Exploring the Significance and Benefits of Ultrasonic Weld Inspection Equipment
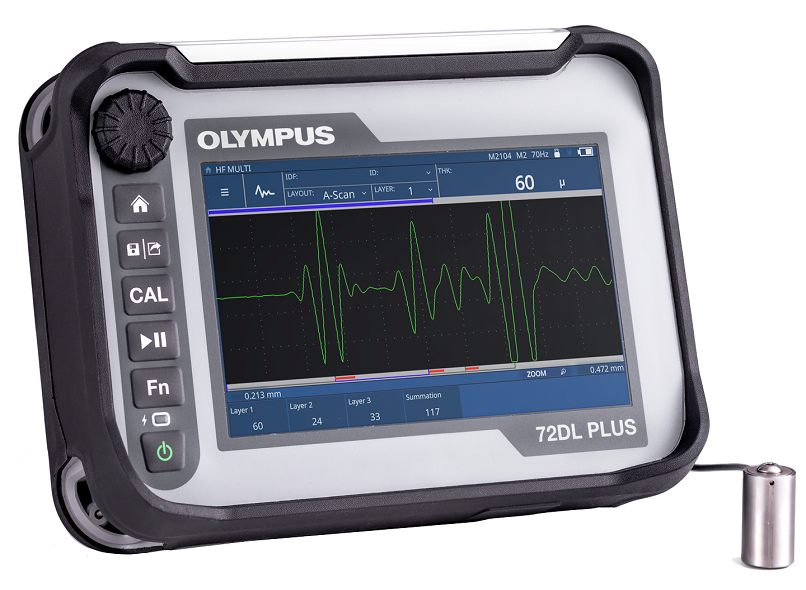
Ultrasonic weld inspection equipment plays a pivotal role in various industries, where welding is a common practice. This specialized tool is used to assess the quality and integrity of welds by utilizing ultrasonic waves. By understanding the intricacies and benefits of ultrasonic weld inspection equipment, manufacturers and construction professionals can ensure the reliability and longevity of their welded components.
Understanding Ultrasonic Weld Inspection
Ultrasonic weld inspection involves the use of high-frequency sound waves to detect and evaluate weld defects. The equipment consists of a transducer that emits ultrasonic waves and a receiver that captures the reflected waves. These waves are sent through the weld, and any changes in the waves' characteristics can indicate the presence of flaws, such as cracks, porosity, or incomplete fusion. By analyzing the time taken for the waves to travel and bounce back, the equipment can determine the size, location, and severity of any defects in the weld.
The Benefits of Ultrasonic Weld Inspection Equipment
- Non-Destructive Testing: One of the key advantages of using ultrasonic weld inspection equipment is that it is a non-destructive testing method. This means that the inspection process does not damage the weld or the surrounding materials. As a result, comprehensive assessments can be conducted without compromising the structural integrity of the weld. This is particularly important in industries where the weld's strength and durability are critical.
- Accurate Detection and Characterization: Ultrasonic weld inspection equipment provides precise and reliable measurements, ensuring accurate detection and characterization of weld defects. It can identify the size, shape, and location of flaws within the weld, allowing for efficient decision-making regarding the acceptability of the weld and the need for any repairs or adjustments. This level of accuracy helps maintain the overall quality and performance of the welded components.
- Versatility and Adaptability: Ultrasonic weld inspection equipment is suitable for various types of welds, including butt welds, fillet welds, and spot welds. It can be used on different materials, such as metals, plastics, and composites. This versatility makes it a valuable tool for industries ranging from automotive manufacturing to construction. Regardless of the material or weld type, ultrasonic inspection provides valuable insights into the weld's integrity.
- Efficient and Time-Saving: The inspection process using ultrasonic equipment is relatively quick and efficient. It allows for rapid detection and evaluation of weld defects, saving time and resources compared to other inspection methods. This efficiency is particularly beneficial in industries with high-volume production, where timely identification of defects is crucial for maintaining productivity and ensuring the quality of the end products.
- Preventive Maintenance and Quality Assurance: By regularly using ultrasonic weld inspection equipment, manufacturers can implement preventive maintenance measures to identify potential issues before they escalate into costly problems. Early detection of weld defects allows for timely repairs or adjustments, minimizing the risk of catastrophic failures and ensuring the long-term reliability of the welded components. This proactive approach to quality assurance can lead to improved customer satisfaction and reduced warranty claims.
- Compliance with Industry Standards: Many industries have specific standards and regulations regarding the quality and integrity of welds. Ultrasonic weld inspection equipment helps ensure compliance with these standards by providing accurate and reliable data on weld quality. This not only helps in meeting regulatory requirements but also enhances the reputation and credibility of the organization within the industry.
- Data Analysis and Documentation: Ultrasonic weld inspection equipment often comes with software that allows for data analysis and documentation of inspection results. This enables detailed record-keeping and trend analysis of weld defects, facilitating continuous improvement efforts and enabling organizations to identify recurring issues and implement targeted corrective actions. The availability of comprehensive data also helps in evaluating the effectiveness of welding processes and making informed decisions regarding process optimization.
- Training and Skill Development: The use of ultrasonic weld inspection equipment requires trained personnel who can effectively operate the equipment and interpret the inspection results. This promotes skill development and professional growth within the organization, ensuring that the inspection process is conducted by knowledgeable and competent individuals. Continuous training and skill development contribute to maintaining a high level of proficiency in weld inspection, leading to improved accuracy and reliability of inspection results.
- Cost Savings: Investing in ultrasonic weld inspection equipment can result in long-term cost savings. By detecting and addressing weld defects early on, organizations can avoid costly rework, repairs, or component failures down the line. The ability to identify and rectify issues promptly helps minimize downtime, improve productivity, and reduce the overall cost of weld quality control.
Conclusion
Ultrasonic weld inspection equipment is a valuable tool for ensuring the quality and reliability of welds in various industries. Its non-destructive nature, high accuracy, versatility, efficiency, preventive maintenance capabilities, compliance with industry standards, data analysis features, and the opportunity for skill development make it an essential component of weld inspection processes. By utilizing this equipment, organizations can enhance weld quality, minimize defects, ensure compliance with industry regulations, and maintain the integrity of their products and structures. Ultimately, ultrasonic weld inspection equipment helps ensure the safety, durability, and performance of welded components, contributing to the overall success of industries reliant on welding technologies.
See more ultrasonic welding for plastics