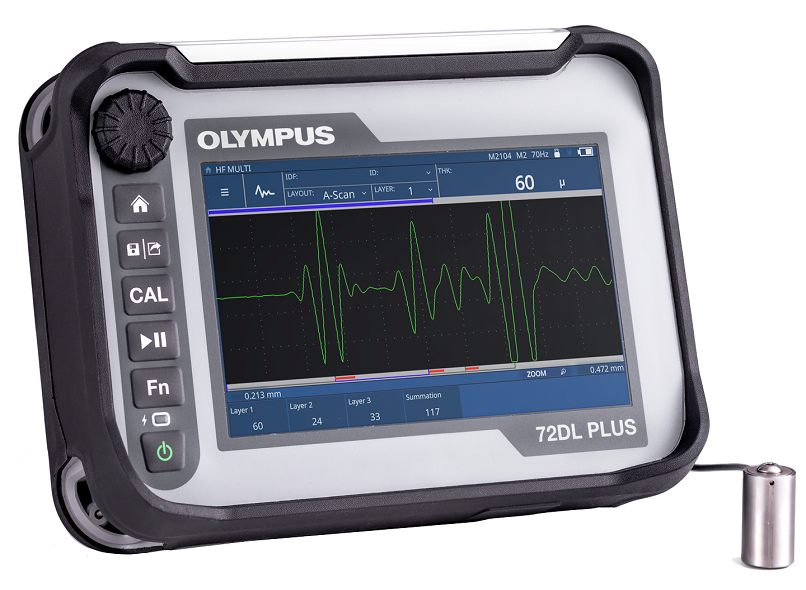
Ultrasonic weld flaw detectors are highly advanced and indispensable tools used in various industries to assess the quality and integrity of welded joints. This non-destructive testing method utilizes ultrasonic waves to detect and evaluate any flaws or discontinuities in the weld, ensuring the reliability and performance of critical components and structures. In this comprehensive article, we will delve into the significance of ultrasonic weld flaw detectors, their working principles, advantages, applications, and the factors that contribute to successful weld inspection.
Understanding Ultrasonic Waves and Weld Inspection
Ultrasonic waves are high-frequency sound waves that are beyond the range of human hearing. When directed into a material, such as a weld joint, these waves travel through it and encounter any flaws or defects. The waves are then reflected back to the transducer, creating echoes. By analyzing the time it takes for the echoes to return and their amplitude, ultrasonic weld flaw detectors can provide valuable information about the size, shape, and nature of the flaw.
Working Principles of Ultrasonic Weld Flaw Detectors
Ultrasonic weld flaw detectors consist of a probe or transducer that emits ultrasonic waves into the weld joint. The waves propagate through the material and interact with any flaws or changes in the weld's structure. The reflected waves are received by the transducer and converted into electrical signals. These signals, containing information about the weld's internal structure, are captured and analyzed by the flaw detector. Advanced algorithms and signal processing techniques are employed to detect and quantify any indications of defects, such as cracks, voids, or lack of fusion. Trained inspectors or technicians interpret the test results, evaluating the size, location, and severity of any detected flaws.
Advantages of Ultrasonic Weld Flaw Detectors
The use of ultrasonic weld flaw detectors offers several advantages in the inspection of welds:
- Non-Destructive Testing: Ultrasonic testing is a non-destructive method, meaning it does not damage the material being inspected. This allows for the evaluation of weld quality without compromising the integrity of the component or structure.
- High Accuracy and Precision: Ultrasonic weld flaw detectors can detect and measure even small flaws with great accuracy and precision. This ensures reliable results and helps in making informed decisions about the acceptability of welds.
- Versatility: Ultrasonic testing can be applied to a wide range of materials, including metals, plastics, and composites. It is suitable for inspecting various weld types, such as butt welds, fillet welds, and spot welds. This versatility makes it an essential tool in industries ranging from manufacturing and construction to aerospace and automotive.
- Early Detection of Flaws: By identifying flaws or defects early on, ultrasonic weld flaw detectors help prevent costly repairs or failures in the future. This proactive approach to weld inspection ensures the integrity and safety of structures and components.
- Cost-Effectiveness: The use of ultrasonic weld flaw detectors can result in cost savings for businesses. By detecting and addressing flaws at an early stage, potential issues can be resolved before they lead to significant failures or production delays. This helps in reducing repair costs and improving overall productivity.
Applications of Ultrasonic Weld Flaw Detectors
Ultrasonic weld flaw detectors find extensive applications in various industries, including:
- Manufacturing: Ultrasonic testing is used in the manufacturing sector to inspect welds in metal fabrication processes. It helps ensure the quality and reliability of welded components in industries such as automotive, aerospace, and heavy machinery.
- Construction: In the construction industry, ultrasonic weld flaw detectors are valuable tools for inspecting welds in structural components, pipelines, and infrastructure projects. They help identify any flaws or defects that could compromise the structural integrity of buildings or bridges.
- Oil and Gas: Ultrasonic weld flaw detectors are utilized in the oil and gas industry to inspect welds in pipelines, storage tanks, and offshore structures. This ensures the safety and reliability of critical infrastructure in the oil and gas sector.
- Power Generation: In the power generation industry, ultrasonic testing is used to inspect welds in power plants, including boilers, turbines, and pipelines. This helps maintain the efficiency and reliability of power generation systems.
- Transportation: Ultrasonic weld flaw detectors are employed in the transportation sector for inspecting welds in railway tracks, bridges, and vehicles. This ensures the safe and reliable operation of transportation infrastructure.
Factors Affecting Successful Weld Inspection
Several factors contribute to the success of ultrasonic weld flaw detectors in inspecting welds:
- Material Properties: The properties of the weld material, such as its thickness, composition, and grain structure, can affect the ultrasonic waves' propagation and the detection of flaws. Understanding these material properties is crucial for accurate weld inspection.
- Transducer Selection: Choosing the appropriate transducer for the specific material and weld type is essential. Different transducers have different frequencies and capabilities, and selecting the right one ensures optimal flaw detection.
- Surface Condition: Proper surface preparation, including cleaning and removal of any coatings or contaminants, is vital for accurate ultrasonic testing. Any irregularities or surface roughness can affect the wave transmission and result in false readings.
- Coupling Medium: The coupling medium used between the transducer and the weld surface, such as a gel or liquid, facilitates the transmission of ultrasonic waves. Proper coupling ensures optimal contact and efficient wave propagation.
- Operator Skill and Training: Ultrasonic weld flaw detectors require skilled operators who are trained in the proper use of the equipment and interpretation of test results. Expertise and experience play a significant role in accurate flaw detection and assessment.
Conclusion
Ultrasonic weld flaw detectors are indispensable tools in the inspection and evaluation of welds. With their ability to utilize ultrasonic waves for non-destructive testing, they provide accurate and reliable information about the quality and integrity of weld joints. The advantages of ultrasonic testing, including non-destructiveness, high accuracy, versatility, early flaw detection, and cost-effectiveness, make it an essential technique in various industries. By incorporating ultrasonic weld flaw detectors into their quality control processes, businesses can ensure the safety, reliability, and performance of their welded components and structures.
See more ultrasonic welding equipment